Файл: Технологический процесс изготовления коптильни из листового металла s 8мм и уголков 25х25х2 ручной дуговой сваркой.docx
ВУЗ: Не указан
Категория: Не указан
Дисциплина: Не указана
Добавлен: 26.10.2023
Просмотров: 64
Скачиваний: 4
ВНИМАНИЕ! Если данный файл нарушает Ваши авторские права, то обязательно сообщите нам.
Из уравнения видно, что сталь хорошо сваривается и не дает трещин, не требует предварительного нагрева.
Свариваемость – свойство металла или сочетания металлов образовывать при установленной технологии сварки соединение, отвечающее требованиям, обусловленным конструкцией и эксплуатацией изделия. В зависимости от назначения и нагрузок изделия выбирают материал из которого оно будет изготовлено. Таким образом, для изготовления ограждения использовалась сталь марки Ст3сп низкоуглеродистая, относится к группе хорошо свариваемых. Углерода в ней до 0,25 % , марганца 0,5% , кремния 0,35%. Чаще всего прокат из данной марки стали используется для разнообразных строительных конструкций благодаря высокой механической прочности, что позволяет использовать более тонкие элементы, чем при использовании других сталей.
1.3 Выбор и обоснование подготовительных операций
Технологический процесс заготовок деталей из проката может включать следующие операции: правку, разметку, резку, обработку кромок и очистку под сварку.
Правка осуществляется за счет создания местной пластической деформации и, как правило, производится в холодном состоянии. Для устранения волнистости листов и полос толщиной от 0,5 до 50мм широко используют многовалковые машины с числом валков больше пяти. Правку мелко- и среднесортного и профильного проката производят на роликовых машинах, работающих по той же схеме, что и листоправильные. Для изготовления решетки правка металла не осуществлялась, так как использовался новый профильный прокат.
Разметка. Использование приспособлений для мерной разметки проката обеспечивает экономию времени. Слесарная операция заключается в нанесении на поверхность заготовки углублений (кернов) и линий (рисок), определяющих контуры изготовляемой детали или места, подлежащие обработке. По рискам с заготовки при обработке удаляют припуск. Разметку осуществляют главным образом в индивидуальном и мелкосерийном производствах. Для разметки квадратного профиля при изготовлении деталей оконной решетки был использован разметочный материал: чертилка, керн, металлическая линейка и рулетка.
Резка, разделка кромок . Резкой металлов называют отделение частей (заготовок) от сортового, листового или литого металла.
Для поперечной резки фасонного проката применяют пресс-ножницы с фасонными ножами или дисковые пилы. В некоторых случаях применяют резку гладким диском.
Так же применяют разделительную кислородную резку. Ручная и полуавтоматическая резка производится обычно по разметке, автоматическая – с помощью копирных устройств и по масштабному чертежу. Кислородная резка используется и при подготовки кромок под сварку. Если эта операция совмещается с разделительной резкой, то односторонний скос с притуплением получают, используя одновременно два резака, а двусторонний скос – при трех резаках. После вырезки детали иногда приходится править.
Механическая обработка кромок обычно производится на станках, либо с помощью «болгарки» (Рис 2), которая необходима:
а) для обеспечения требуемой точности сборки;
б) для образования фасок, имеющих сложные очертания;
в) для удаления металла кромок, обрезанных ножницами или с помощью кислородной резки, когда это считается необходимым.
В данной работе для резки заготовок для оконной решетки использовалась механическая «болгарка».
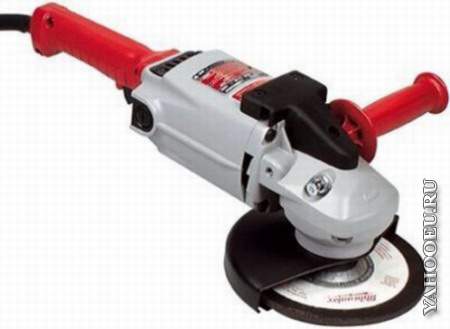
Рисунок 2 – Механическая «болгарка» с отрезным диском
Очистка металла от загрязнений является трудоемкой операцией. Существуют следующие способы очистки: ручным инструментом механическими щетками, абразивными кругами.
Очистка поверхности от загрязнений и ржавчины на заготовках для изготовления ограждения осуществляется угло — шлифовальной машинкой. Для удаления заусенцев, снятие усиления шва и удаления окалины на небольших поверхностях используется очистка абразивными кругами.
Перед сборкой стыка свариваемые кромки на ширину до 20мм зачищают до металлического блеска и обезжиривают.
