Файл: Отчет учебная практика (практика по получению первичных профессиональных умений и навыков).docx
Добавлен: 24.10.2023
Просмотров: 295
Скачиваний: 7
ВНИМАНИЕ! Если данный файл нарушает Ваши авторские права, то обязательно сообщите нам.
СОДЕРЖАНИЕ
2.2 Характеристика сточных вод ПАО «Тольяттиазот»
2.3 Обращение с отходами производства
3 Мероприятия по снижению негативного воздействия на окружающую природную среду
3.2 Охрана поверхностных вод и территории от загрязнения сточными водами
3.3 Охрана окружающей среды при складировании отходов
3.4 Рациональное использование земель
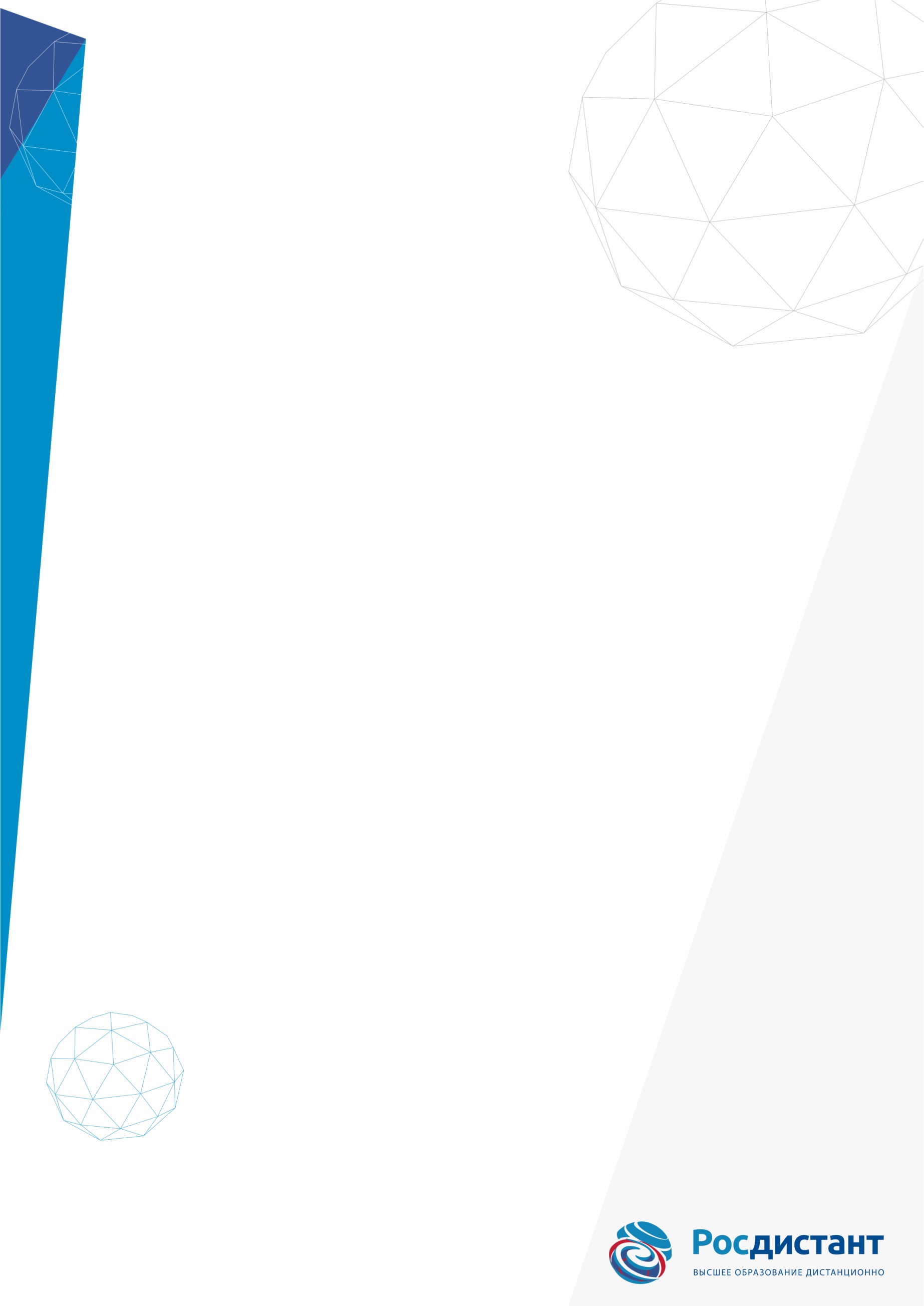
МИНИСТЕРСТВО НАУКИ И ВЫСШЕГО ОБРАЗОВАНИЯ РОССИЙСКОЙ ФЕДЕРАЦИИ
федеральное государственное бюджетное образовательное учреждение
высшего образования
«Тольяттинский государственный университет»
Институт химии и энергетики
(Наименование института)
Химическая технология и ресурсосбережение
(Наименование кафедры, центра, департамента)
ОТЧЕТ
учебная практика (практика по получению первичных профессиональных умений и навыков)
(Наименование практики)
обучающегося Анастасии Викторовны Нахаловой
(И.О. Фамилия)
НАПРАВЛЕНИЕ ПОДГОТОВКИ (СПЕЦИАЛЬНОСТЬ) ЭНЕРГО- И РЕСУРСОСБЕРЕГАЮЩИЕ ПРОЦЕССЫ В ХИМИЧЕСКОЙ ТЕХНОЛОГИИ, НЕФТЕХИМИИ И БИОТЕХНОЛОГИИ
ГРУППА ЭРТбп-1801а
РУКОВОДИТЕЛЬ
ПРАКТИКИ ОТ УНИВЕРСИТЕТА: шевченко юлия николаевна РПиР
(фамилия, имя, отчество, должность)
Руководитель практики от организации
(предприятия, учреждения, сообщества)
_Парфёнов Олег Юрьевич, начальник цеха №17_______________________
(фамилия, имя, отчество, должность)
Тольятти 2021
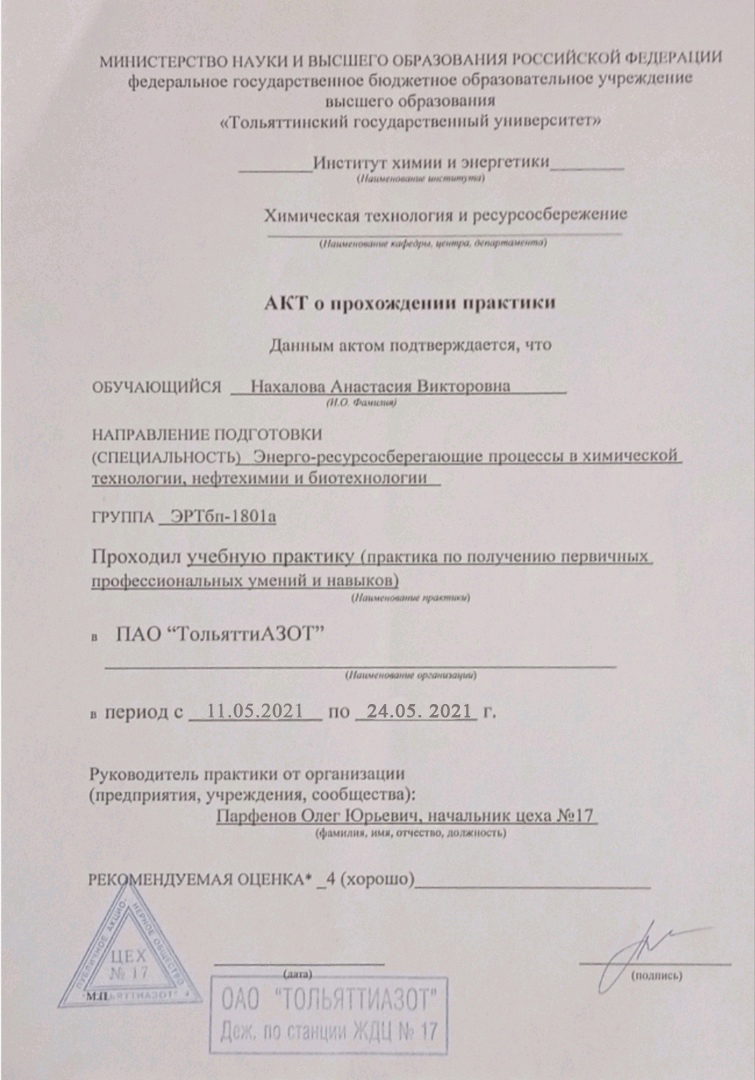
Содержание
ОТЧЕТ 1
обучающегося Анастасии Викторовны Нахаловой 1
(И.О. Фамилия) 1
РУКОВОДИТЕЛЬ 1
ПРАКТИКИ ОТ УНИВЕРСИТЕТА: шевченко юлия николаевна РПиР 1
(фамилия, имя, отчество, должность) 1
Тольятти 2021 1
Введение 4
1 Характеристика деятельности предприятия 5
1.1 Общие сведения о предприятии 5
1.2 История создания и развития организации 6
1.3 Характеристика выпускаемой продукции 10
1.4 Краткое описание технологического процесса 13
2 Воздействие на ООС 23
2.1 Выбросы в атмосферу 23
