Файл: Инструкционная карта 36 Выполнение резки металлов под водой различными способами Цель работы.docx
ВУЗ: Не указан
Категория: Не указан
Дисциплина: Не указана
Добавлен: 05.12.2023
Просмотров: 99
Скачиваний: 1
ВНИМАНИЕ! Если данный файл нарушает Ваши авторские права, то обязательно сообщите нам.
Выполнить схему видов резки и указать достоинства и недостатки.
2. Выполнить тест.
Подводная резка металла используется при осуществлении аварийно-спасательных, строительных и судноподьемных работ.
Для подводных работ применяют электрокислородный и газовый способ резки. Электрокислородный способ резки является более опасным с точки зрения техники безопасности из-за возможности поражения электрическим током, особенно в морской воде.
Подводная резка металла резаком осуществляется преимущественно резаками, работающими на бензине, ибо такое горючее вещество можно подать на значительную глубину под большим давлением. Ацетилен при больших давлениях может взорваться, поэтому не используется. Мощность подогревающей пламени при подводной резке в 10-15 раз превышает мощность пламени для резки на воздухе.
Горит огонь под водой в газовом волдыре, создаваемый продуктами сгорания бензина, или путем подачи воздуха вокруг головки резака для оттеснения воды. Розжиг пламени осуществляется электрозапалом, что подключен к батарее аккумуляторов. Давление в бензиновых бачках создается азотом. В резаках бензин разбрызгивается в завихрительных головках и при этом испаряется.
Для подводной резки широко используется спецустановка БУПР. Рампа кислородных баллонов, канистра с горючим, баллоны с азотом и пульт управления БУПР необходимо размещать над водой. Чрезмерный бензин, всплывая на поверхность воды, может заниматься, потому бензокислородная резка применяется в неглубоких водоемах и замкнутых пространствах.
Водородная резка металла осуществляется водородом, который вырабатывается в аппарате. Вследствие разложения молекул воды на 2 элемента, кислород и водород, получается водород. В результате чего появляется газовая смесь, при помощи которой можно осуществлять работы резке.
Читайте так же: Станок лазерной резки металла своими руками: процесс изготовления
Технология подводной сварки и резки сдвоенным электродом
Подводная электродуговая резка металла нашло широкое применение как при изготовлении трубопроводов для газо-нефтеперерабатывающей отрасли так и в ремонтном производстве благодаря своей оперативности и простоте выполнения. Однако оно имеет значительные трудности как технологического так и металлургического характера. Технологические трудности заключаются в необходимости обеспечения герметичности оборудования и материалов для зажигания дуги под водой, что требует использования трубчатых электродов и дополнительного оборудования для подачи газа, что создает пузырь в котором зажигается дуга. Металлургические трудности обусловлены водородно-кислородной атмосферой парогазового пузыря, который формируется уже в процессе сварки под водой и способствует окислению легирующих элементов и насыщению металла сварочной ванны водородом, а ускоренное охлаждение окружающей водой приводит к его задержке в металле шва и образованию закалочных структур.
Так же могут использоваться сдвоенные экзотермические электроды для подводной резки металла. Эта технология заключается в том, что электродов размещены параллельно друг другу и подключения их к клеммам источника питания переменного тока. Такая технология позволяет зажигать дугу между электродами над водой и заглублять ее на небольшую глубину к месту сварки. Зажигания дуги под водой возможно с помощью осциллятора. В таком случае концы электродов необходимо изолировать, например термоклеем, с обеспечением воздушного канала между их торцами. После зажигания дуги электроды приближают к деталям. Как только расстояние между электродами и изделием становится меньше расстояния между самими электродами дуга начинает гореть между электродами и деталью, что позволяет выполнять как сварку, так и резку металла.
