Добавлен: 06.11.2023
Просмотров: 43
Скачиваний: 2
ВНИМАНИЕ! Если данный файл нарушает Ваши авторские права, то обязательно сообщите нам.
Технический титан часто называют малолегированным многокомпонентным титановым сплавом. Однако этот сплав в ряде случаев является недостаточно прочным, а повышение прочности за счет увеличения количества примесей вызывает значительное понижение пластичности. Вследствие этого приходится переходить к сплавам, легированным алюминием и оловом. Эти элементы, каждый в отдельности и оба вместе, растворяясь в α-титане, повышают его прочность без существенного снижения пластичности, благодаря чему получаемые сплавы могут быть прокатаны в лист, как и технический титан, но имеют значительно более высокую прочность.
Все листовые сплавы (ВТ4, ОТ4, ВТ5, ВТ5-1, ВТ6 и др.) хорошо свариваются аргонно-дуговой сваркой, а сплавы ВТБ и ВТ6 — еще и контактной (точечной, роликовой, стыковой). Ковочно-штамповочные титановые сплавы сварке не подвергаются.
Титан и его сплавы применяют после тщательного учета всех положительных и отрицательных качеств этих материалов. При этом обращают внимание как на эксплуатационные свойства, так и на технологические особенности. Учитывается также и экономический фактор.
2.3 Разработка маршрутного технологического процесса.
Технологический процесс — это часть производственного процесса, содержащая целенаправленные действия по изменению и (или) определению состояния предмета труда. К предметам труда относят заготовки и изделия.
В зависимости от применения в производственном процессе для решения одной и той же задачи различных приёмов и оборудования различают следующие виды техпроцессов:
-
Единичный технологический процесс (ЕТП). Разрабатывается индивидуально для конкретной детали. -
Типичный технологический процесс (ТТП). Создается для группы изделий, обладающих общностью конструктивных признаков. Разработку типовых технологических процессов осуществляют на общегосударственном и отраслевом уровнях, а также на уровнях предприятия в соответствии с общими правилами разработки технологических процессов. -
Групповой технологический процесс (ГТП).
В промышленности и сельском хозяйстве описание технологического процесса выполняется в документах, именуемых операционная карта технологического процесса (при подробном описании) или маршрутная карта (при кратком описании).
-
Маршрутная карта — описание маршрутов движения по цеху изготовляемой детали. -
Операционная карта — перечень переходов, установок и применяемых инструментов. -
Технологическая карта — документ, в котором описан: процесс обработки деталей, материалов, конструкторская документация, технологическая оснастка.
2.4 Выбор технологического оборудования и его техническую характеристику.
Станок модели 1К62
Токарно-винторезный станок 1К62 по предназначен для обработки цилиндрических, конических и сложных поверхностей - как внутренних, так и наружных, а так же для нарезания резьбы. Для обработки торцовых поверхностей заготовок применяются разнообразные резцы, развертки, сверла, зенкеры, а так же плашки и метчики.
Буквенно-цифирный индекс токарно-винторезного станка 1К62 обозначает следующее: цифра 1 - это токарный станок; цифра 6 – обозначает токарно-винторезный станок, буква К – поколение станка, цифра 2 – высота центров (220мм). Наличие буквы «П» в конце индекса обозначает повышенную точность. В этом случает обозначение станка выглядит так: 1К62 П.
Таблица 5 – Технические характеристики станка 1К62
Технические характеристики | Параметры |
1 | 2 |
Диаметр обработки над станиной, мм | 400 |
Диаметр обработки над суппортом, мм | 220 |
Расстояние между центрам | 1000 / 1500 |
Класс точности по ГОСТ 8-82 | Н |
Размер внутреннего конуса в шпинделе | Морзе 6 М80* |
Конец шпинделя по ГОСТ 12593-72 | 6К |
Диаметр сквозного отверстия в шпинделе, мм | 55 |
Максимальная масса заготовки, закрепленной в патроне, кг | 300 |
Максимальная масса детали, закрепленной в центрах, кг | 1300 |
Максимальная масса заготовки, закрепленной в патроне, кг | 23 |
Число ступеней частот обратного вращения шпинделя | 12 |
Пределы частот прямого вращения шпинделя, мин-1 | 12,5 - 2000 |
Пределы частот обратного вращения шпинделя, мин-1 | 19 - 2420 |
Число ступеней рабочих подач - продольных | 42 |
Число ступеней рабочих подач - поперечных | 42 |
