Файл: 1. Описание и метрологический анализ объекта контроля (детали типа вал) 2.docx
ВУЗ: Не указан
Категория: Не указан
Дисциплина: Не указана
Добавлен: 08.11.2023
Просмотров: 37
Скачиваний: 2
ВНИМАНИЕ! Если данный файл нарушает Ваши авторские права, то обязательно сообщите нам.
СОДЕРЖАНИЕ
1.Описание и метрологический анализ объекта контроля (детали типа «вал»)
2. Описание состава и принципа действия прибора контроля полного торцевого биения
3. Обоснование метрологической схемы измерительного устройства
4. Расчеты, подтверждающие работоспособность
Содержание
1.Описание и метрологический анализ объекта контроля (детали типа «вал») 2
2. Описание состава и принципа действия прибора контроля полного торцевого биения 4
3. Обоснование метрологической схемы измерительного устройства 6
4. Расчеты, подтверждающие работоспособность 11
5. Описание методики измерительного контроля 14
Список использованной литературы 17
1.Описание и метрологический анализ объекта контроля (детали типа «вал»)
Объектом контроля является деталь типа «вал» (рисунок 1), изготовленная из стали 45 ГОСТ 1050-88.
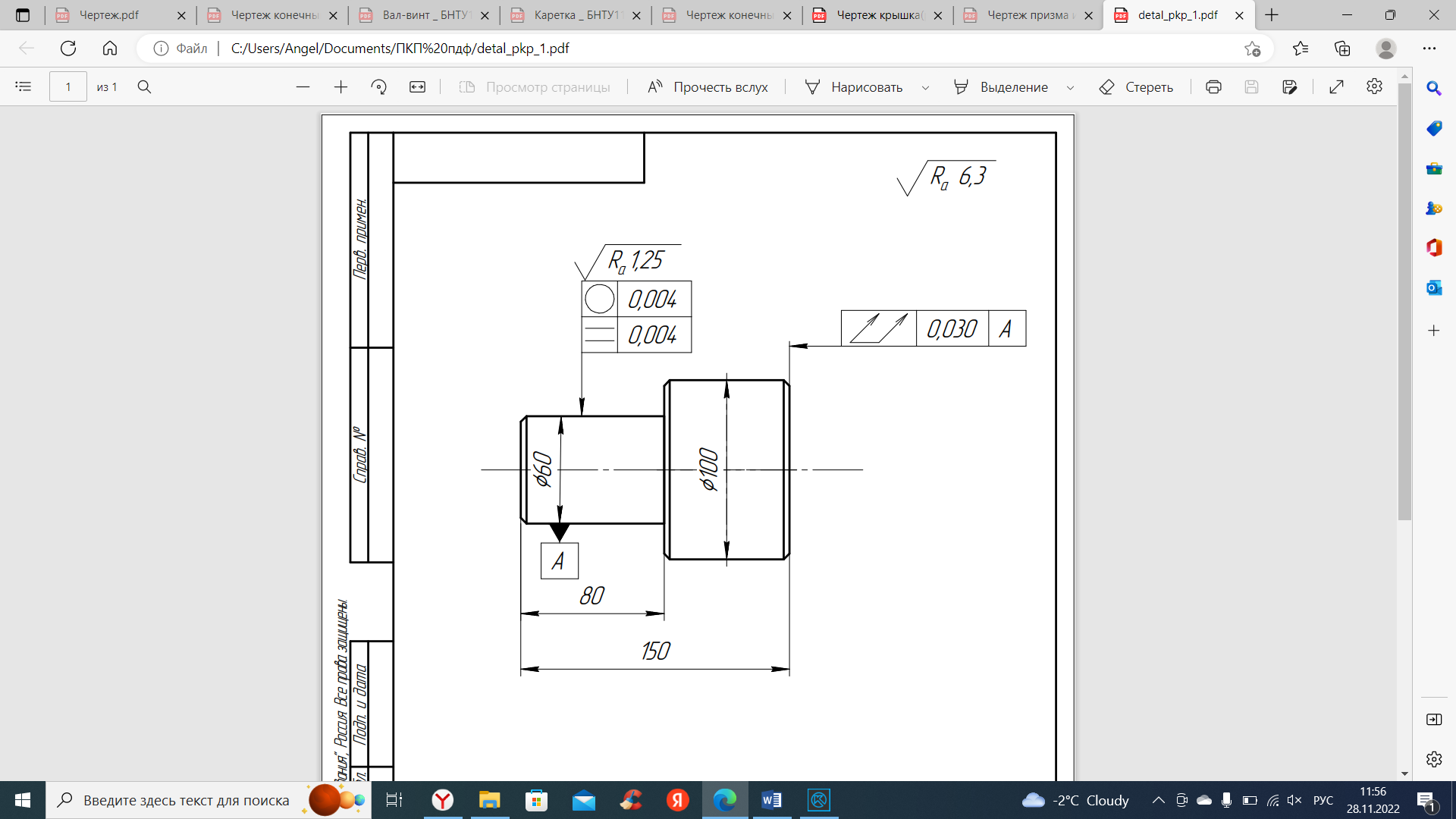
Рисунок 1. Деталь типа вал.