Читайте так же: Резка металла водой: область применения
Для разъединения металлических частей в подводных условиях наибольшее применение нашли ручная электрокислородная и бензокислородная резка. Кроме этих способов, подводную резку можно выполнять плавящимся электродом с покрытием, полуавтоматическую электрокислородную тонким плавящимся электродом, плазменно-дуговую и в отдельных случаях направленным взрывом.
Электрокислородная резка выполняется специальным электродом, изготовленным из стальной трубки размером 7×2,5 мм, покрытым толстым слоем водонепроницаемого состава. В трубку при помощи специального держателя от баллона по шлангу подается кислород под давлением 1,5 - 3,5 ат. Дуга разогревает металл, а кислород окисляет его, как и при обычной кислородной резке. Этот вид резки благодаря своей простоте нашел большое применение.
Процесс подводной резки происходит следующим образом: после включения рабочего тока на поверхности и подачи команды резчиком-водолазом резчик нажимает на рычаг кислородного клапана и возбуждает дугу, после чего начинает перемещение электрода вдоль линии реза. При резке металла большой толщины резчик углубляет электрод в металл для того, чтобы ввести в зону реза большее количество тепла. Скорость резки в вертикальном положении (сверху вниз) будет выше, чем в нижнем, так как в первом случае полнее используется режущий кислород.
Этим способом удается резать металл толщиной до 300 мм.
Для полуавтоматической электрокислородной резки тонкой проволокой разработан полуавтомат ППСР-300-2 (он же применяется и для сварки). Дуга горит в защитном газе, который подается через специальный шланг (вместе, с проволокой), в этом же шланге проходит токоведущий кабель. Кислород подводится по отдельному шлангу.
Скорость резки на установке ППСР-300-2 для толщины металла 10 мм при силе тока 270 - 280 А составляет 11 м/ч, для толщины металла 25 мм при силе тока 300 А - 2,5 - 2,8 м/ч.
Производительность полуавтоматической электрокислородной резки значительно выше ручной; это особенно важно при глубоководных работах, когда время пребывания резчика-водолаза под водой весьма ограничено.
При бензокислородной резке применяют специальный резак, работающий по принципу распыления бензина. К резаку подводятся три шланга: для подогревающего и режущего кислорода и распыленного (азотом) бензина. Подогревающее пламя зажигается под водой специальной электрозажигалкой, питаемой аккумуляторной батареей напряжением 12 В. Шланги, подводящие кислород и распыленный бензин, заключены в металлическую оплетку, позволяющую выполнять работу на глубине до 30 м.
Для бензокислородной резки металла толщиной от 5 до 100 мм под водой выпускается установка БУПР-61.
Скорость резки на установке БУПР-61 на глубине до 10 м: для толщины металла 10 мм - 22 м/ч, для толщины металла 100 мм - 6,5 м/ч.
Производительность подводной резки зависит от вида резки, прозрачности воды, доступности места резки, опытности водолаза и др.
В настоящее время для резки под водой начинают применять плазменную дугу. Разрабатывается резка под водой взрывом. Подводные резаки, действующие с помощью пороховых патронов, могут быть использованы для резки проволоки, кабелей, якорных цепей и других деталей, имеющих форму ленты или шнура. Ими можно перерезать стальную проволоку диаметром 1,6 - 38 мм и специальные кабели диаметром до 90 мм. Для осуществления, резки взрывом установка оснащается кумулятивным (направленным) взрывчатым зарядом, запальным шнуром, детонатором, электрическим кабелем и защитным ограждением материалов, примыкающих к месту реза.
Оборудование для резки в воде любым процессом существенно отличается от промышленного оборудования для резки на воздухе, оно намного сложнее и менее производительно.
В настоящее время техника подводной резки позволяет выполнять работы на глубине до 150 м и резать металл толщиной до 150 мм.
