ВУЗ: Не указан
Категория: Не указан
Дисциплина: Не указана
Добавлен: 07.11.2023
Просмотров: 88
Скачиваний: 1
ВНИМАНИЕ! Если данный файл нарушает Ваши авторские права, то обязательно сообщите нам.
СОДЕРЖАНИЕ
Параметры и конструкция шкивов
5 Выбор конструкций корпусных деталей редуктора и их расчет
6 Выбор конструкции и ориентировочный расчет валов. Подбор параметров шпоночных соединений
7 Выбор подшипников качения и эскизная компоновка редуктора
8 Проверочные расчеты валов, подшипников, шпоночных соединений
.
Согласно требованиям расчета должно выполняться условие:
− условие выполняется
Определяем окружную скорость ремня V м/с
(3.3)
где D1 – диаметр ведущего шкива, мм;
ω1 – угловая скорость вращения ведущего шкива, с-1.
<30 м/с
Определяем минимальное максимальное и минимальное межосевое расстояние
amin = 0.55 · (D1+D2) + h (3.4)
amax= 2 · (D1 + D2) (3.5)
где h– высота ремня (h= 8.0 по таблице 7), мм.
amin=0,55 · (90+250)+ 8 = 195 мм;
amax=2 · (90+250) =680 мм.
Принимаем межосевое расстояние aпр=400 мм.
Определяем требуемую длину ремня, мм
Округляем полученное значение до стандартного, принимаем L=1400 мм.
Уточняем действительное межосевое расстояния, соответствующее
принятой стандартной длине ремня:
Определяем угол обхвата на малом шкиве
(3.6)
где [α] =120°;
Угол обхвата ремнем малого шкива удовлетворяет необходимым условиям
Определяем требуемое число ремней
[Р] = Р0∙Кα∙Кр (3.7)
где Р0 – значение мощности, передаваемое одним ремнем, Р0 = 3,39 кВт (таблица 7.6);
Кα – коэффициент, учитывающий влияние угла обхвата;
Кα = 0.0029∙α +0.4846 = 0.0029 ∙ 157 + 0.4846 = 0,94;
Кр –коэффициент, учитывающий влияние режима работы Кр = 1,0 (таблица 7.3)
[Р] = 3,39 ∙ 0,94 ∙ 1,0 = 3,19 кВт,
Проверка частоты пробегов ремня на шкивах (на долговечность)
Определяем силу предварительного натяжения одного ремня, Н
(3.8)
где
– масса 1 м длины ремня = 0.105 кг (таблица 7.5)
.
Сила, действующая на вал:
Н (3.9)
30>
Ширина обода
В = (Z – 1) ∙ t + 2 · f = (3 – 1) ∙ 15 + 2 ∙ 10 = 50 мм.
Диаметр ступицы
dст =(1.6 – 2.0) ∙ dв= 1,6∙ 24 = 38,4 мм.
Длина ступицы
мм.
Принимаем lст=40 мм.
Основные размеры профиля канавок для клиноременных шкивов регламентированы ГОСТ 20898 в зависимости от профиля сечения ремня. В нашем случае все основные размеры приведены в таблицу 3.1.
Таблица 3.1− Основные размеры профиля канавок для клиноременных шкивов
4.1 Выбор материала и допускаемых напряжений
Ввиду того, что в червячном зацеплении преобладает трение скольжения, применяемые материалы червячной пары должны обладать хорошими антифрикционными свойствами, повышенной износостойкостью и пониженной склонностью к заеданию. Для этого в червячной передаче сочетают разнородные материалы при малой шероховатости контактирующих поверхностей.
Червяки изготавливают из среднеуглеродистых сталей марок 40, 45, 50 или легированных сталей марок 40Х, 40ХН и др. с поверхностной закалкой до твердости HRC 45-55. При этом необходима шлифовка и полировка рабочих поверхностей витков. Хорошую работу передачи обеспечивают червяки из цементируемых сталей (15Х, 20Х и др.) с твердостью после закалки 58-63 HRC.
Зубчатые венцы червячных колёс изготавливают преимущественно из бронзы, причем выбор марки материала определяется скоростью скольжения (Vs = 6-25м/с) и при длительной работе рекомендуются оловянные бронзы марок БрОФ10-1, БрОНФ, которые обладают хорошими противозадирными свойствами. При средних скоростях скольжения (Vs = 2-6 м/с) применяют алюминиевую бронзу марки БрАЖ 9-4. Эта бронза обладает пониженными противозадирными свойствами, в отдельных случаях её применяют при Vs до 8 м/с.
При малых скоростях скольжения (Vs < 2 м/с) червячные колеса можно изготавливать из серых чугунов СЧ12, СЧ15, СЧ18 и др.
Vs ≈ 4.5 ·10-4 · n1 ·
, (4.1)
где Т2 – крутящий момент на валу червячного колеса,
n1 – частота вращения вала червяка,
Т2 = 1596,7 Н.м;n1 = 1000 мин-1;
Выбираем материал I-й группы БрО10Ф1. Способ отливки –литье в кокиль.
σв = 230 МПа,
σт = 140 МПа.
Для I-й группы материалов [8, с.356]
(4.2)
здесь
,
.
Принимаем
.
.
4.2 Проектировочный расчет червячной передачи
При проектировочном расчете определяют ориентировочное значение межосевого расстояния червячной передачи, исходя из контактной выносливости поверхности зубьев, а затем, после уточнения параметров передачи, проверяют действительные контактные напряжения и сравниваются с допускаемыми.
Расчетное межосевое расстояние определяем
, (4.3)
где Z2 – число зубьев червячного колеса;
q – коэффициент диаметра червяка,
КН – коэффициент нагрузки,
Т2 – крутящий момент на валу червячного колеса, Н∙м
[σH] – допускаемое контактное напряжение, МПа.
q = 10; КН = 1,1. [1, c.68]
Z2 = Z1 ∙ U, (4.4)
Z2 = 2∙ 25 = 50.
Определяем осевой модуль зацепления:
(4.5)
Полученный модуль округляют до стандартного по ГОСТ 2144–76,
mст = 8 мм.
Уточняем межосевое расстояние:
.
(4.6)
Определяем скорость скольжения в зацеплении:
, (4.7)
где d1 – делительный диаметр червяка, мм;
γ – угол наклона винтовой линии, град.
