Файл: При сборке и монтаже производственного оборудования часто.docx
ВУЗ: Не указан
Категория: Не указан
Дисциплина: Не указана
Добавлен: 25.10.2023
Просмотров: 32
Скачиваний: 2
ВНИМАНИЕ! Если данный файл нарушает Ваши авторские права, то обязательно сообщите нам.
При сборке и монтаже производственного оборудования часто приходится поднимать и перемещать значительные тяжести. В соответствии с правилами безопасности труда подросткам моложе 16 лет запрещены подъем и перенос тяжестей. Исходя из физиологических особенностей организма подросткового возраста раз решается поднимать и переносить детали и сборочные единицы массой не более 16 кг.
Основой, обеспечивающей безопасное выполнение сборочных работ, является четкая организация труда и рабочего места слесаря механосборочных работ.
В наибольшей степени безопасность труда определяется состоянием рабочих инструментов. Инструменты непременно должны находиться в исправном состоянии и периодически проходить испытания на безопасность их применения в целях предупреждения травматизма.
Все мероприятия, связанные с безопасностью выполнения ра бот, проводятся в три этапа:
-
подготовка к работе; -
ведение работ; -
завершающие действия работника по окончании смены.
Передначаломработыследует придерживаться следующих
правил:
-
надев рабочую одежду, необходимо проверить, нет ли на ней свисающих концов: рукава должны быть либо застегнуты, либо закатаны выше локтя;-
удалить с рабочего места посторонние предметы, при необходимости включить местное освещение; разложить рабочие и из- мерительные инструменты, приспособления и материалы так, чтобы ими было удобно пользоваться; -
убедиться в исправности рабочих инструментов и приспособлений; проверить состояние электрического и пневматического инструмента и срок его переосвидетельствования.
-
Вовремяработы
необходимо:
-
пользоваться только исправными инструментами и приспособлениями, которые указаны в технологической документации на сборку; -
не останавливать вращающийся инструмент руками или какими-либо посторонними предметами; -
при выполнении прессовых операций все перемещения детали осуществлять только при неподвижном штоке пресса; -
укладывать детали в тару или на стеллажи; при укладывании деталей в штабель помнить, что его высота не должна превышать 1 м; -
при запрессовке следить за тем, чтобы детали были установлены без перекоса; -
удерживать гидравлические скобы только за рукоятки; -
при работе с растворителями применять резиновые перчатки и соблюдать правила пожарной безопасности; -
при работе с абразивными инструментами строго соблюдать действующие инструкции; -
помнить, что работы с пневматическим инструментом должны выполняться только лицами старше 18 лет.
Поокончаниисменыследует:
-
отключить все механизмы и убрать рабочий инструмент; -
очистить рабочее место от продуктов обработки и в случае необходимости произвести смазывание оборудования; -
слить использованные растворители в специальную тару для утилизации; -
убрать использованный обтирочный материал в специальный металлический ящик.
2. Механосборочные работы. Инструменты. Оборудование
Процесс обработки деталей резанием основан на образовании новых поверхностей путем деформирования и последующего отделения поверхностных слоев материала с образованием стружки. Та часть металла, которая снимается при обработке, называется припуском. Или, говоря иначе, припуск — это избыточный (сверх чертежного размера) слой заготовки, оставляемый для снятия режущим инструментом при операциях обработки резанием.
После снятия припуска на металлорежущих станках обрабатываемая деталь приобретает форму и размеры, соответствующие рабочему чертежу детали. Для уменьшения трудоемкости и себестоимости изготовления детали, а также ради экономии металла, размер припуска должен быть минимальным, но в то же время достаточным для получения хорошего качества детали и с необходимой шероховатостью поверхности.В современном машиностроении имеется тенденция снижать объем обработки металлов резанием за счет повышения точности исходных заготовок. Основные методы обработки металлов резанием. В зависимости от характера выполняемых работ и вида режущего инструмента различают следующие методы обработки металлов резанием: точение, фрезерование, сверление, зенкерование, долбление, протягивание, развертывание и др.
Точение — операция обработки тел вращения, винтовых и спиральных поверхностей резанием при помощи резцов на станках токарной группы. При точении заготовке сообщается вращательное движение (главное движение), а режущему инструменту— медленное поступательное перемещение в продольном или поперечном направлении (движение подачи).Фрезерование — высокопроизводительный и распространенный процесс обработки материалов резанием, выполняемое на фрезерных станках. Главное движение получает фреза, а движение подачи в продольном направлении — заготовка Сверление — операция обработки материала резанием для получения отверстия. Режущим инструментом служит сверло, совершающее вращательное движение резания и осевое перемещение подачи. Сверление производится на сверлильных станках Строгание — способ обработки резанием плоскостей или линейчатых поверхностей. Главное движение (прямолинейное возвратно-поступательное) совершает изогнутый строгальный резец, а движение подачи (прямолинейное, перпендикулярное главному движению, прерывистое) — заготовка. Строгание производится на строгательных станках. Долбление — способ обработки резцом плоскостей или фасонных поверхностей. Главное движение совершает резец, а движение подачи - заготовка. Долбление производят на долбежных станках. Шлифование — процесс чистовой и отделочной обработки деталей машин и инструментов посредством снятия с их поверхности тонкого слоя металла шлифовальными кругами, на поверхности которого расположены абразивные зерна.
