Файл: Восстановление посадок и взаимного расположения деталей.docx
Добавлен: 26.10.2023
Просмотров: 225
Скачиваний: 8
ВНИМАНИЕ! Если данный файл нарушает Ваши авторские права, то обязательно сообщите нам.
предотвращение окисления расплавленного припоя в процессе пайки, для чего применяются соответствующие паяльные флюсъг
паяние при температуре, близкой к температуре плавления спаиваемой детали;
медленное охлаждение после паяния.
В зависимости от назначения спаиваемых деталей швы пайки подразделяются: на прочные швы (должны выдерживать механические нагрузки); плотные швы (не должны пропускать жидкостей или газов, находящихся под слабым давлением); прочные и плотные швы (должны выдерживать давление жидкостей и газов, находящихся под большим давлением).
В паяемых конструкциях применяют стали всех типов, чугуны, никелевые сплавы (жаропрочные, жаростойкие, кислотостойкие), медь и ее сплавы, а также легкие сплавы на основе титана, алюминия, магния и бериллия. Ограниченное применение имеют сплавы на основе тугоплавких металлов: хрома, ниобия, молибдена, тантала и вольфрама.
Родственным пайке процессом является лужение, при котором поверхность металлической детали покрывают тонким слоем расплавленного припоя, образующего в контакте с основным металлом припой-сплав переменного состава с теми же зонами, что и зоны при пайке. Лужение можно применять как предварительный процесс с целью создания более надежного контакта между основным металлом и припоем или как покрытие для защиты металлов от коррозии.
Напыление — один из способов нанесения металлических покрытий на изношенные поверхности. Сущность процесса состоит в распылении предварительно расплавленного материала струей воздуха, плазмы или пламенем газов и их смесей. Мелкие частицы расплавленного металла подаются на детали с высокой скоростью, деформируются при ударе об их поверхность, внедряются в ее неровности и образуют металлическое покрытие.
Преимущества способа — высокая производительность процесса в сочетании с простотой технологии и применяемого оборудования, а также высокая износостойкость покрытий и возможность нанесения их толщиной до 10 мм и более практически из любых металлов. Недостатки процесса — невысокая прочность сцепления покрытия с основным металлом при пониженной механической прочности.
По способу получения тепловой энергии для нагрева распыляемого материала напыляющие аппараты подразделяют на дуговые, газовые, высокочастотные и плазменные.
Дуговое напыление, схема которого показана на рис. 17.8., заключается в расплавлении электрической дугой исходного материала и напылении его струей сжатого воздуха на поверхность детали 1. Электрическая дуга горит между двумя проволоками 5, протягиваемыми роликами 4. Струя сжатого воздуха вытягивает дугу. Размер распыляемых частиц колеблется в пределах 10..50мкм. Скорость напыления на расстоянии 30 мм от сопла — до 250 м/с. Толщина напыленного слоя составляет от 20 мкм до 10 мм. Для электродугового напыления используют аппараты ЭМ-ЗА, ЭМ-9, ЭМ-б, ЭМ-10.
Газопламенное напыление осуществляют с помощью аппаратов (рис. 17.9.), в которых металлическая проволока или порошковые материалы распыляются ацетилене кислородным пламенем или пламенем других горючих газов в смеси с кислородом. При этом способе повышается прочность сцепления, уменьшаются размеры распыливаемых частиц металла и снижается его окисление. Недостатки — низкая производительность и сложность установки.
Для газопламенного напыления применяют аппараты ГИМ-1М, ГИМ-2М, МГИ-1-57, МГИ-2-65.
