Файл: Задача 1 3 Задача 2 6 Задача 3 9 Библиографический список 13.docx
Добавлен: 24.10.2023
Просмотров: 73
Скачиваний: 4
ВНИМАНИЕ! Если данный файл нарушает Ваши авторские права, то обязательно сообщите нам.
t=h=2.5 мм.
-
Назначаем подачу S0 [2, табл. 3.20]. При черновом подрезании торца при диаметре заготовки 85 мм при глубине резания 2.5 мм 50= 0,6...0,9 мм/об. Принимаем 50=0,6 мм/об. -
Корректируем подачу по паспортным данным станка и принимаем 50=0,6 мм/об. -
Назначаем период стойкости резца. Среднее значение стойкости Т при одноинструментой обработке составляет 60...90 мин. Принимаем Т=60 мин [2, табл. 1.7].
Допустимый износ резца из твердого сплава по задней поверхности при обработке чугуна h3 =0,6...0,8 мм [2, табл.1.5]..
-
Определяем скорость главного движения резания, допускаемую режущими свойствами резца:
V Cv
TmtxSy
Kv, м/мин.

где Т – период стойкости резца.
Сv- коэффициент, зависящий от обрабатываемого материала, вида работ и толщины среза;
т, хv, уv- показатели степени при значениях стойкости инструмента Т, глубины резания t и подачи S ([2], табл. 17, с. 270);
Кv - общий поправочный коэффициент на скорость резания, рассчитываемый как произведение нескольких поправочных коэффициентов, отражающих отличие фактического значения одного из условий резания от стандартизированного при экспериментальном определении табличного коэффициента
Kv=KмvKпvKиvKφvKφ1vKr,
где Kмv - поправочный коэффициент на физико-механические свойства обрабатываемого материала. По [2, табл. 1, с 358]
КмvК
190 n
НВ
190 1,25
190
1,0 ;
г
Kпv - поправочный коэффициент на состояние поверхности заготовки. По [2, табл. 5, с 361] Kпv=1,0;
Kиv - поправочный коэффициент на марку инструментального материала.
По [2, табл. 6, 361] для материала ВК8 Kиv=0,83;
KP 0.83 11 0.83
По [1, табл. 17, с. 367] Сv=243, xv=0,15, yv=0,4, mv=0,2.
V 243
600,2 2,50,15 0,60,4
0,83 95.1 м/мин.
8. Определяем частоту вращения шпинделя, соответствующую найденной скорости:
n 1000Vи
D
1000 95.1 356мин1
3.14 85
Корректируем частоту вращения шпинделя по паспортным данным станка и устанавливаем действительное значение частоты вращения: nд=315 мин”1.
-
Определяем действительную скорость главного движения резания \
V Dnдд1000
3,14 85 315 84м/ мин
1000
10. Определение силы резания
Px,y,z
10Cp
tx SyVn K
o
p
Для заданных условий обработки СРz=92, xPz,=1,0, yPz,=0,75, nPz=0.
Кр - общий поправочный коэффициент, представляющий собой произведение поправочных коэффициентов на механические свойства обрабатываемого материала и на выбранные геометрические параметры резца
КРг= КмрКφрКγрКλ рКгр,
где Кмр- поправочный коэффициент, учитывающий влияние качества
190 0,4
обрабатываемого материала. KMp 190 1,0
По[2 табл. 23, с. 374]Кφр=1,0,Кγр=1,0,Кλр=1,0-поправочные коэффициенты, учитывающие влияние геометрических параметров режущей части инструмента.
z
P 10 92 2,51,0 0,60,75 840 1,0 1,0 1,0 1,0 1568Н
-
Определяем эффективную мощность резания
N'
PzVст
1020 60
1568 84 2,2кВт
1020 60
-
Проверяем, достаточна ли мощность привода станка. Необходимо, чтобы Nрез ≤Nшп- Мощность на шпинделе станка по приводу
Nmin=Nдη.
У станка 16К20 Nд=10 кВт; η=0,75; Nmin=10*0,75=7,5 кВт. Следовательно, Nрез<Nmu(0,7< 7,5), т. е. обработка возможна.
