Файл: Содержание Введение 2 Актуальность специалистов по слесарному делу. 3 Координатнорасточный станок 2А450. 4.docx
Добавлен: 26.10.2023
Просмотров: 161
Скачиваний: 3
ВНИМАНИЕ! Если данный файл нарушает Ваши авторские права, то обязательно сообщите нам.
СОДЕРЖАНИЕ
Актуальность специалистов по слесарному делу.
1.Координатно-расточный станок 2А450.
1.1. Назначение и область применения
1.2. Принцип работы и особенности конструкций станка.
1.3. Расположение органов управления координатно-расточным станком.
1.4. Конструкция и характеристика работы основных узлов станка 2А450.
2. Шпиндельная бабка координатно-расточного станка.
2.2. Ремонт шпиндельной бабки.
конструктивный узел, отделив его от коробки скоростей. Этим значительно уменьшается передача на шпиндель вибраций и динамических нагрузок, возникающих в приводе.
В шпиндельную бабку входит ряд сборочных единиц, в том числе корпус, планшайба, расточный шпиндель, хвостовая часть и ползун расточного шпинделя, технология ремонта которых приводится ниже. Рассмотрим вначале ремонт базовой детали данной сложной сборочной единицы, т. е. самого корпуса (рис. 7.3) шпиндельной бабки. Для выбора метода ремонта корпуса его следует установить на направляющие уже отремонтированной передней стойки и определить величину смещения оси гайки шпиндельной бабки относительно оси отверстия кронштейна винта передней стойки. При этом необходимо учесть толщину слоя, который надо снять для выравнивания поверхностей 2, 3 и 4 направляющих шпиндельной бабки. При ремонте направляющих корпуса шпиндельной бабки восстанавливают параллельность поверхностей 3 и 4 к оси шпинделя, а поверхности 7 и 8 располагают перпендикулярно оси шпинделя. Ремонт указанных поверхностей осуществляют путем механической обработки и шабрением.
Ремонт направляющих корпуса шпиндельной бабки шабрением. Направляющие корпуса шпиндельной бабки расточного станка ремонтируют шабрением в следующем порядке.
рис.3. Корпус бабки
Ремонт расточного шпинделя. До выбора метода ремонта шпинделя необходимо промерить индикаторным микрометром размеры диаметра по всей длине. Круглость и цилиндричность всей наружной поверхности можно также проверить пассиметром. Затем шпиндель устанавливают на призмах и проверяют изогнутость его путем вращения (биение наружной поверхности — по индикатору и биение конического отверстия — по контрольной оправке). Допускаемые отклонения: круглость наружной поверхности 15 мкм, цилиндричность 5 мкм на длине 1000 мм. Изогнутость шпинделя 0,02 мм на длине 1000 мм. Радиальное биение оправки, вставленной в конусное отверстие, 0,01 мм — у торца шпинделя и 0,02 мм — на длине 300 мм. При повышенных отклонениях производят шлифование наружной поверхности и конусного отверстия. Параметр шероховатости Ra = 0,160,08 мкм. Конусное отверстие с большим износом восстанавливают постановкой ремонтной втулки.
Опорные втулки расточного шпинделя, как правило, изготовляют заново. Их запрессовывают в полый шпиндель и затем растачивают на токарном станке, снимая припуск по внутреннему диаметру. Далее индикаторным нутромером определяют диаметры опорных втулок, а также точность посадки шпинделя со втулками. Допускаемые отклонения — круглость отверстий втулок и разность диаметров отверстий — 0,01 мм. Должно быть плавное перемещение шпинделя внутри полого шпинделя при диаметральном зазоре между ними в пределах 0,01—0,02 мм.
Ремонт хвостовой части. При ремонте хвостовой части (восстанавливают прямолинейность поверхностей 2, 3, 5 и 6, взаимную параллельность поверхностей 3, 5, и перпендикулярность их к поверхности 1. Поверхности 2 и 6 должны находиться в одной плоскости и быть перпендикулярны к поверхности 1. Восстановление поверхностей осуществляют шабрением или механической обработкой на станках (в зависимости от величины износа).
Ремонт ползуна расточного шпинделя. Вследствие износа поверхностей 1—6 ось отверстия отклоняется от оси шпинделя и нарушается центровка винта с осью гайки перемещения ползуна. Поверхности ползуна оказываются непараллельными оси шпинделя.
