Файл: Расчет ректификационной колонны для Разделения бинарной смеси по мдк.docx
ВУЗ: Не указан
Категория: Не указан
Дисциплина: Не указана
Добавлен: 22.11.2023
Просмотров: 85
Скачиваний: 2
ВНИМАНИЕ! Если данный файл нарушает Ваши авторские права, то обязательно сообщите нам.
устройств и расстояния между ними.
При проведении расчета колонны его условно разделяют на 2 части: тех- нологическую, основным содержанием которой является определение техноло- гического режима разделения, и гидравлическую, поскольку основные размеры аппарата определяются на основе гидравлических зависимостей взаимодей- ствия двухфазных потоков пар – жидкость.
Основой технологического расчета тарельчатых колонн является термо- динамический расчет процессов разделения, которой выполняется на базе по- нятия о теоретической тарелке. Под теоретической тарелкой понимается такая ступень контакта, на которой осуществляется изменение концентраций фаз от рабочего до равновесного состояния. Термодинамический расчет позволяет определить максимальную разделяющую способность колонны, поскольку тео- ретическая тарелка характеризует предельное состояние массообмена при кон- такте фаз.
Истинное распределение концентраций и потоков по высоте аппарата,
оптимальное место ввода питания, количество реальных тарелок и другие пока-
затели, характеризующие работу аппарата, могут быть найдены только при по- мощи кинетического расчета, т.е. с учетом реально протекающего процесса массопередачи между газом и жидкостью.
При выполнении технологического расчета процессов ректификации ре- комендуется следующая последовательность расчета: расчет материального ба- ланса колонны по внешнему контуру, выбор рабочего давления в колонне, определение флегмового числа и числа теоретических тарелок, составление теплового баланса колонны, определение внутренних материальных потоков в
колонне.
Из уравнений материального баланса колонны по потокам и низкокипя- щему компоненту (НКК) определяются массовые расходы получаемых дистил- лята D и кубового остатка W.
???? = ???? ???????? − ????????
???????? − ????????
(1)
???? = ???? − ????, (2)
где L = 10000 кг/час (2,778 кг/с) – массовый расход сырья;
???????? = 0,95; ???????? = 0,03; ???????? = 0,5 – массовые доли НКК соответственно в ди- стилляте, остатке и сырье.
???? = 10000 0,05 − 0,03 = 5100 кг �1,417 кг
0,95 − 0,03
час с �
???? = 10000 − 5100 = 4900 кг
час
�1,361 кг
�
с
Давление и температура являются основными параметрами технологиче- ского режима в ректификационной колонне. Чем выше принимаемое давление, тем больше должна быть температура в колонне, так как с повышением давле- ния увеличивается температуры кипения и конденсации разделяемых смесей.
Температура кипения (конденсации) бензола 80,5℃, толуола 110,5℃ при атмосферном давлении. Следовательно, процесс ректификации в рассматрива-
емом случае можно проводить при атмосферном давлении. Однако для преодо- леня потерь напора парового потока через шлемовую трубу и конденсатор – холодильник примем давление в верху колонны несколько выше атмосферного, например 900 мм. рт. ст.
В случае ректификации бинарных смесей для расчета числа теоретиче- ских тарелок широко используется графический метод, известный в литературе как метод Мак – Кеба и Тиле (диаграмма y – х). Диаграмма кривых изобар поз- воляет легко определить температуры внешних потоков ректификационной ко- лонны.
Кривые равновесия и изобары строятся в пределах температур кипения низкокипящего и высококипящего компонентов при принятом давлении в ко- лонне.
В этом интервале температур принимается ряд значений температуры, для каждой температуры определяется по опытным (справочным) данным или рассчитываются (например, по уравнению Антуана) давления насыщенных па- ров компонентов (или константы фазового равновесия компонентов).
Рисунок 2 – Кривые равновесия и изобар. Графическое определение тем- ператур внешних потоков и числа теоретических тарелок в колоне.
где ???? = 900 мм рт.ст. ˗ давление в колонне;
При построении кривых равновесия и изобар использованы массовые концентрации (рисунок 2).
Флегмовое число или отношение количества горячего орошения к коли- честву дистиллята, вместе с числом тарелок является основным параметром, определяющим заданное разделение в процессе ректификации.
