Файл: Пк 1 Слесарная обработка узлов и деталей, входящих в состав оборудования.doc
ВУЗ: Не указан
Категория: Не указан
Дисциплина: Не указана
Добавлен: 08.11.2023
Просмотров: 155
Скачиваний: 2
ВНИМАНИЕ! Если данный файл нарушает Ваши авторские права, то обязательно сообщите нам.
В зависимости от конструкции различают шпоночные соединения с призматическими, сегментными, направляющими, скользящими и клиновыми шпонками, каждое из которых имеет свои достоинства и недостатки.
Призматические шпонки имеют прямоугольное сечение, противоположные грани у них параллельны. Работают эти шпонки боковыми сторонами. Призматические шпонки изготавливаются в двух исполнениях: с закругленными и плоскими торцами. Соединение шпонки с валом неподвижное напряженное. В паз ступицы шпонка входит с зазором.
Сегментные шпонки подобно призматическим работают боковыми гранями. При необходимости по длине вала могут устанавливаться две, а иногда и три шпонки. К достоинствам сегментных шпонок относится простота изготовления как самих шпонок, так и пазов под них, к недостаткам — необходимость изготовления глубоких пазов в валах, что снижает прочность последних. В связи с этим сегментные шпонки применяют только для передачи сравнительно небольших моментов.
Направляющие шпонки применяют в тех случаях, когда ступица должна иметь возможность перемещаться вдоль вала. Такие шпонки крепят к валу при помощи винтов. Для крепления шпонки к валу в ней выполняют два отверстия, имеющих углубления под головки винтов. Еще одно отверстие выполняется в шпонке для подвода смазки. Соединение шпонки с пазом вала неподвижное плотное, а с пазом ступицы — свободное с зазором,
Скользящие шпонки применяют вместо направляющих в тех случаях, когда требуется значительное перемещение ступицы вдоль вала. Шпонка имеет цапфу, которая входит в отверстие, выполненное в ступице, перемещаемой вдоль вала. При изменении положения ступицы на валу шпонка перемещается вместе со ступицей по пазу вала.
Клиновые шпонки в совокупности с валом и ступицей образуют напряженное соединение. Они представляют собой клин прямоугольного сечения с уклоном 1:100, Работают такие шпонки широкими гранями и обеспечивают неподвижное крепление детали на валу. Клиновые шпонки плохо центрируются, поэтому применяются только для неответственных тихоходных передач.
При сборке шпоночного соединения большое значением имеет строгое соблюдение посадок в соединении шпонки с валом и ступицей. Одной из основных причин неправильного распределения нагрузки и смятия шпонки является увеличение зазора в соединении. К смятию может также привести неправильное расположение паза на валу нередко наблюдается и перекос осей пазов относительно оси вала, что значительно затрудняет сборку шпоночного соединения и вызывает перекос охватывающей детали на валу.
Прежде чем приступить к сборке шпоночных соединений, особенно ответственных, необходимо произвести контроль размеров шпоночного паза на валу и его расположения относительно оси вала.
Контроль глубины паза (рис. 2, а) осуществляется при помощи шаблона и щупа.
Проверку положения боковых сторон шпоночного паза относительно его оси осуществляют при помощи клиновых плиток (рис. 2, б), которые укладывают в паз, а затем щупом контролируют зазоры в точках I и II. При отсутствии перекоса боковых стенок паза зазор должен быть одинаковым.
Отклонение от параллельности стенок шпоночного паза относительно оси вала может быть определен индикаторным прибором (рис. 2, в). При отсутствии отклонения от параллельности показания индикатора на одном и другом конце паза должны быть одинаковы.
