Файл: Курсовой проект кппсм31012014 2014 Министерство общего и профессионального образования Свердловской области.docx
ВУЗ: Не указан
Категория: Не указан
Дисциплина: Не указана
Добавлен: 24.10.2023
Просмотров: 110
Скачиваний: 2
ВНИМАНИЕ! Если данный файл нарушает Ваши авторские права, то обязательно сообщите нам.
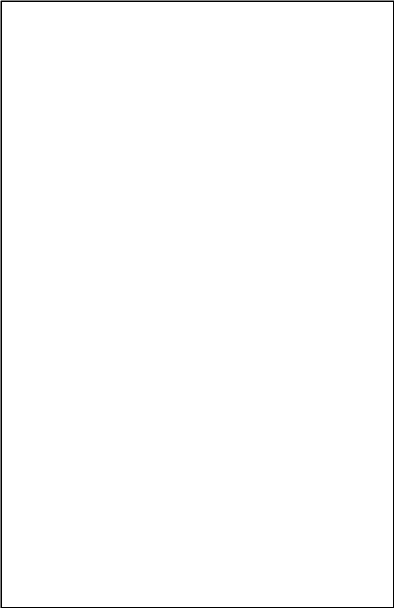
ГАОУ СПО СО «Екатеринбургский колледж транспортного строительства»
Специальность 270809 «Производство неметаллических строительных изделий и конструкций»
Основы расчета установок для тепловлажностной обработки
Курсовой проект
КП-ПСМ-31-01-2014
2014
Министерство общего и профессионального
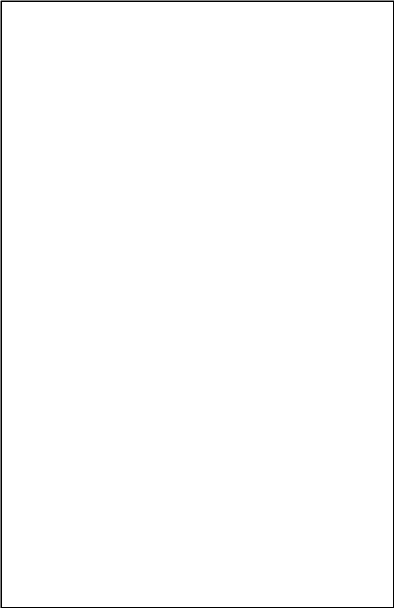
ГАОУ СПО СО «Екатеринбургский колледж транспортного строительства»
Специальность 270809 «Производство неметаллических строительных изделий и конструкций»
Основы расчета установок для тепловлажностной обработки
Пояснительная записка
к курсовому проекту
КП-ПСМ-31-01-2014-ПЗ
Разработала:
Студентка гр.ПСМ-31 _ _ _ _ _ _/Н.П.Андронаки
Руководитель: _ _ _ _ _ _/Т.Г.Михайлова
Консультанты:
Н.Контроль:
2014
Задание на курсовое проектирование
Исходные данные: наименование изделия
Qгод = 11000м3
Плотность бетона – 2350кг/м3
Влажность – 7%
Расход цемента марки М400 – 420кг
Водоцементное отношение - В/Ц = 0,6
Удельная теплоёмкость бетона Сб = 0,9кДж/(кг × К)
Удельная теплоёмкость кирпича Скр = 0,8кДж/(кг × К)
Масса металла (поддоны, арматура), загружаемого в форму – 0,14748 т
Металлоёмкость форм – 2,1 т/м3
Удельная теплоёмкость металла – 0,48 кДж/(кг × К)
Продолжительность подъёма температуры – 2ч
Продолжительность изотермического прогрева – 4ч
Охлаждение – 3ч
Период тепло - обработки – 6ч
ТВО = 9ч (2 + 4 + 3)
Полный цикл – 9ч
Пар из паропровода поступает с давление - 0,2МПа
Влажность -W15%
Температура пропаривания – 373К
Давление отработанного пара - 0,1МПа
Средняя температура наружной поверхности – 313К
Температура конденсата – 353К
Температура воздуха в цехе – 293К
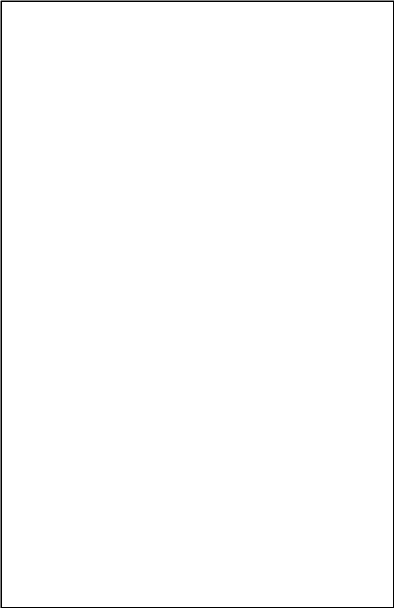
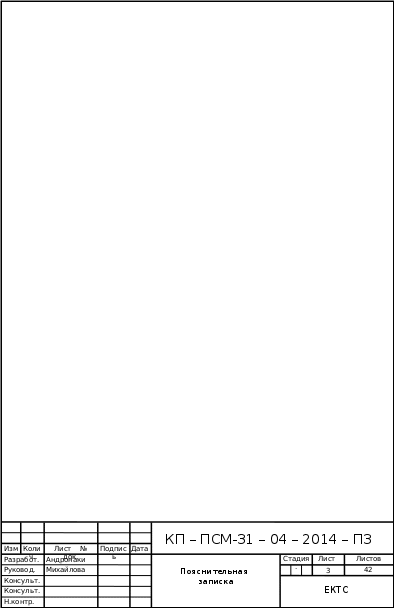
Введение
Целью курсового проектирования является изучение конструкций тепловых установок и приобретение навыков их проектирования.
