Файл: Сборник статей по итогам Международной научно практической конференции 04 мая 2018.docx
ВУЗ: Не указан
Категория: Не указан
Дисциплина: Не указана
Добавлен: 12.01.2024
Просмотров: 1184
Скачиваний: 1
СОДЕРЖАНИЕ
ДОСТОВЕРИЗАЦИЯ ДАННЫХ В АСУТП НА ПРЕДПРИЯТИЯХ ПЕРЕРАБОТКИ НЕФТИ
Список использованной литературы
Список использованной литературы
Научный руководитель: Апасов Т.К.
МЕТОДЫ БОРЬБЫ С АСПО ПРИ ЭКСПЛУАТАЦИИ СКВАЖИН, ОБОРУДОВАННЫХ УЭЦН,
В УСЛОВИЯХ ДРУЖНОГО МЕСТОРОЖДЕНИЯ
Список использованной литературы
АНАЛИЗ ТЕХНИЧЕСКОГО ОТЧЕТА В СТРОИТЕЛЬСТВЕ
Список использованной литературы:
ФУНКЦИОНАЛЬНАЯ АРХИТЕКТУРА СИСТЕМЫ ДЛЯ ПРОФЕССИОНАЛЬНЫХ ИТ СЕРВИСОВ
Список использованной литературы:
ОПТИМИЗАЦИЯ РЕЖИМОВ ДОБЫВАЮЩИХ СКВАЖИН НА КАЛЬЧИНСКОМ МЕСТОРОЖДЕНИИ
ЗАРЕЗКА БОКОВЫХ СТВОЛОВ НА КАЛЬЧИНСКОМ МЕСТОРОЖДЕНИИ
Список использованной литературы:
Список использованной литературы
Список использованной литературы
Ключевые слова:
щебеночно - мастичный асфальтобетон, стабилизирующие добавки, проектирование состава, показатель стекания вяжущего, расслаивание, водонасыщение.
В настоящее время наряду с обычным мелко - и крупнозернистым асфальтобетоном при проектировании и строительстве дорожных одежд активно применяются щебеночно - мастичного асфальтобетона (ЩМА). Технология её приготовления предусматривает обязательное включение стабилизирующих волокнистых добавок. Это делается для предотвращения неизбежного стекания излишков вяжущего в процессе транспортировки и укладки смеси.
С распространением ЩМА, на рынке появилось множество вариантов стабилизирующих добавок, различающихся по своим свойствам, составу и технологии применения. Условия строительства дорог и производства ЩМА всегда различны в регионах, что сказывается на технологии приготовления и выборе исходных материалов, в том числе и стабилизирующих добавок. Для выбора оптимального варианта было проведено сравнительное исследование четырех добавок. В ходе работы была выбрана смесь ЩМА - 15. Подбор состава осуществлялся с использованием материалов применяемых в IV дорожно - климатической зоне (ДКЗ).
При подборе состава и приготовления готовой смеси ЩМА - 15 используем следующие материалы:
-
Щебень фракции 5 / 10 ОАО «Орское КУ»; -
Щебень фракции 10 / 15 ОАО «Орское КУ»; -
Песок из отсевов дробления фракции 0 - 5 ОАО «Орское КУ»; -
Минеральный порошок ООО «Самаратрансстрой»; -
Полимерно - битумное вяжущее (ПБВ 60); -
Адгезол № 6.
Минеральная часть смеси ЩМА подобрана на основании зерновых составов исходных компонентов (таблица 1 - 4), по формуле 1 с учетом предельно допустимых значений
каждой фракции в составе готовой смеси в соответствии с требованиями ГОСТ 31015 - 2002 [2] (рисунок 1).
