Файл: 1. описание токарновинторезного станка 5 1Устройство и классификация станков 5.docx
Добавлен: 06.12.2023
Просмотров: 33
Скачиваний: 2
ВНИМАНИЕ! Если данный файл нарушает Ваши авторские права, то обязательно сообщите нам.
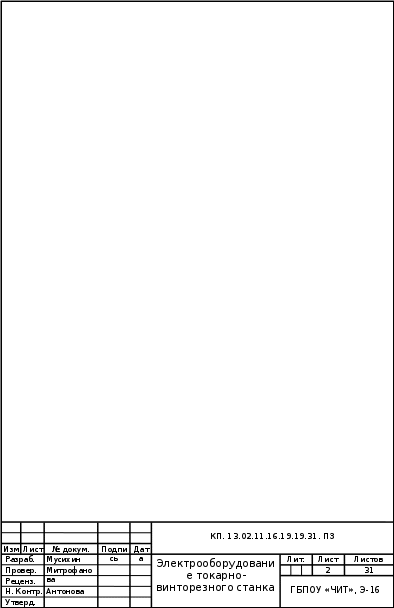
СОДЕРЖАНИЕ
СОДЕРЖАНИЕ 3
4
1.ОПИСАНИЕ ТОКАРНО-ВИНТОРЕЗНОГО СТАНКА 5
1.1Устройство и классификация станков 5
1.2 Описание главного привода станка, механизма подач, коробки подач 6
1.3 Резцедержатель, фартук и разъемная гайка 8
1.4 Суппорт 9
1.5 Задняя бабка 11
ЗАКЛЮЧЕНИЕ 22
СПИСОК ЛИТЕРАТУРЫ 23
Иные источники. 23
ПРИЛОЖЕНИЕ 1 24
Токарно-винторезный станок. 24
ВВЕДЕНИЕ
Объектами исследования в первом вопросе являются токарно-винторезные станки любой модификации.
В процессе исследования будут подробно разобраны составные компоненты устройства токарно-винторезных станков, принципы действия и особенности конструкции.
Разобраны основные характеристики и требования, предъявляемые к токарным станкам в зависимости от конкретных задач. Приведены основные принципы работы и виды конструкторских решений.
Во втором вопросе будут подробно рассмотрены виды токарных резцов, их возможные конструкции и технические реализации.
Приведены спецификации производства, стандарты Гост, и некоторые примеры применения.
-
ОПИСАНИЕ ТОКАРНО-ВИНТОРЕЗНОГО СТАНКА
-
Устройство и классификация станков
Токарно-винторезные станки предназначены для обработки единичных деталей или малых групп деталей, включая нарезание резьбы, если имеется ходовой винт. Однако бывают станки без ходового винта. На таких станках можно выполнять практически все виды токарных работ, за исключением нарезания резьбы резцом.
Техническими параметрами, по которым классифицируют токарно-винторезные станки, являются наибольший диаметр обрабатываемой заготовки (детали) – D или высота центров над станиной (равная 0,5 D), наибольшая длина обрабатываемой заготовки (детали) - L и масса станка. Для существующих на данное время станков эти характеристики стандартизированы и разбиты на группы (см приложение 1 таблица 1)
Наибольшая длина L обрабатываемой детали определяется расстоянием между центрами станка. Выпускаемые станки при одном и том же значении D могут иметь различные значения L.
Легкие токарные станки применяются в инструментальном производстве, приборостроении, часовой промышленности, в экспериментальных и опытных цехах предприятий. Эти станки выпускаются как с механической подачей, так и без нее.
На средних станках производится 70 - 80% общего объема токарных работ. Эти станки предназначены для чистовой и получистовой обработки, а также для нарезания резьб разных типов. Станки этого типа характеризуются высокой жесткостью, достаточной мощностью и широким диапазоном частот вращения шпинделя и подач инструмента, что позволяет обрабатывать детали на экономичных режимах с применением современных прогрессивных инструментов из твердых сплавов и сверхтвердых материалов. Средние станки оснащаются различными приспособлениями, расширяющими их технологические возможности, облегчающими труд рабочего и позволяющими повысить качество и сократить время обработки, имеют достаточно высокий уровень автоматизации.
Крупные и тяжелые токарные станки применяются в основном в тяжелом и энергетическом машиностроении, а также в других отраслях для обработки валков прокатных станов, железнодорожных колесных пар, роторов турбин и других крупногабаритных деталей
Все сборочные единицы и механизмы токарно-винторезных станков имеют одинаковое название, назначение и расположение (Приложение I рисунок 1). Типичный токарно-винторезный станок 16К20 завода "Красный пролетарий" показан на рисунке 2.
1.2 Описание главного привода станка, механизма подач, коробки подач
Главный привод станка.