Задачи курсового проектирования:
-
Изучение литературы по устройству и принципах работы тепловых установок. -
Выбор конструкции установки, и анализ эффективности установки; -
Проведение технологических расчетов; -
Проведение теплотехнических расчетов; -
Технико-экономический анализ и заключение об эффективности запроектированной установки.
По заданию требуется запроектировать установку периодического действия обеспечивающую производительность 11000 м3 в год. Существуют 4 типа ямных камер.
По заданию запроектирована установка: камера Л.А.Семенова, с интенсивной циркуляцией среды.
Курсовой проект содержит пояснительную записку на 21 листах и графическая часть на 1 листе.
1 Общая часть
Тепловая установка предназначена для тепловлажностной обработки панелей шахт-лифтов ПШЛ 100-42-1 (эскиз изделия см.рис.1). Характеристика изделия дана в таблице 1.
Таблица 1- Характеристика изделия
Наименование и маркировка | Класс (марка) бетона | Габаритные размеры, мм | Объем бетона, м3 | Расход стали, кг | Масса изделия, т |
1 панель шахт-лифтов ПШЛ100-42-1 | В25 (М350) | 2510×4180×140 | 1,04 | 147,48 | 2,6 |
В проекте предусмотрена ямная камера Семенова. Она имеет прямоугольную форму иногда со скругленными углами для улучшения циркуляции теплоносителя. Высота камер обычно не более 4м, ширина 1,5-4м, длина 7-13м. Как правило, ямные камеры заглублены в землю на 0,5-2,0м. Пол камеры бетонный с гидроизоляцией и слоем утеплителя имеет уклон 0,005-0,01 для стока конденсата. Стены обычно железобетонные с отверстиями для подключения к вентиляционному каналу, сообщения с атмосферой в период охлаждения и для ввода паропровода (в данном проекте - кирпичные). Сверху камеру закрывают съемной крышкой, представляющей собой жесткую рамную конструкцию, заполненную теплоизоляцией. Для создания паронепроницаемости нижняя поверхность крышки обшита стальным листом. Крышку делают с уклоном 0,005-0,01, чтобы капли конденсата с нее не попадали на поверхность изделия. Уплотнение между крышкой и камерой выполнено в виде гидравлического или песочного затвора, представляющего собой желоб, образованный швеллерными балками, уложенными по периметру стен. Желоб заполняют водой или песком, в которые погружены края крышки. Повышение температуры в камере приводит к увеличению в ней давления, что может привести к нарушению герметизации и выбиванию пара в помещение цеха. Для этого предусмотрено устройство обратной трубы, соединенной со специальным гидравлическим затвором. В случае повышения давления в камере излишек пара выбрасывается через трубу. Подачу пара
производят через перфорированные трубы, расположенные у пола и верха камеры, по периметру или двум длинным ее сторонам. Диаметр отверстий 3-5мм. Большое влияние на теплообмен в ямной камере оказывает интенсивная циркуляция теплоносителя. Для улучшения циркуляции пара в камере и повышения дальнобойности струи рекомендуют отверстия в перфорированных трубах делать в виде сопл и направлять выходящие из них струи пара вдоль поверхности изделий, что в силу инжектирующего действия усиливает циркуляцию пара между рядами изделий. В целях уменьшения сопротивления движения пара расстояние между формами рекомендуют иметь не менее 50мм. Нижняя форма отстоит от пола камеры на 200мм для снижения воздействия холодного пола. Камеры оборудованы стойками типа СМЖ-293 с поворотными кронштейнами для укладки изделий.