Сборка. В процессе изготовления сварных конструкций должны быть обеспечены заданные технологическим процессом взаимное положение соединяемых деталей и условия, наиболее благоприятные для образования качественного соединения. Это достигается применением технологических приспособлений и оснастки.
Технологические приспособления делятся на сборочные, предназначенные для сборки под сварку и фиксации деталей при помощи прихваток (или простейших механических устройств); сварочные, предназначенные для сварки заранее собранных деталей с зафиксированным взаимным положением и сборочно-сварочные, позволяющие совместить операции сборки и сварки.
Сборка металлоконструкций – трудоемкая операция, требующая большой точности, особенно при сборке решетчатых конструкций. Конструкции собирают по технологическим чертежам металлоконструкций на стеллажах или на сборочных стендах.
Конструкция ограждения была выполнена из квадратного профиля с помощью сборочных приспособлений.
В качестве приспособлений применялись зажимы, стяжки, угольник.
Из профиля 10*10 собираем раму (контур) ограждения по её размерам. Сборку осуществляем в соответствии размеров по сторонам и диагоналям, это можно сделать при помощи угольника и рулетки. Если все размеры совпадают, то детали нужно зафиксировать помощью зажимов, а затем прихватками.
2 Специальная часть
2.1 Выбор и обоснование способа сварки
Способ сварки выбираем из условия требуемых эксплуатационных свойств конструкции (точность, прочность, надежность), и конструктивными особенностями, применяемых материалов. При выборе способа сварки так же руководствуются видом производства, производительностью процесса и программой выпуска.
Выбор того или иного способа сварки зависят от следующих факторов:
-толщины свариваемого материала;
-протяжённости сварных швов;
-требований к качеству выпускаемой продукции;
-химического состава металла.
Среди способов электродуговой сварки наиболее употребляемыми являются:
-ручная дуговая сварка;
-полуавтоматическая сварка в среде защитных газов;
-автоматическая сварка в среде защитных газов и под флюсом.
Ручная дуговая сварка (РДС) из за низкой производительности и высокой трудоёмкости не приемлема в серийном и массовом производствах. Она используется в основном в единичном и мелкосерийном производстве. Сварка элементов ограждения должна осуществляться механизировано на больших производственных площадях. Единичные экземпляры ограждений небольших размеров можно выполнить ручной дуговой сваркой.
Из различных способов сварки выбираем ручную дуговую сварку штучным электродом. Этот способ характеризуется наименьшими суммарными материальными затратами на материалы, энергию и оборудование.
Для правильного выбора сварочного оборудования необходимо рассчитать и выбрать режим сварки, а также систему регулирования и управления требуемых характеристик оборудования (мощность, пределы регулирования режимов, форма внешней характеристики для источника питания).
Параметрами расчета режимов сварки ручной дуговой сварки являются: диаметр электрода
д э , род и полярность тока, величина сварочного тока I св , напряжение на дуге U д , число проходов n (при многопроходной сварке), площадь наплавленного за один проход металла F н ..
Обычно толщина сварных соединений, выполняемых за один проход ручной дуговой сварки, не превышает 6мм ( S ≤ 6мм), катет углового шва в тавровых и нахлесточных соединениях не превышает 8 мм ( k ≤ 8мм).
При многопроходной ручной дуговой сварки максимальное поперечное сечение, наплавляемое за один проход, не должно превышать 30 мм 2 ( F н ≤30мм 2 ).
Диаметр электрода рекомендуется выбирать по таблице 2, в зависимости от толщины металла, либо от величины катета.
Таблица 2 — Зависимость диаметра электрода от толщины металла и катета
Толщина металла ( S ) равна 3 мм, отсюда д э ,= 3 , при сварке углового соединения (У4) катет k =3мм.