В передней бабке станка размещены коробка скоростей и шпиндель, которые приводят во вращение обрабатываемую деталь при выбранных глубине резания и подаче. На рисунке 3 показано устройство коробки скоростей, которая работает следующим образом. Заготовка зажимается в кулачковом патроне, который крепится к фланцу шпинделя. Вращение от электродвигателя через ременную передачу и муфту включения передается на вал. Блок из трех шестерен, расположенный на валу, с помощью реечной передачи связан с рукояткой. Этой рукояткой блок шестерен вводится в зацепление с одним из зубчатых колес, жестко закрепленных на валу. Колеса 4 и 12 сопряжены соответственно с колесами 15 и 16, которые передают крутящий момент шпинделю через зубчатую муфту, соединенную с рукояткой 18. Если муфта передвинута вправо, то шпиндель получает вращение через зубчатое колесо 16, а если влево - через зубчатое колесо 15. Таким образом, коробка скоростей обеспечивает шесть ступеней частоты вращения шпинделя.
Механизм подач.
Связь шпинделя и суппорта станка для обеспечения оптимального режима резания осуществляется с помощью механизма подач, состоящего из реверсирующего устройства (трензеля) и гитары, которые осуществляют изменение направления и скорости перемещения суппорта.
Привод этого механизма осуществляется от коробки скоростей через трензель (рисунок 4), который состоит из четырех зубчатых колес а, б, в, г, связанных с рукояткой 19, переключением которой осуществляется реверс (т. е. изменение направления вращения) вала 20 (приводного вала суппорта). Позиции а, б, в, г, 19 и 20. При крайнем нижнем положении рукоятки 19 (положение А) зубчатые колеса а, б, в, г соединены последовательно и направление вращения вала 20 совпадает с направлением вращения шпинделя. При верхнем положении рукоятки 19 (положение В) соединены только зубчатые колеса а, в, г и направление вращения вала 20 изменяется на противоположное. В среднем положении рукоятки 19 (положение Б) зубчатые колеса б и в не соединяются с зубчатым колесом а и вал 20 не вращается. С помощью гитары (рисунок 5) устанавливают (настраивают) зубчатые колеса с определенным передаточным отношением, обеспечивающим необходимое перемещение суппорта на один оборот шпинделя. Расстояние L между валами 1 и 2 является постоянным. На валу 2 свободно установлен приклон 3 гитары, закрепленный болтом 4. Ось 5 промежуточных колес можно перемещать по радиальному пазу, тем самым изменяя расстояние А между центрами колес c и d. Дуговой паз приклона 3 позволяет регулировать размер В.
Коробка подач.
Назначение коробки подач - изменять скорости вращения ходового винта и ходового вала, чем достигается перемещение суппорта с выбранной скоростью в продольном и поперечном направлениях. Вал 14 в подшипниках 15 (смотри рисунок 5) коробки подач получает вращение от зубчатых колес гитары; вместе с ним вращается и имеет возможность перемещаться вдоль него зубчатое колесо 11 с рычагом 10. На одном конце рычага 10 вращается (на оси) зубчатое колесо 12, сопряженное с зубчатым колесом 11, а на другом - рукоятка 9, с помощью которой рычаг 10 перемещается вдоль вала 14 и может занимать любое из десяти положений (по числу зубчатых колес в механизме 1). В каждом из таких положений рычаг 10 поворачивается и удерживается штифтом 9, который входит в соответствующие отверстия на передней стенке 7 коробки подач. При этом зубчатое колесо 12 входит в зацепление с соответствующим зубчатым колесом 13 механизма 1, в результате чего устанавливается выбранное число оборотов вала 2. Вместе с валом 2 вращается зубчатое колесо 3, которое можно перемещать вдоль него рукояткой. При перемещении вправо зубчатое колесо 3 посредством кулачковой муфты 4 соединяется с ходовым винтом 5 и передает ему вращательное движение, а при перемещении влево - входит в зацепление с зубчатым колесом 8 и передает вращательное движение ходовому валу 6.
1.3 Резцедержатель, фартук и разъемная гайка
Устройство резцедержателя показано на рисунке 6 (приложение 1). В центрирующей расточке верхних салазок 5 установлена коническая оправка 3 с резьбовым концом. На конусе оправки установлена четырехсторонняя резцовая головка 6. При вращении рукоятки 4 головка 2 перемещается вниз по резьбе конической оправки 3 и через шайбу 1 и упорный подшипник обеспечивает жесткую посадку резцовой головки 6 на конической поверхности оправки 3. От поворота при закреплении резцовая головка удерживается шариком, который заклинивается между поверхностями, образованными пазом на основании конической оправки 3 и отверстием в резцовой головке 6. При необходимости сменить позицию инструмента рукоятку 4 поворачивают против часовой стрелки. При этом головка 2 поворачивается и перемещается вверх по резьбе конической оправки 3, снимая усилие затяжки резцовой головки 6 на конусе конической оправки 3. Одновременно головка 2 поворачивает резцовую головку 6 посредством тормозных колодок, фрикционно-связанных с поверхностью расточки головки 2 и соединенных с резцовой головкой 6 штифтами 7. При этом шарик, расположенный у основания конической оправки 3, не препятствует повороту резцовой головки, так как он утапливается в отверстие, сжимая пружину. Если в процессе работы рукоятка 4 (в зажатом положении) стала останавливаться в неудобном положении, то, изменяя толщину шайбы 1, можно установить ее в удобное для рабочего положение.