Таблица1–Составщебняфракции5-10
№ сита | Масса на сите, г | Частный остаток, % | Полный остаток, % | Полный проход, % |
40 | 0 | 0 | 0 | 100 |
20 | 0 | 0 | 0 | 100 |
15 | 0 | 0 | 0 | 100 |
10 | 116 | 2,3 | 2,3 | 87,7 |
5 | 4493 | 89,9 | 92,2 | 7,8 |
2,5 | 192 | 3,8 | 96,0 | 4,0 |
1,25 | 34 | 0,7 | 96,7 | 3,3 |
0,63 | 19 | 0,4 | 97,1 | 2,9 |
0,315 | 14 | 0,3 | 97,4 | 2,6 |
0,16 | 26 | 0,4 | 97,8 | 2,2 |
0,071 | 60 | 1,2 | 99,0 | 1,0 |
| 52 | 1,0 | 100 | 0 |
Таблица2–Составщебняфракции10-15
№ сита | Масса на сите, г | Частный остаток, % | Полный остаток, % | Полный проход, % |
40 | 0 | 0 | 0 | 100 |
20 | 0 | 0 | 0 | 100 |
15 | 1765 | 11,6 | 11,6 | 88,4 |
10 | 12347 | 81,5 | 93,1 | 6,9 |
5 | 890 | 5,9 | 99,0 | 1 |
2,5 | 22 | 0,1 | 99,1 | 0,9 |
1,25 | 11 | 0,1 | 99,2 | 0,8 |
0,63 | 10 | 0,1 | 99,3 | 0,7 |
0,315 | 13 | 0,1 | 99,4 | 0,6 |
0,16 | 30 | 0,2 | 99,6 | 0,4 |
0,071 | 53 | 0,3 | 99,9 | 0,1 |
| 18 | 0,1 | 100 | 0 |
Таблица3–Составпескаизотсевовдробления
№ сита | Масса на сите, г | Частный остаток, % | Полный остаток, % | Полный проход, % |
40 | 0 | 0 | 0 | 100 |
20 | 0 | 0 | 0 | 100 |
15 | 0 | 0 | 0 | 100 |
10 | 0 | 0 | 0 | 100 |
5 | 26 | 5,2 | 5,2 | 94,8 |
2,5 | 60 | 12,0 | 17,2 | 82,8 |
1,25 | 98 | 19,6 | 36,8 | 63,12 |
0,63 | 85 | 17,0 | 53,8 | 46,2 |
0,315 | 65 | 13,0 | 66,8 | 33,2 |
0,16 | 57 | 11,4 | 78,2 | 21,8 |
0,071 | 40 | 8,0 | 86,2 | 13,8 |
| 69 | 13,8 | 100 | 0 |
Таблица4–Составминеральногопорошка
№ сита | №1 | №2 | №3 | №4 | Среднее |
1,25 | 99,68 | 99,96 | 100 | 100 | 99,91 |
0,63 | 99,5 | 99,9 | 99,9 | 99,9 | 99,8 |
0,315 | 99,1 | 99,6 | 99,5 | 99,7 | 99,475 |
0,16 | 96,1 | 97,1 | 96,7 | 97,2 | 96,775 |
0,071 | 81,7 | 82,6 | 82 | 82,8 | 82,275 |
| | | | | |
∑????
????j????ij
i
???? = j=1(1)
100
где – содержание i- й фракции в смеси, % ;
j– порядковый номер компоненты;
n – количество компонентов в смеси;
– содержание j- й компоненты в смеси, % ;
– содержание i- й фракции в j- й компоненте, % .
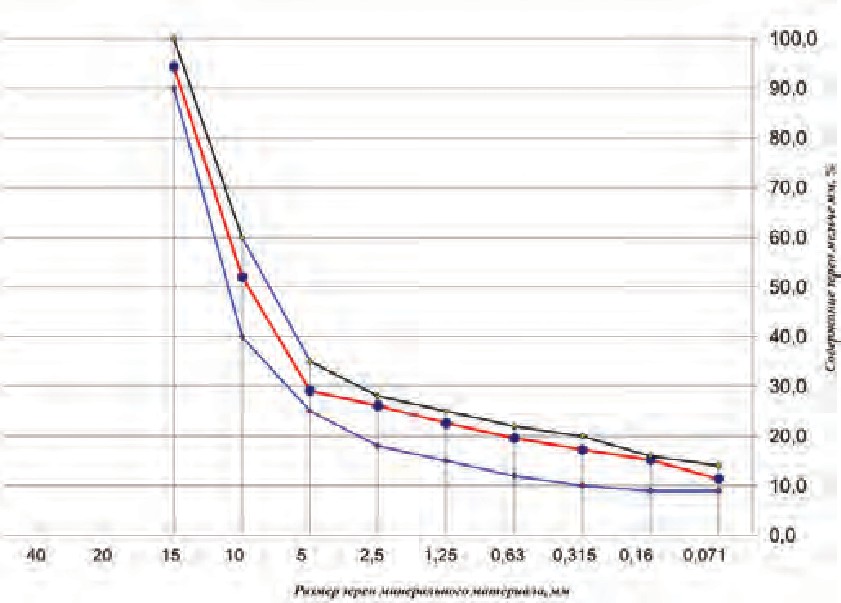
Рисунок2.Графикзерновогосоставаминеральнойчасти
Для уточнения оптимального количества вяжущего были выполнены пробные замесы для определения водонасыщения, остаточной пористости и стекания вяжущего. На основании результатов испытаний, содержание вяжущего в смеси принято 5,5 % сверх 100
% от общей массы смеси.
В качестве стабилизирующих добавок рассматривалось четыре варианта:
-
СТАБ №1 -
СТАБ №2 -
СТАБ №3 -
«Viatop premium»
Гранулы стабилизатора добавлялись в раздавленном виде при повышенной температуре каменных материалов (220 - 230 °С) в количестве 0,4 %
В ходе опыта соблюдался технологический режим, приближённый к реальным производственным условиям.
Высушенные каменные материалы разогревались до температуры 220 - 230 °С. Затем был добавлен холодный минеральный порошок и стабилизирующая добавка. Затем всё перемешивалось и снова ставилось разогреваться на 20 - 25 минут. После чего добавляли разогретое до 165 °С ПБВ, перемешивали и разогревали в сушильном шкафу в течении 15 минут. Температура в сушильном шкафу 230°С. Изготовление образцов проходит при температурах сушильного шкафа - 175°С, цилиндрических форм 110 - 130°С. Водонасыщение, истинную плотность и остаточную пористость определяли по ГОСТ 12801 – 98 [1]. Показатель стекания вяжущего определяем по приложению «В» ГОСТ 31015