рис.4. Хвостовая часть и ползун шпинделя
рис.5. Технологический процеес ремонта 1
Координатно-расточные станки, среди прочего металлорежущего оборудования, занимают привилегированное положение, поскольку им доверяется обработка самых серьезных и точных деталей. Наличие специального отсчетного механизма, позволяет заготовке перемещаться относительно рабочего органа с отклонением до 0,001 мм, что гарантирует выполнение работ с минимальными погрешностями. С помощью координатно-расточных станков выполняют обработку отверстий с предельно точным расстоянием их расположения, не применяя дополнительных устройств, направляющих инструмент. Список операций, на которые рассчитано подобное оборудование, включает, сверление, растачивание, фрезерование, зенкерование, развертывание отверстий, разметку заготовок, контрольно-измерительные работы, чистовую обработку торцов изделий. Исходя из того, что такие станки решают чрезвычайно ответственную задачу, фактически, не допуская ни
малейших отклонений от координатных размеров, к их исправности предъявляются повышенные требования. Таким образом, ремонт координатно-расточных станков совсем необязательно связан с возвратом работоспособности. Чаще всего, на реставрацию поступают станки, нуждающиеся в восстановлении первоначальных технических характеристик.
Процесс капитального ремонта станка:
В ходе прохождения производственной практики был собран материал, необходимый для написания отчета. Данная производственная практика является хорошим практическим опытом для дальнейшей самостоятельной деятельности. За время пройденной практики я познакомилась с новыми интересными фактами. Процесс прохождения производственной практики научил меня терпению и трудолюбию. Я узнала много новой и полезной информации, которая пригодится мне в дальнейшей учебе и трудоустройстве. Задания, выполняемые на практике, напрямую связанны с нашей специальностью, что значительно повысило мои знания по своей профессии. Также я извлекла для себя полезные уроки из различных рабочих ситуаций. производственная практика весьма необходима студентам для закрепления теоретических знаний, полученных в колледже.
2.2. Ремонт шпиндельной бабки.
В шпиндельную бабку входит ряд сборочных единиц, в том числе корпус, планшайба, расточный шпиндель, хвостовая часть и ползун расточного шпинделя, технология ремонта которых приводится ниже. Рассмотрим вначале ремонт базовой детали данной сложной сборочной единицы, т. е. самого корпуса (рис. 7.3) шпиндельной бабки. Для выбора метода ремонта корпуса его следует установить на направляющие уже отремонтированной передней стойки и определить величину смещения оси гайки шпиндельной бабки относительно оси отверстия кронштейна винта передней стойки. При этом необходимо учесть толщину слоя, который надо снять для выравнивания поверхностей 2, 3 и 4 направляющих шпиндельной бабки. При ремонте направляющих корпуса шпиндельной бабки восстанавливают параллельность поверхностей 3 и 4 к оси шпинделя, а поверхности 7 и 8 располагают перпендикулярно оси шпинделя. Ремонт указанных поверхностей осуществляют путем механической обработки и шабрением.
Ремонт направляющих корпуса шпиндельной бабки шабрением. Направляющие корпуса шпиндельной бабки расточного станка ремонтируют шабрением в следующем порядке.
-
Зачищают поверхности 1—4, 6—8 от забоин, а с поверхностей 3, 4, 7 и 8 дополнительно снимают шабером верхний прикатанный слой металла. -
Устанавливают корпус поверхностью 6 на поверочной плите и определяют параллельность оси шпинделя к направляющим 3 и 4. Измерения производятся от плиты индикатором методом засечек по концам шпинделя с обеих сторон корпуса. Допуск параллельности этих поверхностей к оси шпинделя 0,02 мм на длине 1000 мм. -
Проверяют перпендикулярность поверхности 7 к оси шпинделя 5. Для этого к поверхности 4 и 7 прикладывают контрольный валик, концы которого выступают за пределы направляющих с обеих сторон корпуса. В отверстие для шпинделя устанавливают специальную оправку или собирают шпиндель на своих опорах. На шпинделе закрепляют специальный рычаг, на конце которого помещают индикатор. Вращением оправки или шпинделя делают при помощи индикатора засечки на образующей валика по обоим концам направляющей 7 и по разности наибольших отклонений стрелки определяют величину неперпендикулярности, которая допускается 0,03 мм на длине 1000 мм. -
Шабрят поверхности 3, 4, 7 и 8 по сопрягаемым поверхностям стойки. При этом учитывают замеренные отклонения. Количество отпечатков краски после шабрения должно быть 8—12 на площади 2525 мм. Замеры повторяются в процессе шабрения до достижения необходимой точности.