2.2 Характеристика сточных вод ПАО «Тольяттиазот» 24
2.3 Обращение с отходами производства 26
3 Мероприятия по снижению негативного воздействия на окружающую природную среду 32
3.1 Охрана атмосферы 32
3.2 Охрана поверхностных вод и территории от загрязнения сточными водами 32
3.3 Охрана окружающей среды при складировании отходов 33
3.4 Рациональное использование земель 34
4 Производственный экологический контроль 35
Заключение 36
Список используемой литературы и источников 38
Введение
Учебная практика – это форма учебных занятий, которая проходит в организациях (предприятиях) разных форм собственности и организационно – правовых форм.
Целью настоящей учебной практики является закрепление и углубление теоретических знаний, и приобретение практических навыков и компетенций в сфере профессиональной деятельности.
В задачи учебной практики входит:
1) ознакомление с предприятием, работой предприятия, реальным технологическим процессом;
2) приобретение первых практических навыков по избранной специальности;
3) анализ технологической документации (технологический регламент производства, протоколы исследований качества возвратных вод, отчетов по инвентаризации отходов; инвентаризации стационарных источников выбросов);
4) подготовка отчета о выполненной работе;
5) приобретение опыта работы.
Объектом практики является предприятие ПАО «Тольяттиазот».
Сроки прохождения практики: с 11.05.2021 по 24.05.2021.
1 Характеристика деятельности предприятия
1.1 Общие сведения о предприятии
ПАО «Тольяттиазот» (ТОАЗ) – является одним из крупнейших предприятий химической промышленности России, и входит в тройку основных производителей аммиака в стране, а также в десятку мировых лидеров по производству аммиака. ПАО «Тольяттиазот» – единственный в мире химический комбинат, который способен производить до 3 миллионов тонн аммиака ежегодно.
Основной деятельностью ПАО «Тольяттиазот» является выпуск минеральных удобрений и различной химической продукции. В настоящее время завод включает в себя 7 агрегатов по производству аммиака и 2 агрегата карбамида. Указанные агрегаты расположены на территории производственной площадки более чем 200 га.