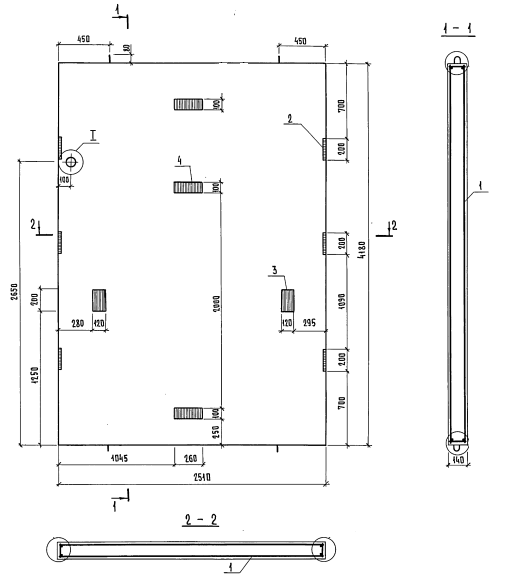
Рисунок 1 –
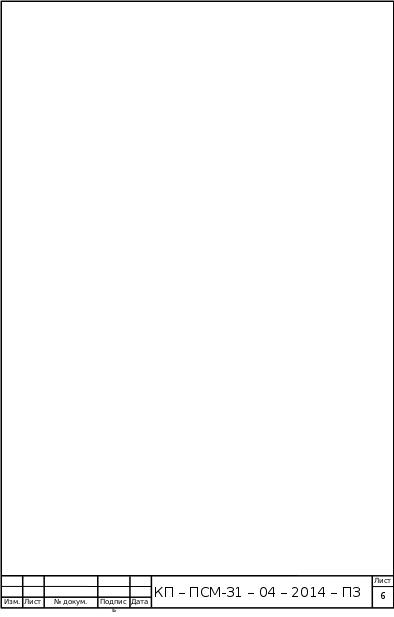
Принцип работы ямной камеры состоит в следующем. После очередной загрузки камеры изделиями крышку закрывают и начинают впуск пара. Ввиду того что весь свободный объем камеры до этого был заполнен воздухом, в первый период тепловлажностной обработки сказывается вредное влияние воздуха- понижаются коэффициент теплоотдачи и скорость подъема температуры. Пока парциальное давление пара в паровоздушной смеси не достигнет максимального значения, т.е. пока весь воздух не будет вытеснен из камеры и ее не заполнят, чистым паром, температура при атмосферном давлении не достигнет 373К (100˚С). Следовательно, в период подогрева изделий увеличение температуры связано с вытеснением ее паром. Период подогрева завершится, когда поверхность изделий нагреется до температуры теплоносителя. Во втором периоде тепловлажностной обработки количество подаваемого пара меньше, чем в первом. В этот период происходит выравнивание температур по сечению изделий. По окончанию периода изотермической выдержки подачу пара прекращают. В период охлаждения камеры вентилируют. Остывшие изделия выгружают, и цикл повторяют снова.
Одним из условий рационального расхода пара на тепловлажностную обработку изделий в ямных камерах, а также на создание равномерного нагревания этих изделий является организация подачи пара. Неравномерное температурное поле в камере приводит к неодинаковому нагреванию изделия, а значит и к разной прочности. Поэтому большое внимание уделяется организации подачи пара в ямные камеры.
Существуют различные схемы снабжения паром ямных камер.
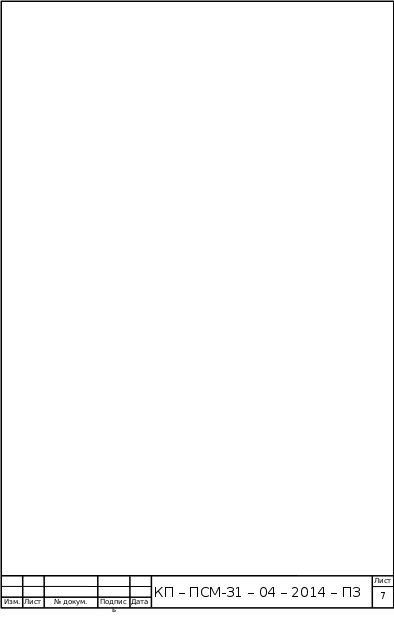
2 Расчетная часть
2.1 Технологические расчеты
В цехе предусмотрена агрегатно-поточная технология .