Реализация такого способа подводной сварки возможна с использованием обычных искусственных электродов с предварительно нанесенным на их поверхность водоотталкивающим изоляционным покрытием. Однако подводная сварка кроме технологических трудностей, имеет ряд металлургических связанных с насыщением металла сварочной ванны водородом и ускоренным охлаждением. Для исследования влияния этих факторов были проведены эксперименты с использованием для подводной сварки электродов марок АНО-21, МР-3, УОНИ 13/45. Все они позволяют формировать в воде качественный сварной шов с характерным металлическим блеском аустенитным нержавеющим сталям.
Общеизвестно, что высокоуглеродистые стали с мартенситной структурой имеют высокую твердость и малую пластичность. Эти обстоятельства имеют существенное значение для установления способности сварных швов заваренных под водой. Технология двухэлектродной подводной сварки и резки штучными электродами на ряду со своей простотой в использовании показала такую эффективность, какую не дает подводная кислородная резка металла. Полученные соединения имеют высокое качество и структуру с небольшой твердостью по глубине, что позволяет делать вывод о пригодности предлагаемой технологии в промышленности.
Нетривиальная задача: надо разрезать металлическую конструкцию под водой не извлекая её: чем это можно сделать?
В современных способах обработки металла при необходимости выполнения работ под водой применяются два принципиально различных способа резки металла:
Последний способ в свою очередь делится на два подвида по типу нагрева металла:
Самым простым способом, который применяют в большинстве случаев для выполнения резки металла под водой на данный момент времени остается дуговая резка, для которого организую подачу тока не менее 500 a. Хорошие результаты дает этот способ при обработке металла толщиной до 2 см, с увеличением толщины производительность выполнения работ быстро снижается, а расход электродов растет, кроме того образуется неровный край реза. Поэтому, хоть и существует возможность применения электродуговой резки к порезам металла толщиной до 70 mm, но гораздо чаще для больших толщин металла или для резки нескольких слоев применяют электрокислородный способ.
Но и у этого способа есть свои минусы, так в первую очередь, это быстрый выход из строя электродов. Так самый доступный трубчатый стальной электрод в среднем сгорает за 1 мин и требуется его замена, что увеличивает время выполнения работ в три-четыре раза. Поэтому основные усилия в продвижении этого способа направлены на поиск и разработку более стойких электродов.
Читайте также: Пресс - упражнения, особенности тренировки, анатомия
По качеству создания кромки самые лучшие результаты показывает газокислородный способ резки. Но и этот способ имеет свои ограничения. Так, хорошие показатели резки получаются при разделении стали, титана и марганца и сплавов на их основе. А остальные металлы и сплавы, в частности, на основе меди и алюминия, почти не поддаются газокислородной обработке, потому что температура их плавления ниже температуры их активного окисления в кислороде, а это условие является одним из необходимых условий газокислородной резки.
2. Выполнить тест.
Подводная резка металла используется при осуществлении аварийно-спасательных, строительных и судноподьемных работ.
Для подводных работ применяют электрокислородный и газовый способ резки. Электрокислородный способ резки является более опасным с точки зрения техники безопасности из-за возможности поражения электрическим током, особенно в морской воде.
Подводная резка металла резаком осуществляется преимущественно резаками, работающими на бензине, ибо такое горючее вещество можно подать на значительную глубину под большим давлением. Ацетилен при больших давлениях может взорваться, поэтому не используется. Мощность подогревающей пламени при подводной резке в 10-15 раз превышает мощность пламени для резки на воздухе.
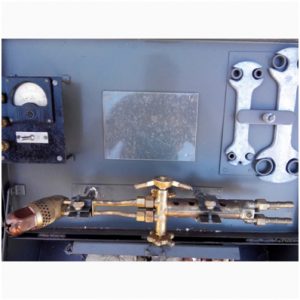
Горит огонь под водой в газовом волдыре, создаваемый продуктами сгорания бензина, или путем подачи воздуха вокруг головки резака для оттеснения воды. Розжиг пламени осуществляется электрозапалом, что подключен к батарее аккумуляторов. Давление в бензиновых бачках создается азотом. В резаках бензин разбрызгивается в завихрительных головках и при этом испаряется.
