Файл: Основное и вспомогательное оборудование Описать принцип работы коксовых камер.docx
ВУЗ: Не указан
Категория: Не указан
Дисциплина: Не указана
Добавлен: 25.10.2023
Просмотров: 27
Скачиваний: 2
ВНИМАНИЕ! Если данный файл нарушает Ваши авторские права, то обязательно сообщите нам.
Содержание.
-
Основное и вспомогательное оборудование…………………………..…7 -
Описать принцип работы коксовых камер…………………………….....8 -
Проанализировать периодические и
непрерывные процессы коксования……………………………....………8
-
Опишите работу гидромолота……………………………………………10 -
Виды фланцевых соединений……………………………………………11 -
Охрана труда и техника безопасности на установке……….…………..13 -
Назначение и принцип действия приборов КИПиА …………………...15 -
Возможные неполадки оборудования, причины и способы их устранения………………………………………………………….……..18 -
Заключение……………………………………………………….……….22 -
Список используемых источников……………………………..……….22
Основное и вспомогательное оборудование
Оборудование современного нефтеперерабатывающего завода состоит из большого количества разнообразных аппаратов, машин, механизмов, контрольно-измерительных приборов и др.
При изучении аппаратов целесообразно придерживаться классификации основной и вспомогательной аппаратуры, приведенной ниже:
Нагревательные аппараты огневого действия. К ним относятся аппараты, нагреваемые открытым огнем. В современных установках аппараты этой группы почти не применяются. Они встречаются на старых технологических установках.
Трубчатые нагреватели (печи) различных технологических установок. Они отличаются по конструкции и теплопроизводительности.
Топки под давлением. К ним относятся генераторы инертного газа, топки для нагрева воздуха, топки специального назначения (для сжигания вредных сред и др.).
Теплообменные аппараты. В эту группу входят горизонтальные и вертикальные кожухотрубные теплообменники (или конденсаторы) различных конструкций: жесткого типа (Т-1), с компенсаторами на корпусе (ТЛ), с плавающей головкой (ТП), с У-образными трубками (ТУ); теплообменники высокого давления, для получения искусственного жидкого топлива; теплообменники типа «труба в трубе» ; рибойлеры-подогреватели с паровым пространством; кристаллизаторы типа «труба в трубе», кожухотрубные кристаллизаторы; конденсаторы воздушного охлаждения шатрового типа (горизонтальные и вертикальные) с принудительным потоком охлаждающего воздуха; секционные и змеевиковые погружные конденсаторы-холодильники.
Реакторы, регенераторы, контакторы. Представляют группу камера крекинг-установок, реакторов и регенераторов различных каталитических процессов со стационарным или движущимся катализатором (шариковым, порошковым, микросферическим и псевдоожиженным слоем): ступенчато-противоточные реакторы и регенераторы; реакторы и коксонагреватели установок пылевидного и контактного коксования; реакционные колонны установок Коксования — процесс переработки жидкого или твёрдого топлива нагреванием без доступа кислорода. При разложении топлива образуется твёрдый продукт — нефтяной или каменноугольный кокс и летучие продукты.
Основные фракционирующие аппараты. К ним относятся ректификационные колонны работающие под давлением, атмосферные и вакуумные колонны, колонны для разделения газов (бутана, пропана, этана). Вертикальные колонны и аппараты различного назначения: испарители, газогенераторы, абсорберы, десорберы, стабилизационные и экстракционные колонны, очистные башни.
Фильтры: фильтрпрессы, вакуум-фильтры, и др.
Вспомогательные аппараты — приемники для газов и жидкостей (вертикальные и горизонтальные), отстойники, мешалки, смесители, воздухоподогреватели. Емкости, работающие под давлением: шаровые емкости, горизонтальные и вертикальные емкости для сжиженных нефтяных газов и легкого бензина. Трубопроводы из углеродистых и легированных сталей для технологических процессов, нефтепереработки и нефтехимии.
Описать принцип работы коксовых камер
Коксование — процесс переработки жидкого или твёрдого топлива нагреванием без доступа кислорода. При разложении топлива образуется твёрдый продукт — нефтяной или каменноугольный кокс и летучие продукты.
Нагретое в печи сырье поступает в коксовые камеры, где происходит его крекинг с образованием кокса и продуктов крекинга. В результате протекания реакций крекинга, циклизации, ароматизации, дегидрирования, поликонденсации и уплотнения образуется сплошной слой кокса. Заполнение каждой коксовой камеры коксом до безопасного эксплуатационного уровня производится в течение 18 часов. Продукты крекинга выходят из верхней части коксовых камер в виде потока пара с приблизительной температурой 449 °C и давлением 1,05 кг/см2 (изб.). Рабочее давление в коксовой камере поддерживается как можно более низким для снижения количества образующегося кокса и увеличения выхода дистиллята. Горячий поток паров из коксовой камеры немедленно охлаждается до температуры 429 °C или менее при теплообмене с ТГК для прекращения реакций крекинга и полимеризации, вследствие чего коксообразование в линии паров с верха коксовой камеры к фракционирующей колонне установки коксования сводится к минимуму.