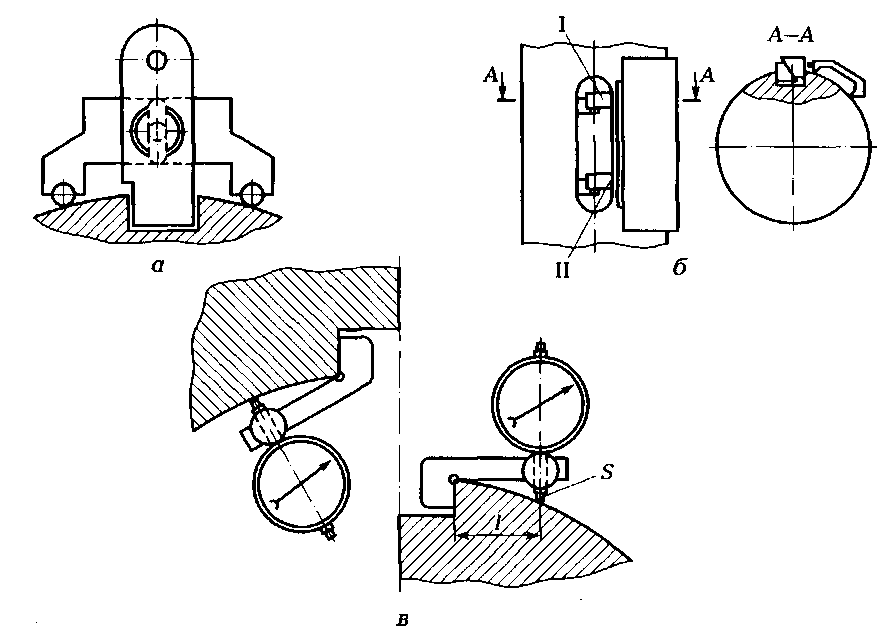
Рисунок 2 - Схемы контроля ответственных соединений со шпонками
а — глубины шпоночного паза; б — положения стенок паза относительно его оси; в — перекоса паза относительно его оси; I, II — точки установки измерительных призм; S — измерительная ножка индикатора; l — расстояние от боковой поверхности шпоночного паза до точки контакта измерительной ножки индикатора с поверхностью вала
Сборку шпоночного соединения начинают с пригонки шпонки по пазу вала, предварительно притупив острые кромки пазов и шпонок. После пригонки шпонку устанавливают в пазу вала, обеспечивая указанную на чертеже посадку. Поскольку, в большинстве случаев, шпонка устанавливается в пазу вала по посадке с натягом, то для ее установки следует использовать медный молоток, струбцину или пресс.
При установке направляющих шпонок следует, используя отверстия под винты, выполненные в шпонке, в качестве кондуктора просверлить отверстия в пазу вала и нарезать в них резьбу для крепежных винтов и после этого закрепить шпонку в пазу вала.
После установки шпонки в паз вала необходимо проверить высоту выступающей части при помощи микрометрической головки и мостика (рис. 3, а). В тех случаях когда на валу устанавливают несколько шпонок, их взаимное положение проверяют так, как это показано на рис. 3, б). На шпонки устанавливают приспособление с раздвижными ножками 2, снабженными цилиндрическими валиками 3, и фиксируют положение ножек винтом 4. По показаниям индикатора часового типа 1 при перемещении приспособления вдоль оси вала по поверхностям шпонок определяют взаимное положение последних (при перемещении приспособления показания индикатора не должны изменяться, т.е, стрелка отсчетного устройства должна оставаться неподвижной).