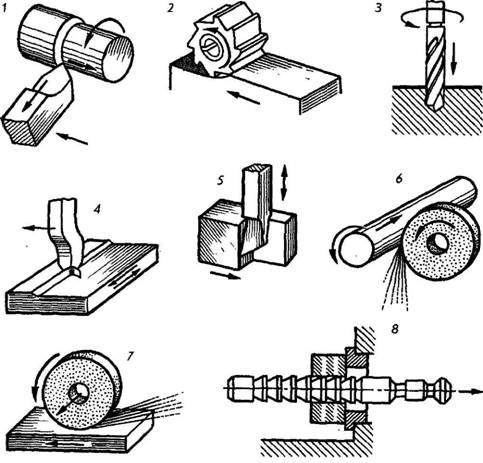
Рис 29- Процессы обработки деталей
Протягивание — процесс, производительность при котором в несколько раз больше, чем при строгании и даже фрезеровании. Главное движение прямолинейное и реже вращательное (рис 29).
Механическая обработка металлов применяется во многих отраслях промышленного производства. С течением времени этот процесс совершенствуется, появляются современные машины, оборудование и инструмент по механической обработке металла.
Применяемое оборудование и инструмент:
Одним из них является фреза, которая представляет собой зубчатое колесо, каждый зубчик которого является резцом. При вращении этого зубчатого колеса отрезаются кусочки металла, передвигающегося под ним. Сам процесс называется фрезерование. Для того, чтобы просверливать в металле отверстия применяются сверлильные станки: вертикально-сверлильные (применяются в сборочных и слесарных цехах) и расточные. Существует три вида таких станков: настольные, настенные и на колонне. Если последовательно перемещать на сверлильном станке (многошпиндельном) деталь, можно произвести целый ряд операций механической обработки - сверление, развертывание, зенкерование и пр. Шлифовальный станок предназначен для шлифовки поверхностей деталей.
Металлоре́жущий стано́к — станок, предназначенный для размерной обработки металлических заготовок путем снятия материала механическим способом.
Станки классифицируются по множеству признаков.
-
По классу точности металлорежущие станки классифицируются на пять классов:-
(Н) Нормальной точности -
(П) Повышенной точности -
(В) Высокой точности -
(А) Особо высокой точности -
(С) Особо точные станки (мастер-станки)
-
-
Классификация металлорежущих станков по массе:-
лёгкие (< 1 т) -
средние (1-10 т) -
тяжёлые (>10 т) -
уникальные (>100 т)
-
-
Классификация металлорежущих станков по степени автоматизации:-
ручные -
полуавтоматы -
автоматы -
станки с ЧПУ -
гибкие производственные системы
-
-
Классификация металлорежущих станков по степени специализации:-
универсальные. -
специализированные. -
Специальные
-
3. Разборка и сборка разъемных соединений
Разъемные соединения
Способы соединения деталей и сборочных единиц механизмов различны. Их можно разделить на неразъемные и разъемные. Разъемные соединения отличаются тем, что их разборка возможна без разрушения деталей, входящих в соединение. Разъемные соединения в свою очередь делятся на подвижные и неподвижные. С помощью подвижных соединений можно обеспечить определенное перемещение одних деталей относительно других. К ним относятся различные опоры и направляющие. Неподвижные соединения обеспечивают фиксированное положение одних деталей по отношению к другим. Разъемные соединения допускают многократную сборку и разборку. К ним относят резьбовые, штифтовые, шпоночные, шлицевые соединения. Выбор типа соединения зависит от предъявляемых к нему требований: конструктивных, технологических и экономических.Резьбовые соединения
Резьбовыми называют соединения составных частей изделия с применением деталей, имеющих резьбу. Они наиболее распространены в приборо- и машиностроении. Резьбовые соединения бывают двух типов:
-
соединения с помощью специальных резьбовых крепежных деталей (болтов, винтов, шпилек, гаек); -
соединения свинчиванием соединяемых деталей, т.е. резьбы, нанесенной непосредственно на соединяемые детали.
Достоинствами резьбовых соединений являются простота, удобство сборки и разборки, широкая номенклатура, стандартизация и массовый характер производства крепежных резьбовых деталей, взаимозаменяемость, относительно невысокая стоимость и высокая надежность.
Недостатками резьбовых соединений являются наличие концентраций напряжений во впадинах резьбы, что снижает прочность соединений; чувствительность к вибрационным и ударным воздействиям, которые могут привести к самоотвинчиванию и низкая точность взаимоположения соединяемых деталей.
Основным элементом соединения является резьба, т.е. поверхность, которая образуется при винтовом движении плоской фигуры по цилиндрической или конической поверхности. Соответственно различают цилиндрическую и коническую резьбы. По профилю выступа и канавки резьбы в плоскости осевого сечения резьбы делятся на треугольные, трапецеидальные симметричные, трапецеидальные несимметричные или упорные, прямоугольные и круглые. Также резьбы бывают внутренние и внешние.