-
Определить часовую производительность формовочного агрегата по формуле:
Пч =
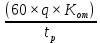
где 60 – количество минут в часе;
q – объем бетона изделий формуемых одновременно на 1-ом формовочном агрегате;
Кот = 1,015 , коэффициент отхода б/с;
tp – ритм работы формовочной линии, минуты;
Пч =
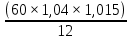
-
Определить количество формовочных агрегатов:
Z =

где Qгод – годовая производительность линий, м3/год;
m = 253, количество рабочих суток в году;
y = 16 часов, количество рабочих часов в сутки для двухсменной работы;
Пч – часовая производительность формовочного агрегата , м3/час.
Для курсового проекта обосновывается выбор типа камеры, дается ее преимущества и краткое описание.
Z =
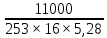
= 0,51 шт, берем 1 шт;
-
Определяем внутренние размеры камеры:
Lк = n×L+(n+1)×l ,м,
где Lк – внутренняя длина камеры, м;
n – количество изделий (форм) укладываемых по длине , шт (если L>4, то n =1);
l = 0,35-0,40 м (принимать одну единицу), расстояние между изделием и стенкой камеры с учетом формы и зазора;
Lк = 2×2,51+(2+1)×0,4=6,22 м;
Bк = n1×B+(n1+1)×b, м,
где Bк – внутренняя ширина камеры, м;
n1 – количество изделий по ширине камеры, шт, (если B>2 , то n=1),
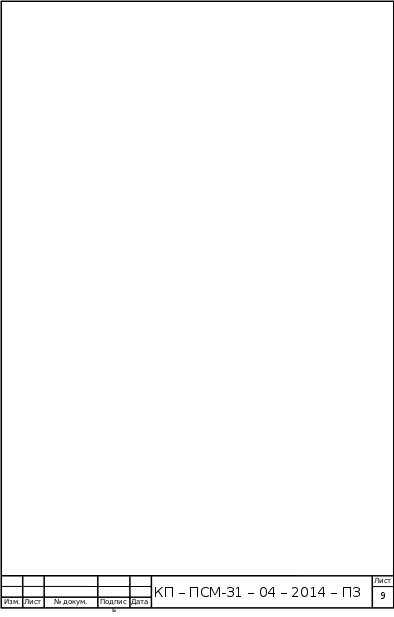
Bк = 1×4,18+(1+1)×0,4=4,98 м;
Hк = n2×(H+H1)+H2+H3 , м,
где Hк – внутренняя глубина камеры , м;
n2 – число рядов изделий по высоте камеры (принимается из расчета, чтобы высота получилась около 3 м; учесть, что нижняя форма ставится на бруски толщиной 100×100; 100×150 мм, затем ставится форма на форму без прокладок или учитывают автоматические кронштейны. Кронштейны применяются при немедленной распалубке, когда изделие отправляют в камеру на поддоне, должны учесть зазор между поверхностью изделия и крышкой);
H – высота изделия, м;
H1 = 0,2-0,3 м, расстояние между изделиями по высоте с учетом формы и зазора (выбирать конкретную цифру для расчета);
H2= 0,15 м, расстояние между нижней формой и полом камеры, т.е. размер бруска;
H3=0,15 м, расстояние между верхом изделия и крышкой камеры;
Hк = 6×(0,14+0,3)+0,15+015= 2,94 м;
-
Определить полезный объем камеры:
Vк = q×n3 , м3,
где q – объем одного изделия по бетону;
n3 – количество изделий в камере, шт (не забыть учесть количество изделий по длине и ширине);
Vк = 1,04×12=12,48 м3;
-
Определить продолжительность цикла камеры:
tц.к = t1 + t2 + t3 +t4 +t5 +t6 , ч,
где t1 – время загрузки камеры, ч;
t1 =

где Vк – полезный объем камеры м3 ;
Z – количество формовочных агрегатов в пролете , шт;
Пч – часовая производительность агрегата , м3/ч;
tтр – время транспортировки изделий и установки крышки камеры: на каждое перемещение 2-3 минуты берется:
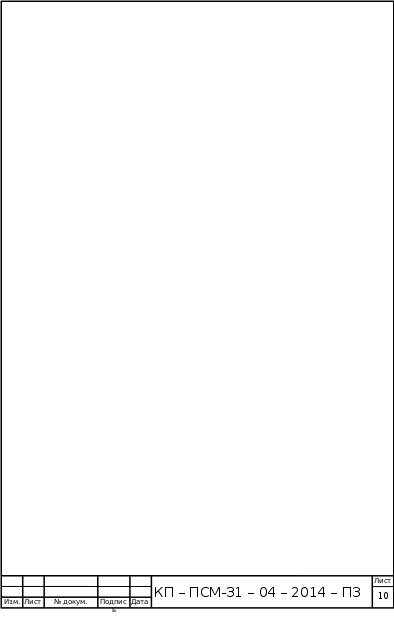