При увеличении флегмового числа необходимое число тарелок уменьша- ется, и наоборот. Предельные значения флегмового числа (???? = ???????????????? и ???? = ∞) определяют характерные условия разделения. Минимальное сечение колонны движущая сила процесса разделения равна нулю. Часто таким сечением являет- ся питательная секция колонны.
При минимальном флегмовом числе количество тарелок, потребное для разделения, будет равно бесконечности. При бесконечном флегмовом числе, т.е. когда нет отбора дистиллята, потребное количество тарелок становится ми- нимальным. Таким образом, предельными условиями работы колонны являют- ся с одной стороны, минимальное флегмовое число при бесконечном количе- стве тарелок и, с другой стороны, минимальное количество тарелок при беско- нечном флегмовом числе. Реальные условия работы колонны соответствуют оптимальному флегмовому числу и оптимальному количеству тарелок.
Оптимальное флегмовое число определяется техноэкономическим расчё- том. Для приблизительной его оценки можно воспользоваться рекомендациями Джиллиленда
???? = 1,35???????????????? + 0,35 (3)
Тогда ???? = 1,35 ∙ 1,476 + 0,35 = 2,34
Число теоретических тарелок находим графическим путём [3].
Тепловой баланс колонны составляется с целью определения необходи- мых затрат тепла и холода.
При остром испаряющемся орошении уходящий с верха колонны дистил-
При проведении расчета колонны его условно разделяют на 2 части: тех- нологическую, основным содержанием которой является определение техноло- гического режима разделения, и гидравлическую, поскольку основные размеры аппарата определяются на основе гидравлических зависимостей взаимодей- ствия двухфазных потоков пар – жидкость.
-
Технологический расчет
Основой технологического расчета тарельчатых колонн является термо- динамический расчет процессов разделения, которой выполняется на базе по- нятия о теоретической тарелке. Под теоретической тарелкой понимается такая ступень контакта, на которой осуществляется изменение концентраций фаз от рабочего до равновесного состояния. Термодинамический расчет позволяет определить максимальную разделяющую способность колонны, поскольку тео- ретическая тарелка характеризует предельное состояние массообмена при кон- такте фаз.
Истинное распределение концентраций и потоков по высоте аппарата,
оптимальное место ввода питания, количество реальных тарелок и другие пока-
затели, характеризующие работу аппарата, могут быть найдены только при по- мощи кинетического расчета, т.е. с учетом реально протекающего процесса массопередачи между газом и жидкостью.
При выполнении технологического расчета процессов ректификации ре- комендуется следующая последовательность расчета: расчет материального ба- ланса колонны по внешнему контуру, выбор рабочего давления в колонне, определение флегмового числа и числа теоретических тарелок, составление теплового баланса колонны, определение внутренних материальных потоков в
колонне.
- 1 2 3 4 5 6 7 8 9
Материальный баланс колонны
Из уравнений материального баланса колонны по потокам и низкокипя- щему компоненту (НКК) определяются массовые расходы получаемых дистил- лята D и кубового остатка W.

???????? − ????????
(1)
???? = ???? − ????, (2)
где L = 10000 кг/час (2,778 кг/с) – массовый расход сырья;
???????? = 0,95; ???????? = 0,03; ???????? = 0,5 – массовые доли НКК соответственно в ди- стилляте, остатке и сырье.
???? = 10000 0,05 − 0,03 = 5100 кг �1,417 кг



0,95 − 0,03
час с �

час
�1,361 кг

�
с
-
Определение давления и температуры в колонне
Давление и температура являются основными параметрами технологиче- ского режима в ректификационной колонне. Чем выше принимаемое давление, тем больше должна быть температура в колонне, так как с повышением давле- ния увеличивается температуры кипения и конденсации разделяемых смесей.
Температура кипения (конденсации) бензола 80,5℃, толуола 110,5℃ при атмосферном давлении. Следовательно, процесс ректификации в рассматрива-
емом случае можно проводить при атмосферном давлении. Однако для преодо- леня потерь напора парового потока через шлемовую трубу и конденсатор – холодильник примем давление в верху колонны несколько выше атмосферного, например 900 мм. рт. ст.