(4.8)
d1 = 8 ∙ 10 = 80 мм,
(4.9)
Определяем степень точности в зависимости от назначения передачи, условий ее работы и возможности производства. Принимаем степень точности равную 8.
Условие прочности по контактным напряжениям имеет вид:
Согласно требованиям расчета должно выполняться условие:
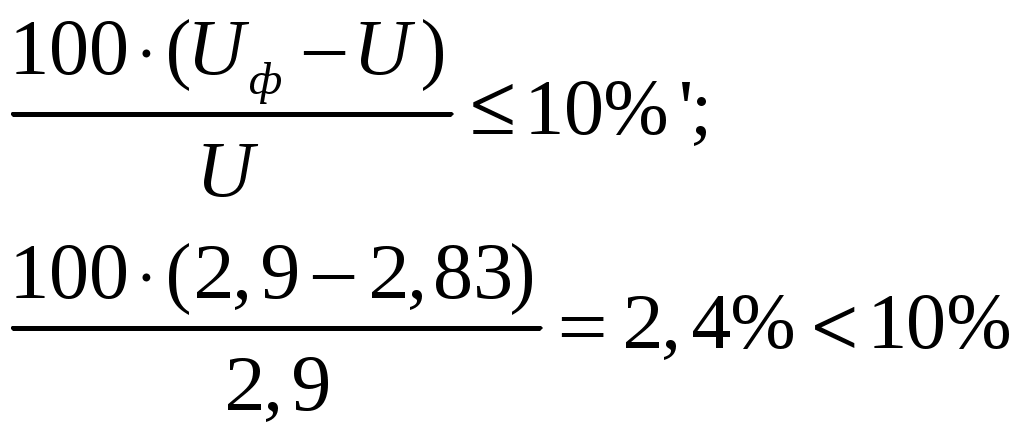
Определяем окружную скорость ремня V м/с
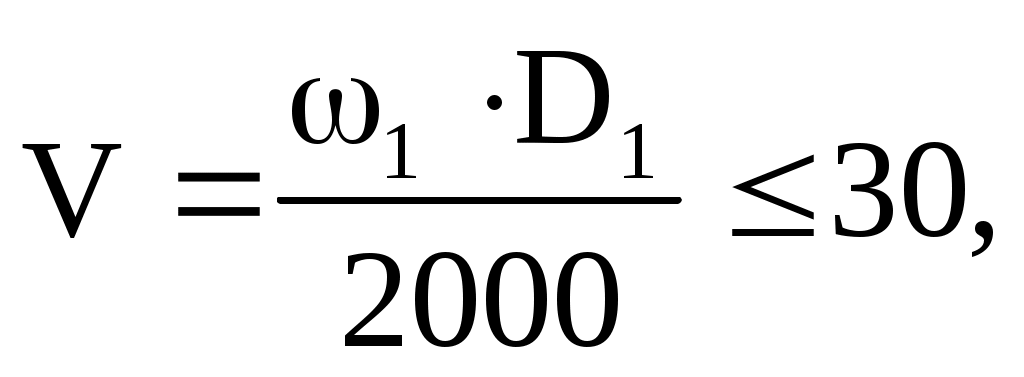
где D1 – диаметр ведущего шкива, мм;
ω1 – угловая скорость вращения ведущего шкива, с-1.
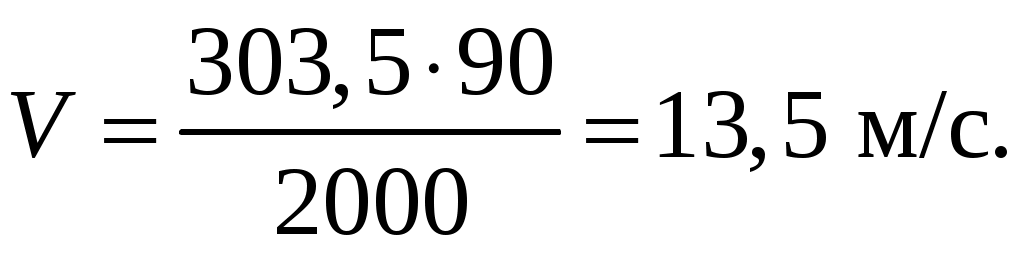
Определяем минимальное максимальное и минимальное межосевое расстояние
amin = 0.55 · (D1+D2) + h (3.4)
amax= 2 · (D1 + D2) (3.5)
где h– высота ремня (h= 8.0 по таблице 7), мм.
amin=0,55 · (90+250)+ 8 = 195 мм;
amax=2 · (90+250) =680 мм.
Принимаем межосевое расстояние aпр=400 мм.
Определяем требуемую длину ремня, мм
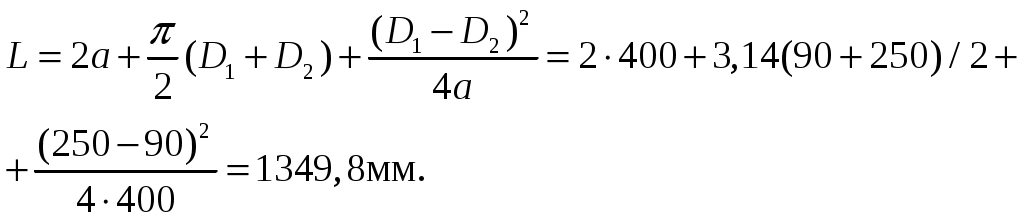
Округляем полученное значение до стандартного, принимаем L=1400 мм.
