Файл: Сборник статей по итогам Международной научно практической конференции 04 мая 2018.docx
ВУЗ: Не указан
Категория: Не указан
Дисциплина: Не указана
Добавлен: 12.01.2024
Просмотров: 1195
Скачиваний: 1
СОДЕРЖАНИЕ
ДОСТОВЕРИЗАЦИЯ ДАННЫХ В АСУТП НА ПРЕДПРИЯТИЯХ ПЕРЕРАБОТКИ НЕФТИ
Список использованной литературы
Список использованной литературы
Научный руководитель: Апасов Т.К.
МЕТОДЫ БОРЬБЫ С АСПО ПРИ ЭКСПЛУАТАЦИИ СКВАЖИН, ОБОРУДОВАННЫХ УЭЦН,
В УСЛОВИЯХ ДРУЖНОГО МЕСТОРОЖДЕНИЯ
Список использованной литературы
АНАЛИЗ ТЕХНИЧЕСКОГО ОТЧЕТА В СТРОИТЕЛЬСТВЕ
Список использованной литературы:
ФУНКЦИОНАЛЬНАЯ АРХИТЕКТУРА СИСТЕМЫ ДЛЯ ПРОФЕССИОНАЛЬНЫХ ИТ СЕРВИСОВ
Список использованной литературы:
ОПТИМИЗАЦИЯ РЕЖИМОВ ДОБЫВАЮЩИХ СКВАЖИН НА КАЛЬЧИНСКОМ МЕСТОРОЖДЕНИИ
ЗАРЕЗКА БОКОВЫХ СТВОЛОВ НА КАЛЬЧИНСКОМ МЕСТОРОЖДЕНИИ
Список использованной литературы:
Список использованной литературы
Список использованной литературы
Ключевые слова:
процесс прокаливания, анодная масса, снижение расхода угольной пены, повышение качества анода, технологический процесс, металлургическое предприятие
Актуальность совершенствования технологии прокаливания нефтяных коксов на металлургическом производстве обусловлена растущими финансовыми, материальными и трудовыми затратами, что негативно сказывается на себестоимости конечной продукции, а также современными требованиями рыночных отношений – минимизировать экономические потери за счет снижения расхода анодной массы, образования угольной пены в ванне.
Целью данной работы является разработка и экономическое обоснование мероприятий по оптимизации режима прокаливания нефтяных коксов на АО «РУСАЛ Красноярск».
Прокаливание сырых коксов
Под прокаливанием кокса понимают процесс обработки кокса в течение определенного времени при высоких температурах. Прокаливание кокса относится к одному из основных процессов в производстве анодной массы, поскольку основные ее физико - химические и эксплуатационные свойства зависят от качества прокаленного кокса. Прокаливание кокса осуществляется в барабанных вращающихся печах типа УВП 3×45 (диаметром 3 м, длиной 45 м) [1].
Одним из основных факторов, определяющих эффективность работы прокалочной печи, является коэффициент заполнения печи, т.е. количество кокса
единовременно находящегося в печи. При увеличении коэффициента заполнения печи выше оптимального, ухудшаются условия теплообмена кокса с топочными газами и часть материала в слое кокса не соприкасается ни с футеровкой печи, ни с раскаленными газами. В этом случае физико - химические процессы в коксе не успевают закончиться. При заполнении прокалочной печи ниже оптимального, возможно «перепрокаливание» кокса и тепловая энергия топочных газов используется не полностью.
Другим фактором, определяющим эффективность работы прокалочной печи, является удельный расход топлива на единицу прокаленного материала. Удельный расход топлива зависит от многих факторов: конструкции горелочного устройства, качества топлива и его температуры, количества подаваемого вторичного воздуха, состояния перемешивающих порогов, коэффициента заполнения печи коксом. Так, например, при форсировании работы печи, т.е. одновременном увеличении коэффициента заполнения барабана печи коксом и подачи мазута, повышение производительности печи возможно, однако расход топлива на единицу материала в этом случае возрастает, а также существует опасность резкого увеличения пылеуноса в связи с ростом скорости печных газов [2].
Выбор оптимального режима прокаливания сложен и зависит от целого ряда факторов. Существенное влияние имеет не только температура прокалки кокса, но и его влажность, крупность и время нахождения материала в зоне высоких температур.