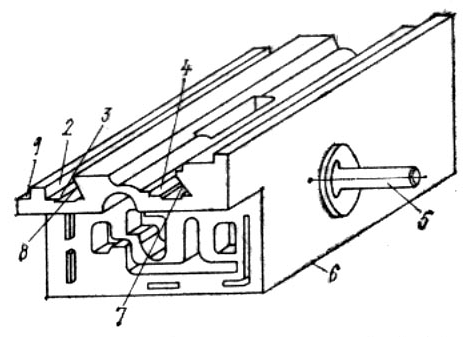
рис.3. Корпус бабки
Ремонт расточного шпинделя. До выбора метода ремонта шпинделя необходимо промерить индикаторным микрометром размеры диаметра по всей длине. Круглость и цилиндричность всей наружной поверхности можно также проверить пассиметром. Затем шпиндель устанавливают на призмах и проверяют изогнутость его путем вращения (биение наружной поверхности — по индикатору и биение конического отверстия — по контрольной оправке). Допускаемые отклонения: круглость наружной поверхности 15 мкм, цилиндричность 5 мкм на длине 1000 мм. Изогнутость шпинделя 0,02 мм на длине 1000 мм. Радиальное биение оправки, вставленной в конусное отверстие, 0,01 мм — у торца шпинделя и 0,02 мм — на длине 300 мм. При повышенных отклонениях производят шлифование наружной поверхности и конусного отверстия. Параметр шероховатости Ra = 0,160,08 мкм. Конусное отверстие с большим износом восстанавливают постановкой ремонтной втулки.
Опорные втулки расточного шпинделя, как правило, изготовляют заново. Их запрессовывают в полый шпиндель и затем растачивают на токарном станке, снимая припуск по внутреннему диаметру. Далее индикаторным нутромером определяют диаметры опорных втулок, а также точность посадки шпинделя со втулками. Допускаемые отклонения — круглость отверстий втулок и разность диаметров отверстий — 0,01 мм. Должно быть плавное перемещение шпинделя внутри полого шпинделя при диаметральном зазоре между ними в пределах 0,01—0,02 мм.
Ремонт хвостовой части. При ремонте хвостовой части (восстанавливают прямолинейность поверхностей 2, 3, 5 и 6, взаимную параллельность поверхностей 3, 5, и перпендикулярность их к поверхности 1. Поверхности 2 и 6 должны находиться в одной плоскости и быть перпендикулярны к поверхности 1. Восстановление поверхностей осуществляют шабрением или механической обработкой на станках (в зависимости от величины износа).
-
Приведем пример ремонта направляющих хвостовой части шлифованием. Очищают поверхности 9—11 установочных приливов, забоины, выступающие над этими поверхностями, и устанавливают корпус хвоста этими поверхностями на стол плоскошлифовального станка. -
Выверяют индикатором, установленным на корпусе шлифовальной бабки, параллельность поверхностей 8, 7 и 4 направлению перемещения станка и направлению перемещения каретки шлифовальной бабки по направляющим траверсы. Допускаемые отклонения 0,02 мм на длине 1000 мм. Аналогично выверяется параллельность поверхности 1 направлению перемещения каретки шлифовальной бабки по направляющим траверсы станка и направлению перемещения траверсы по колонне. Допуск параллельности 0,02 мм на длине 1000 мм. После окончательного закрепления хвостовой части на столе плоскошлифовального станка шлифуют поверхности 2 и 6, проверяя, чтобы эти плоскости строго лежали в одной плоскости. Допускаемые отклонения не более 0,02 мм на длине 1000 мм. Затем шлифуют поверхности 3 и 5, соблюдая строгую параллельность между ними. Допуск параллельности 0,02 на длине 1000 мм
Ремонт ползуна расточного шпинделя. Вследствие износа поверхностей 1—6 ось отверстия отклоняется от оси шпинделя и нарушается центровка винта с осью гайки перемещения ползуна. Поверхности ползуна оказываются непараллельными оси шпинделя.