Вал имеет 2 ступени номинальным диаметром 60 мм и 100 мм, номинальные длины которых 80 и 70 мм соответственно. Общая длина вала 150 мм.
Их технических соображений на чертеже обозначаем номинальные значения геометрических параметров с указанием предельных отклонений:
Ø60 h4 (-0.008)
Ø100 h8 (-0.054)
На поверхности Ø100 h8 контролируем полное торцевое биение. Допуск полного торцевого биения задан по 8-ой степени точности и составляет 30 мкм.
Контролепригодность объекта контроля определяем в ходе метрологической экспертизы:
контролируемый параметр доступен для инструмента,
Индикаторная многооборотная головка МИГ (ГОСТ 9696-82) соответствует точности измерения ([∆] = 1/3 * Т = 1/3 * 30 = 10 мкм).
Базирование контролируемой детали типа «вал» при заданных условиях более целесообразно произвести на таких базирующих устройствах как: призма и патрон. Так как при базировании в центрах и в оправке нет возможности определения полного торцевого биения.
Допуски размеров определяют допуски формы и допусти расположения. Тогда к поверхностям Ø60 мм предъявляем требования в виде допусков круглости равных 4 мкм и допусков профиля продольного сечения равных 4 мкм. Общие допуски назначаем по ГОСТ 30893.1-m.
Таким образом, допуски размеров, допуски формы и расположения и параметры микрогеометрии взаимосвязаны и согласованы
2. Описание состава и принципа действия прибора контроля полного торцевого биения
У деталей типа тел вращения наиболее часто нормируют радиальное и торцовое биения, являющиеся суммарными отклонениями формы и расположения поверхностей этих деталей.
Полное торцовое биение является результатом совместного проявления отклонения от плоскостности рассматриваемой поверхности (отклонение формы) и отклонения ее от перпендикулярности относительно базовой оси (отклонение расположения). При измерении полного торцового биения, кроме вращения детали, следует дополнительно перемещать измерительное средство (например, индикатор) по радиусу от центра к периферии (или наоборот).
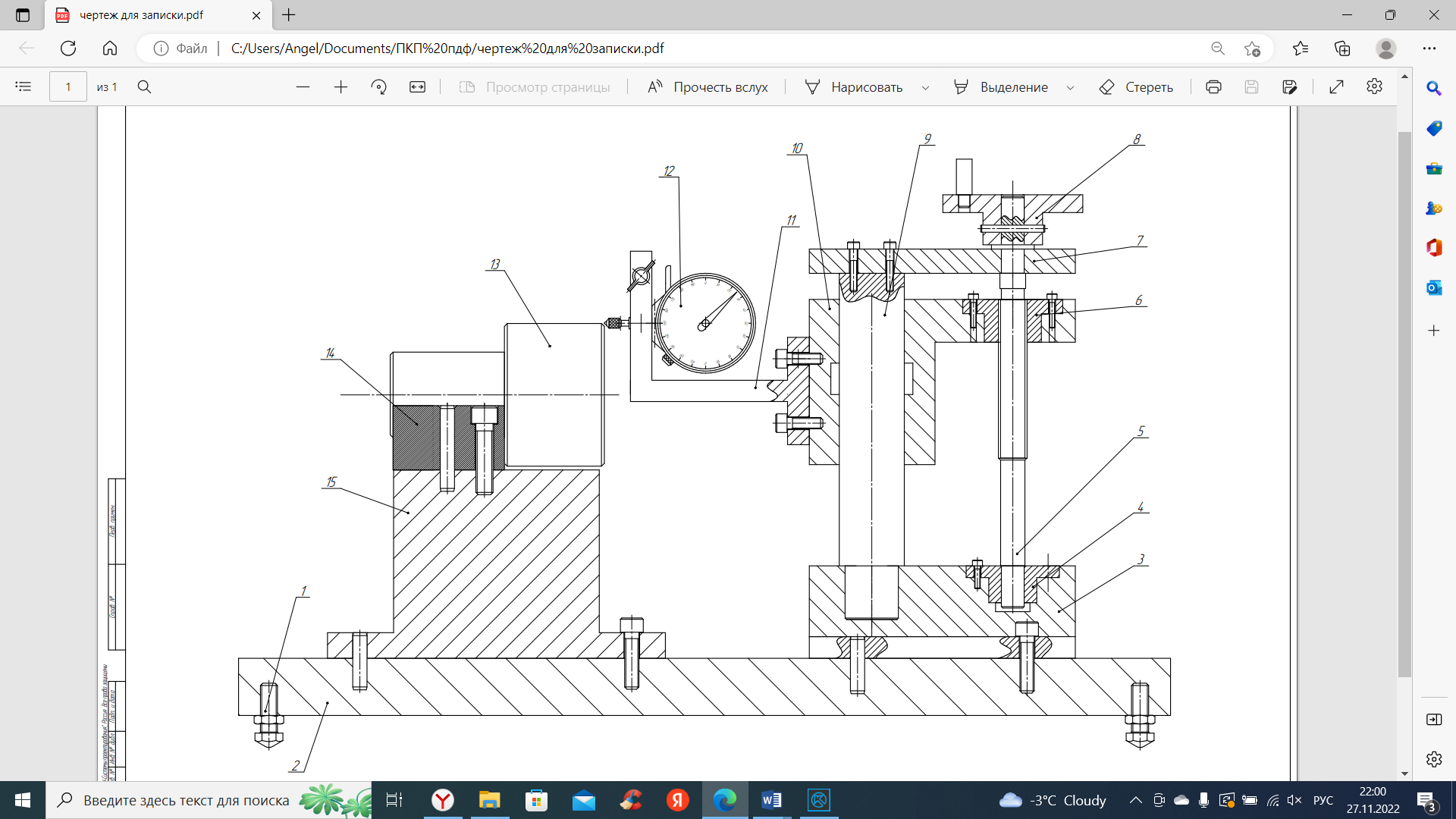
Рисунок 2. Устройство прибора контроля полного торцевого биения
1 - регилируемые опоры; 2 - установочная плита; 3 – корпус; 4 –(втулка); 5 – вал-винт; 6 – гайка; 7 – крышка; 8 – ручка; 9 – вал (направляющая); 10 – каретка; 11 – кронштейн; 12 – многооборотная индикаторная головка (МИГ); 13 - контролируемая деталь; 14 – опорная призма; 15 – установочная деталь
Контролируемая деталь типа «вал» устанавливается наружной поверхностью Ø60 мм на опорную призму (14). Призма закрепляется с помощью винтов и штифтов на установочной детале (15), которая в свою очередь крепится на установочной плите (2).