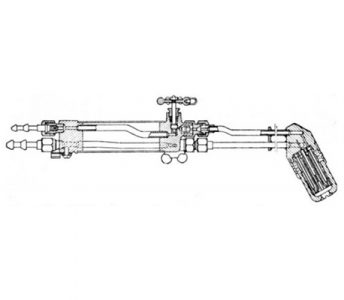
Для подводной резки широко используется спецустановка БУПР. Рампа кислородных баллонов, канистра с горючим, баллоны с азотом и пульт управления БУПР необходимо размещать над водой. Чрезмерный бензин, всплывая на поверхность воды, может заниматься, потому бензокислородная резка применяется в неглубоких водоемах и замкнутых пространствах.
Водородная резка металла осуществляется водородом, который вырабатывается в аппарате. Вследствие разложения молекул воды на 2 элемента, кислород и водород, получается водород. В результате чего появляется газовая смесь, при помощи которой можно осуществлять работы резке.
Читайте так же: Станок лазерной резки металла своими руками: процесс изготовления
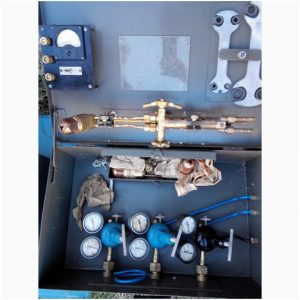
Технология подводной сварки и резки сдвоенным электродом
Подводная электродуговая резка металла нашло широкое применение как при изготовлении трубопроводов для газо-нефтеперерабатывающей отрасли так и в ремонтном производстве благодаря своей оперативности и простоте выполнения. Однако оно имеет значительные трудности как технологического так и металлургического характера. Технологические трудности заключаются в необходимости обеспечения герметичности оборудования и материалов для зажигания дуги под водой, что требует использования трубчатых электродов и дополнительного оборудования для подачи газа, что создает пузырь в котором зажигается дуга. Металлургические трудности обусловлены водородно-кислородной атмосферой парогазового пузыря, который формируется уже в процессе сварки под водой и способствует окислению легирующих элементов и насыщению металла сварочной ванны водородом, а ускоренное охлаждение окружающей водой приводит к его задержке в металле шва и образованию закалочных структур.
Так же могут использоваться сдвоенные экзотермические электроды для подводной резки металла. Эта технология заключается в том, что электродов размещены параллельно друг другу и подключения их к клеммам источника питания переменного тока. Такая технология позволяет зажигать дугу между электродами над водой и заглублять ее на небольшую глубину к месту сварки. Зажигания дуги под водой возможно с помощью осциллятора. В таком случае концы электродов необходимо изолировать, например термоклеем, с обеспечением воздушного канала между их торцами. После зажигания дуги электроды приближают к деталям. Как только расстояние между электродами и изделием становится меньше расстояния между самими электродами дуга начинает гореть между электродами и деталью, что позволяет выполнять как сварку, так и резку металла.
Читайте так же: Резка металла водой: область применения
§ 70. Подводная резка
Для разъединения металлических частей в подводных условиях наибольшее применение нашли ручная электрокислородная и бензокислородная резка. Кроме этих способов, подводную резку можно выполнять плавящимся электродом с покрытием, полуавтоматическую электрокислородную тонким плавящимся электродом, плазменно-дуговую и в отдельных случаях направленным взрывом.
Электрокислородная резка выполняется специальным электродом, изготовленным из стальной трубки размером 7×2,5 мм, покрытым толстым слоем водонепроницаемого состава. В трубку при помощи специального держателя от баллона по шлангу подается кислород под давлением 1,5 - 3,5 ат. Дуга разогревает металл, а кислород окисляет его, как и при обычной кислородной резке. Этот вид резки благодаря своей простоте нашел большое применение.