Заглядывая в историю развития химической отрасли государства, необходимо отметить, что с самого своего основания ТОАЗ играл значимую роль не только в развитии химической отрасли страны, но и в обеспечении благополучия родного города Тольятти, а также, несомненно и всей Самарской области. В настоящее время ПАО «Тольяттиазот» входит в пятерку крупнейших налогоплательщиков региона. Кроме того, развитая инфраструктура гарантирует поставки продукции заказчикам, находящимся не только в Российской Федерации, но заказчикам в десятках стран на 5 континентах. Это возможно благодаря собственному железнодорожному парку, состоящему из более 1400 вагонов. Кроме того, ТОАЗ имеет доступ к уникальному аммиакопроводу протяженностью более 2000 км «Тольятти-Одесса». [1-3].
Согласно отчетов за год на ПАО «Тольяттиазот» на производственных мощностях выпускается следующая основная продукция:
1) карбамид - 960 тыс. тонн;
2) углекислота - порядка 70 тыс. тонн
3) жидкий аммиак - 3 млн. тонн.
На мировом рынке Россия входит в десятку лидеров по производству аммиака. Аммиак - один из наиболее важных продуктов химической промышленности и синтеза, как в России, так и в мире. Аммиак применяется в качестве источника азота (сырья) для производства минеральных удобрений. Также аммиак применяется в таких производствах как:
- производство пластмасс;
- производство взрывчатых веществ;
- производство (синтез) гидразина, аминов, амидов, нитрилов
- производство органических азотных соединений,
- производство красок
- производство фармацевтических препаратов
- и др.
Жидкий аммиак является также важным растворителем. Кроме того, жидкий аммиак применяется в качестве хладагента (R-717).
На территории России действуют 28 агрегатов по производству аммиака, на которых в год производится более 13 млн. тонн продукции.
1.2 История создания и развития организации
Любая учебная практика начинается с вводного инструктажа по охране труда, а также с ознакомления с предприятием, с его историей создания и развития. Поэтому в данной части представлена история создания и развития ПАО «Тольяттиазот». Основными источниками изложенных в настоящем разделе сведений являются архивные материалы, исторические сведения, а также, что, несомненно, информация с официального сайта предприятия.
Согласно исторических сведений в начале 20-го века возникли растущие опасения нехватки продовольствия в связи с быстрым ростом населения Земли. Для решения продовольственной проблемы необходимо было увеличивать объемы производства в сельском хозяйстве, в частности.
Огромные территории нашей страны требовали значительного объема удобрений, т.к. не были в достаточной мере пригодными для сельского хозяйства. В связи с этим научное сообщество нашего государства, а также разных стран начало эксперименты по связыванию атмосферного азота в аммиак, и использование аммиака как основы для других соединений.
В конце 60-х годов того же столетия, с целью решения вышеуказанной проблемы в СССР начались переговоры с иностранными компаниями о поставках оборудования, а также переговоры по организации собственного производства аммиака внутри страны.
Именно с этого момента и начинается история ПАО «Тольяттиазот»[1].
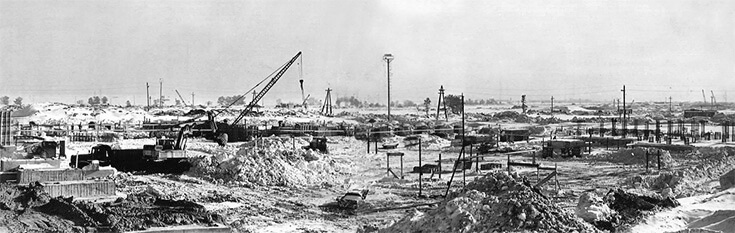
Рисунок 1 – Фото начала строительства «Тольяттиазот» [1]
Тогда, в ноябре 1974 года началось строительство Тольяттинского азотного завода, которому в последствии суждено было стать одним из лидеров мировой химической промышленности. Объект возводился по соглашению с известной в то время фирмой Арманда Хаммера «Оксидентал Петролеум» (США). Именно благодаря этому сотрудничеству, наше государство получило современное оборудование и передовые технологии, которые обеспечили высокую эффективность в работе агрегатов производства карбамида и аммиака.
Свои первые тонны аммиака «Тольяттиазот» произвел и выдал в апреле 1979 года. В этом же году был введён эксплуатацию первый агрегат по производству карбамида. Буквально уже через полгода за этим последовал пуск второго агрегата. На «Тольяттиазот» сдавался объект за объектом, и уже в августе 1983 года была получена первая продукция жидкой двуокиси углерода. Затем в октябре 1985 года была сдана в эксплуатацию установка по получению карбамидоформальдегидной смолы (сокращенно - КФС). А в июне 1986 года был введён в эксплуатацию седьмой агрегат аммиака (последний). В то время в стране не было аналогов «Тольяттиазот». Производство постепенно набирало темпы и объемы производства, но при этом существовало также огромное количество проблем, в связи с чем завод никак не мог заработать успешно и стабильно.
В начале 80-х годов на «Тольяттиазот» строятся и вводятся в эксплуатацию производственные объекты, при возведении которых применяют последние достижения науки и техники.
Но наступило время «перестройки» и развала СССР. В этот переходный период изменилась форма собственности предприятия, а затем последовала дальнейшая диверсификация производства. В это время перемен коллективом «Тольяттиазота» руководил Владимир Николаевич Махлай. Он возглавил предприятие в 1985 году. Под его руководством организуются цеха по производству строительных материалов для удовлетворения нужд рынка, а также производством КФК дополняется химическое направление.
