Файл: Рисунок 7 Принцип действия магнитопорошкового контроля.docx
ВУЗ: Не указан
Категория: Не указан
Дисциплина: Не указана
Добавлен: 04.02.2024
Просмотров: 39
Скачиваний: 1
ВНИМАНИЕ! Если данный файл нарушает Ваши авторские права, то обязательно сообщите нам.
В магнитопорошковом контроле используется одно или несколько магнитных полей для обнаружения поверхностных и приповерхностных неравномерностей в ферромагнитных материалах. Магнитное поле может создаваться с помощью постоянного магнита или электромагнита. При использовании электромагнита поле присутствует только при подаче тока. Когда магнитное поле сталкивается с разрывом, поперечным направлению магнитного поля, силовые линии создают собственное поле рассеяния магнитного потока, как показано на рисунке 7 [1].
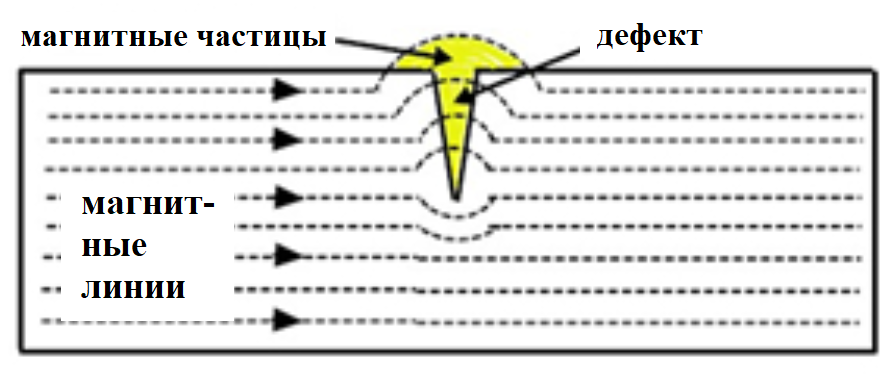
Рисунок 7 – Принцип действия магнитопорошкового контроля
Ферромагнитные частицы, нанесенные на поверхность исследуемого изделия, будут втягиваться в неоднородность, создавая видимую индикацию на поверхности детали. Магнитные частицы могут представлять собой сухой порошок или жидкий растворе, они могут быть окрашены видимым красителем или флуоресцентным красителем, который отчетливо виден в ультрафиолетовом свете [1]. При использовании «жидкого» метода магнитные частицы суспендируются в жидкости (вода или масло); при сухом способе магнитный порошок распыляют в воздухе. Для оптимизации результатов испытаний тщательно контролируются размер, форма и цвет частиц. Частицы окрашены таким образом, чтобы обеспечить хорошее цветовой контраст с проверяемой деталью. При этом магнитные частицы не должны быть токсичными.
«Жидкие» частицы обычно используются в стационарных устройствах, где их можно постоянно перемешивать, перекачивать и рециркулировать через распылительную насадку до тех пор, пока жидкость не загрязнится грязью, маслом или посторонними магнитными частицами. Влажные частицы можно использовать в небольшом портативном оборудовании, при условии, что частицы постоянно перемешиваются. Сухие магнитные частицы предназначены для использования с портативным оборудованием и оказываются особенно эффективны на больших деталях с шероховатой поверхностью. Сухие магнитные частицы используются однократно и редко восстанавливаются для повторного использования.
При использовании данного метода важно выбирать подходящую концентрацию магнитных частиц. Если концентрация частиц слишком мала, не индикация дефекта может оказаться незаметной; если концентрация магнитных частиц, напротив, слишком высока, может произойти маскирование дефекта [9].
1.8 Нейтронная дефектоскопия
В нейтронной дефектоскопии в качестве проникающей среды используется интенсивный пучок нейтронов низкой энергии, а не гамма- или рентгеновское излучение, как в обычной радиографии. Генерируемые линейными ускорителями, бетатронами и другими источниками нейтроны могут проникать в большинство металлических материалов, но замедляются большинством органических материалов (включая воду из-за высокого содержания в ней водорода), что позволяет регистрировать эти материалы внутри проверяемого изделия [1]. Различие изображений, полученных с помощью пучка нейтронов, в различных сечениях исследуемого образца сечений позволяет получить информацию о внутреннем распределении неоднородностей в тестируемом образце. В качестве частного случая нейронной дефектоскопии можно выделить нейтронная компьютерную томографию, при которой трехмерная модель исследуемого изделия восстанавливается по совокупности отдельных изображений, полученных при различных угловых положениях образца относительно направления нейтронного пучка [14].