12. Основное время
,
Li
То nS
0
где i— число рабочих ходов.
Длина рабочего хода резца L=I+у+Δ мм.
Врезание резца у=l ctg φ=2,5ctg45° =2,5 мм. Перебег резца Δ=1…3 мм; принимаем Δ=1 мм.
L 85 65 2.5 1 13,5мм
2
i= 1;
То
13,5 1
315 0,6
0,07мин.
ЗАДАЧА 1.3
На токарно-винторезном станке 16Б16П растачивают глухого отверстие диаметром d=38 мм до диаметра D=41H12 мм. Длина обрабатываемой поверхности l=35 мм, длина заготовки 55 мм. Заготовка выполнена из стали 40Х с пределом прочности σв=700 МПа. Заготовка отливка без корки. Растачивание черновое Rz80 мкм. Система СПИД - средняя. Эскиз обработки показан на рис.3.
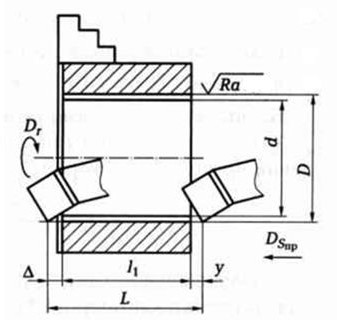
Рисунок 3 – Эскиз растачивания А. Выбор резца и его геометрических элементов.
-
Выбираем токарный расточный резец для обработки глухих отверстий по ГОСТ 18883—73 [2, табл. 13 с. 123]. Для чернового точения применяется твердый сплав Т5К10 [2, табл. 3.13]. Материал корпуса резца — сталь 45. Размеры поперечного сечения корпуса резца В*Н =25x25 мм. Длина резца 200 мм. -
Геометрические элементы резца выбираем по справочным таблицам:
-
при растачивании глухого отверстия в стальной заготовке со высокой жесткостью принимаем φ=90° [2, табл. 1.3]; -
вспомогательный угол в плане φ1=5...10°, принимаем φ1=15°[2, табл.
1.4];
Геометрические элементы резца выбираем по [2, табл. 3.7]. Форму заточки передней поверхности принимаем радиусную с фаской ɣф =-5°.
Передний и задний углы выбираем по [2, табл.1.1]: α = 8°, ɣ=12°.
При черновом растачивании стали λ=0…5° [2, табл.1.2]. Принимаем λ=5°.
Б. Назначение режима резания (нормативным таблицам).
-
Глубина резания при снятии припуска за один рабочий ход равна припуску на сторону:
t D d
2
41 38 1,5мм.
2
-
Назначаем подачу S0[2, табл.3,19). Для чернового растачивания заготовки из стали диаметром 41 мм и глубине резания 1,5 мм выбираем подачу S0=0,5...0,3 мм/об. Принимаем среднее значение S0=0,4 мм/об.
Корректируем подачу по паспортным данным станка 16Б16П и принимаем S0 =0,4 мм/об ([4] Приложение 4).
-
Назначаем период стойкости резца. Среднее значение стойкости при одноинструментной обработке Т=60...90 мин. Принимаем Т=90 мин [2 табл.1.7].
Допустимый износ резца из твердого сплава по задней поверхности для черновой обработки стали h3 =1,0…1,4 мм [2, табл.1.5].
-
Определяем скорость главного движения резания, допускаемую режущими свойствами резца [2, табл. 3.31], по формуле
Vи=VTa6nKMv.
где Vтабл – табличное значение скорости резания.
Для стали с пределом прочности σв=700 МПа при глубине резания t =1,5 мм и подаче S0 =0,4 мм/об скорость Vтабл =180 м/мин.
Поправочный коэффициент на скорость резания при точении [2, табл.3.33.
KV KMV KTV KИV KV
Коэффициент, учитывающий твердость обрабатываемого материала КМ=1,15.
Коэффициент, учитывающий материал режущей части инструмента КИ=0,65.
Коэффициент, учитывающий влияние главного угла в плане Кφ=0,88 С учетом поправочных коэффициентов
Vи=180 . 1,15 .0,65 .0,88=118,4 м/мин .