-
Точность направляющих ползуна рационально восстанавливать установкой компенсационных накладок. Для этого необходимо поместить корпус ползуна поверхностями 2 и 4 на шлифованные подставки, установленные на столе поперечно-строгального станка. -
Индикатором, находящимся на корпусе ползуна поперечно-строгального станка, выверяют параллельность поверхностей 1 и 3 перемещению ползуна по направляющим станины. Допускаемые отклонения 0,02 мм на длине 1000 мм. -
Поверхности 1,3,5 и 6 строгают на глубину 1—3 мм с отклонениями до ±0,2 мм. На эпоксидном клее располагают компенсационные накладки из текстолита марки ПТ или других заменителей толщиной 3—5 мм, фрезеруют поверхности 1, 3, 5 и 6 до размера, определенного технологом в результате ремонта корпуса хвостовой части. -
Устанавливают ползун на расточный шпиндель горизонтально-расточного станка, собранного после ремонта, и пригоняют планками до рабочего натяга. Пришабривают компенсирующие накладки поверхностей 1, 3–6 до свободного перемещения расточного шпинделя по всей длине направляющих корпуса хвоста от легкого вращения маховичка вручную. Пришабривают поверхности 2 и 4 ползуна, добиваясь параллельности поверхностям 5 и 6 и точности прилегания к прижимным планкам. Допуск параллельности поверхностей 5 и 6–0,01 мм на всей длине. Количество отпечатков краски 8–12 на площади 25x25 мм.
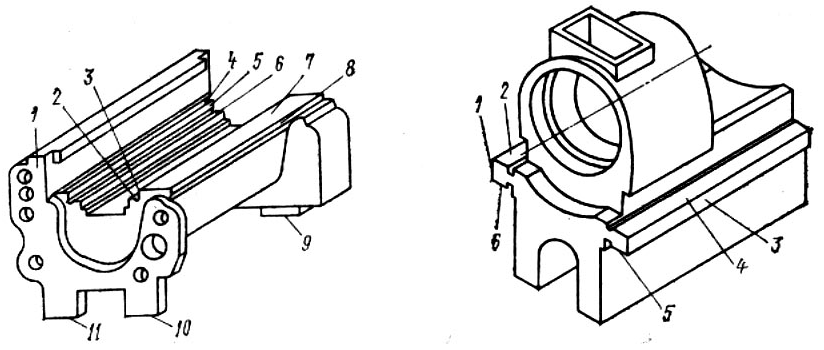
рис.4. Хвостовая часть и ползун шпинделя
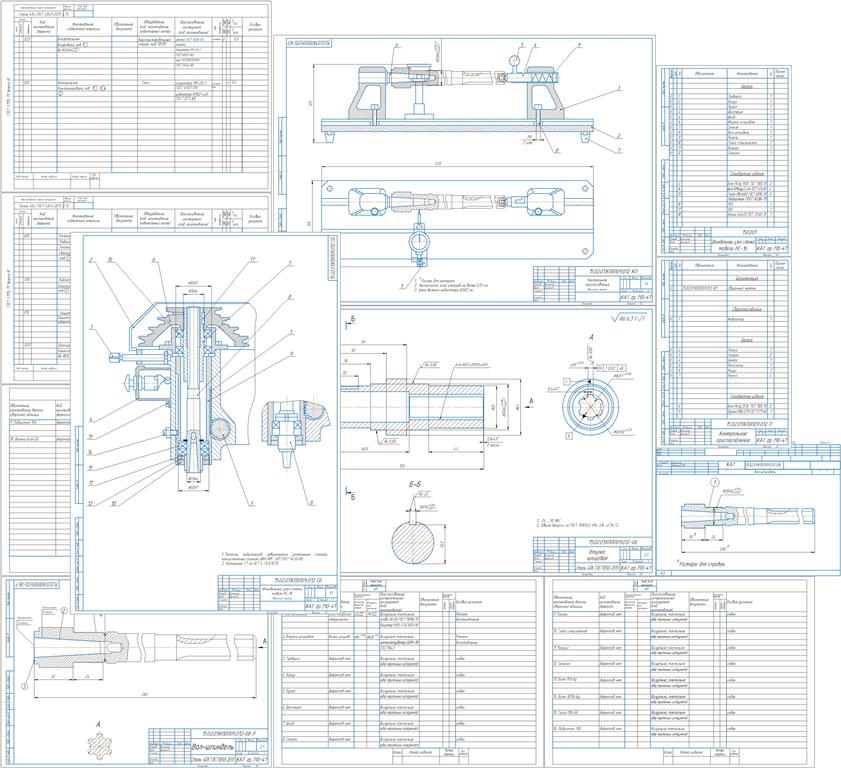
рис.5. Технологический процеес ремонта 1
3. Ремонт координатно-расточных станков
Координатно-расточные станки, среди прочего металлорежущего оборудования, занимают привилегированное положение, поскольку им доверяется обработка самых серьезных и точных деталей. Наличие специального отсчетного механизма, позволяет заготовке перемещаться относительно рабочего органа с отклонением до 0,001 мм, что гарантирует выполнение работ с минимальными погрешностями. С помощью координатно-расточных станков выполняют обработку отверстий с предельно точным расстоянием их расположения, не применяя дополнительных устройств, направляющих инструмент. Список операций, на которые рассчитано подобное оборудование, включает, сверление, растачивание, фрезерование, зенкерование, развертывание отверстий, разметку заготовок, контрольно-измерительные работы, чистовую обработку торцов изделий. Исходя из того, что такие станки решают чрезвычайно ответственную задачу, фактически, не допуская ни
малейших отклонений от координатных размеров, к их исправности предъявляются повышенные требования. Таким образом, ремонт координатно-расточных станков совсем необязательно связан с возвратом работоспособности. Чаще всего, на реставрацию поступают станки, нуждающиеся в восстановлении первоначальных технических характеристик.