Нейтронная радиография часто используется при проверке компонентов внутри изготовленных устройств, которые обычно не видны с помощью рентгеновской радиографии. Некоторыми приложениями нейтронной радиографии являются проверки изготовленных компонентов многих типов, таких как компоненты, разработанные для авиационной, аэрокосмической и автомобильной промышленности, включая изготовление лопастей газотурбинных двигателей, коррозию, дефекты клеевых соединений, внутренние дефекты и трещины, пустоты или другие типы внутренних дефектов в материалах и т. д [15].
1.9 Контроль течеисканием
Контроль течеисканием (тестирование на герметичность) используется для обнаружения сквозных утечек. Выделяют следующие методы контроля течеисканием: пузырьковый, метод падения давления, тестирование с применением «способа щупа» и с применением масс-спектрометра. Эти методы описаны подробнее далее.
Принцип работы пузырькового метода контроля заключается в регистрации локальных утечек в объекте по возникновению пузырьков контрольного газа в индикаторной жидкости или на индикаторном покрытии. Метод применяется для контроля герметичности емкостей, гидравлических и газовых систем, находящихся под избыточным давлением. К пузырьковым методам можно отнести метод контроля способом пенопленочного индикатора. На контролируемую поверхность, находящуюся под большим давлением, наносится специальное пенообразующее вещество. Контрольный газ, проникая через дефекты поверхности, оказывает механическое воздействие на пенопленочный индикатор и деформирует его, образуя пузырьки и пенные вздутия.
Необходимый перепад давления может создаваться с помощью вакуумного насоса. Для этого на испытываемый объект, например сварной шов, наносится пенопленочный индикатор и устанавливается вакуумная рамка, которая затем вакуумируется с помощью механического насоса. После создания градиента давления на контролируемом участке воздух, проникающий через течи в камеру рамки, образует пузырьки в пенопленочном индикаторе. Регистрация утечки пузырьковым методом продемонстрирована на рисунке 8 [16].
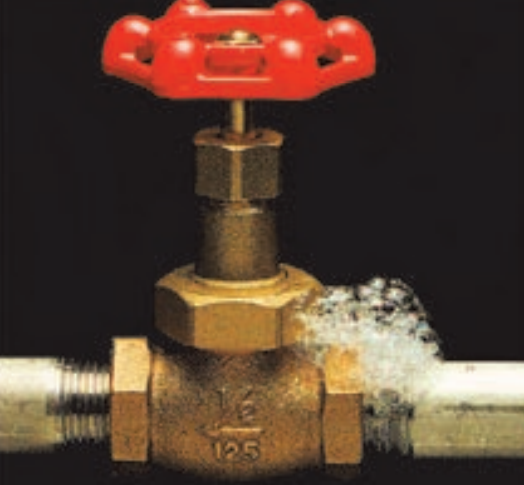
Рисунок 8 – Регистрация утечки пузырьковым методом
Контроль методом падения давления может проводиться только в закрытых системах. Обнаружение утечки производится либо путем повышения давления в системе, либо путем создания вакуума, а затем контроля давления. Уменьшение давления или уменьшение уровня вакуума в течение заданного промежутка времени указывает на наличие утечки в системе. Важно отметить, что изменения температуры внутри системы могут привести к изменению давления, поэтому получаемые показания необходимо корректировать с учетом температуры [1].
Другим методом контроля течеисканием является так называемый «способ щупа», при котором исследуемый объект заполняется пробным веществом (контрольным газом) до давления выше атмосферного, после чего наружная поверхность исследуемого объекта контролируется с применением специального щупа, который соединен с детектором течеискателя. В результате перепада давления пробное вещество проникает через имеющиеся дефекты и в месте течи регистрируется щупом и индицируется детектором течеискателя. Кроме того, при использовании данного метода также можно применять масс-спектрометр, что отражено в таблице 1 [14], характеризующий перечень «щуповых» способов и методов контроля течеисканием.
