Файл: 1. Единая система газоснабжения. Назначение. Основные составные элементы. Единая система газоснабжения.docx
ВУЗ: Не указан
Категория: Не указан
Дисциплина: Не указана
Добавлен: 07.11.2023
Просмотров: 93
Скачиваний: 2
ВНИМАНИЕ! Если данный файл нарушает Ваши авторские права, то обязательно сообщите нам.
Рабочие лопатки осевого компрессора являются одними из самых нагруженных элементов ГТД. В процессе работы лопатки испытывают большие нагрузки, изменяющиеся в широких пределах. Они выполняются с высокой степенью точности и с минимальной шероховатостью.
Назначение лопаток статора: Направляющие лопатки располагаются внутри статора и крепятся на неподвижной части осевого компрессора, они не подвержены воздействию центробежных сил. Такие лопатки образуют каналы, в которых рабочая среда приобретает необходимую скорость и направление.
Венец рабочих лопаток компрессора и расположенный за ним венец лопаток направляющего аппарата образуют ступень осевого компрессора. Обычно компрессор ГТД имеет от 5 до 25 ступеней.
В процессе работы на лопатки действуют инерционные и аэродинамические силы, вызывающие напряжения растяжения, изгиба и кручения. Лопатки испытывают вибрационные нагрузки, изменяющиеся в широких пределах.
О
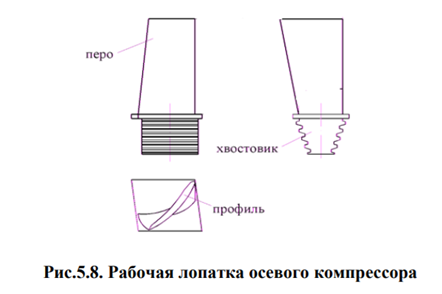
Форма и размеры пера лопатки определяются аэродинамическими и прочностными расчетами. Материалами для изготовления лопаток являются теплостойкие и коррозионностойкие хромистые стали и жаропрочные, титановые сплавы.
Соединения лопаток с ротором компрессора должно обеспечивать:1)размещение нужного количества лопаток; 2)необходимую прочность и жесткость крепления при минимальном весе хвостовика; 3)требуемую точность размещения на роторе; 4)простоту монтажа и демонтажа;
Виды креплений: ласточкин хвост(а); шарнирный(б) (позволяет лопатке устанавливаться в плоскости вращения так, чтобы уменьшить напряжения); елочка(в).
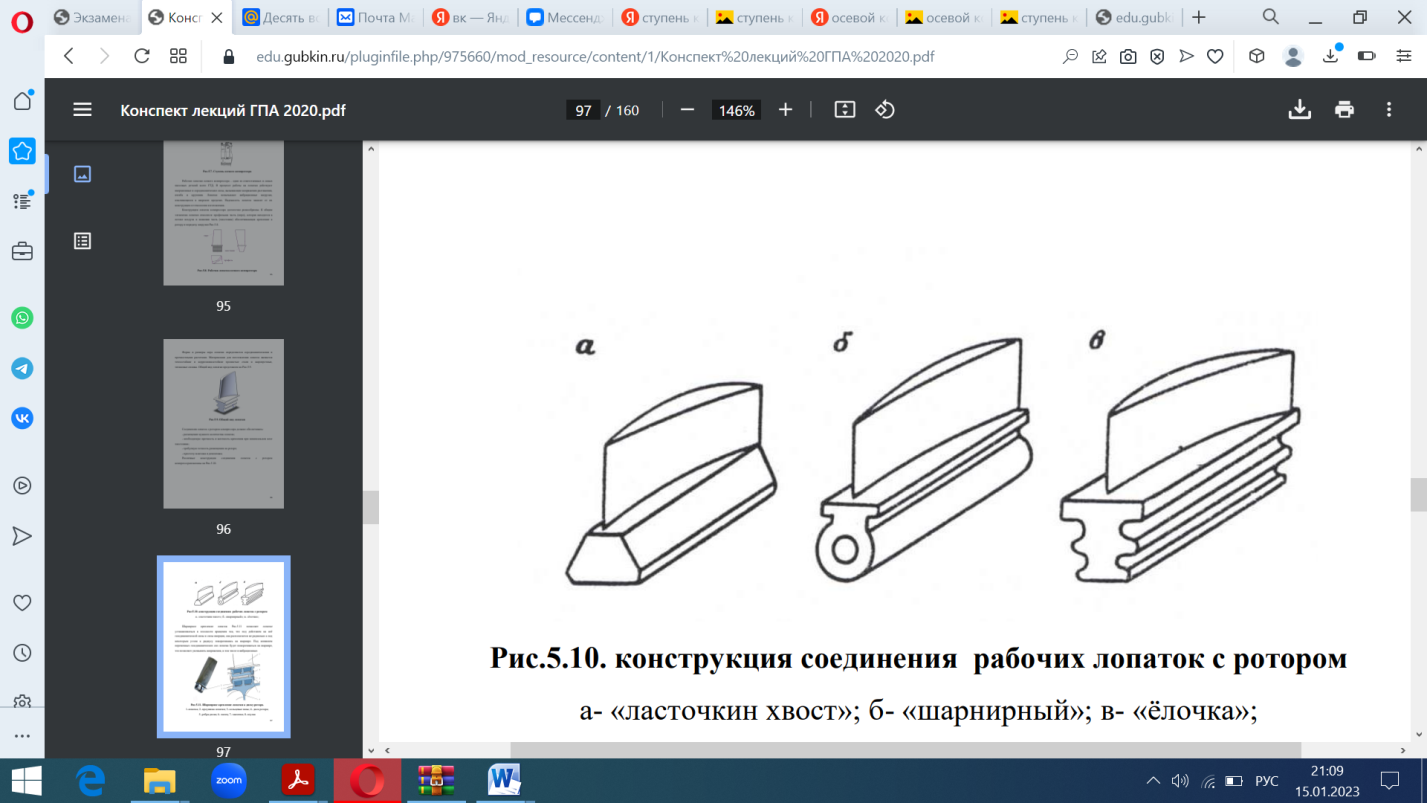
Устойчивую с необходимыми характеристиками работу компрессора
достигают с помощью регулирования работы компрессора перепуском воздуха