Процесс капитального ремонта станка:
-
Проводятся осмотр и диагностика состояния станка. В процессе осмотра выявляются имеющиеся наружные дефекты, износ поверхностей и отклонения геометрических параметров станка от паспортных значений. Так, например, повышенный уровень шума при включении подачи стола или повышенная вибрация шпинделя (проявляющаяся даже не на всех значениях оборотов) могут свидетельствовать о значительном износе подшипников редуктора и шпинделя. Наличие рывков при подаче стола или шпинделя может указывать на износ бронзовых деталей червячных передач. -
Производится полная разборка станка: демонтируется стол, снимаются лицевые панели, двигатель и противовес, коробка скоростей, шпиндельная коробка. Далее производится поузловая разборка станка на отдельные детали с дальнейшей их очисткой, промывкой и дефектацией. В результате этих операций дополняются данные, внесённые в дефектную ведомость, и уточняется стоимость ремонта. -
Приступают к ремонту механической части станка. Особое внимание уделяют восстановлению плоскостности поверхности стола, который является базой при обработке деталей. Восстановлению также подлежат направляющие станины и направляющие качения, по которым перемещаются стол и салазки. Инженеры компании подберут оптимальный способ их восстановления. Например, для направляющих станины чаще всего используют метод шабрения. При ремонте направляющих качения извлекают все ролики из металлического сепаратора, проводят их калибровку и подгонку под нужный размер. -
Шпиндельный узел обеспечивает правильность геометрической формы, чистоту обработки и точность межосевых расстояний для обрабатываемых отверстий. Во время ремонта шпиндельного узла будут восстановлены радиальные однорядные роликоподшипники и упорные шарикоподшипники. Необходимый диаметр шпинделя восстанавливают методом хромирования гильзы с последующей шлифовкой. Отверстие в бабке притирается под имеющуюся гильзу. Отдельно проверяют инструментальный конус на биение, доводя его точность до 0,5 мкм. Ремонту также подлежат механизм точной ручной подачи, механизм осевой подачи, устройство остановки подачи при достижении заданной глубины. -
В случае сильной деградации или неправильной работы оптической системы отсчёта координат специалисты могут установить устройство цифровой индикации, обеспечивающее точность позиционирования 1–5 мкм. -
На заключительном этапе ремонта будет произведена сборка, окраска и испытание станка.
Заключение
В ходе прохождения производственной практики был собран материал, необходимый для написания отчета. Данная производственная практика является хорошим практическим опытом для дальнейшей самостоятельной деятельности. За время пройденной практики я познакомилась с новыми интересными фактами. Процесс прохождения производственной практики научил меня терпению и трудолюбию. Я узнала много новой и полезной информации, которая пригодится мне в дальнейшей учебе и трудоустройстве. Задания, выполняемые на практике, напрямую связанны с нашей специальностью, что значительно повысило мои знания по своей профессии. Также я извлекла для себя полезные уроки из различных рабочих ситуаций. производственная практика весьма необходима студентам для закрепления теоретических знаний, полученных в колледже.
Список литературы
-
Ачеркан Н.С. Металлорежущие станки, Том 1, 2019 -
Батов В.П. Токарные станки, 2020 -
Белецкий Д. Г. Справочник токаря-универсала, 2018 -
Денежный П.М., Стискин Г.М., Тхор И.Е. Токарное дело, 2021. (1к62) -
Денежный П.М., Стискин Г.М., Тхор И.Е. Токарное дело, 2022. (16к20)