Уточняем действительное межосевое расстояния, соответствующее
принятой стандартной длине ремня:

Определяем угол обхвата на малом шкиве
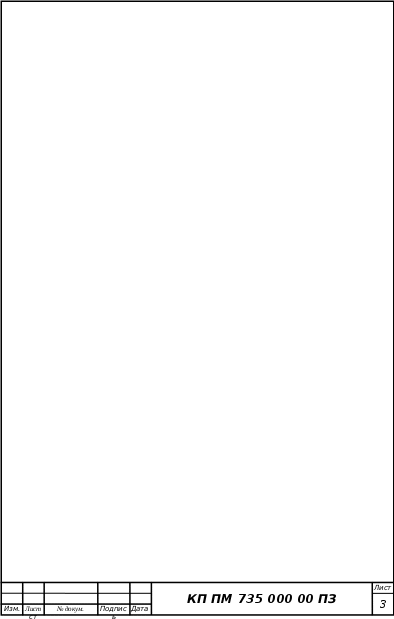
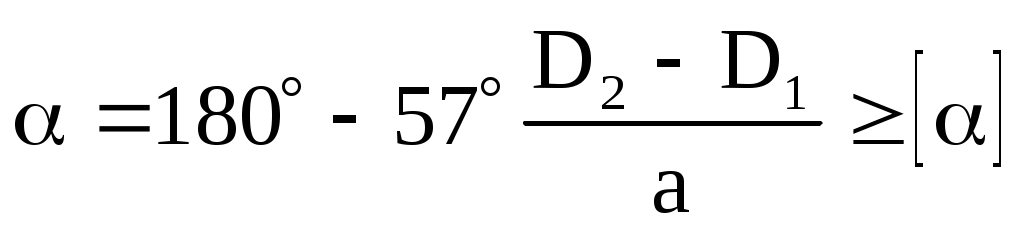
где [α] =120°;

Угол обхвата ремнем малого шкива удовлетворяет необходимым условиям
Определяем требуемое число ремней
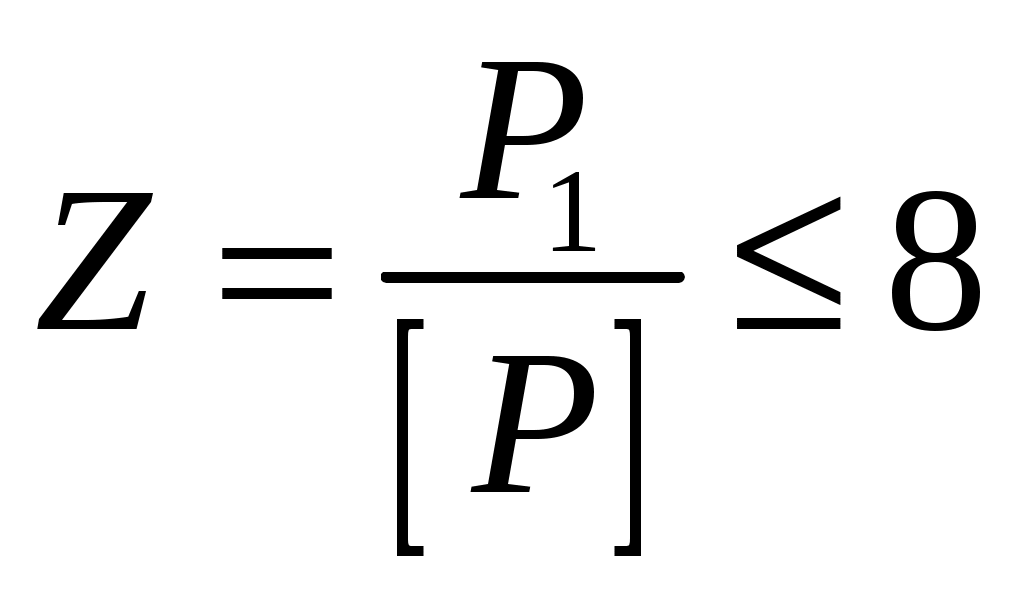
[Р] = Р0∙Кα∙Кр (3.7)
где Р0 – значение мощности, передаваемое одним ремнем, Р0 = 3,39 кВт (таблица 7.6);
Кα – коэффициент, учитывающий влияние угла обхвата;
Кα = 0.0029∙α +0.4846 = 0.0029 ∙ 157 + 0.4846 = 0,94;
Кр –коэффициент, учитывающий влияние режима работы Кр = 1,0 (таблица 7.3)
[Р] = 3,39 ∙ 0,94 ∙ 1,0 = 3,19 кВт,
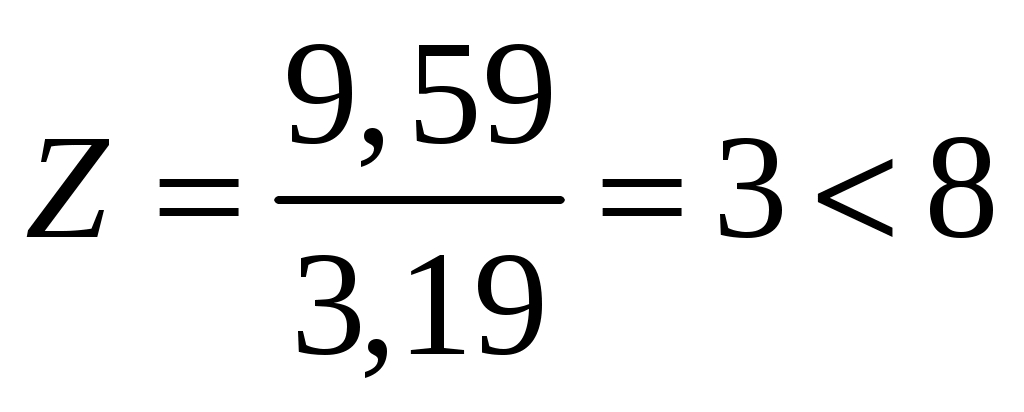
Проверка частоты пробегов ремня на шкивах (на долговечность)
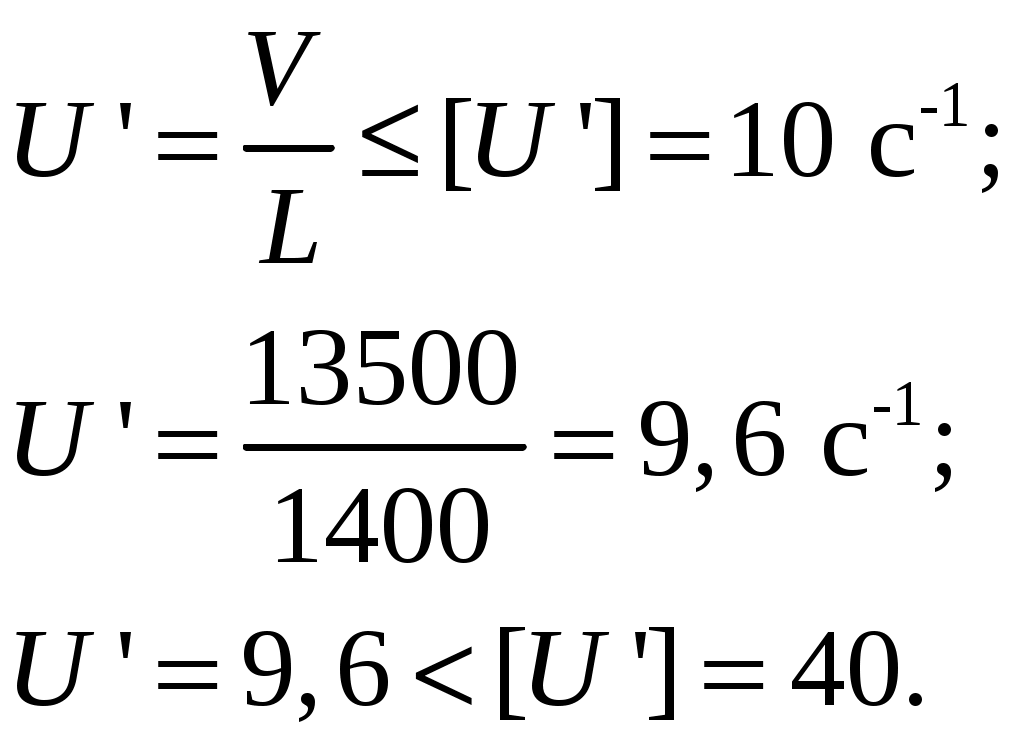
Определяем силу предварительного натяжения одного ремня, Н
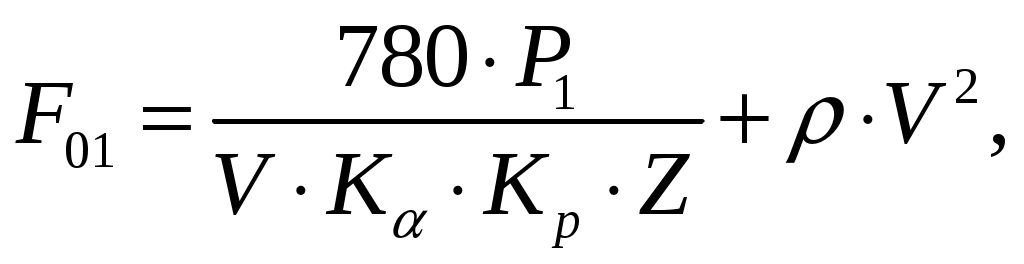
где


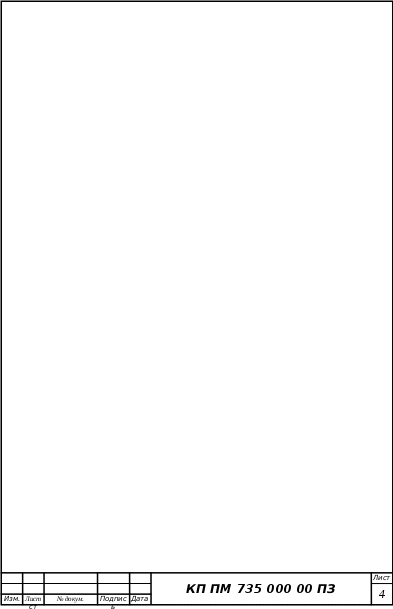

30>
Н.
Параметры и конструкция шкивов