Измерение производится с использованием многооборотной индикаторной головки (12). Гильза многооборотной индикаторной головки (12) вставляется в отверстие между ушками кронштейна (11) и прочно закрепляется винтом. Кронштейн (11) закрепляется с помощью винтов на каретке (10). Поперечное перемещение многооборотной индикаторной головки (12) в цилиндрической направляющей (9) обеспечивается передачей винт-гайка (5, 6). Передача винт-гайка (5,6) фиксируется в корпусе (3) по средством крышки (втулки) (4), крышки (7) самого прибора и резьбовых крепежных элементов. Ручка (8) закреплена на вал-винте (5,6) штифтом, тем самым обеспечивая защиту от проворачиваемости.
Принцип работы прибора контроля полного торцевого биения осуществляется следующим образом: крутящий момент на ручке через штифт передается на вал-винт передачи винт-гайка. При помощи данной передачи осуществляется продольное перемещение каретки с кронштейном по цилиндрической направляющей (т. е. продольное перемещение многоборотной индикаторной головки). Вращение контролируемой детали типа «вал» осуществляется вручную вокруг своей оси.
3. Обоснование метрологической схемы измерительного устройства
Измерение контролируемого параметра в соответствии с заданием более целесообразно производить на таких базирующих устройствах как: призма и патрон. Схема измерения может быть различной. Проанализируем несколько схем и путем их сопоставления найдем недостатки и достоинства каждой.
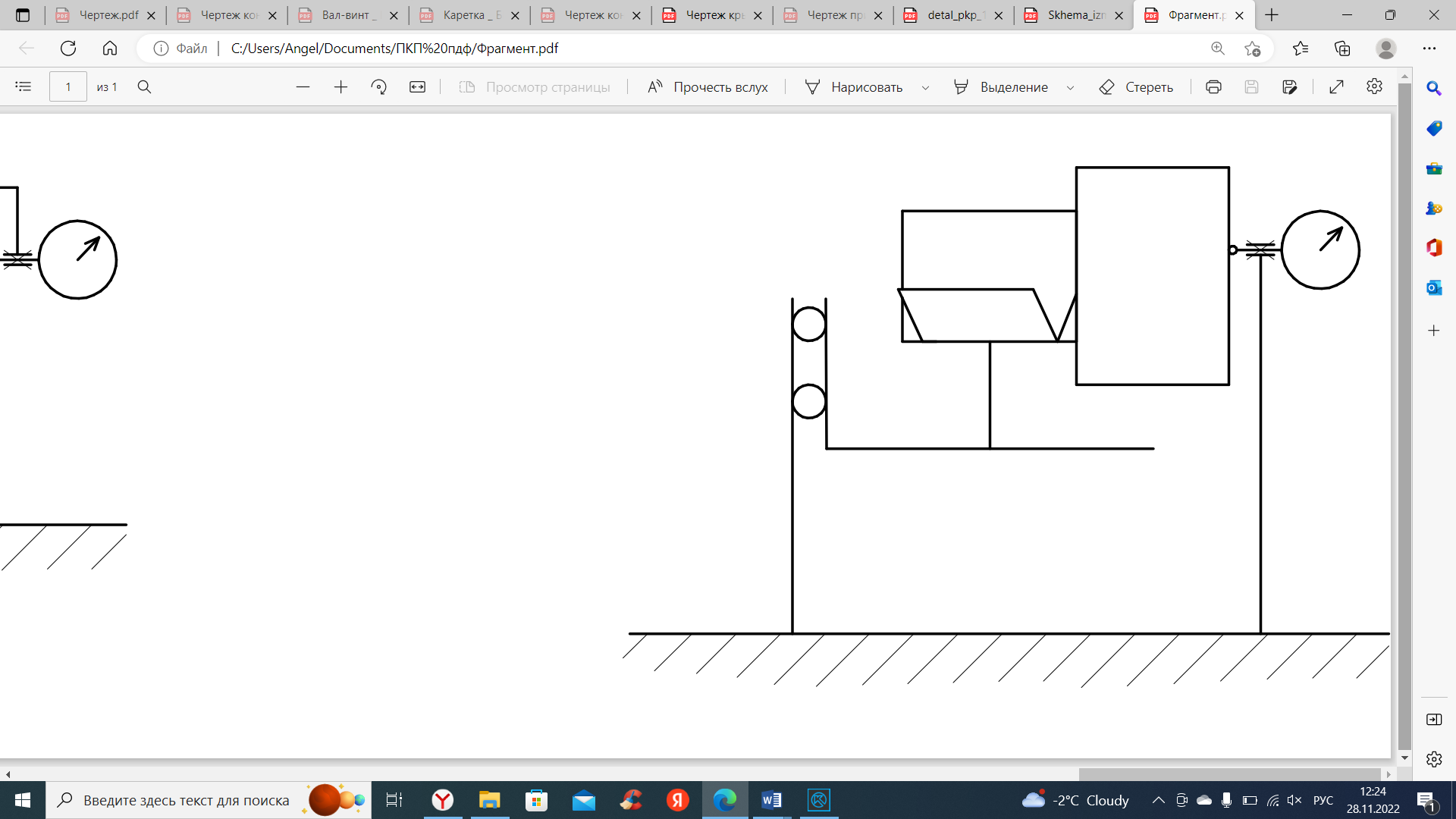
Рисунок 3. Возможная схема измерения полного торцевого биения
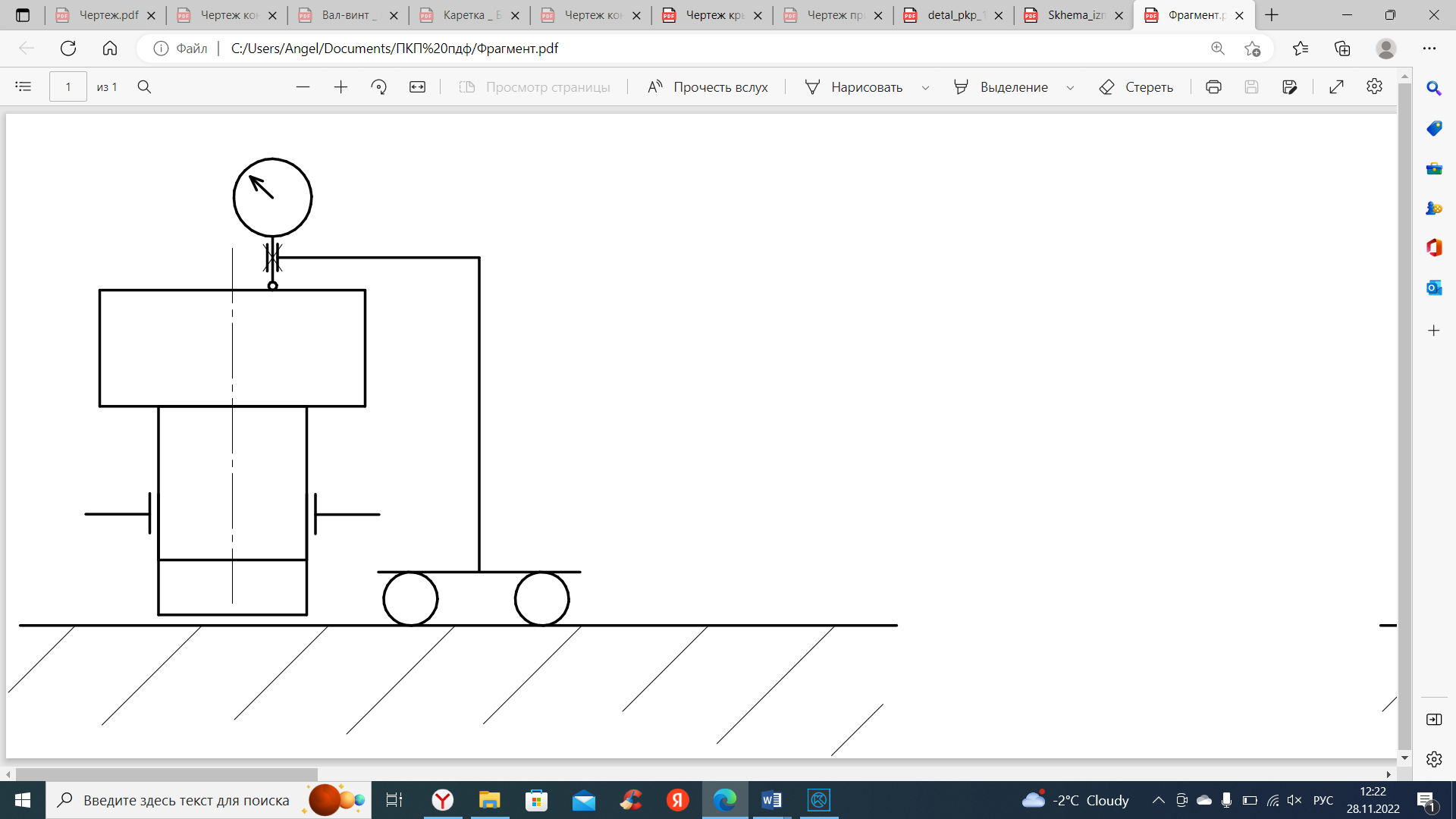
Рисунок 4. Возможная схема измерения полного торцевого биения
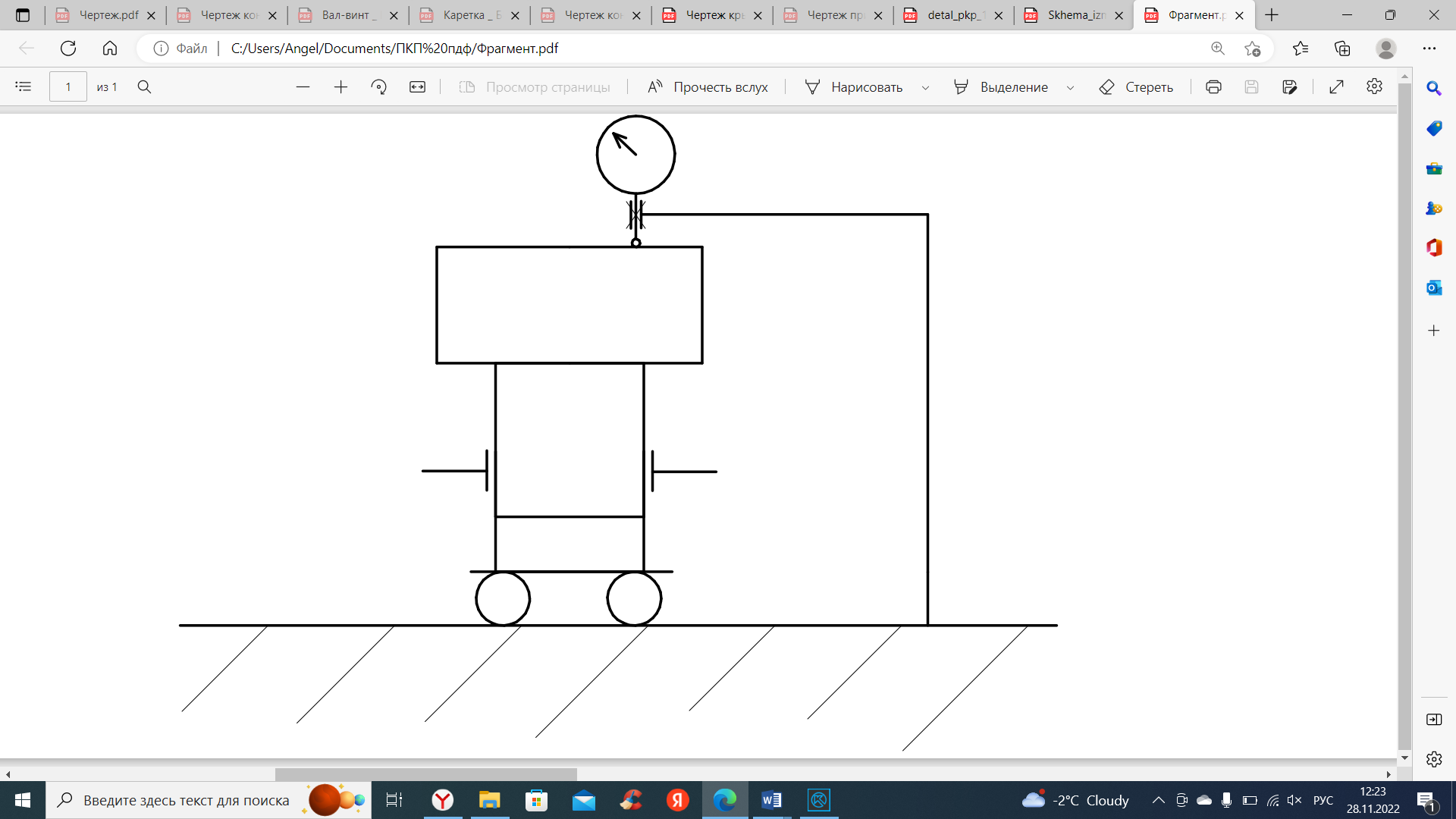