и поворотом направляющих лопаток. Перепуск воздуха обычно применяется в зоне средних ступеней осевого компрессора и позволяет на низких частотах вращения ротора компрессора увеличить расход воздуха через передние ступенине увеличивая расход воздуха через последние ступени компрессора. +тип ротора
из Вопр. 7
-
Лопатки турбины газотурбинного двигателя. Конструкция. Системы охлаждения.
Рабочие и сопловые лопатки турбины работают в прямом контакте с высокотемпературными продуктами горения, поступающими из камеры сгорания, при этом допустимая температура материалов рабочих и сопловых лопаток обычно на 200 - 500°С ниже температуры газов. Для обеспечения надежной и длительной эксплуатации турбины при ее изготовлении используются жаропрочные, жаростойкие и коррозионностойкие материалы, специальные покрытия и уникальные технологии изготовления лопаток. Лопатки должны обладать высокой прочностью, низким уровнем вибраций, высокой точностью изготовления и низкой шероховатостью, технологичностью изготовления.
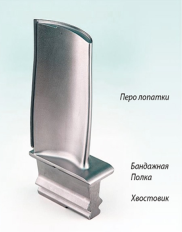
Основные конструктивные элементы лопатки: гребешки, бандажная полка, гребешки торцевого лабиринтного уплотнения, отверстие для подвода охлаждающего воздуха во внутренние каналы охлажд. лопатки.
Все рабочие и сопловые лопатки ТВД охлаждаются воздухом высокого давления, отбираемым за компрессором высокого давления. В первые сопловые лопатки воздух для охлаждения подается со стороны верхней и нижней полок. Рабочая лопатка первой ступени охлаждается воздухом, который подается под замки каждой лопатки и затем по отверстиям в замках поступает во внутренную полость лопатки и выходит в проточную часть обеспечивая и дополнительное пленочное охлаждение наружной поверхности лопатки. Для охлаждения соплового аппарата второй ступени используется воздух от промежуточной ступени компрессора. Воздух подводится в кольцевую полость над сопловыми лопатками и подается в каждую лопатку, охлаждает её и выходит в проточную часть. Воздух для охлаждения рабочих лопаток второй ступени ТВД так же отбирается от КВД. Лопатки ТНД неохлаждаемые.