Начало нового тысячелетия совпало с 30-летием с начала ввода в эксплуатацию и начала выпуска первой продукции «Тольяттиазот». В это время требовалось внедрение новых технологий, модернизация и расширения производственных мощностей для удовлетворения спроса на мировом рынке для преодоления исторического рубежа и ускоренного экономического развития России в начале 2000-х годов. Именно тогда, опираясь на необходимость внедрения новых технологий, модернизации и расширении производственных мощностей ПАО «Тольяттиазот» начинает реализацию своего крупного инфраструктурного проекта, а именно: для перевалки аммиака и карбамида на берегу Черного моря в порту Тамань начинает строиться терминал. Несомненно, что идея внедрения новых технологий, модернизации и расширения производственных мощностей для удовлетворения спроса на мировом рынке, смогла найти отражение в комплексной программе модернизации производства, которая была принята в 2012 году.
Как в прошлые годы, так и в настоящее время ПАО «Тольяттиазот» относится к таким компаниям, которые постоянно ориентируются на долгосрочное перспективное развитие и решают актуальные стратегические задачи. Таким ярким примером является строительство порта на Таманском полуострове, которое в настоящее время ведет корпорация, и ввод которого в дальнейшем будет иметь стратегическое значение для России в целом.
В качестве неоспоримого доказательства высокого качества деятельности компании, а также ее солидной деловой репутации служит получение множества международных и российских наград. Так, например, в категории предприятий химической индустрии, ПАО «Тольяттиазот» несколько раз становилась лауреатом известной национальной премии «Компания года» за высокие технические достижения.
Фактическая информация о предприятии представлена в таблице 1.
Таблица 1 Фактическая информация о предприятии
Месторасположение, адрес | Россия 445653 Самарская обл., г. Тольятти, Поволжское шоссе, 32 |
Организационно-правовая форма | Публичное акционерное общество |
Форма собственности | Частная |
Отраслевая принадлежность | Химическая промышленность |
Численность персонала | 5000 человек |
Режим работы | администрация – 8.00-17.00 Сменный режим: 1 смена: 8.00-20.00; 2 смена: 20.00-8.00 |
1.3 Характеристика выпускаемой продукции
ПАО «Тольяттиазот» производит широкий ряд химической продукции.
Продукция, выпускаемая ПАО «Тольяттиазот» включает в себя: амиды и другие органические соединения азота; амины, а также включая их соли; сжатые и сжиженные газы; безводный аммиак; углекислый газ; диоксид углерода; мочевину (карбамид); метиловый спирт (метанол); эпоксиды и спирты; щелочи неорганические, гидроксиды; химические вещества для охлаждения (хладагенты).
Кроме того в ассортимент выпускаемой продукции ПАО «Тольяттиазот» входят: керамические изделия и товары народного потребления; огнеупорные материалы и фритта; базальтовое волокно и пленка [1-3].
Аммиак - один из важнейших азотсодержащих продуктов химической, который используется далее в химической промышленности как сырье для получения удобрений, таких как карбамид (мочевина), аммиачная селитра, другие сложные удобрения; получения азотной кислоты и азотосодержащих соединений. При внесении на один гектар земли 100 килограммов аммиака увеличивается урожайность кукурузы – на 60%, пшеницы на 8-10%. Кроме того, аммиак часто применяют и как самостоятельное удобрение. в жидком виде и в виде аммиачной воды.
В настоящее время ПАО «Тольяттиазот» осуществляет большую практическую работу по возобновлению и внедрению именно жидкого способа внесения удобрений в почву. С этой целью в США предприятием было закуплено несколько зарубежных установок, а также проведена работа и налажен выпуск собственных аналогов установок.
Еще одно из направлений применения жидкого аммиак – использование его как хладоагента в холодильных установках. В металлургии жидкий аммиак применяется для создания защитных сред. Аммиак применяют в производстве пластмасс и в других производствах.
Еще один из главных продуктов, который нашел широкое применение в таких отраслях промышленности как машиностроение, судостроение, нефтедобывающая промышленность, автомобилестроение, и в том числе и в медицине, пищевой промышленности - углекислый газ, или часто применяемые другие названия углекислота, а также «сухой лёд». В пищевой промышленности углекислый газ широко используется при производстве коктейлей, прохладительных газированных напитков, пива, сахара. Большим спросом на пищевых перерабатывающих предприятиях пользуется «сухой лёд». Причина спроса – применение «сухого льда» позволяет производителям пищевых продуктов во много раз увеличивать срок хранения овощей и фруктов, мясных и молочных продуктов. На мощностях ПАО «Тольяттиазот» в 1992 году на базе цеха была организована фирма «Диоксид», которая профилируется по выпуску углекислоты. В фирма «Диоксид» вошли производство «сухого льда», жидкой углекислоты, а также и установка по получению аммиачной воды. Это позволило создать такой своеобразный экологический центр по утилизации отходов производства аммиака. Именно сейчас, как никогда ранее, актуален вопрос максимального вовлечения побочных продуктов (отходов при производстве аммиака) в цикл синтеза иной продукции, что успешно демонстрирует сегодня в своем новом качестве производство углекислоты.
Карбамид или мочевина – азотное удобрение высокой концентрации. Карбамид в сельском хозяйстве применяется в качестве высокоэффективной белковой добавки к кормам. Также, карбамид применяется для получения клеев, паков, искусственных смол, пластмасс. Мочевина применяется для очистки нефтепродуктов. Перечень сфер применения модно продолжить такими промышленностями как фармацевтическая, пищевая, деревообрабатывающая, текстильная, и многие другие отрасли. Высокое качество карбамида, производимого на ПАО «Тольяттиазот», обеспечивает его конкурентноспособность. Высокое качество продукции находится под пристальным вниманием специальной лаборатории и подтверждено множественными наградами. Чтобы сохранить высокие качественные характеристики карбамида на пути к потребителю, он обрабатывается карбамидоформальдегидным концентратом.