В нашем случае, исходя из окружной скорости V = 13,5 м/с и диаметра ведомого шкива D2 = 250 мм, принимаем следующую конструкцию: материалом для изготовления принимаем СЧ20; обод и ступица соединяются между собой диском, в котором предусмотрены круглые отверстия.Ширина обода
В = (Z – 1) ∙ t + 2 · f = (3 – 1) ∙ 15 + 2 ∙ 10 = 50 мм.
Диаметр ступицы
dст =(1.6 – 2.0) ∙ dв= 1,6∙ 24 = 38,4 мм.
Длина ступицы
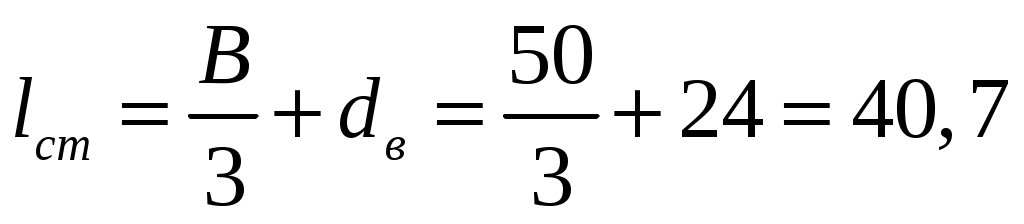
Принимаем lст=40 мм.
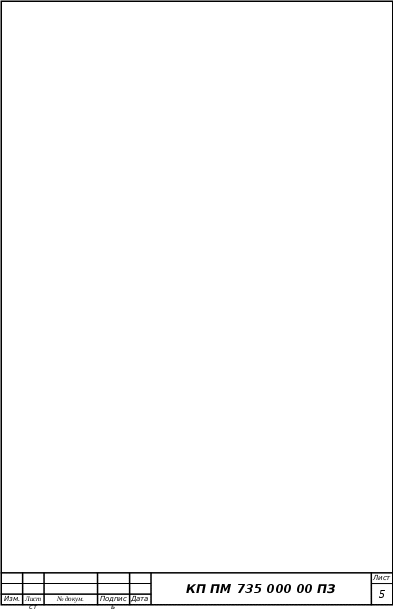
Таблица 3.1− Основные размеры профиля канавок для клиноременных шкивов

Обозна-чение сеченияремня | Конструкция шкива при d, мм | Размеры профиля канавок, мм | ||||||
Монолит-ная | С диском | Со спица-ми | bmin | hmin | Bp | t | f | |
А | 90 – 100 | 112 – 200 | 224 | 3.3 | 8.7 | 11.0 | 15.0±0.3 | 10 |
4 Расчет закрытой передачи
4.1 Выбор материала и допускаемых напряжений
Ввиду того, что в червячном зацеплении преобладает трение скольжения, применяемые материалы червячной пары должны обладать хорошими антифрикционными свойствами, повышенной износостойкостью и пониженной склонностью к заеданию. Для этого в червячной передаче сочетают разнородные материалы при малой шероховатости контактирующих поверхностей.