Таблица 1 – Перечень «щуповых» способов и методов контроля течеисканием
№ | Способы и методы контроля течеисканием | Диапазоны пороговых чувствительностей, м3, Па/с | Масса течеискателя, кг, цена, руб | Примечания |
1 | Способ гелиевого щупа с применением масс-спектрометрических течеискателей | Более 10-9 до 10-7 и далее меньше | ≈1 млн. руб., ≈ 40 кг. | Контрольный газ - гелий |
2 | Способ атмосферного щупа с применением катарометрических течеискателе | Более 10-9 до 10-7 и далее меньше | – | Течеискатель не выпускается отечественной промышленностью, контрольный газ – любой отличный по теплопроводности от воздуха |
3 | Способ галогенного атмосферного щупа | Более 10-9 до 10-7 и далее меньше | ≈100 тыс. руб., ≈ 3 кг. | Контрольный газ – фреоны (не реагирует на гелий) |
4 | Метод щупа с применением сенсорных течеискательных элементов | Более 10-9 до 10-7 и далее меньше | ≈100 тыс. руб., ≈ 3 кг. | Контрольный газ – реакционно-способные газы (не реагирует на гелий) |
5 | Метод щупа с применением акустических течеискателей | Чувствительность не нормируется, хуже чем 10-4 | ≈100 тыс. руб., ≈ 3 кг. | Низкая чувствительность к контрольному газу, контрольный газ – любой отличный по скорости звука от воздуха |
Как можно видеть из таблицы 1, способ гелиевого щупа с применением масс-спектрометрических течеискателей имеет наивысшую чувствительность. В процессе работы детектор масс-спектрометрического течеискателя селективно выявляет контрольный газ – гелий. Тем не менее, течеискатель достаточно дорог, при этом его реализация возможна только в стационарном виде.
Способ атмосферного щупа с использованием катарометрических течеискателей универсален в эксплуатации, однако детектор данного течеискателя не обладает селективностью, и регистрирует все посторонние газы, теплопроводность которых отличается от теплопроводности воздуха.
Способ галогенного атмосферного щупа и метод щупа с применением сенсорных течеискательных элементов также не обладают селективностью и помимо этого не обеспечивают индикацию гелия (наиболее безопасного контрольного газа). Также следует отметить неустойчивую работу перечисленных методов и способов в случае загазованности зоны контроля пробным газом. Способ щупа с применением акустических течеискателей не обладает селективностью и чувствительность метода низка.
Важно отметить, что при «щуповых» методах контроля не оценивается суммарная степень негерметичности. Вывод о герметичности исследуемого изделия принимается на основании результатов аккуратного и тщательного сканирования поверхности исследуемого изделия щупом течеискателя специалистом по неразрушающему контролю. При этом скорость перемещения щупа течеискателя составляет, как правило, 10-15 см/мин [16].
1.10 Радиографический контроль
Рентгенографический (радиографический) контроль работает следующим образом. На тестируемое изделие воздействуют проникающим излучением таким образом, чтобы излучение проходило через проверяемый объект и регистрирующий материал, помещенный на противоположную сторону этого объекта. Для более тонких или менее плотных материалов, таких как алюминий, обычно используется электрически генерируемое рентгеновское излучение (рентгеновские лучи), а для более толстых или плотных материалов обычно используется гамма-излучение.
В качестве регистрирующего материала может выступать рентгеновская пленка или один из нескольких типов цифровых детекторов излучения. В обоих случаях излучение, проходящее через тестируемый объект, воздействует на данный материал или детектор, вызывая эффект в виде потемнения областей, соответствующим местам, где через исследуемый образец прошло большее количество излучения, и более светлых областей, где, соответственно, через исследуемый образец прошло меньшее количество излучения. Если в исследуемом образце есть пустота или дефект, через нее проходит больше излучения, что приводит к более темному изображению на пленке или детекторе, как показано на рисунке 9 [1].