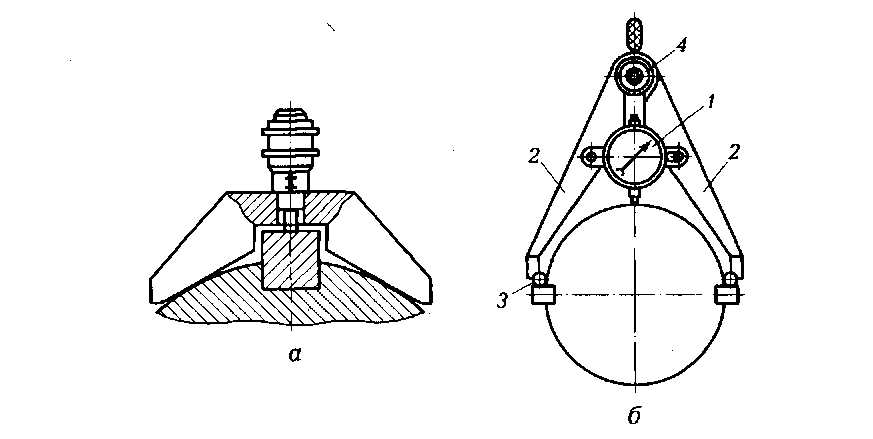
А
Рисунок 3 - Схемы контроля положения шпонок на валу
а — высоты выступающей части; б — взаимного расположения шпонок на валу: 1 — индикатор: 2 — раздвижные ножки; 3 — цилиндрический валик; 4 — винт
Таблица 1. Типичные дефекты при выполнении пригоночных работ
-
Дефект
Причина
Способ предупреждения или исправления
Ступица устанавливается на вал слишком туго
Мала ширина паза ступицы или его глубина
Пригнать более точно паз по шпонке
Для установки шпонки в паз вала требуется слишком большое усилие
Плохо пригнана шпонка
Повторить пригонку шпонки по пазу вала
Шпонка не удерживается на валу
Снят слишком большой слой материала с поверхности шпонки
Заменить шпонку и вновь пригнать ее по пазу вала
Сборка соединений со скользящими шпонками начинается с пригонки шпонки по пазу ступицы и ее установки в этом пазу, после чего осуществляется пригонка паза вала по шпонке. После сборки при перемещении ступицы не должно наблюдаться ее качания относительно вала.
В процессе выполнения пригоночных работ при сборке шпоночных соединений могут появиться различные дефекты, причины появления которых и способы предупреждения приведены в табл. 1.
5 Пригоночные операции слесарной обработки при сборке
Процесс сборки состоит из двух этапов:
1 Подготовка деталей к сборке (очистка, промывка, сушка, слесарно-пригоночные работы)
2 Выполнение соединений сопрягаемых деталей с обеспечением требуемой точности их сопряжения и взаимного положения
Перед соединением деталей необходимо провести подготовку.
Пригонка деталей необходима для компенсирования неблагоприятного суммирования допусков в многозвенной размерной цепи, а также при наличии конструктивных особенностей сопрягаемых деталей.
Шабрение - технология прецизионного (высокоточного) выравнивания поверхности изделия из металла (реже — из дерева или пластика) специальным режущим инструментом — шабером.
Высококачественное шабрение позволяет получить поверхность с неравномерностью порядка единиц микрона. Шабрение практически не поддаётся механизации и остаётся одной из самых трудоемких слесарных работ.
Шабрение выполняют после зачистки поверхности от явных сколов и выбоин. Зачастую перед шабрением производят грубое выравнивание (шлифование) механизированным абразивным инструментом.
Для шабрения деталей на краску используют плиту или линейку, а также краску. В качестве краски для шабрения используют смесь машинного масла с парижской лазурью или ультрамарином, имеющую консистенцию легкой пасты. Иногда используется смесь машинного масла с сажей.
Краска наносится тампоном, сделанным из чистых льняных тряпок, сложенных в несколько раз. Удобно наносить краску также при помощи мешочка, изготовленного из чистого полотна (холста), в который накладывается краска. В тех местах пришабриваемой поверхности, которые несколько углублены, краска будет скапливаться, а места, еще более углубленные, вообще не смачиваются краской.
Так возникают:
- Белые пятна - наиболее углубленные места, не покрытые краской;
- Темные места - менее углубленные, в них скопилась снятая краска;
- Серые места - наиболее выступающие, на них краска ложится тонким слоем.