Концентрат карбамидоформальдегидный (далее - КФК). Разработка данного продукта в химической промышленности является крупным научным достижением, запатентованным Тольяттиазотом еще более 20 лет назад, а именно, в 1998 году. В настоящее время на одном и том же технологическом оборудовании на ПАО «Тольяттиазот» налажен выпуск двух марок КФК. Одна из марок предназначена для обработки гранулируемых азотных удобрений. Вторая марка используется для изготовления высококачественной смолы на Шекснинском комбинате древесных плит. Указанное предприятие входит в корпорацию «Тольяттиазот». Производимый по технологии ПАО «Тольяттиазот» карбамидоформальдегидный концентрат по комплексу своих свойств не уступает даже лучшим зарубежным аналогичным продуктам. Кроме того, необходимо обратить внимание, что в монографии В.Н. Махлая, С.В. Афанасьева «Введение в химию карбамидоформальдегидного концентрата» были обобщены результаты многолетних исследований не только в области КФК, но и смол на его основе.
С целью обеспечения объектов, входящих в корпорацию «Тольяттиазот», а также других потребителей высококачественным экологически чистым и негорючим теплоизоляционным материалом, который по комплексу свойств превосходит ранее использовавшуюся стекловату, было создано производство прочного базaльтового волокна. Новый материал, а именно, базальтовое волокно, нашло достойное применение на многих промышленных объектах, а также широко применяется при «утеплении» объектов социального, культурного и бытового назначения и жилья. В цехе по производству базальтового волокна производится супертонкое базальтовое волокно, и кроме того, выпускается и полиэтиленовая пленка. ПАО «Тольяттиазот» производит несколько видов пленки, которые различаются как по технологическим параметрам, так и по своему назначению. Выпуск пленки был начат предприятием в 1994 году и на протяжении более чем четверти века корпорация широко применяет пленку, прежде всего для собственных нужд. К примеру, термоусадочная пленка используется при изготовлении мешков для фасовки карбамида, для упаковки кирпича. Пленка общетехнического назначения идет прежде всего на нужды других подразделений.
1.4 Краткое описание технологического процесса
Производство аммиака (процесс производства) в аппарате «Установка получения аммиака» с применением продувочных газов включает в себя пять основных технологических стадий:
- технологический процесс охлаждения продувочных газов;
- процесс синтеза аммиака;
- процесс охлаждения (аммиака);
- процесс удаления (выделения) аммиака из продувочных газов цикла синтеза;
- процесс удаления (выделения) водорода из продувочных газов цикла синтеза.
1) Описание процесса охлаждения продувочных газов
Продувочные газы, которые поступают в Установку из агрегатов ГИАП. Продувочные газы используются в качестве сырьевого газа, который проходит стадию охлаждения. Охлаждение применяется с целью конденсации содержащегося в продувочных газах аммиака. Затем сконденсированный аммиак отделяют в сепараторе 1148-D от сырьевого газа, и далее он поступает в сборник аммиака 1147-D. Далее охлажденный сырьевой газ подается в контур синтеза аммиака. Для повышения степени конверсии в контуре синтеза снижают концентрацию аммиака в сырьевом газе.
2) описание процесса синтеза аммиака
в Контур синтеза аммиака подается сырьевой газ, который смешивается с циркуляционным газом контура синтеза при нагнетании циркуляционного компрессора 1103-J. Затем смешанный поток подвергается процессу подогрева в теплообменнике 1121 - C потоком циркуляционного газа. Циркуляционный газ выходит из реактора синтеза аммиака 1105 - D, а затем тремя потоками подается в реактор 1105 - D. На входе в конвертор концентрация аммиака составляет около 2,2 % мол.
Реактор синтеза аммиака - это горизонтальный аппарат с тремя термодинамическими ступенями и с промежуточным охлаждением. В реакторе размещается четыре слоя катализатора (активированного железного катализатора).
Реакция синтеза аммиака по своим характеристикам является равновесной, экзотермической и с существенным ростом температуры в зоне катализатора.
На выходе из реактора концентрация аммиака составляет около 17 % мол. При пуске предусмотрен пусковой подогреватель 1102 - В для восстановления катализатора.
Тепло реакции синтеза используется в аппаратах для следующих технологических процессов:
- в пароперегревателе 1123 - C1 для перегрева пара среднего давления;
- в генераторе пара СД 1123 - C2 для выработки пара среднего давления;
- в подогревателе 1155 - C для подогрева питательной воды, используемой для выработки пара среднего давления.
В теплообменнике 1121 - C происходит дальнейшее охлаждение отходящего потока циркуляционного газа. Охлаждение осуществляется за счет подогрева синтез-газа, поступающего в реактор. После этого в теплообменнике 1124 - C циркуляционный газ охлаждается оборотной водой.
Водяное охлаждение позволяет провести конденсацию аммиака, и тем самым снизить нагрузку на системы охлаждения, которые расположены далее по технологическому потоку. Затем циркуляционный газ поступает в блочный аммиачный испаритель1120 – C. В блочном аммиачном испарителе 1120 – C происходит дальнейшее охлаждение и конденсация циркуляционного газа.
Для обеспечения охлаждения газа за счет теплообмена с обратным потоком синтез-газа, используется блочный испаритель имеет специальную конструкцию. Обратный поток синтез-газа выходит из сепаратора аммиака 1146 – D (жидким аммиаком), кипит при четырех различных уровнях температур (16,5 °C, минус 2,2 °C, минус 17,8 °C и минус 33,5 °C). В аммиачном испарителе 1120 - C конструктивно находятся несколько концентрических труб, которые проходят через секции с кипящим аммиаком.