Система охлаждения должна обеспечивать: необходимый уровень температур деталей; равномерность их прогрева, исключающую появление опасных температурных напряжений, приводящих к появлению трещин.
Основные методы охлаждения относятся конвективное, пленочное и пористое.
1.Конвективное охлаждение - осуществляется путем съема тепла с поверхности детали потоком воздуха, двигающегося по каналам внутри детали или вдоль её поверхности, с последующим выпуском воздуха в проточную часть двигателя.
2.Пленочное охлаждение - воздух после конвективного охлаждения подается в виде защитной пленки на поверхность лопатки для защиты от горячих газов.
3.Наибольший эффект от увеличения эффективности охлаждения за счет увеличения поверхности теплообмена, достигается при пористом охлаждении лопаток, однако такой метод не нашел широкой реализации.
Наибольшее распространение получили конвективное охлаждение и комбинированное конвективно-пленочное охлаждение. В них воздух подводится через корневую часть лопатки и растекается по внутренним каналам в различных направлениях.
10. Системы охлаждения роторов газовых турбин.
Ротор подвергается: тепловым, статическим, вибрационным нагрузкам, связанным с вращением ротора и является наиболее напряженной частью турбины.
Основным элементом ротора является диск(либо барабан), служащий для размещения на нем рабочих лопаток, от которых крутящий момент через диск передается на вал турбины. Для обеспечения защиты диска от перегрева необходима система охлаждения диска.
Три схемы охлаждения дисков: с радиальным обдувом, струйное и комбинированное струйно-радиальное.
1.Радиальный обдув: Радиальное течение охлаждающей среды происходит в зазоре между корпусом и боковыми поверхностями дисковых или барабанных роторов. (Течение может быть направлено как от оси вращения ротора к периферии дисков, так и в противоположную сторону). Охлаждение происходит с помощью специального покрывного диска-дефлектора. Охлаждающий воздух после дефлектора проходит через зазоры между хвостовиками рабочих лопаток и пазами диска, отведя часть теплоты, поступающий к диску, через перо рабочей лопатки.
2.Струйное охлаждение: Применяют для резкого усиления теплообмена на ограниченной поверхности. Струйное охлаждение позволяет, не повышая расхода охлаждающей среды, увеличить скорость ее натекания на поверхность диска. Охлаждающую среду подают через узкий кольцевой канал либо отдельными струями, вытекающими из расположенных на одной окружности круглых или прямоугольных сопл.При струйном охлаждении необходимо тщательно уплотнять приторцевую полость диска, отделяя ее от проточной части турбины.
3.Комбинированное струйно-радиальное охлаждение: Применяется, если по конструктивным соображениям нельзя применять струйное охлаждение. Такая схема позволяет отбирать основное количество теплоты от дисков в наиболее нагретой его части – местах крепления хвостовиков рабочих лопаток. Соотношение расходов воздуха на струйное и радиальное охлаждение обеспечивает необходимое распределение температур в диске.
Иногда для охлаждения самых горячих элементов газовой турбины воздух, отбираемый из выходного диффузора компрессора, направляют сначала в воздухоохладитель, где его охлаждают (обычно водой) до 180—200°С и затем направляют на охлаждение. В этом случае воздуха для охлаждения требуется меньше, но при этом появляются затраты на воздухоохладитель, усложняется ГТУ, теряется часть теплоты, отводимой охлаждающей водой.
Система охлаждения газовой турбины — самая сложная система в ГТД, определяющая ее срок службы, она должна обеспечивать не только необходимый уровень температур деталей, но и равномерность их прогрева, исключающую появление опасных температурных напряжений, циклическое действие которых приводит к появлению трещин.