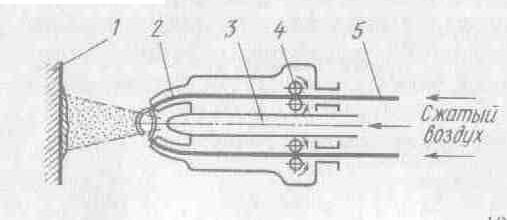
Рис 17.8. Схема дугового напыления деталей
1 — деталь, 2 — наплавляющие наконечники. 3 — воздушное сопло, 4 — подающие ролики. 5 — проволока
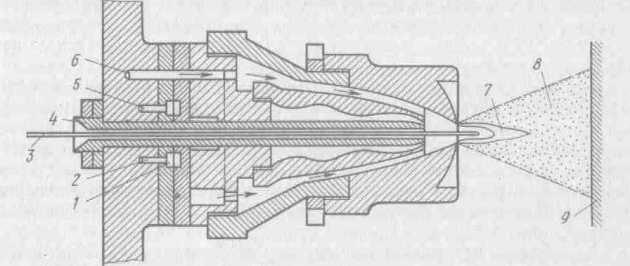
Рис. 17.9. Аппарат для газопламенного напыления;
1 — смесительная камера, 2 — канал для подвода кислорода, 3 — проволока, 4 — наплавляющая в гулка, 5 —канал для подвода ацетилена, 6 — воздушный канал, 7 –– пламя, 8 –– газометаллическая струя, 9 — деталь
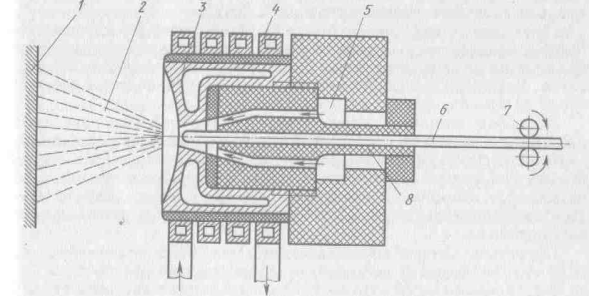
Рис. 17.10. Аппарат для высокочастотного напыления;
1 — деталь, 2 — газометаллическая струя, 3 — концентратор тока, 4 — индуктор, 5 — воздушный канал, 6 — проволока, 7 —подающие ролики, 8 — направляющая втулка
Высокочастотное напыление основано на использовании принципа индукционного нагрева при плавлении исходного материала. Распылительные головки аппаратов (рис. 17.10.) работают по принципу концентратора вихревых токов высокой частоты или конического нагревательного индуктора. В качестве источников питания применяют ламповые генераторы токов высокой частоты ГЗ-46, ЛГП-30, ЛГПЗ-60.
Преимущества высокочастотного напыления — незначительное окисление металла и достаточно высокая механическая прочность покрытия, недостатки — сложность и высокая стоимость оборудования
Плазменное напыление выполняют с помощью плазматронов, в которых плазмообразующий газ (аргон) протекает сквозь столб электрического разряда, частично или полностью ионизируется и превращается в плазму.
Плазмагрон состоит из катода и анода (сопла), охлаждаемых водой. От источника постоянного тока между катодом и анодом возбуждается электрическая дуга. Плазмообразующий газ, введенный в зону горения, ионизируется и выходит из сопла плазматрона в виде струи небольшого сечения. Высокая электропроводность плазменной струи значительно повышает плотность тока, температуру газа и скорость его истечения. Рабочая температура струи достигает 7000...15 000°С при скорости истечения до 1500 м/с.
Для плазменного напыления используют установки У ПУ-ЗМ, УМП-4-64, УМП-5-68, которые обеспечивают более высокие, чем при других способах напыления, механические свойства покрытия и более прочное его соединение с поверхностью детали. Покрытие обладает высокой износостойкостью и не снижает усталостной прочности детали. За счет высокой температуры плазменной струи можно наносить покрытия практически из любых материалов. Процесс полностью автоматизирован, что повышает производительность труда.
При плазменной наплавке проволокой можно использовать газопорошковую среду, которая служит как для защиты сварочной ванны, так и для использования порошка в качестве присадочного материала. В качестве плазмообразующего газа при распылении порошка кроме аргона применяют азот, водород, гелий.
Прочность сцепления повышается в 7...10 раз в случае оплавления покрытия при температуре, близкой к точке плавления нанесенного материала. Для плазменного напыления с последующим оплавлением наиболее пригодны порошковые сплавы на основе никеля, так называемые самофлюсующиеся порошковые материалы никельхромборкремниевой группы Ni — О — В — Si — С в виде гранулированных порошков.
Подготовка деталей к напылению включает в себя обезжиривание и очистку, механическую обработку, создание, шероховатости на поверхности детали (дробеструйной обработкой или накаткой зубчатым роликом) и защиту поверхностей, не подлежащих напылению.
После напыления обработка деталей состоит из медленного охлаждения их до температуры окружающей среды и механической обработки поверхности до требуемого размера. В зависимости от метода напыления, твердости покрытия, требуемой точности и шероховатости поверхностей применяют токарную обработку, растачивание или шлифование
В авторемонтном производстве при восстановлении деталей нашли широкое применение гальванические и химические процессы. Они применяются для компенсации износа рабочих поверхностей деталей, а также при нанесении на детали противокоррозионных и защитно-декоративных покрытий.
Из гальванических процессов наиболее широко применяются хромирование и железнение, а также никелирование, цинкование и меднение. Применяются также химические процессы; химическое никелирование, оксидирование и фосфатирование.