Проанализировать периодические и непрерывные процессы коксования
-
Периодическое коксование (в кубах)
-Простой и старый способ
-Применяется для получения электродного кокса (крупнокускового)
-Процесс не перспективен – малая производительность и небольшой срок службы коксовых кубов, большие энергозатраты на выгрузку кокса
Периодическое коксование нефтяных остатков в кубах является наиболее простым и старым способом. Его применяют для получения электродного кокса — крупнокускового. Однако процесс не перспективен из-за малой производительности и небольшого срока службы кубов, большой затраты труда на выгрузку кокса и т. д.
-
Непрерывное коксование (в «кипящем» слое)
-Целевое назначение – газ, жидкие продукты
-Частицы кокса – 0,1-0,5 мм
-Кокс получается порошкообразный
Непрерывные процессы коксования используются для получения максимального количества дистиллятов. Для их осуществления необходимо аппаратурное оформление, которое позволило бы непрерывно выводить образующийся кокс из реактора. Идея непрерывного вывода кокса привела к разработке реактора с псевдоожиженным слоем кокса, выводимого в виде порошка. Толчком к строительству установок «флюид» послужили общая тенденция к углублению переработки нефти, более высокий выход жидких продуктов по сравнению с другими формами термической переработки нефтяных остатков, возможность переработки наиболее тяжелых гудронов и природных битумов, включая высокосернистые, а также возможность очистки от серы всех получаемых продуктов.
Процесс коксования «флюид» идет более интенсивно, так как большая поверхность порошкообразного теплоносителя способствует улучшению контакта фаз. Хорошая летучесть такого теплоносителя дает возможность перемещения больших его масс по стоякам и создания установок большой мощности.
Основные особенности коксования «флюид»:
- более высокий выход жидких продуктов и меньший выход кокса по сравнению с замедленным коксованием;
- гибкость в отношении качества сырья;
- относительная легкость эксплуатации и большая продолжительность межремонтных пробегов;
- возможность сочетания процесса с установками АТ, каталитического крекинга, производства энергии;
- отсутствие печи для нагрева сырья;
- экономия, достигаемая вследствие большой мощности установок.
Опишите работу гидромолота.
Основным элементом молота является его боёк, т.е. определенная масса m, которую нужно переместить на некоторое расстояние от инструмента и разогнать до заданной скорости V в сторону инструмента. Энергия удара или же кинетическая энергия бойка равна mv2/2. Для того чтобы разогнать боёк до нужной скорости к нему нужно приложить соответственную силу, величина которой определяется давлением рабочей жидкости и площадью, на которую действует это давление, а также давление газа в пневмокамере и соответствующей площадью торца бойка, на которую действует давление газа.
Чем короче ход бойка, тем больше должна быть сила, которая его разгоняет. Однако такая же реактивная сила действует в противоположную сторону, т.е. передаётся на базовую машину. Поэтому сила, разгоняющая боёк ограничена возможностью базовой машины её воспринимать на максимальном вылете рабочего оборудования.
В конце рабочего хода непосредственно перед ударом поршень своей проточкой соединяет камеру управления золотником со сливной линией, обеспечивая переключение золотника в позицию взвода бойка. Золотник гидрораспределителя гидромолота выполнен с рабочими поясками разных диаметров, таким образом, что со стороны одного из его торцев постоянно действует давление рабочей жидкости, а на противоположный торец на него действует давление только на фазе торможения и во время рабочего хода бойка.
1
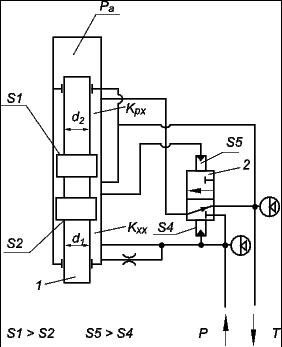
– боёк; 2 – распределитель; Kxx – камера холостого хода; Kpx – камера рабочего хода; Pa – пневмокамера; А – сетевой гидроаккумулятор напорной линии; У – линия управления золотником гидрораспределителя; S1 и S2 – площади камер рабочего цилиндра; S4 и S5 – площади камер управления золотником
Виды фланцевых соединений
Фланец представляет собой диск круглой или квадратной формы со сквозным отверстием в центре, который используют повсеместно для соединения трубных участков, патрубков, шаровых кранов, аппаратов, машинных элементов и прочего трубопроводного оборудования.