Пределы рабочих подач - продольных, мм/об | 0.7 - 4,16 |
Пределы рабочих подач - поперечных, мм/об | 0,035-2,08 |
Число нарезаемых метрических резьб | 45 |
Число нарезаемых дюймовых резьб | 28 |
1 | 2 |
Число нарезаемых модульных резьб | 38 |
Число нарезаемых питчевых резьб | 37 |
Число нарезаемых резьб - архимедовой спирали | 5 |
Наибольший крутящий момент, кНм | 2 |
Наибольшее перемещение пиноли, мм | 200 |
Поперечное смещение корпуса, мм | ±15 |
Наибольшее сечение резца, мм | 25 |
Мощность электродвигателя главного привода | 10 кВт |
Мощность электродвигателя привода быстрых перемещений суппорта, кВт | 0,75 или 1.1 |
Мощность насоса охлаждения, кВт | 0,12 |
Габаритные размеры станка (Д х Ш х В), мм | 2812/3200х1166х1324 |
Масса станка, кг | 3035 |
Вертикально-фрезерный станок 6Р12
Вертикально-фрезерный станок 6Р12, предназначен для фрезерования, сверления и выполнения расточных работ заготовок любых форм и из любых материалов - от чугуна до сплавов цветных металлов, пластмасс. Шпиндельная головка вертикально-фрезерного станка оснащена механизмами поворота и ручного осевого перемещения шпинделя. Это позволяет производить обработку отверстий, расположенных под наклоном до ±45° к поверхности стола. Высокая жесткость вертикально-фрезерного станка 6Р12 в сочетании с мощным приводом позволяет использовать фрезы с пластинами из быстрорежущей стали, а также из твердых и сверхтвердых материалов.
Буквенно-цифирный индекс вертикально-фрезерного станка 6Р12, обозначает следующее: цифра 6 - это фрезерный станок; индекс Р - обозначает завод-производитель станка, цифра 1 – обозначает вертикально-фрезерный станок, цифра 2 – типоразмер станка (размер стола).
Таблица 6 – Технические характеристики станка 6Р12
Технические характеристики | Параметры |
1 | 2 |
Размеры рабочей поверхности стола, мм | 1250 х 320 |
Наибольшее продольное перемещение стола, мм | 800 |
Наибольшее поперечное перемещение стола, мм | 320 |
Наибольшее вертикальное перемещение стола, мм | 420 |
1 | 2 |
Расстояние от торца шпинделя до рабочей поверхности стола, мм | 30 - 450 |
Пределы частот вращения шпинделя, мин -1 | 31,5 - 1600 |
Ускоренное продольное перемещение стола, мм/мин | 4000 |
Ускоренное поперечное перемещение стола, мм/мин | 4000 |
Ускоренное вертикальное перемещение стола, мм/мин | 1330 |
Максимальная масса обрабатываемой детали с приспособлением, кг | 250 / 550 |
Мощность электродвигателя привода шпинделя, кВт | 7,5 / 11 |
Мощность электродвигателя привода стола, кВт | 3 |
Конус шпинделя по ГОСТ 30064-93 | ISO 50 |
Габаритные размеры станка (Д х Ш х В), мм | 2280 х 1965 х 2265 |
Масса станка с электрооборудованием, кг | 3250 |
2.6 Расчет режимов резания и норм времени.
2.6.1 Расчет режимов резания на токарную операцию 015.
Деталь – корпус. Материал – ВТ5-1. Заготовка - штамповка. Масса детали – 4,3*10-3кг. Оборудование - универсальный токарно-винторезный станок 1К625, с охлаждением.
В качестве режущего инструмента принимается:
-
Резец проходной упорный черновой, материал режущей части ВК8;
– Главный угол в плане для подрезки ȹ = 90°;
– Радиус вершины резца r = 1,0 мм.
Содержание операции:
А. Установ 1
-
Подрезать торец 1; -
Точить поверхность 2; -
Расточить отверстие 3;
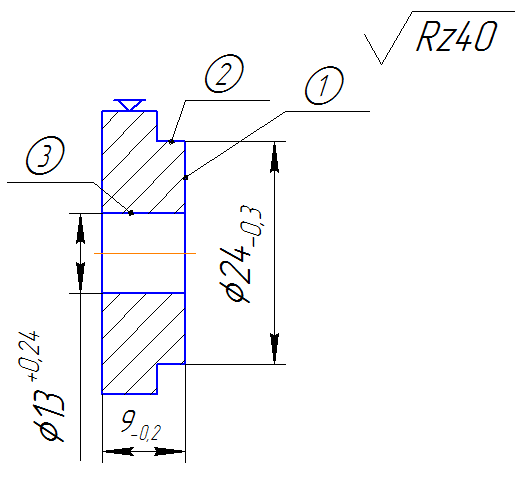
Рисунок 3 – Операция 015 токарная
а) Определение мест обработки:
- Определение длины обработки (l) согласно эскизу:
Переход 1
Длина обработки торца заготовки
l1 = 4,5+4 = 8,5 мм;
Переход 2
Длина обработанной поверхности
l2 = 3+4 = 7 мм;
Переход 3
Длина растачиваемого отверстия
l3 = 9+4 = 13 мм;
- Определение глубины резания (t):
t1 = 3 мм;
t2 = 3 мм;
t3 = 7,5 мм;
- Подача при точении по табл. 40.;
Переход 1
S1 = 0,3-0,4 мм/об.;
Уточнение подачи по паспорту станка: S1пасп = 0,4 мм/об.;
Переход 2
S2 = 0,3-0,4 мм/об.;
Уточнение подачи по паспорту станка: S2пасп=0,4 мм/об.
Переход 3
S3 = 0,10 мм/об.;
Уточнение подачи по паспорту станка: S3пасп = 0,10 мм/об.;
- Скорость резания при точении определяется по табл. 43
Переход 1
При подрезки торца: t = 3 мм; S = 0,4 мм/об.; φ=90°; Vр = 34 м/мин.;
Переход 2
При продольном обтачивании: t = 3 мм; S= 0,4 мм/об.; Vр = 32 м/мин.;
Переход 3
При растачивании отверстия: t=2 мм; S= 0,7мм/об Vтаб.3 = 71м/мин.
- Частота вращения шпинделя (n) определяется по формуле:
n =