Силу сварочного тока рассчитываем по формуле:
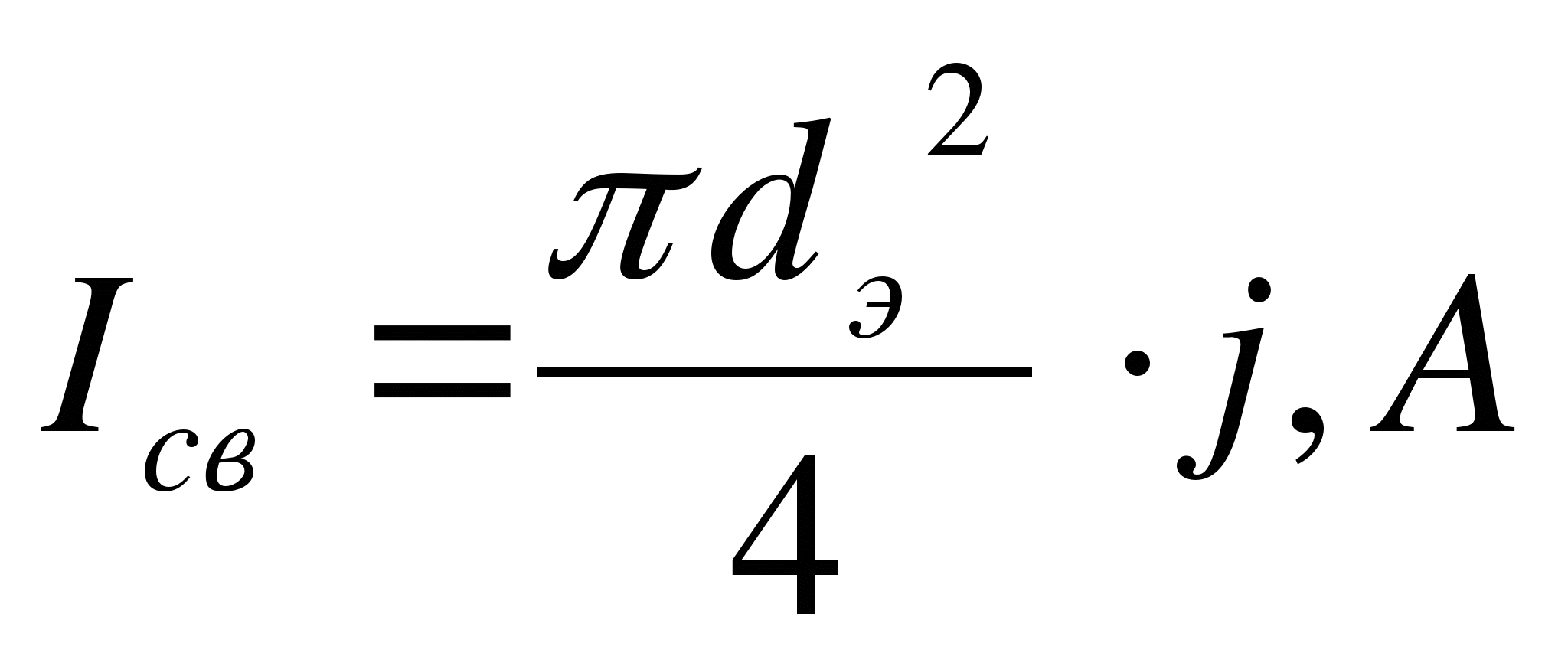
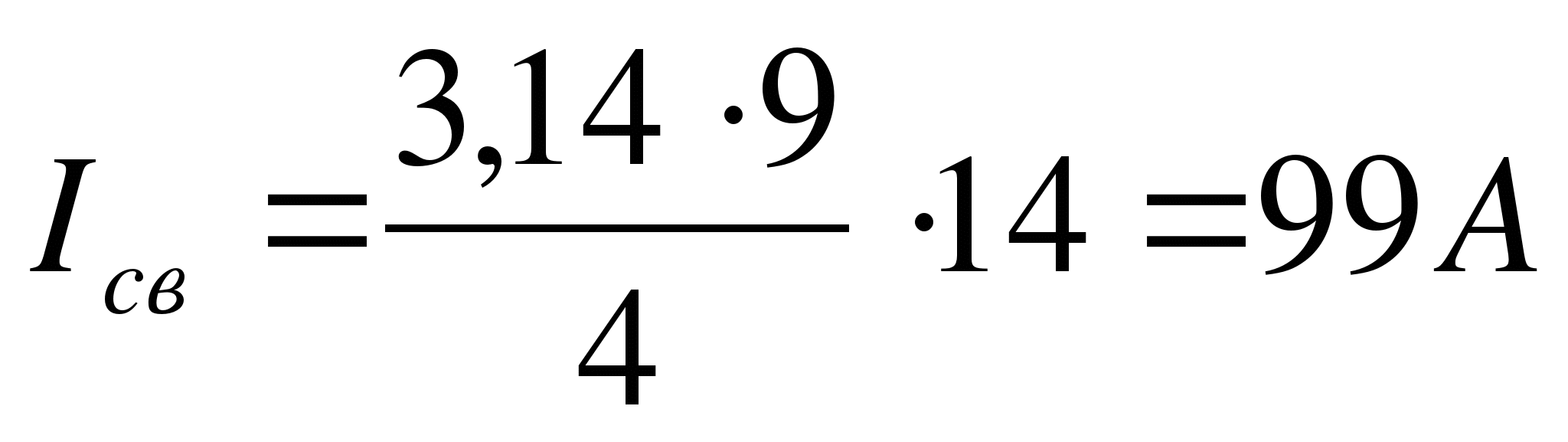
Напряжение на дуге ручной дуговой сварки выбирают по паспорту электрода в пределах от 20 до 36В.