Рисунок 5. Возможная схема измерения полного торцевого биения
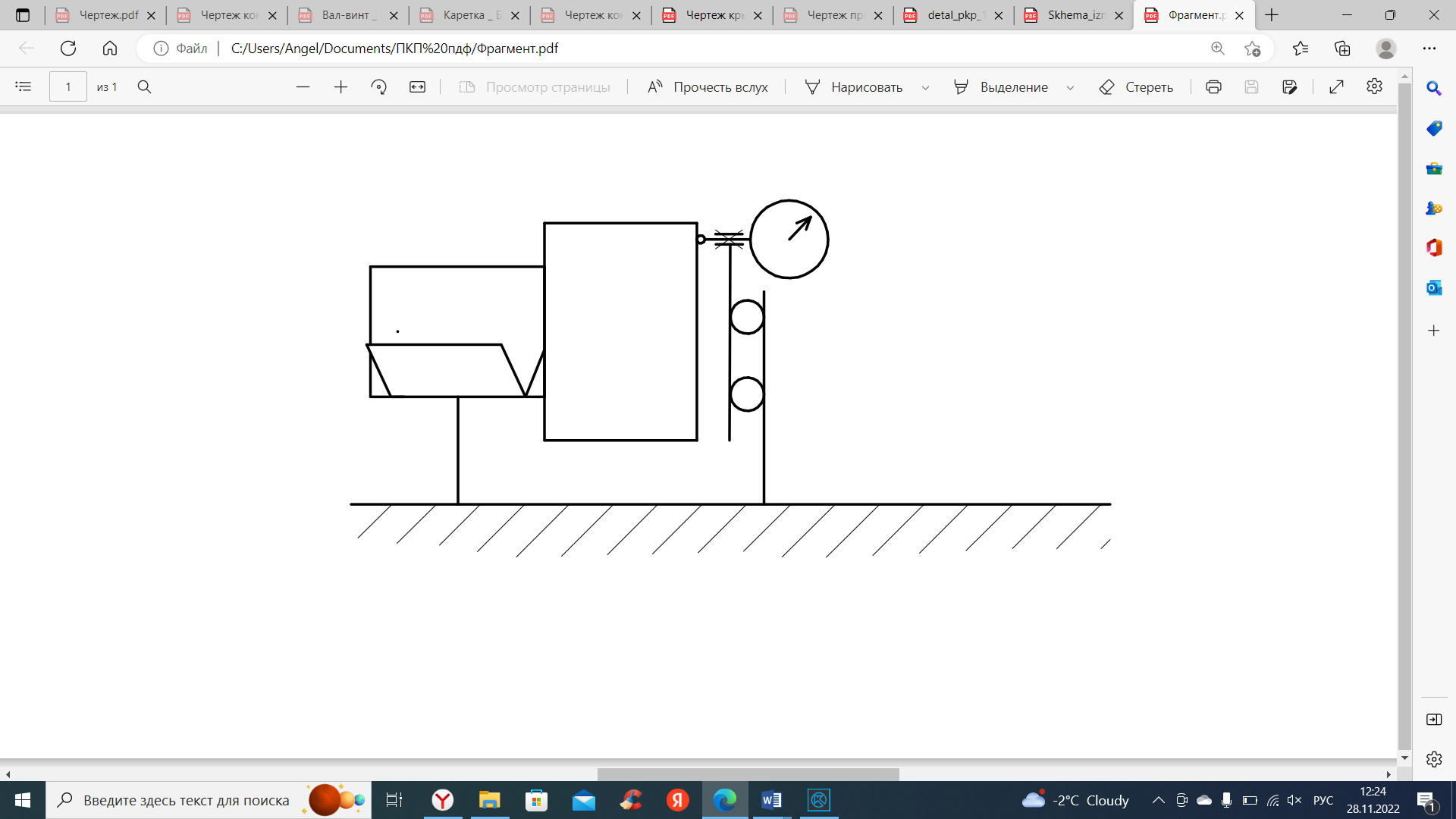
Рисунок 6. Возможная схема измерения полного торцевого биения
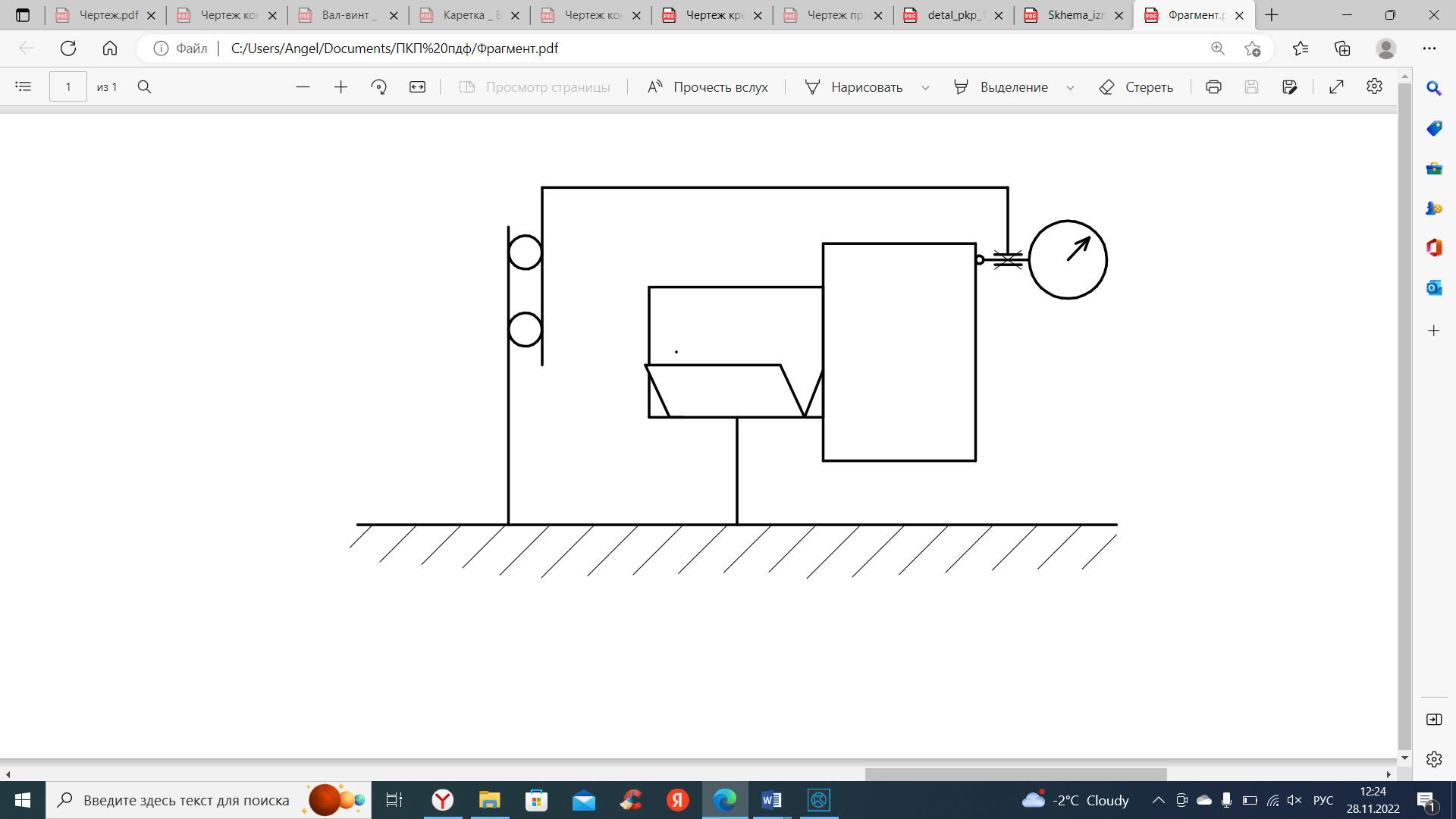
Рисунок 7. Возможная схема измерения полного торцевого биения
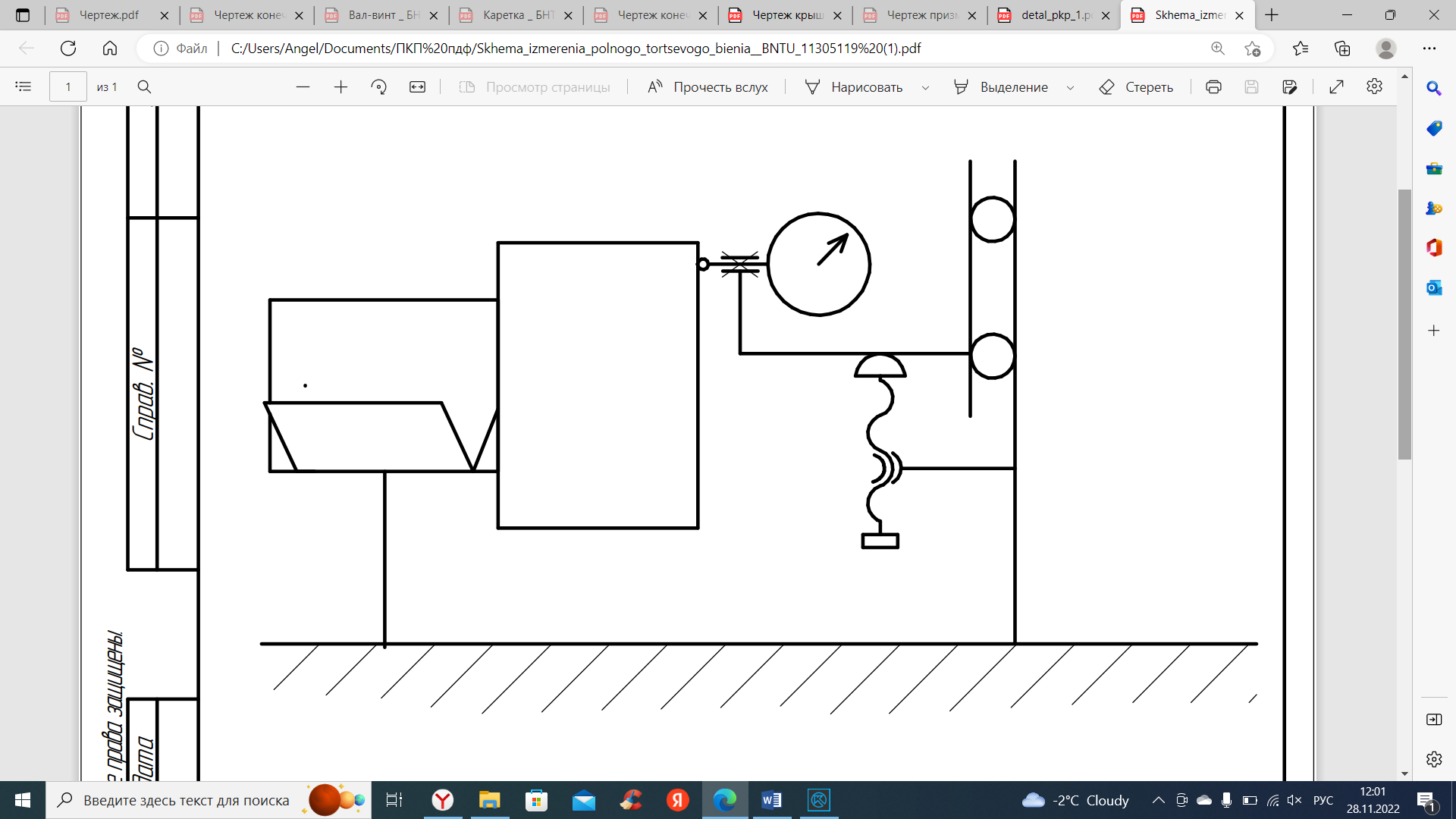
Рисунок 8. Возможная схема измерения полного торцевого биения
Рассмотрим схемы измерения, представленные на рисунках 3,4,5.