Гальванические покрытия получают из электролитов, в качестве которых применяют водные растворы солей тех металлов, которыми необходимо покрыть детали.
Катодом при гальваническом; осаждении металлов из электролитов является восстанавливаемая деталь анодом — металлическая пластина.
Применяют два вида анодов: растворимые и нерастворимые. Растворимые аноды изготавливают из металла, который осаждается на детали, а нерастворимые — из свинца.
При прохождении постоянного тока через электролит на катоде разряжаются положительно заряженные ионы и, следовательно, выделяются металл и водород. На аноде при этом происходят разряд отрицательно заряженных ионов и выделение кислорода. Металл анода растворяется и переходит в раствор в виде ионов металла взамен выделившихся на катоде.
Толщина гальванических покрытий на поверхности детали обычно получается неравномерной. Причиной этого является неудовлетворительная рассеивающая способность электролитов.
Под рассеивающей способностью электролита понимают его свойство обеспечивать получение равномерных по толщине покрытий на деталях. Чем выше рассеивающая способность электролита, тем более равномерными по толщине получаются покрытия на деталях.
Рассеивающая способность электролита может быть повышена за счет изменения состава электролита. Электролиты с малой концентрацией основной соли имеют более высокую рассеивающую способность. Более равномерное по толщине покрытие может быть также получено при применении фигурных анодов, копирующих форму детали; за счет рационального размещения анодов относительно катода; постановкой дополнительных катодов и токонепроводящих экранов.
Металлические покрытия, полученные в гальванических ваннах, имеют кристаллическое строение. Однако их кристаллическая решетка в значительной степени искажена. Причинами этого являются большие внутренние напряжения и внедрение водорода, выделяющегося на катоде.
На величину внутренних напряжений и другие свойства покрытий большое влияние оказывают режим их нанесения и состав электролита. Изменяя режим электролиза и состав электролита, можно управлять качеством гальванических покрытий.
Процесс нанесения покрытий на детали включает в себя три группы операций — подготовку деталей к нанесению покрытия, нанесение покрытия и обработку деталей после покрытия.
Подготовка деталей к нанесению покрытия включает следующие операции:
- механическую обработку поверхностей, подлежащих наращиванию;
- очистку деталей от окислов и предварительное обезжиривание;
- монтаж деталей на подвесное приспособление;
- изоляцию поверхностей, не подлежащих покрытию;
- обезжиривание деталей с последующей промывкой в воде;
- анодную обработку (активацию).
Предварительная механическая обработка деталей имеет цель придать восстанавливаемым поверхностям правильную геометрическую форму. Производится эта обработка в соответствии с рекомендациями по механической обработке соответствующего материала.
Очистку деталей от окислов с целью «оживления» поверхности производят путем обработки шлифовальной шкуркой или мягкими кругами с полировальной пастой. Предварительное обезжиривание деталей производят путем промывки в растворителях (уайт-спирите, дихлорэтане, бензине и др.).
При монтаже деталей на подвесное приспособление необходимо обеспечить их надежный электрический контакт с токопроводящей штангой, благоприятные условия для равномерного распределения покрытия по поверхности детали и для удаления пузырьков водорода, выделяющихся при электролизе. Для защиты поверхностей, не подлежащих наращиванию, применяют: цапонлак в смеси с нитроэмалью в соотношении 1:2 (его наносят в несколько слоев при послойной сушке на воздухе); чехлы из полихлорвинилового пластиката толщиной 0,3... 0,5 мм; различные футляры, втулки, экраны, изготовленные из неэлектропроводных кислотостойких материалов (эбонит, текстолит, винипласт и т. п.).
Окончательное обезжиривание подлежащих наращиванию поверхностей деталей производят путем электрохимической обработки в щелочных растворах следующего состава: едкий натр -10 кг/м3, сода кальцинированная — 25 кг/м3, тринатрийфосфат — 25 кг/м3, эмульгатор ОП-7 3...5 кг/м3. Режим обезжиривания: температура раствора 70...80°С; плотность тока 5... 10 А/дм; длительность процесса 1... 2 мин.
После обезжиривания детали промывают в горячей, а затем в холодной воде. Сплошная без разрывов пленка воды на обезжиренной поверхности свидетельствует о хорошем качестве удаления жиров. Активацию (анодную обработку) производят для удаления тончайших окисных пленок с поверхности детали и обеспечения наиболее прочного сцеплений гальванического покрытия с деталью.

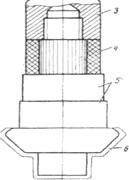
2. Крючок;