Процесс подводной резки происходит следующим образом: после включения рабочего тока на поверхности и подачи команды резчиком-водолазом резчик нажимает на рычаг кислородного клапана и возбуждает дугу, после чего начинает перемещение электрода вдоль линии реза. При резке металла большой толщины резчик углубляет электрод в металл для того, чтобы ввести в зону реза большее количество тепла. Скорость резки в вертикальном положении (сверху вниз) будет выше, чем в нижнем, так как в первом случае полнее используется режущий кислород.
Этим способом удается резать металл толщиной до 300 мм.
Для полуавтоматической электрокислородной резки тонкой проволокой разработан полуавтомат ППСР-300-2 (он же применяется и для сварки). Дуга горит в защитном газе, который подается через специальный шланг (вместе, с проволокой), в этом же шланге проходит токоведущий кабель. Кислород подводится по отдельному шлангу.
Скорость резки на установке ППСР-300-2 для толщины металла 10 мм при силе тока 270 - 280 А составляет 11 м/ч, для толщины металла 25 мм при силе тока 300 А - 2,5 - 2,8 м/ч.
Производительность полуавтоматической электрокислородной резки значительно выше ручной; это особенно важно при глубоководных работах, когда время пребывания резчика-водолаза под водой весьма ограничено.
При бензокислородной резке применяют специальный резак, работающий по принципу распыления бензина. К резаку подводятся три шланга: для подогревающего и режущего кислорода и распыленного (азотом) бензина. Подогревающее пламя зажигается под водой специальной электрозажигалкой, питаемой аккумуляторной батареей напряжением 12 В. Шланги, подводящие кислород и распыленный бензин, заключены в металлическую оплетку, позволяющую выполнять работу на глубине до 30 м.
Для бензокислородной резки металла толщиной от 5 до 100 мм под водой выпускается установка БУПР-61.
Скорость резки на установке БУПР-61 на глубине до 10 м: для толщины металла 10 мм - 22 м/ч, для толщины металла 100 мм - 6,5 м/ч.
Производительность подводной резки зависит от вида резки, прозрачности воды, доступности места резки, опытности водолаза и др.
В настоящее время для резки под водой начинают применять плазменную дугу. Разрабатывается резка под водой взрывом. Подводные резаки, действующие с помощью пороховых патронов, могут быть использованы для резки проволоки, кабелей, якорных цепей и других деталей, имеющих форму ленты или шнура. Ими можно перерезать стальную проволоку диаметром 1,6 - 38 мм и специальные кабели диаметром до 90 мм. Для осуществления, резки взрывом установка оснащается кумулятивным (направленным) взрывчатым зарядом, запальным шнуром, детонатором, электрическим кабелем и защитным ограждением материалов, примыкающих к месту реза.
Оборудование для резки в воде любым процессом существенно отличается от промышленного оборудования для резки на воздухе, оно намного сложнее и менее производительно.
В настоящее время техника подводной резки позволяет выполнять работы на глубине до 150 м и резать металл толщиной до 150 мм.
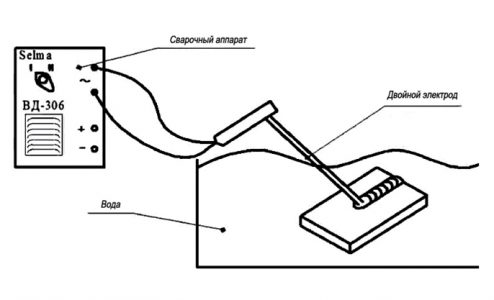
Реализация такого способа подводной сварки возможна с использованием обычных искусственных электродов с предварительно нанесенным на их поверхность водоотталкивающим изоляционным покрытием. Однако подводная сварка кроме технологических трудностей, имеет ряд металлургических связанных с насыщением металла сварочной ванны водородом и ускоренным охлаждением. Для исследования влияния этих факторов были проведены эксперименты с использованием для подводной сварки электродов марок АНО-21, МР-3, УОНИ 13/45. Все они позволяют формировать в воде качественный сварной шов с характерным металлическим блеском аустенитным нержавеющим сталям.