Шабрение начинают с самых выступающих мест, обозначенных светлым цветом краски. Затем следуют пятна с густой окраской. Светлые пятна не шабрятся.
Шабрение выполняется с помощью образцовой поверхности соответствующего качества (поверочная плита, линейка и т. д.). Процедура состоит из многократного повторения ряда действий:
- Получение яркого рисунка неровностей. Для этого обрабатываемую поверхность слегка притирают с образцовой поверхностью с контрастной краской. В результате краска останется на горбах по которым впоследствии проходят шабером.
- Режущим инструментом снимают видимые выпуклости.
- Качество результата контролируется по количеству цветных пятен краски после притирки на определённой площади. Подразумевается, что чем больше пятен, тем меньше их площадь и, соответственно, меньше неровность.
Качество шабрения определяется с помощью контрольной рамки 25 х 25 мм. Ее накладывают на прошабренную поверхность и считают число пятен: шабрение считается грубым, если пятен в рамке 5–6, чистовым – 6–10 пятен, точным – 10–14 пятен, тонким – более 22 пятен.
После получения требуемого результата на поверхность нередко наносится однообразный рисунок легкими движениями шабера. Этот рисунок позволяет выявить возникающие в процессе эксплуатации изделия дефекты поверхности (вмятины, истирание, срезы). В некоторых изделиях этот рисунок помогает удерживать смазочное масло на детали.
Требования безопасности труда:
- Шаберы не должны иметь трещин и отколов, их рукоятки должны быть чистыми и гладкими. Для предохранения рук от пореза режущей кромкой второй конец двусторонних шаберов необходимо закрывать специальным футляром.
- Во время шабрения следует удалять металлическую пыль или стружку специальной, щеткой.
- Работая механизированными шаберами, необходимо изучить инструкцию по пользованию ими и строго соблюдать указанные там правила техники безопасности.
- Необходимо бережно относиться к контрольно-проверочному инструменту, применяемому при шабрении. Поверхности поверочных плит и линеек должны быть всегда чистыми, их следует оберегать от механических повреждений (забоин, вмятин), попадания на их контрольные плоскости грязи, стружки, а также влаги, что может вызвать коррозию. (Для увеличения срока службы поверочной плиты в работе надо пользоваться всей ее контрольной поверхностью.)
- После окончания работы поверочную плиту и линейки следует промыть керосином, вытереть сухой чистой тряпкой, смазать машинным маслом и положить в футляр.
Притиркой называется обработка деталей, работающих в паре, для обеспечения наилучшего контакта их рабочих поверхностей.
Доводка – это чистовая обработка деталей с целью получения точных размеров и малой шероховатости поверхностей.
Притирка и доводка осуществляются абразивными порошками или пастами, наносимыми на обрабатываемые поверхности, или специальный инструмент - притир.
Припуск на притирку составляет 0,01-0,02 мм, на доводку – 0,001-0,0025 мм.
Точность притирки – 0,001-0,002 мм. Доводка обеспечивает точность по 5-6 квалитетам и шероховатость до Rz 0,05.
Абразивные материалы (абразивы) – это мелкозернистые кристаллические порошкообразные или массивные твёрдые тела, применяемые для механической обработки материалов.
Абразивы делятся на природные и искусственные, и различаемые по твёрдости.
Твёрдые естественные абразивные материалы – это минералы, содержащие оксид алюминия (наждак) и оксид кремния (кварц, кремень, алмаз).
Твёрдые искусственные абразивы – получают в электропечах, имеют высокую твёрдость и однородность состава. К ним относятся: электрокорунды - нормальный (1А); белый (2А); хромистый (3А); монокорунд (4А); карбиды кремния (карбокорунд) зелёный (6С); чёрный (5С); карбид бора (КБ); кубический нитрид бора (КБН); эльбор (Л); алмаз синтетический (АС). Применяют при обработке чугуна, хрупких и труднообрабатываемых материалов.