Прокаливание проводят
при температуре в зоне прокаливания 1240–1300 °С; при этом полностью удаляется влага, происходят процессы разложения сложных углеводородов с удалением летучих веществ и прежде всего водорода, а также уплотнение структуры кокса. Удаление летучих веществ начинается при температурах 400–450 °С и достигает максимального значения при 600–800 °С. При этих температурах выделение летучих веществ происходит за счет простой отгонки (дистилляции) и только частично за счет деструкции (разложения углеводородов с выделением водорода). С повышением температуры прокалки процесс разложения интенсифицируется, при этом сложные углеводороды разлагаются на элементарные составляющие: водород и пиролитический углерод. Последний имеет способность откладываться в порах кокса и повышать его объемную массу. Удаление углеводородов, отложение пиролитического углерода, формирование плотной структуры и частичная рекристаллизация кокса приводят к его
уплотнению и повышению
истинной плотности [3].
В процессе прокаливания происходит объемная усадка кокса. Степень усадки для разных видов коксов при одинаковой температуре прокалки неодинакова и зависит от качества исходного кокса (в основном, содержания летучих веществ).
Таким образом, в результате физико - химических процессов при температуре 1100– 1200°С в прокаливаемых углеродистых материалах возрастает содержание углерода (в основном за счет снижения содержания водорода), полностью удаляется влага и летучие, происходит объемная усадка, увеличивается истинная плотность, повышается электропроводность и механическая прочность, снижается окисляемость (реакционная способность). Все эти превращения обеспечивают получение прокаленного кокса требуемого качества [4].
Эффективность процесса прокалки контролируется по показателю истинной плотности прокаленного кокса. Для этой цели после холодильников прокалочного отделения установлены пробоотборники, с помощью которых производится отбор проб прокаленного кокса от каждой печи. На основании результатов анализа, а также технологических параметров работы печей на момент отбора проб, прокальщик при необходимости производит корректировку технологических параметров прокаливания.
Мероприятия. Для достижения повышенной истиной плотности прокаленного кокса, нужно повысить температуру в зоне прокаливания, для этого нужно выполнить ряд следующих мероприятий по прокалочному комплексу.
-
Установить внутри (в футеровке) прокалочной печи продольные пороги из армированного огнеупорного бетона. -
Увеличить разрежения в печи. -
Заменить запечный дымосос на более производительный (ДН - 24). -
Снизить аэродинамическое сопротивление газовому потоку в месте его перехода из печи в холодную головку (изменением конфигурации входного отверстия в холодную головку печи). -
Снизить подсосы воздуха в газоходный тракт прокалочного комплекса – установкой на холодной головке печи комбинированного (лабиринтно - графито - сегментного) уплотнения. -
Заменить дозатор сырого кокса в печи ДВЛ 16 на более производительный и современный – типа 4488 ДН - У. -
Усовершенствовать узел сжигания мазута (укоротить на 700 мм водоохлаждаемую фурму и мазутную форсунку). -
Смонтировать систему рециркуляции газов из холодильника в печь в комбинации с системой впрыска охлаждающей воды внутрь загрузочной головки холодильников ( в т.ч. осуществить замену частотного преобразователя дымососа подачи воздуха и воздухоохлаждаемой фурмы). -
Доработать и настроить существующая АСУ ТА прокаливания. -
Увеличить температуру в зоне прокаливания до 1320 °С.
Зависимость истиной плотности прокаленного кокса и выхода угольной пены
С середины 2017 г. и по сегодняшний день выход угольной пены в корпусах электролиза находится на уровне 30 и менее кг / т Al. Это значительно ниже, чем предыдущие периоды до 2016 г., одной из причин снижения можно предположить повышение истинной плотности прокаленного кокса со среднего значения 2,03 г / см3 до 2,057 г / см3 начиная с июля 2017 г. по декабрь 2017 г.
Оценим зависимости изменения показателей качества анодной массы от значений истинной плотности прокаленного кокса и далее динамику изменения выхода угольной пены.
Теоретически, повышение истинной плотности кокса должно увеличить истинную плотность анодной массы и снизить ее реакционную способность (рис 1.). Учитывая, что основные поставщики пека и сырых коксов в течение 2017г. значимо не изменились, за исключением некоторых вариаций и неритмичных их поставок, первичный анализ провиден с начала 2017 г. по среднемесячным показателям:
-
истинная плотность прокаленного кокса, -
качество анодной массы, -
выход угольной пены.
г/смм3
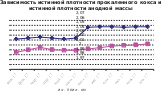