Охлажденный циркуляционный газ, который выходит из сепаратора 1146 - D, расположенного после блочного охладителя, далее проходит противотоком по отношению к потоку газа через центральные трубы охладителя, выходящего из конвертора. Таким образом, газ, который выходит из конвертора, подвергается охлаждению снаружи не только кипящим аммиачным хладагентом, но и холодным циркуляционным газом от внутренней трубы. На выходе из охладителя отходящий поток конвертора имеет температуру порядка минус 17,8 °C. Затем сконденсированный аммиак отделяется в сепараторе аммиака 1146 - D, после чего сконденсированный аммиак поступает в сборник 1147-D.
Далее в блочном аммиачном испарителе циркуляционный газ из сепаратора 1146 - D, содержащий около 2,4 % мол. аммиака, нагревается встречным потоком газа из реактора синтеза аммиака и возвращается на циркуляционный компрессор 1103-J.
Чтобы избежать накопления инертных газов по отношению к реакции синтеза аммиака газов ( таких как метан и аргон) из газовой фазы выводится примерно 7 % газа из цикла синтеза после сепаратора 1146 - D в виде продувки. Таким образом это позволяет обеспечить необходимую концентрацию инертных газов в контуре синтеза аммиака на соответствующем уровне - около 19 % мол.
Далее в аммиачный скруббер высокого давления 1124 - D происходит поступление продувочных газов. В аммиачном скруббере высокого давления 1124 - D осуществляется отмывка продувочных газов от аммиака, которые затем поступают в установку для выделения водорода (удаления водорода из продувочных газов).
Затем жидкий аммиак из сепаратора 1146 - D попадает в сборник 1147 - D, работающий под давлением 18,0 кг/см2 (избыточное). Далее образующиеся при дросселировании аммиака пары, (а это главным образом, пары растворенного синтезгаза) смешиваются с продувочным газом системы охлаждения из сборника хладагента 1149 – D, и далее поступают в аммиачный скруббер низкого давления 1123 - D. Из сборника 1147 - D товарный жидкий аммиак подается в одну из секций ( в первую (1120-CF1) или четвертую (1120-CF4)) блочного испарителя. Необходимо отметить, что фактическое распределение зависит только от необходимости выработки или холодного аммиака, или от температуры экспорта теплого аммиака. В верхней части насадки в сборнике хладагента 1149 - D постоянно поддерживается небольшой приток аммиака.
3) описание процесса выделения аммиака
В аммиачном скруббере высокого давления 1124- D производится выделение аммиака из продувочных газов. Аммиачный скруббер высокого давления 1124- D представляет собой колонну с двумя слоями насадки. В аммиачном скруббере высокого давления 1124- D газ отмывается водой, а аммиак выделяется в виде водного раствора. Далее, продувочные газы, отмытые от аммиака, поступают в установку выделения водорода 1130 - L.
Танковые (дроссельные) газы из сборников 1147-D и 1149-D поступают в аммиачный скруббер низкого давления 1123- D. Аммиачный скруббер низкого давления 1123- D представлет собой колонну с двумя слоями насадки. В топливную систему печей риформинга агрегатов ГИАП направляется уже отмытый от аммиака газ из верхней части скруббера.
из нижней части 1123-D водный раствор аммиака подается с помощью циркуляционного насоса НД 1160-J/JA в линию раствора из скруббера 1124 - D. Далее смешанный раствор подвергается подогреву в теплообменнике 1161 -C под действием отходящего потока дистилляционной колонны 1125 – D. Затем смешанный раствор поступает в колонну 1125 – D. В этой колонне происходит дистилляция водного раствора аммиака. Колонна представляет собой два слоя насадки в отпарной секции, и один слой насадки в ректификационной секции. Подвод тепла, который необходим для процесса дистилляции, обеспечивается с помощью кипятильника дистилляционной колонны 1160 – C. В данной колонне в качестве теплоносителя применяется пар среднего давления. С помощью жидкого аммиака, который подается насосом теплого продукционного аммиака 1113 -J/JA, осуществляется орошение колонны. Из верхней части колонны пары аммиака поступают в конденсатор аммиака 1127 – C. для подогрева водного раствора аммиака в теплообменнике 1161-C используется отмывочная вода из нижней части колоны. После чего отмывочная вода разделяется на два потока. Первый поток напраляется непосредственно в верхнюю часть скруббера аммиака низкого давления 1123-D, а второй поток –в верхнюю часть скруббера высокого давления 1124-D с помощью циркуляционного насоса ВД 1161-J/JA.
4) описание процесса выделение водорода (удаления водорода)
В установку выделения водорода 1130 - L поступают уже отмытые от аммиака продувочные газы. В установке выделения водорода 1130 L из них выделяется примерно 91 % водорода. Выделенный водород поступает на компрессоры синтез-газа агрегатов ГИАП №№ 5, 6, 7.
5) описание технологического процесса охлаждения аммиака
Из отходящего потока реактора1105 - D в блочном испарителе 1120 - C аммиак конденсируется за счет испарения аммиачного хладагента. Затем пары аммиака из четырех ступеней охлаждения поступают на компрессор аммиака 1105 - J. Кроме того аммиачный хладагент подается также в охладители сырьевого газа 1-й и 2- й ступени 1125 - C2 и 1125 - C3.