Общеизвестно, что высокоуглеродистые стали с мартенситной структурой имеют высокую твердость и малую пластичность. Эти обстоятельства имеют существенное значение для установления способности сварных швов заваренных под водой. Технология двухэлектродной подводной сварки и резки штучными электродами на ряду со своей простотой в использовании показала такую эффективность, какую не дает подводная кислородная резка металла. Полученные соединения имеют высокое качество и структуру с небольшой твердостью по глубине, что позволяет делать вывод о пригодности предлагаемой технологии в промышленности.
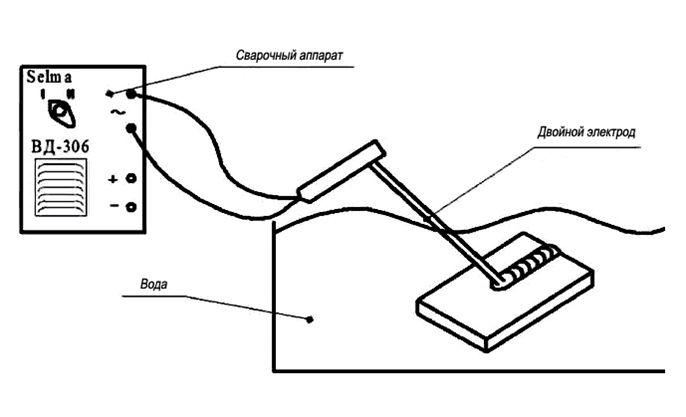
Резка металла под водой
Нетривиальная задача: надо разрезать металлическую конструкцию под водой не извлекая её: чем это можно сделать?
В современных способах обработки металла при необходимости выполнения работ под водой применяются два принципиально различных способа резки металла:
-
Электродуговой, при котором резка выполняется за счет термического воздействия на материал; -
Плазменная резка; -
Резка посредством создания условий протекания химической реакции, позволяющей металлу сгорать в кислороде, при этом струя кислорода выступает режущим инструментом. Способ получил название кислородной резки.
Последний способ в свою очередь делится на два подвида по типу нагрева металла:
-
Газокислородная, далее разделяющаяся на подвиды по типу используемого горючего газа для разогрева металла до температуры возгорания; -
Электрокислородная, при которой нагрев осуществляется посредством создания электрической дуги, делится на подвиды по типу применяемых в ней электродов.
Самым простым способом, который применяют в большинстве случаев для выполнения резки металла под водой на данный момент времени остается дуговая резка, для которого организую подачу тока не менее 500 a. Хорошие результаты дает этот способ при обработке металла толщиной до 2 см, с увеличением толщины производительность выполнения работ быстро снижается, а расход электродов растет, кроме того образуется неровный край реза. Поэтому, хоть и существует возможность применения электродуговой резки к порезам металла толщиной до 70 mm, но гораздо чаще для больших толщин металла или для резки нескольких слоев применяют электрокислородный способ.
Но и у этого способа есть свои минусы, так в первую очередь, это быстрый выход из строя электродов. Так самый доступный трубчатый стальной электрод в среднем сгорает за 1 мин и требуется его замена, что увеличивает время выполнения работ в три-четыре раза. Поэтому основные усилия в продвижении этого способа направлены на поиск и разработку более стойких электродов.
Читайте также: Пресс - упражнения, особенности тренировки, анатомия
По качеству создания кромки самые лучшие результаты показывает газокислородный способ резки. Но и этот способ имеет свои ограничения. Так, хорошие показатели резки получаются при разделении стали, титана и марганца и сплавов на их основе. А остальные металлы и сплавы, в частности, на основе меди и алюминия, почти не поддаются газокислородной обработке, потому что температура их плавления ниже температуры их активного окисления в кислороде, а это условие является одним из необходимых условий газокислородной резки.