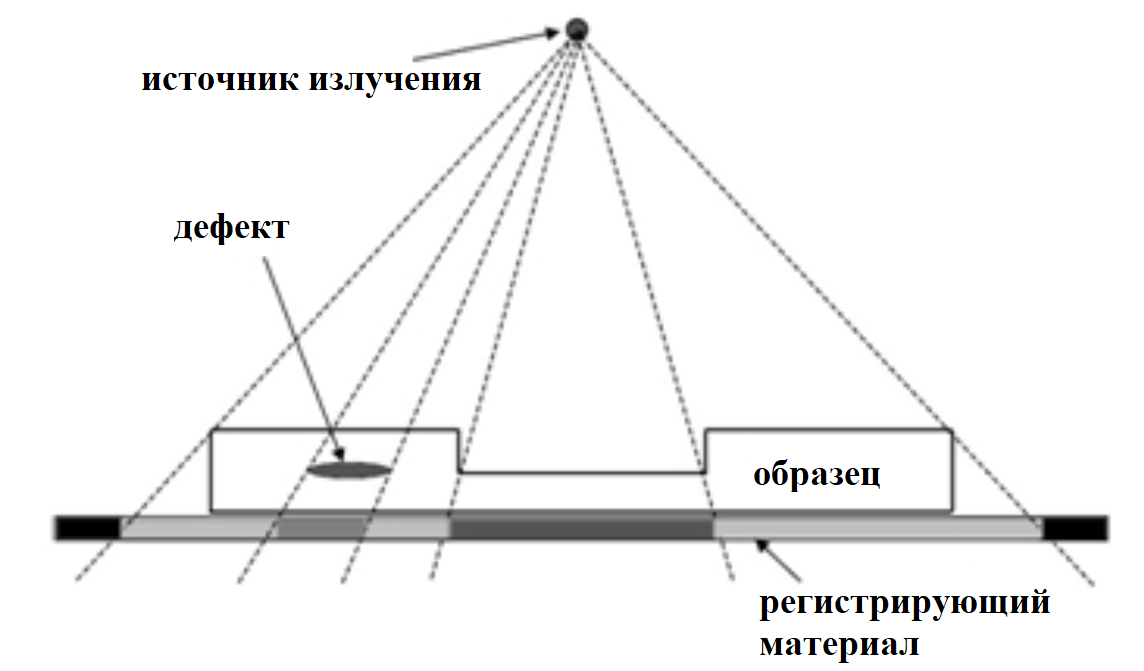
Рисунок 9 – Принцип работы радиографического контроля
Можно выделить несколько основных методов радиографического контроля:
– пленочная рентгенография;
– цифровая рентгенография;
– компьютерная рентгенография;
– компьютерная томография.
В пленочной рентгенографии используется пленка, состоящая из тонкого прозрачного пластика, покрытого слоем бромистого серебра с одной или обеих сторон. При воздействии радиации начинается реакция, которая при проявлении пленки окрашивает серебро в черный цвет. В процессе проявления пленки это серебро также закрепляется на пластике, и после высыхания получается готовая рентгенографическая пленка.
Чтобы пленка была пригодной для использования, интересующая область (например, зона сварного шва и т.д.) на пленке должна находиться в пределах определенного диапазона плотности (затемнения) и должна обладать достаточным контрастом, чтобы можно было зафиксировать интересующие дефекты. Эти параметры зависят от дозы излучения, расстояния источника до пленки и толщины исследуемой детали. Если какой-либо из этих параметров не соблюдается, для этой области детали необходимо произвести повторную экспозицию (сделать еще один «снимок»).
Цифровая рентгенография преобразует излучение, проходящее через объект, непосредственно в изображение, которое может быть отображено на мониторе компьютера. Можно выделить три основные технологии, используемые в прямой цифровой визуализации: аморфный кремний, устройства с зарядовой связью и КМОП (комплементарная структура металл-оксид-полупроводник). Полученные изображения становятся доступны для просмотра и анализа за считанные секунды по сравнению со временем, необходимым для сканирования в компьютерной рентгенографии, рассмотренной далее. Повышенная скорость обработки является результатом уникальной конструкции пикселей, а также, которое обеспечивает более высокое разрешение, чем в компьютерной рентгенографии и большинстве пленочных приложений.
Компьютерная томография использует компьютер для восстановления изображения плоскости поперечного сечения объекта в отличие от обычного рентгенографического изображения, за счет чего можно получить более точное представление о дефектах в исследуемом образце, как продемонстрировано на рисунке 10 [1]. В данном случае изображение создается на основе нескольких снимков, сделанных под разными углами обзора, которые реконструируются с помощью компьютера. При традиционной рентгенографии положение внутренних дефектов не может быть точно определено без снятия нескольких снимков под различными углами для определения местоположения дефекта с помощью триангуляции.