Режимом сварки называется совокупность характеристик сварочного процесса, обеспечивающих получение сварных соединений заданных размеров, форм, качества. При всех дуговых способах сварки такими характеристиками являются следующие параметры: диаметр электрода, сила сварочного тока, напряжение на дуге, скорость перемещения электрода вдоль шва (скорость сварки), род тока и полярность. При механизированных способах сварки добавляется ещё один параметр — скорость подачи сварочной проволоки, а при сварке в защитных газах — удельный расход защитного газа.
Параметры режима сварки влияют на форму, и размеры шва. Поэтому, чтобы получить качественный сварной шов заданных размеров, необходимо правильно подобрать режимы сварки, исходя из толщин свариваемого металла, типа соединения и его положения в пространстве. На форму и размеры шва влияют не только основные параметры режима сварки; но также и технологические факторы, как род и плотность тока, наклон электрода и изделия, вылет электрода, конструкционная форма соединения и величина зазора.
Расчёт режима сварки производится всегда для конкретного случая, когда известен тип соединения, толщина свариваемого металла.
2.2 Выбор сварочного оборудования для изготовления конструкции
Ручная электродуговая сварка в настоящее время остается одним из самых распространенных способов сварки. Это объясняется возможностью сварки в различных пространственных положениях и в местах, недоступной для механизированных способов сварки, также простотой и мобильностью применяемого оборудования.
Для выполнения сварочных работ и изготовления оконной решетки использовался выпрямитель ВДМ – 1601 (Приложение 2) , так как он наиболее удобен. При использовании выпрямителя легко можно подобрать силу тока.
Выбор источника питания зависит от внешней вольт — амперной характеристики. Работа выполнялась ручной дуговой сваркой, используя выпрямитель, имеющий жесткую вольт — амперную характеристику.
Сварочный выпрямитель многопостовой ВДМ–1601 предназначен для питания сварочной дуги постоянным током, от сети трехфазного переменного тока при ручной дуговой сварки. Он состоит из сварочного трансформатора с подвижной первичной катушкой, выпрямительного кремниевого блока с вентилятором, пусковой и защитной аппаратуры. При параллельном соединении обмоток в электрическую цепь получают диапазон больших токов (рисунок 3). Первичная обмотка подвижна, с помощью ее ведется регулирования силы тока.
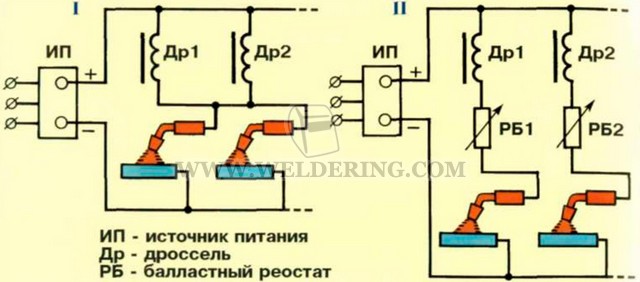
Рисунок 3 — Электрическая схема подключения выпрямителя
Техническая характеристика выпрямителя ВДМ 1601
Напряжение 3×380 В
Частота 50 Гц
Номинальный сварочный ток 1600 А (100%)
Коэффициент одновременности работы постов 0,5
Номинальный сварочный ток одного поста 315 А (100%)
Количество одновременно работающих постов 9 шт
Напряжение холостого хода 75 В
Номинальное рабочее напряжение 60 В
Потребляемая мощность 96 кВА
Коэффициент полезного действия, не менее 80 %
Габаритные размеры 1010х690х810 мм
Масса 300 кг
Для выполнения работы целесообразно для изготовления ограждения в качестве сварочного оборудования, использовать сварочной выпрямитель, сварочный инвертор, так как при постоянном токе удобно проводить сварочные работы.
2.3 Выбор сварочных материалов
Для сварки низкоуглеродистых сталей применяются электроды марок: ОЗС – 3; ОЗС – 4 ; МР – 3, стержень этих электродов изготовлен из проволоки марки СВ – 08А. В состав покрытия входит: 30 – 50% двуокиси титана, полевой шпат, ферромарганец, жидкое стекло. Эти электроды дают наименьшей процент разбрызгивания металла, они пригодны для сварки на постоянном и переменном токе и не вредны для организма человека, поэтому широко используются в промышленности.