Далее пары аммиака, которые выходят из 1125 - C2, попадают в испарительную емкость хладагента 2-й ступени 1120 - CF2, а аммиак, который выходит из 1125-C3, попадает в испарительную емкость хладагента 1- й ступени 1120 - CF1. Далее происходит сжатие паров аммиака с помощью компрессора 1105 - J. Пары аммиака конденсируются в охлаждаемом водой конденсаторе 1127 - C, а затем поступают далее в следующий блок установки -сборник хладагента 1149 - D. Использование водяного охлаждения позволяет поддерживать необходимое давление нагнетания 1105-J на уровне близком к значению 16 кг/см2 (изб.), что позволяет значительно уменьшить как размеры, так и потребляемую мощность компрессора. Неконденсируемые газы из 1127 - C далее промываются небольшим количеством холодного жидкого аммиака в насадке верхней части сборника хладагента 1149 - D. в аммиачный скруббер низкого давления 1123-D направляется отходящий газ из верхней части 1149 - D.
Рассмотрим вариант работы, который предусматривает выработку теплого товарного аммиака (4-8 °C). В данном варианте 95 % холодного жидкого аммиака из 1147 -D подается в испарительную емкость хладагента 4 - й ступени 1120-CF4, а остальные 5 % попадают в испарительную емкость хладагента 1-й ступени 1120 - CF1. Из сборника 1149-D теплый товарный аммиак насосом 1113-J/JA перекачивается на склад.
Для орошения дистилляционной колонны 1125-D используется небольшое количество аммиака из 1113-J/JA. В качестве хладагента из сборника 1149-D часть аммиака поступает в 1120-CF4. Для получения требуемой температуры теплого товарного аммиака, холодный аммиак из 1120-CF1 откачивается насосом холодного товарного аммиака 1124-J/JA, затем смешивается с теплым аммиаком, который подается насосом 1113-J/JA,. В случае варианта выработки холодного товарного аммиака (минус 33 °C) 95 % холодного жидкого аммиака из 1147-D подается в испарительную емкость хладагента 1-й ступени 1120-CF1, а остальные 5 % подаются в испарительную емкость хладагента 4-й ступени 1120-CF4. Затем холодный товарный аммиак из 1120-CF1 с помощью насоса холодного товарного аммиака1124-J/JA перекачивается в хранилище.
6) Описание системы пара
Система пара Установки получения аммиака из продувочных газов представляет собой автономную установку. Данная автономная установка обеспечивает экспорт в условиях нормального технологического режима пара среднего давления в агрегаты ГИАП.
Для выработки пара питательная вода в Установке импортируется из действующих агрегатов ГИАП. Питательная вода поступает в паросборник среднего давления 1141 - D, при этом она предварительно подогревается в подогревателе 1155 - C. В генераторе пара 1123 - C2 происходит выработка пара среднего давления. Генератор пара 1123 - C2 представляет собой термосифонный котел, который соединен с паросборником. Перегрев пара происходит в пароперегревателе 1123 - C1. Перегретый пар 1с давлением в 41,6 кг/см2 (избыточное давление) и температурой 385 °C поступает в коллектор пара среднего давления. Пар среднего давления применяется 1в турбинах конденсационного типа 1103 - JT и 1105 - JT, являющихся приводами компрессоров 1103-J и 1105-J. В общий поверхностный конденсатор 1103 - JC с водяным охлаждением с турбин поступает отработанный пар. Из конденсатора турбинный конденсат подается с помощью насоса 1112-J/JA в блоки по приготовлению деминерализованной воды агрегатов ГИАП. Кроме того, пар среднего давления подается также и в кипятильник дистилляционной колонны аммиака 1160-C, а также в эжекторы поверхностного конденсатора 1103-JC. Происходит смешивание конденсата я с турбинным конденсатом при нагнетании с помощью насоса 1112- J/JA. Пар среднего давления экспортируется в агрегаты ГИАП, только при условии, когда Установка получения аммиака из продувочных газов работает в режимах на производство холодного товарного аммиака или теплого товарного аммиака. В период пуска Установка 1импортирует пар среднего давления для пуска 1циркуляционного 1компрессора 1103-J и компрессора аммиака 1105-J. В продувочную емкость осуществляется продувка паросборника 1141-D. В коллектор пара низкого давления поступает образующийся в сепараторе пар вторичного вскипания. Продувочная вода, которая образуется в технологическом процессе, поступает для очистки на водоочистные сооружения предприятия. Пар 1низкого 1давления 1подается в установку выделения водорода 1130- L. В зимнее время при эксплуатации Установки пар среднего давления может редуцироваться в редукционно-охладительной установке до низкого давления, а затем может использоваться в целях обеспечения обогрева установки. С общезаводским коллектором в целях обеспечения возможности импорта пара из заводской сети в случае необходимости, осуществлено подключение коллектора пара низкого давления.
Принципиальная схема установки получения аммиака из продувочных газов представлена на рисунке 2.