Червяки изготавливают из среднеуглеродистых сталей марок 40, 45, 50 или легированных сталей марок 40Х, 40ХН и др. с поверхностной закалкой до твердости HRC 45-55. При этом необходима шлифовка и полировка рабочих поверхностей витков. Хорошую работу передачи обеспечивают червяки из цементируемых сталей (15Х, 20Х и др.) с твердостью после закалки 58-63 HRC.
Зубчатые венцы червячных колёс изготавливают преимущественно из бронзы, причем выбор марки материала определяется скоростью скольжения (Vs = 6-25м/с) и при длительной работе рекомендуются оловянные бронзы марок БрОФ10-1, БрОНФ, которые обладают хорошими противозадирными свойствами. При средних скоростях скольжения (Vs = 2-6 м/с) применяют алюминиевую бронзу марки БрАЖ 9-4. Эта бронза обладает пониженными противозадирными свойствами, в отдельных случаях её применяют при Vs до 8 м/с.
При малых скоростях скольжения (Vs < 2 м/с) червячные колеса можно изготавливать из серых чугунов СЧ12, СЧ15, СЧ18 и др.
Vs ≈ 4.5 ·10-4 · n1 ·

где Т2 – крутящий момент на валу червячного колеса,
n1 – частота вращения вала червяка,
Т2 = 1596,7 Н.м;n1 = 1000 мин-1;

Выбираем материал I-й группы БрО10Ф1. Способ отливки –литье в кокиль.
σв = 230 МПа,
σт = 140 МПа.
Для I-й группы материалов [8, с.356]

здесь
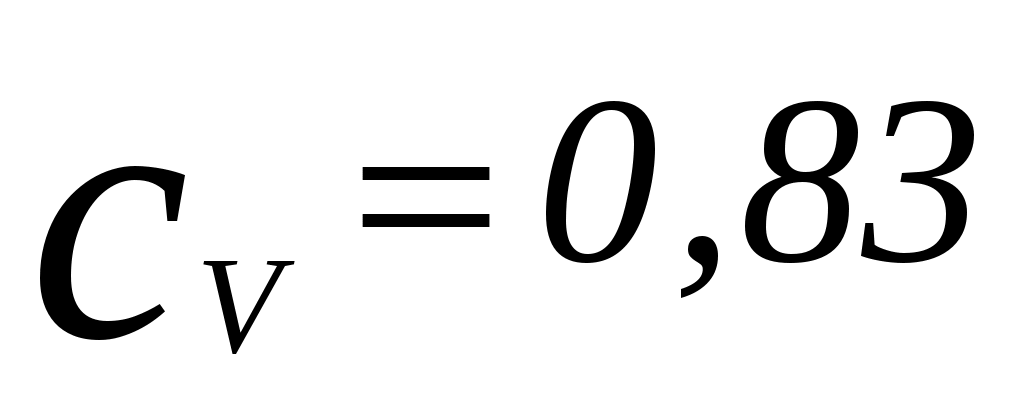
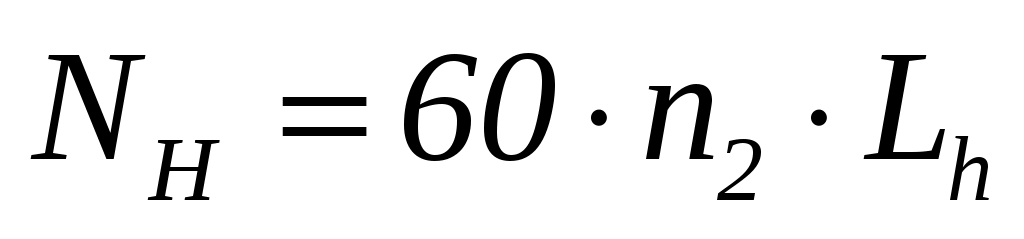
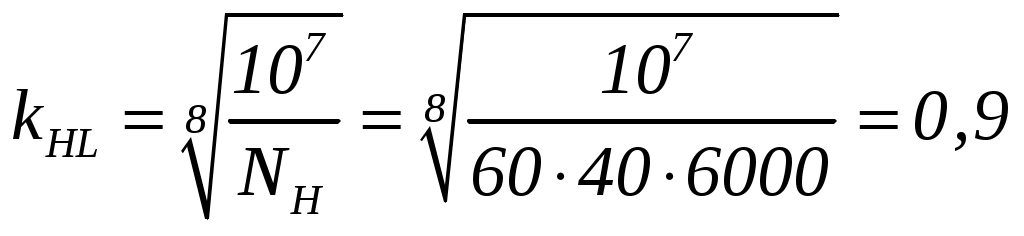
Принимаем
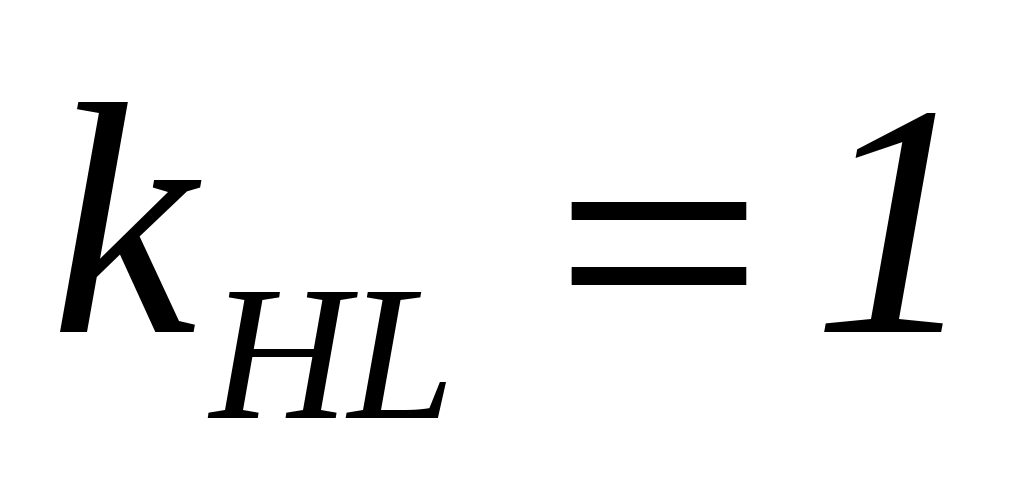

4.2 Проектировочный расчет червячной передачи
При проектировочном расчете определяют ориентировочное значение межосевого расстояния червячной передачи, исходя из контактной выносливости поверхности зубьев, а затем, после уточнения параметров передачи, проверяют действительные контактные напряжения и сравниваются с допускаемыми.