Особенность фланцевого соединения заключается в возможности его многократного использования. Герметичность стыка в процессе эксплуатации достигается за счет периодической подтяжки крепления, а также своевременной замены прокладки, которая исключает течь продукта транспортировки, снижает трение/износ стальных деталей.
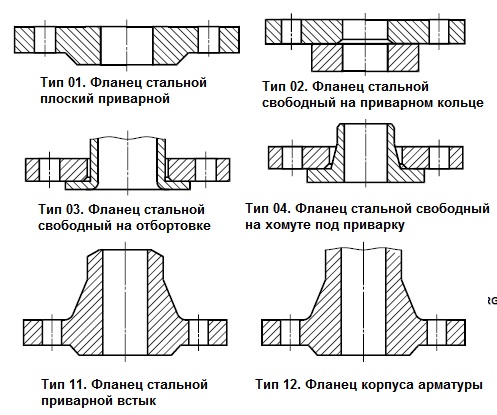
Фланец тип 01
Стальная плоская приварная соединительная деталь выдерживает нагрузки до 2,5 Мпа. Ее изготавливают номинальным диаметром от 10 до 2400 мм. Эксплуатация возможна при температуре не ниже -40 °C.
Фланец тип 02
Свободный плоский соединитель на приварном кольце позволяет без проворота трубы легко производить стыковку арматуры или оборудования. Используют при укладке трубопроводов в труднодоступных местах, на трубных участках, где часто проводят ремонтные работы. Изготавливают методом ковки, штамповки или вырезают из листа.
Особенность элемента заключается в отсутствии контакта с рабочей средой. При монтаже на трубу сначала надевают фланец, затем кольцо. Далее кольцо приваривают к трубопроводу, после чего с ответной деталью образуют фланцевое соединение.
Фланцы тип 03 и 04
Детали стальные плоские свободные на отбортовке (тип 3) и на хомуте (тип 4) под приварку. Установку изделия производят аналогичным способом ‒ сначала надевают соединитель, далее отбортовку/хомут.
Тип 03 используют только на давление PN2,5, PN6, PN10, PN16.
Тип 04 применяют только при нагрузках PN10, PN16, PN25.
Оба вида выпускают диаметром от 10 до 600 мм.
В целях экономии производители иногда предлагают своим клиентам изготовление соединителя из алюминия, а отбортовки из нержавеющей или углеродистой стали. Поскольку алюминиевый диск не контактирует с транспортируемым продуктом, на материале можно сэкономить.
Фланец тип 11
Обладает характерным выступом ‒ «воротником», благодаря которому получил свое название «воротниковый фланец» иначе его называют «приварным встык».
За счет выпуклости, минимизирующей нагрузки у основания детали, его устанавливают в трубопроводных коммуникациях с давлением 01‒25 МПа. Условный проход (Ду) трубодетали ‒ от 10 до 4000 мм.
Фланец тип 12
Является частью/корпусом арматуры. Его изготавливают литьем из стали, серого или ковкого чугуна. Сфера применения и размер зависят от материала изготовления:
Сталь используют при Ру от 2,5 до 250 кгс/см2, сечение ‒ от 10 до 2000 мм;
Серый чугун ‒ от 1 до 16 кгс/см2, диаметр ‒ от 10 до 4000 мм;
Ковкий чугун ‒ от 6 до 40 кгс/см2, условный проход ‒ от 10 до 300 мм.
Охрана труда и техника безопасности на установке
Охрана труда и техника безопасности на предприятии – это, прежде всего, зона ответственности работодателя и соответствующих служб организации.
Работодатель обязан разработать внутреннюю нормативную документацию, проводить инструктажи и проверки знаний в соответствии с требованиями законодательства, информировать работников обо всех обстоятельствах, от которых зависит безопасность на производстве.
Также работодатель обязан создать для работников безопасные условия труда. Для этой цели предусматривается комплекс требований:
-
Использование оборудования и конструкций, соответствующих требованиям стандартов и другой нормативной документации; -
Соблюдение сроков периодических ремонтов и обслуживания оборудования; -
Соблюдение требований пожарной и электробезопасности при оснащении производственных и офисных помещений; -
Установка необходимых защитных приспособлений и конструкций; -
Обеспечение достаточной освещенности, вентиляции, поддержание оптимального температурного режима на рабочих местах; -
Своевременное устранение пыли и отходов производства; -
Обеспечение работников спецодеждой и спецобувью, а также другими средствами индивидуальной защиты в соответствии со спецификой производства; -
Обеспечение работников актуальными инструкциями по ТБ, наглядными материалами; -
Создание на рабочих местах и в производственных помещениях всех необходимых систем сигнализации, размещение знаков безопасности и т.д.