В этих схемах измерения базирование контролируемой детали происходит в цанговом патроне. При таком базирование возникают следующие погрешности:
-
погрешность формы детали (в продольном сечении); -
погрешность подшипников, в которых вращается патрон:
-
инструментальная погрешность, вызванная радиальным биением подшипников; -
погрешность, вызванная перекосом в подшипниках.
Из-за наличия большого количества погрешностей, которые вносят значительный вклад в суммарную погрешность, эти схемы измерения далее не будут рассматриваться
Рассмотрим схему измерения, представленную на рисунке 6.
В данном случае используются: направляющие, которые совершают поперечное перемещение и призма в качестве базирующего устройства. Недостаток данной схемы является большое расстояние между серединой направляющих и осью индикатора (длина кронштейна), которое вносит вклад в инструментальную погрешность непрямолинейности направляющей.
Рассмотрим схему измерения, представленную на рисунке 7.
В данном случае также используются: направляющие, которые совершают поперечное перемещение и призма в качестве базирующего устройства. Но из-за особенностей конструкции мы уменьшаем инструментальную погрешность, вызванную непрямолинейнностью направляющих (так как уменьшили длину кронштейна). Основным недостатком данной схемы является не эргономичность конструкции: расположение устройства перемещения с левой стороны при учете того что вращение детали также производится с левой стороны. Дополнительным недостатком выступает увеличение габаритов и утяжеление конструкции.
Рассмотрим схему измерения, представленную на рисунке 8.
Данная схема наиболее предпочтительна. Она позволяет минимизировать погрешности, влияющие на точность измерения:
-уменьшена инструментальная погрешность, вызванная непрямолинейнностью направляющих (так как уменьшили длину кронштейна);
-погрешность, вызываемая базированием в призме, является только погрешность формы детали (в продольном сечении);
-конструкция прибора при данной схеме измерения эргономична и имеет умеренные габариты и массу.
Для нашего контрольного приспособления из всех вышеперечисленных схем воспользуемся схемой измерения, представленной на рисунке 8.
Устройство состоит из установочной плиты на которой закрепляются наш прибор; цилиндрических направляющих, которые закрепляются на плите с помощью корпуса и резьбовых крепежных элементов; и базирующего устройства – призмы.
Выбор в пользу данной направляющей обусловлен тем, что данный тип направляющей имеет сравнительно простую схему работы, основанную на взаимодействии цилиндрической направляющей с телами качения. Зазор в сопряжении направляющая-каретка выбирается с помощью винта, зажимаемого на каретке и давящего через металлическую пластинку на направляющую.
А выбор базирования связан с максимальным уменьшением количества погрешностей базирующего устройства.
4. Расчеты, подтверждающие работоспособность
Важнейшим расчетом, который доказывает работоспособность механизма, является расчет на точность.
В задании необходимо обеспечить расчетным путем на стадии проектирования показатели качества изделия - контрольного приспособления для контроля полного торцевого биения детали типа «вал» с диаметром 100 мм, изготовленного с допуском радиального биения IT = 30 мкм по 8-ой степени точности.
Для контроля параметра принято, чтобы погрешность измерения не превышала 1/3..1/5 от допуска:
[∆] = (1/3..1/5) * IТ
Погрешность измерения состоит из 4-ех составляющих:
∆изм = ∆инстр * ∆м * ∆у * ∆оп,
где ∆у- погрешность из-за отличия условий измерения от нормальных;
∆м- погрешность метода измерений;
∆оп- погрешность оператора;
∆инстр- инструментальная погрешность.
В нашем случае предполагаем, что погрешность ∆у (из-за близости условий измерения к нормальным) пренебрежимо мала, на ∆м- (при измерении в призме) и ∆оп приходится 2…3 мкм. (на основе экспериментальных данных). Тогда основным показателем качества изделия будем считать инструментальную погрешность измерения, включающую в себя погрешность измерительного преобразователя и схемную погрешность.
Таким образом [∆] = 1/3 * IТ = 1/3 * 30 = 10 мкм.
Так как измерительный преобразователь 1 МИГ - покупное стандартизованное изделие, то ∆изм.пр будет равна погрешности измерения МИГ по паспорту, т.е.
∆изм.пр = 1 мкм.
Инструментальные погрешности:
1.Зазор в сопряжении каретка-направляющая:






2. непрямолинейность направляющей:




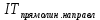