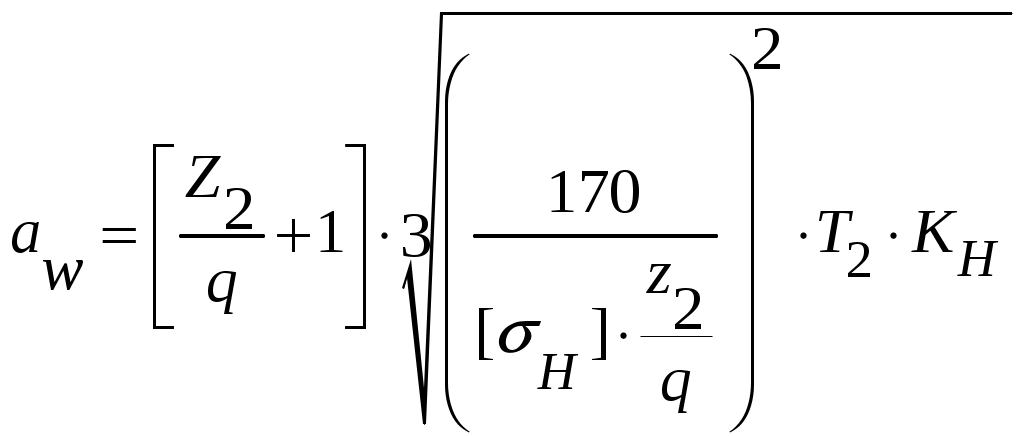
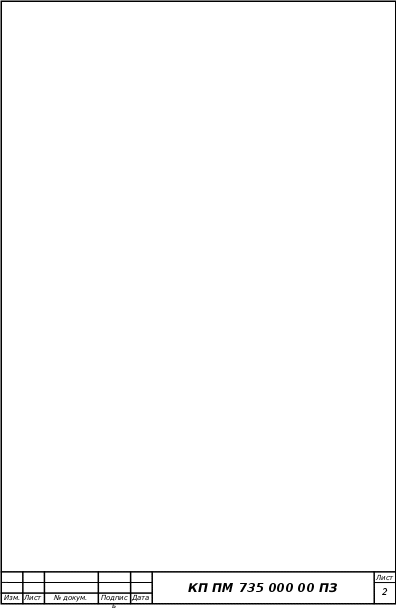
q – коэффициент диаметра червяка,
КН – коэффициент нагрузки,
Т2 – крутящий момент на валу червячного колеса, Н∙м
[σH] – допускаемое контактное напряжение, МПа.
q = 10; КН = 1,1. [1, c.68]
Z2 = Z1 ∙ U, (4.4)
Z2 = 2∙ 25 = 50.
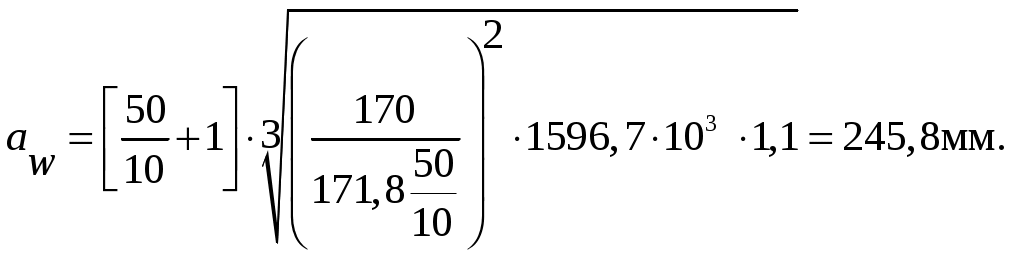
Определяем осевой модуль зацепления:
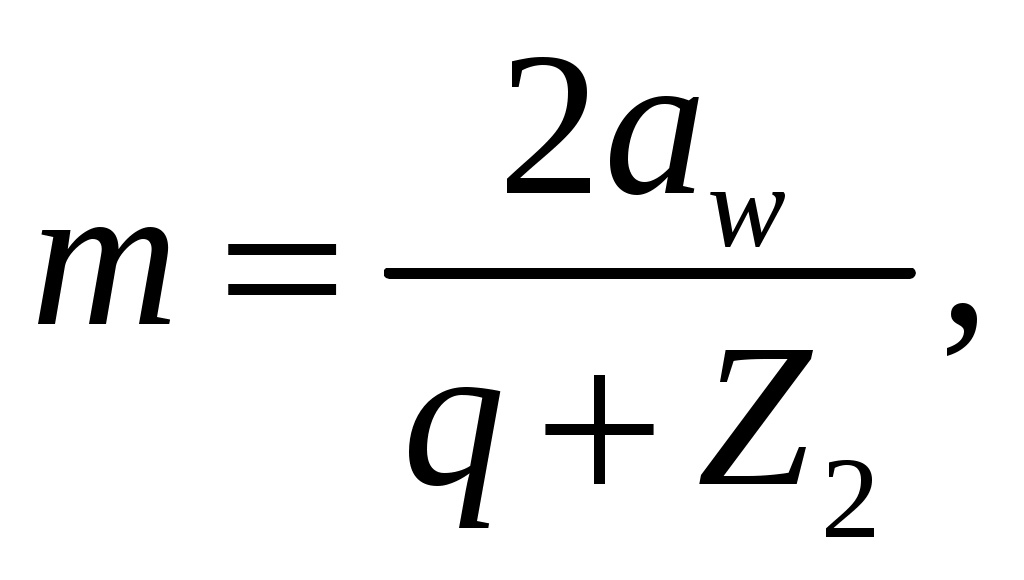
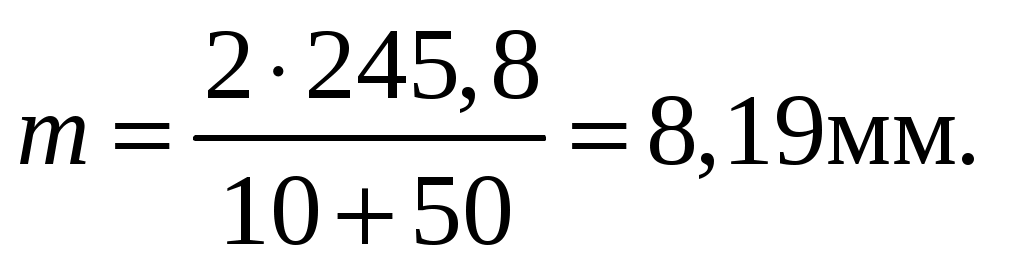
Полученный модуль округляют до стандартного по ГОСТ 2144–76,
mст = 8 мм.
