ВУЗ: Не указан
Категория: Не указан
Дисциплина: Не указана
Добавлен: 25.10.2023
Просмотров: 83
Скачиваний: 3
ВНИМАНИЕ! Если данный файл нарушает Ваши авторские права, то обязательно сообщите нам.
2 слайд
Изопре́н (2-метилбута-1,3-диен) — ненасыщенный углеводород, принадлежащий к диеновому ряду, представляющий собой бесцветную летучую жидкость с характерным запахом.
На сегодняшний день известно 6 способов получения изопрена, в промышленном масштабе освоено 4 метода получения изопрена, 2 метода не нашли применения в промышленности :
-
дегидрированием изопентана; -
извлечение изопрена из фракции С5 пиролиза нефтепродуктов; -
жидкофазным окислением углеводородов; -
из изобутена и формальдегида.
Данные методы не нашли применения в промышленности
-
Димеризацией пропилена -достоинством этот метода является
использование в качестве сырья доступный и дешевый пропилен. Но так же имеется существенный недостаток- много стадийность, низкая селективность, сложные условия пиролиза и необходимость очистки изопрена.
-
Из ацетона и ацетилена- достоинствами процесса являются высокие
выходы продуктов на всех стадиях, небольшое количество побочных продуктов и высокая чистота получаемого изопрена. Основные недостатки – это технологические трудности, связанные с применением ацетилена
И водорода под давлением, в частности взрывоопасность. В связи с этим наблюдается тенденция к замене ацетилена нефтехимическим сырьем, как в большинстве классических процессов.
3 слайд
1. Получение изопрена каталитическим дегидрированием изопентана
Каталитическое дегидрирование – наиболее простой метод получения диенов С5, поскольку молекула изопентана обладает готовым углеродным скелетом изопрена, и весь механизм сводится к отщеплению двух молекул водорода. Процесс дегидрирования алканов С5 требует жесткого режима и имеет ряд ограничений по термодинамическим параметрам, благодаря чему при обычных условиях получить продукт с технически допустимым выходом в одну стадию практически невозможно. Поэтому выход диена может быть увеличен только с помощью таких приемов, как: сопряженное или окислительное дегидрирование
, применение вакуума. Другим принципиальным недостатком метода дегидрирования во всех его вариациях является сложность выделения целевого диена. Поскольку фракция, полученная при дегидрировании, представляет собой сложную смесь низкокипящих углеводородов, имеющих одинаковое число атомов углерода и близкие температуры кипения, то выделение чистого продукта является сложным процессом Метод дегидрирования, несмотря на его недостатки, остается ведущим способом синтеза мономеров, особенно в современных вариациях (окислительное дегидрирование).

4 слайд
2.Извлечение изопрена из фракции С5 пиролиза нефтепродуктов
Выделение изопрена из продуктов пиролиза представляет определенную трудность. Главным способом промышленного разделения смеси компонентов с разными температурами кипения является ректификация. Основными компонентами фракции С5 пиролиза, помимо изопрена, являются н-пентан, изопентан, циклопентадиен-1,3, пентадиен-1,3. Близость температур кипения компонентов данной фракции не позволяет экономически выгодно выделить изопрен методами традиционной ректификации из-за необходимости больших размеров колонн и высоких затрат энергии для проведения данных процессов.
Альтернативным методом разделения является экстрактивная ректификация, основанная на изменении относительной летучести компонентов при добавлении разделяющего агента. В качестве разделяющего агента использовался диметилформамид (ДМФА)
Колонны К-1 служат для отделения бутан-бутеновой фракции. В колонне К-2 отделяются тяжелые углеводороды. Колонны К-3 и К-4 – колонны экстрактивнойректификации, в которыхсовместно с ДМФА отделяется изопрен. В колонне К-5 происходит разделение изопрена и ДФМА, причем все присутствующие примеси других углеводородов выделяются вместе с изопреном. Поэтому отсутствует необходимость регенерации ДМФА.
5 слайд
3. Получение изопрена жидкофазным окислением углеводородов
Получение изопрена жидкофазным окислением изопентана основано на реакции эпоксидирования его органическими гидропероксидами. Процесс разработан в начале 1960-х годов американской фирмой «Халкон»
П

1)Окисление изопентана кислородом воздуха до трет-пентилгидропероксида:
2)Взаимодействие гидропероксида с 2-метилбутеном-2, который является промежуточным продуктом синтеза, с образованием оксида 2-метилбутена-2:
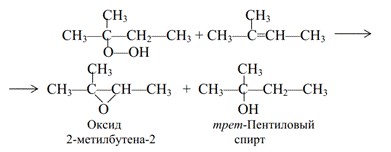
6 слайд
3)Изомеризация оксида 2-метилбутена-2 в ненасыщенный спирт 2-метилбутен-1-ол-3:

4)Дегидратация спирта в изопрен:

7 слайд
4. Получение изопрена из изобутилена и формальдегида
Советский промышленный способ получения изопрена из изобутилена и формальдегида был разработан М. С. Немцовым, М. И. Фарберовым, Я. И. Рогштейном.
Самым распространенным промышленным способом производства изопрена на сегодняшний день является его двухстадийный синтез из изо-бутилена и формальдегида через промежуточное получение 4,4-диметил-1,3- диоксана (ДМД). Синтез осуществляется в две стадии.
1)На первой в присутствии кислотного катализатора производится конденсация изобутилена с формальдегидом в 4,4-диметилдиоксан-1,3.
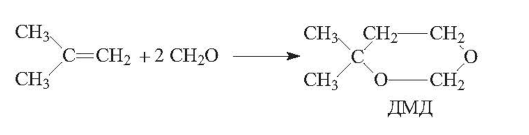
2
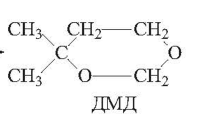

Вторая стадия получения изопрена осуществляется термокаталитическим разложением диметилдиоксана (ДМД). На практике используется компактный катализатор (без носителя), представляющий собой смесь средних и кислых фосфатов кальция. Наиболее эффективными катализаторами разложения ДМД являются кальций фосфатный
Главным достоинством рассматриваемого метода синтеза изопрена является низкое содержание примесей, даже в сыром, неочищенном продукте. Несмотря на многие достоинства двухстадийного способа получения изопрена из изобутилена и формальдегида (дешевизна сырья, относительно простая очистка изопрена, возможность применения побочных продуктов), данный метод всё же имеет ряд недостатков. Основные из них это высокий расход сырья (прежде всего формальдегида), высокая энергоемкость процесса, а также образование малоценных побочных продуктов, возникающих, как при взаимодействии, так и при пиролизе .