Излишнее охлаждение деталей так же вредно, так как оно приводит к повышенным затратам охлаждающего воздуха, на сжатие которого в компрессоре затрачивается мощность турбины. Повышенные расходы воздуха на охлаждение приводят к снижению температуры газов за турбиной, что очень существенно влияет на работу оборудования, установленного за ГТД(ниже КПД).
11. Уплотнения в конструкции газотурбинных двигателей. Типы. Назначение.
Назначение. Уплотнения предназначены для уменьшения утечек воздуха (газа) из газовоздушного тракта двигателя; для уменьшения внутренних перетеканий воздуха (газа) из области с повышенным в область с пониженным давлением газового тракта двигателя, для уменьшения или полного устранения утечек жидкостей в агрегатах и опорах валов.
Для уменьшения утечек применяются радиальные, торцевые и радиально-торцевые уплотнения.
Уплотнения подвижных соединений можно разделить на бесконтактные (лабиринтное, щеточное, графитовое бесконтактное) и контактные (графитовое контактное, металлические и мягкие набивки сальников, манжеты).
Типы уплотнений: масляные, сухие и барьерные уплотнения.
Назначение «сухие уплотнения»: применяются для исключения потерь газа из зоны рабочего колеса, и обусловлено это следующими факторами: сухие газодинамические уплотнения обладают высокой герметизирующей способностью, т.е. уровень протечек через них в несколько раз ниже, чем у уплотнений других типов. Конструкция уплотнительной ступени: пара (картридж): торец и седло. В нерабочем состоянии нагнетателя графитовое кольцо картриджа плотно прижато к кольцу со спиральными канавками. Герметичность уплотнения достигается за счет контакта гладких притертых частей обоих колец.
Назначение «барьерное уплотнение»: предназначено для изоляции газового уплотнения от подшипниковой камеры и предотвращения попадания масла на уплотнительные поверхности. Оно выполняется в виде лабиринтного уплотнения или сегментного графитового кольца. Уплотнение в этом месте достигается за счет подачи буферного воздуха.
Назначение «масляное уплотнение»: Принцип работы таких уплотнений следующий: в камеру между торцевым уплотнением и опорным подшипником подводится масло с давлением на 0,1–0,3 МПа больше, чем давление газа в камере после лабиринтного уплотнения. Система регулирования уплотнения нагнетателя поддерживает необходимое превышение давления уплотняющего масла под давлением газа.
12.Центробежные нагнетатели. Назначение. Конструкция.
Центробежный нагнетатель – это устройство, предназначенное для повышения давления перекачиваемого газа с помощью центробежной силы(за счет преобразования механической энергии привода в энергию сжатого газа.).
Назначение ЦБН: сжатие газа в небольшом объеме, при одновременном увеличении давления и температуры сжимаемого газа.
Основным элементом центробежного компрессора является ротор, состоящий из вала, на котором закреплено рабочее колесо РК с лопатками. Захваченный лопастями газ, вращаясь вместе с РК, под действием центробежной силы, приобретает ускорение, направленное по радиусу колеса, и выходит из колеса со скоростью и давлением намного большими чем на входе. В установленном на выходе из колеса диффузоре скорость газа уменьшается, часть кинетической энергии переходит в потенциальную, а давление возрастает. Газ через устройство сбора газа («Улитка»)поступает в трубопровод нагнетания.
Р
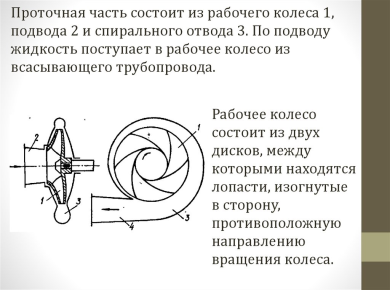
Диффузор – важная часть центробежного компрессора, где кинетическая энергия газового потока после рабочего колеса преобразуется в потенциальную энергию давления. Одновременно диффузор обеспечивает равномерность потока по величине и направлению скорости, снижая в определенной степени закрутку потока после выхода его из рабочего колеса.
Конструкция центробежных нагнетателей имеет классификацию и по типу корпуса