Уточняем межосевое расстояние:
.
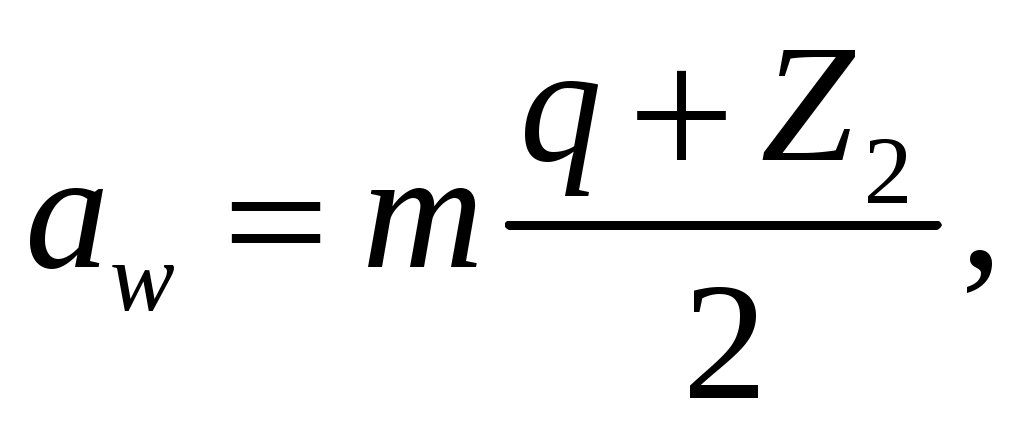
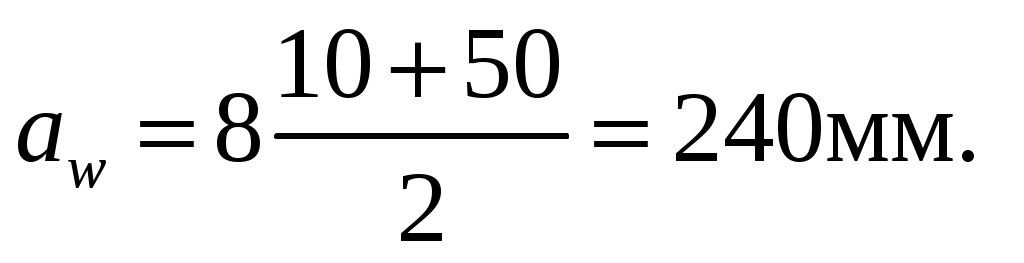
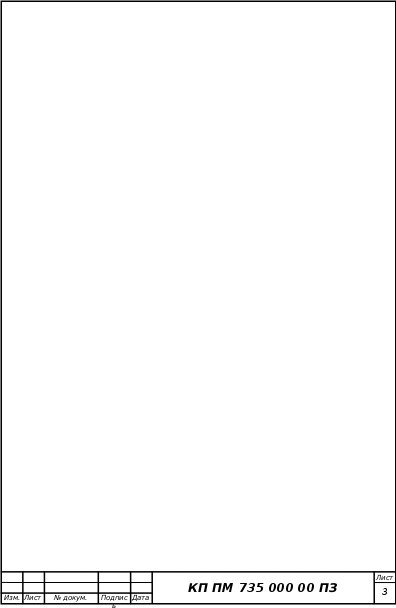
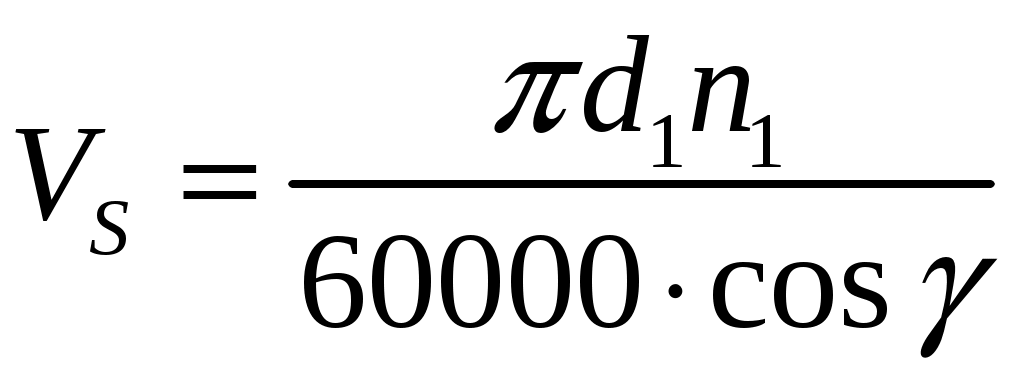
где d1 – делительный диаметр червяка, мм;
γ – угол наклона винтовой линии, град.