1.4 Суппорт
Одним из важнейших достижений машиностроения в начале XIX века стало распространение металлорежущих станков с суппортами - механическими держателями для резца. Каким бы простым и, на первый взгляд, незначительным не казался этот придаток к станку, можно без преувеличения сказать, что его влияние на усовершенствование и распространение машин было так же велика, как влияние изменений, произведенных Уаттом в паровой машине. Введение суппорта разом повлекло за собой усовершенствование и удешевление всех машин, дало толчок к новым усовершенствованиям и изобретениям.
Суппорт (рисунок 7 приложение 1) предназначен для перемещения режущего инструмента, закрепленного в резцедержателе во время обработки заготовки. Он состоит из нижних салазок (продольного суппорта) - 1, которые перемещаются по направляющим станины с помощью рукоятки - 15 и обеспечивают перемещение резца вдоль заготовки. На нижних салазках по направляющим - 12 перемещаются поперечные салазки (поперечный суппорт) 3, которые обеспечивают перемещение резца перпендикулярно оси вращения заготовки (детали). На поперечных салазках - 3 расположена поворотная плита - 4, которая закрепляется гайкой 10. По направляющим - 5 поворотной плиты перемещаются (с помощью рукоятки - 13) верхние салазки - 11, которые вместе с поворотной плитой могут поворачиваться в горизонтальной плоскости относительно поперечных салазок и обеспечивать перемещение резца под углом к оси вращения заготовки (детали). Резцедержатель (резцовая головка) - 6 с болтами - 8 крепится к верхним салазкам с помощью рукоятки 9, которая перемещается по винту 7. Привод перемещения суппорта производится от ходового винта 2, от ходового вала, расположенного под ходовым винтом, или вручную. Включение автоматических подач производится рукояткой 14.
Устройство поперечного суппорта показано на рисунке 8 (приложение 1). По направляющим продольного суппорта - 1 ходовым винтом - 12, оснащенным рукояткой - 10, перемещаются салазки поперечного суппорта. Ходовой винт - 12 закреплен одним концом в продольном суппорте - 1, а другим - связан с гайкой (состоящей из двух частей 15 и 13 и клина 14), которая крепится к поперечным салазкам - 9. Затягивая винт - 16, раздвигают (клином 14) гайки 15 и 13, благодаря чему. выбирается зазор между ходовым винтом 12 и гайкой 15. Величину перемещения поперечного суппорта определяют по лимбу 11. К поперечному суппорту крепится (гайками 7) поворотная плита 8, вместе с которой поворачиваются верхние салазки 6 и резцедержатель 5. На некоторых станках на поперечных салазках 9 устанавливается задний резцедержатель 2 для проточки канавок, отрезки и других работ, которые могут быть выполнены перемещением поперечного суппорта, а также кронштейн 3 с щитком 4, защищающим рабочего от попадания стружки и смазочно-охлаждающей жидкости.
1.5 Задняя бабка
Задняя бабка предназначена для фиксирования свободного конца длинной заготовки или для торцевой обработки заготовок.
Устройство задней бабки показано на рисунке.9 (приложение 1) В корпусе - 1 (при вращении винта - 5 маховиком - 7) перемещается пиноль - 4, закрепляемая рукояткой 3. В пиноли устанавливается центральный конический хвостовик - 2 (или инструмент). Задняя бабка перемещается по направляющим станка вручную или с помощью продольного суппорта. В рабочем неподвижном положении задняя бабка фиксируется рукояткой 6, которая соединена с тягой 8 и рычагом 9. Сила прижима рычага 9 тягой 8 к станине регулируется гайкой 11 и винтом 12. Более жесткое крепление задней бабки производится с помощью гайки 13 и винта 14, который прижимает к станине рычаг 10.
2. ПРИНЦИП ДЕЙСТВИЯ СХЕМЫ ТОКАРНО-ВИНТОРЕЗНОГО
СТАНКА
3. РАСЧЕТ И ВЫБОР ЭЛЕКТРОПРИВОДОВ И ДРУГИХ ЭЛЕКТРОПРИЕМНИКОВ
Электродвигатели к рабочим машинам и производственным механизмам выбирают по каталогам при соблюдении следующих условий:
1. Выбранный электродвигатель должен соответствовать параметрам питающей сети: напряжению и роду тока;
2. Мощность электродвигателя в процессе работы должна использоваться максимально;
3. При выборе двигателя по частоте вращения нужно стремиться к тому, чтобы частота вращения двигателя была как можно ближе к частоте вращения рабочей машины. Но при несовпадении частоты вращения рабочей машины и электродвигателя более целесообразно применить высокоскорстные электродвигатели (в частности, на 1500 мин