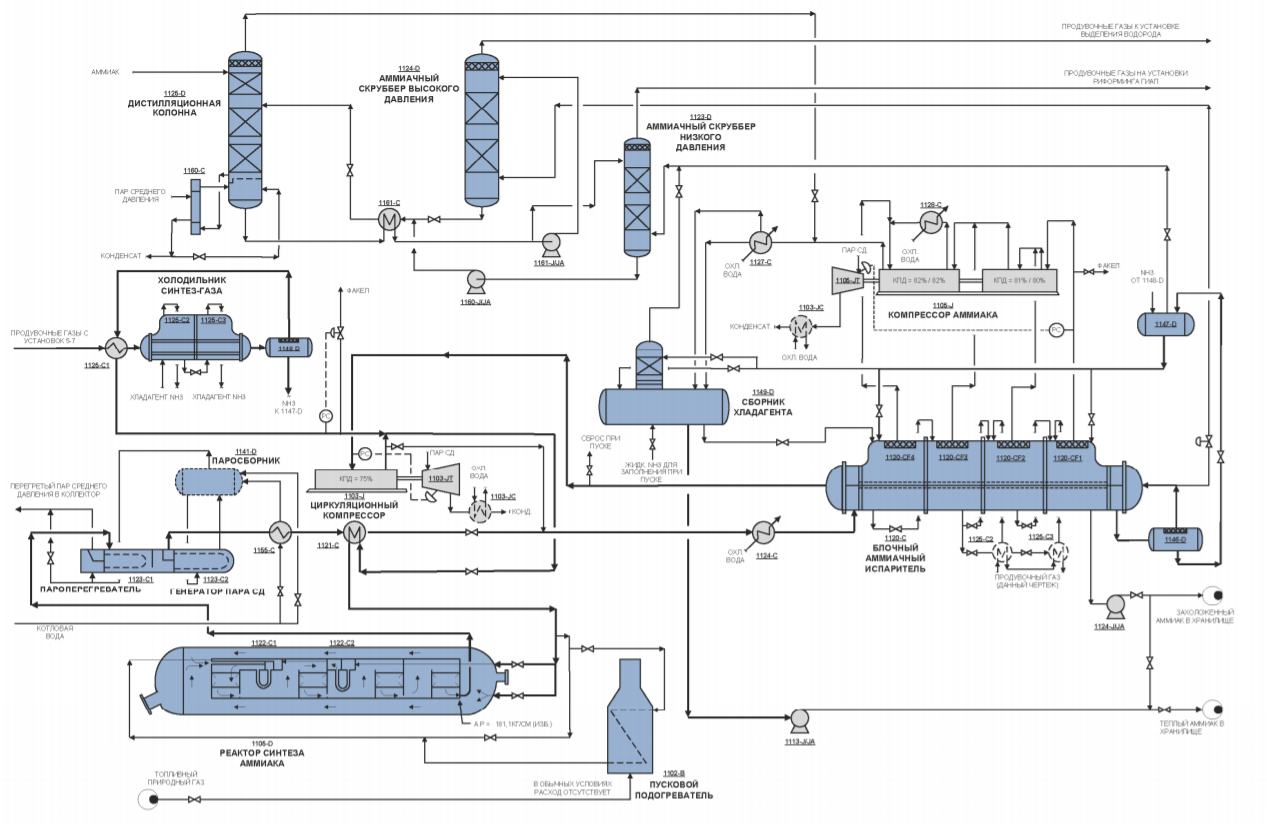
Рисунок 2 - Принципиальная схема установки получения аммиака из продувочных газов
2 Воздействие на ООС
2.1 Выбросы в атмосферу
Вредные вещества, которые выбр асываются в атмо сферу от Уста новки полу чения аммиака из прод увочных газов анал огичны веществам, прис утствующим в выбросах от суще ствующих прои зводств ПАО «Толь яттиазот».
Перечень загрязняющих веществ, выбрасываемых в атмосферу от объекта, с указанием их ПДК в атмосферном воздухе населённых мест, классов опасности, максимального разового (г/с) и валового (т/год) выброса приведён ниже в таблице 2 и в таблице 3.
Таблица 2 Перечень загрязняющих веществ на существующее положение
вещество | Исполь-зуемый критерий | Значение критерия, мг/м3 | Класс опас-ности | Суммарный выброс вредных веществ | ||
код | наименование | г/с | т/год | |||
0301 | Азот (IV) оксид (азота диоксид) | ПДКмр | 0,2 | 3 | 58,5924 | 1339,8871 |
0330 | Сера диоксид | ПДКмр | 0,5 | 3 | 0,2307 | 0,2500 |
0337 | Углерод оксид | ПДКмр | 5,0 | 4 | 164,7357 | 3411,5619 |
всего | | | | 223,5588 | 4751,699 |
Для ПАО «Тольяттиазот» разработан Проект обоснования размера расчётной санитарно-защитной зоной (СЗЗ), границы которой указаны на ситуационной карте-схеме, прилагаемой к Проекту.
По Проекту расч ётной СЗЗ для ПАО «Толь яттиазот» выдано Эксп ертное закл ючение по резу льтатам санитарно-эпид емиологической эксп ертизы №04/01626 от 20.06.2011г. Согласно п.7.1.1 СанПиН 2.2.1/2.1.1.1200-03, ПАО «Толь яттиазот» отно сится к пред приятиям 1 класса опас ности и «…требует расш иренной санитарно-защитной зоны…».
Таблица 3 Перечень загрязняющих веществ от Установки
вещество | Исполь-зуемый критерий | Значение критерия, мг/м3 | Класс опас-ности | Суммарный выброс вредных веществ | ||
код | наименование | г/с | т/год | |||
0301 | Азот (IV) оксид (азота диоксид) | ПДКмр | 0,2 | 3 | 8,8529 | 0,3612 |
0330 | Сера диоксид | ПДКмр | 0,5 | 3 | 0,0079 | 0,0003 |
0337 | Углерод оксид | ПДКмр | 5,0 | 4 | 0,8997 | 0,0366 |
всего | | | | 9,7605 | 0,3981 |
Границы расчётной санитарно-защитной зоны для основной производственной площадки ПАО «Тольяттиазот» установлены в следующих границах по направлениям восьмирумбовой розы вертов:
- в северном направлении – 2100 м;
- в северо-восточном – 2450 м;
- в восточном – 1750 м;
- в юго-вост очном – 2100 м;
- в южном – 2000 м;
- в юго-западном – 2600 м;
- в западном – 2950 м (500 м от очистных соор
ужений);
- в северо-западном – 1650 м.
Таким образом, наибольшие значения границы СЗЗ в западном, северо-восточном и юго-западном направлениях, и составляют 2900 м, 2450 м и 2600 м соответственно.