-
Построение диаграмм фазового равновесия и кривых изобар
В случае ректификации бинарных смесей для расчета числа теоретиче- ских тарелок широко используется графический метод, известный в литературе как метод Мак – Кеба и Тиле (диаграмма y – х). Диаграмма кривых изобар поз- воляет легко определить температуры внешних потоков ректификационной ко- лонны.
Кривые равновесия и изобары строятся в пределах температур кипения низкокипящего и высококипящего компонентов при принятом давлении в ко- лонне.
В этом интервале температур принимается ряд значений температуры, для каждой температуры определяется по опытным (справочным) данным или рассчитываются (например, по уравнению Антуана) давления насыщенных па- ров компонентов (или константы фазового равновесия компонентов).
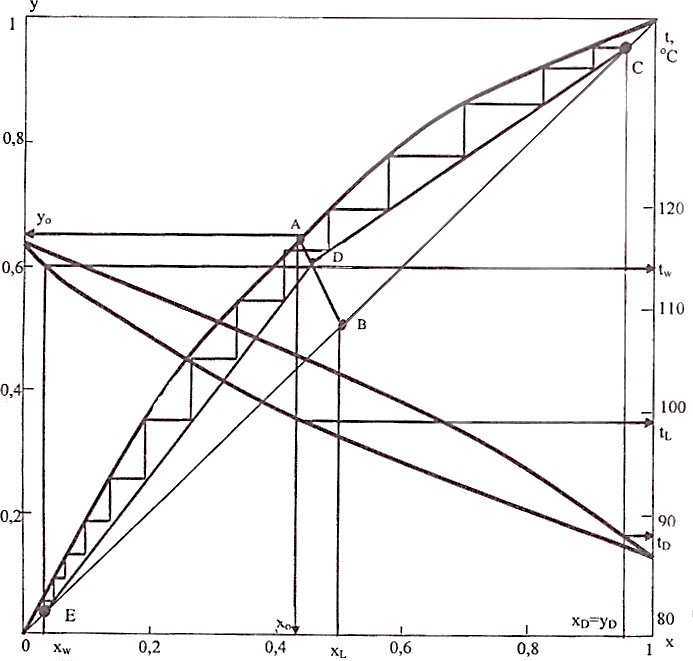
Рисунок 2 – Кривые равновесия и изобар. Графическое определение тем- ператур внешних потоков и числа теоретических тарелок в колоне.
где ???? = 900 мм рт.ст. ˗ давление в колонне;
При построении кривых равновесия и изобар использованы массовые концентрации (рисунок 2).
- 1 2 3 4 5 6 7 8 9
Определение флегмового числа и числа теоретических тарелок
Флегмовое число или отношение количества горячего орошения к коли- честву дистиллята, вместе с числом тарелок является основным параметром, определяющим заданное разделение в процессе ректификации.
При увеличении флегмового числа необходимое число тарелок уменьша- ется, и наоборот. Предельные значения флегмового числа (???? = ???????????????? и ???? = ∞) определяют характерные условия разделения. Минимальное сечение колонны движущая сила процесса разделения равна нулю. Часто таким сечением являет- ся питательная секция колонны.
При минимальном флегмовом числе количество тарелок, потребное для разделения, будет равно бесконечности. При бесконечном флегмовом числе, т.е. когда нет отбора дистиллята, потребное количество тарелок становится ми- нимальным. Таким образом, предельными условиями работы колонны являют- ся с одной стороны, минимальное флегмовое число при бесконечном количе- стве тарелок и, с другой стороны, минимальное количество тарелок при беско- нечном флегмовом числе. Реальные условия работы колонны соответствуют оптимальному флегмовому числу и оптимальному количеству тарелок.
Оптимальное флегмовое число определяется техноэкономическим расчё- том. Для приблизительной его оценки можно воспользоваться рекомендациями Джиллиленда
???? = 1,35???????????????? + 0,35 (3)
Тогда ???? = 1,35 ∙ 1,476 + 0,35 = 2,34
Число теоретических тарелок находим графическим путём [3].
-
Тепловой баланс колонны
Тепловой баланс колонны составляется с целью определения необходи- мых затрат тепла и холода.
При остром испаряющемся орошении уходящий с верха колонны дистил-