Где V – табличное значение скорости;
D – диаметр обрабатываемой поверхности;
n1 =

n2 =

n3 =

Уточнение оборота по паспорту станка
n1 пасп = 710 об/мин;
n2 пасп = 450 об/мин;
n3 пасп = 710 об/мин;
- Фактическая скорость резания (Vф) определяется по формуле:
V
ф =

Vф1 =
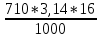
Vф2 =
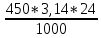
Vф3 =
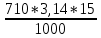
- Число проходов при точении зависит от глубины, подачи и скорости резания:
i1,2,3 = 1;
- Минутная подача (Sм) определяется по формуле:
Sм = S*n (21)
Sм1 = 0,4*710 = 284 мм/мин.;
Sм2 = 0,4*450 = 180 мм/мин.;
Sм3 = 0,1*710 = 71 мм/мин.;
- Основное технологическое время определяется по формуле:
То =

Где То – основное время обработки;
Т1 =

Т2 =

Т3 =

То = 0,04+0,08+0,12 = 0,24 мин.;
- Вспомогательное время определяется по формуле:
Тв = (tуст+Σtпер + Σt’пер + Σtизм)*Ktв (23)
Где tуст - время на установку и снятие детали, мин, (определяется по табл. 47);
Σtпер - время, связанное с переходом, мин., при точении по табл. 48;
Σt’пер - время, на приемы не вошедшие в комплекс, мин., при точении по табл. 49;
Σtизм - время на контрольные измерения, мин. (по табл. 53);
Ktв – коэффициент на вспомогательное время (табл. 54);
tуст = 0,25 мин.;
Σtпер = 0,08+0,08+0,08 = 0,24 мин.;
Σt’пер = 0,07+0,07+0,07 = 0,21 мин.;
Σtизм = (0,10+0,25+0,25)*0,9 = 0,54 мин.;
Ktв = 0,81 мин.;
Тв = (0,25+0,24+0,21+0,54)*0,81 = 1,0 мин.
- Время на обслуживание рабочего места и перерывы (табл. 50):
аобс= 4%; аотл =4%.
- Штучное время определяется по формуле:
Тобс= (То + Тв)*

Тотл= (То + Тв)*

Тобс = (0,24+1,0)*(4/100) = 0,04 мин.;
Тотл