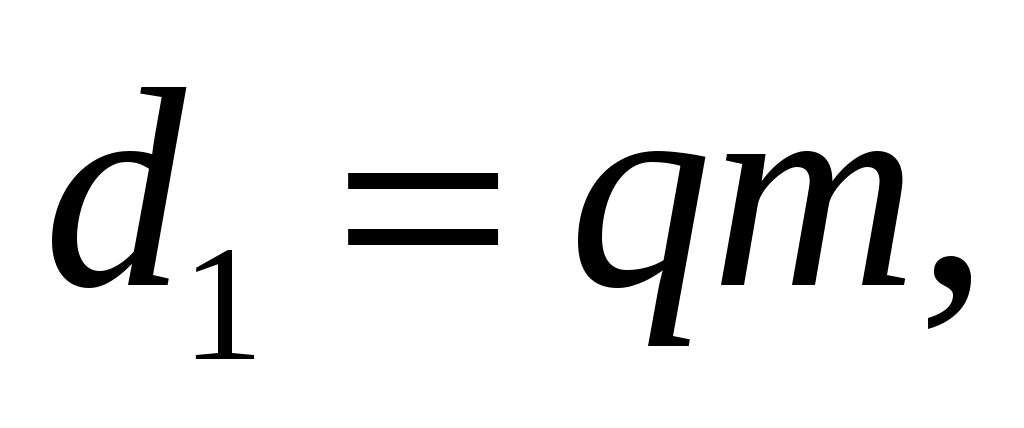
d1 = 8 ∙ 10 = 80 мм,
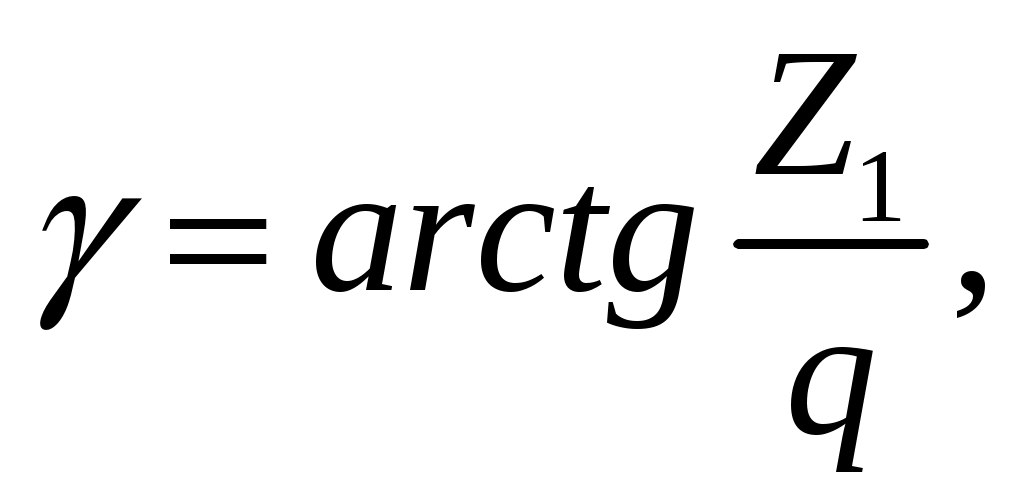
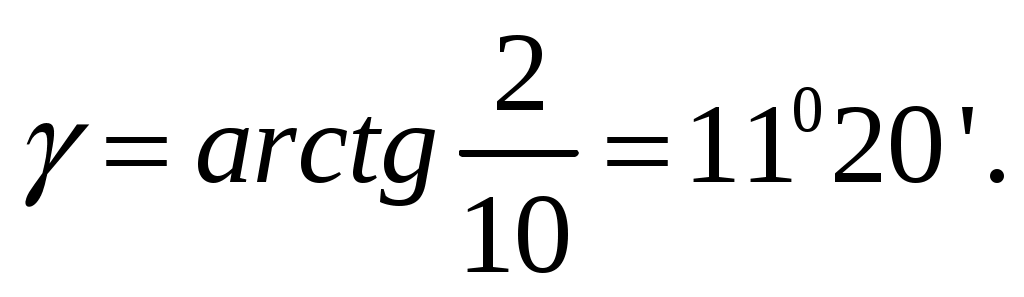
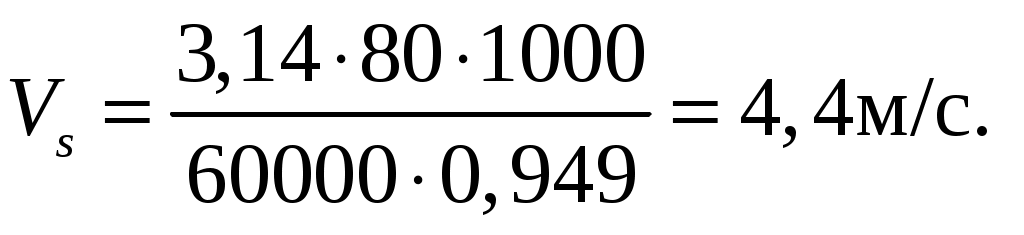
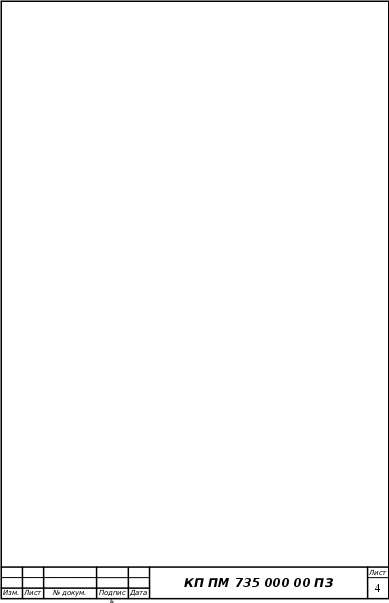
4.3 Проверочный расчет на контактную выносливость
Условие прочности по контактным напряжениям имеет вид:
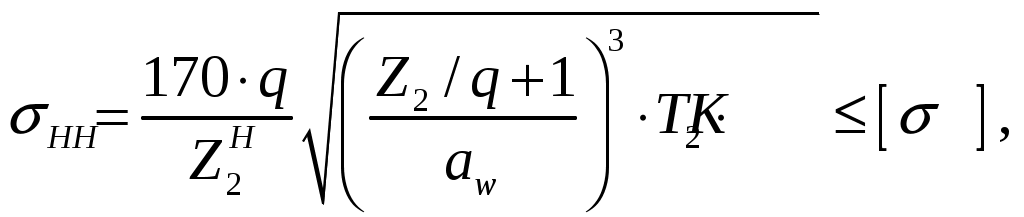