Файл: Восстановление посадок и взаимного расположения деталей.docx
Добавлен: 26.10.2023
Просмотров: 226
Скачиваний: 8
ВНИМАНИЕ! Если данный файл нарушает Ваши авторские права, то обязательно сообщите нам.
Государственное бюджетное профессиональное образовательное учреждение
Республики Марий Эл «Аграрно строительный техникум»
Специальность: 35.02.16Эксплуатация и ремонт сельскохозяйственной техники и оборудования
Курсовая работа
На тему: Восстановление посадок и взаимного расположения деталей
Выполнил: Иванов С.В
Группа 411
Руководитель: Садовин Е.В
2023г.
Содержание
Введение
1 Восстановления деталей слесарно - механической обработкой
2 Восстановления деталей способом пластического деформирования
3 Восстановления деталей сваркой и наплавкой
4 Восстановления деталей пайкой
5 Восстановления деталей напылением
6 Восстановление деталей гальваническими покрытиями
Введение
1. Большое количество деталей автомобилей и агрегатов в результате износа, усталости материала, механических и коррозийных повреждений
утрачивают свою работоспособность. Однако лишь некоторые из этих деталей -
наиболее простые и недорогие в изготовлении-утрачивают работоспособность
полностью и требуют замены. Большинство деталей имеет остаточный ресурс и м. б.
использованы повторно после проведения сравнительно небольшого объёма работ по
их восстановлению.
Восстановление деталей является одним из основных источников повышения экономической эффективности автомобильного производства.
При восстановлении деталей сокращаются расходы, связанные с обработкой деталей, т.к. при этом обрабатываются не все поверхности деталей, а лишь те, которые имеют дефекты.
Расходы на приобретение запасных частей составляют от 40-60% от себестоимости КР автомобилей, их можно значительно сократить за счёт расширения восстановления деталей.
Значение восстановления деталей состоит так же в том, что оно позволяет уменьшить потребности в производстве запасных частей.
Учитывая большое значение восстановления деталей, необходимо всемерно расширять эту сторону деятельности авторемонтных предприятий.
Слесарно-механическая обработка подразделяется на слесарную и механическую. Слесарные работы обычно дополняют или завершают механическую обработку восстанавливаемых деталей. Их применяют также при подготовке деталей к восстановлению другими способами, например сварке, пайке, склеиванию и т. д. К слесарным работам относятся опиловка, развертывание, зенкерование отверстий, сверление, прогонка и нарезание резьбы, шабрение, притирка, доводка до более полного прилегания.
Притирка пастами обеспечивает шероховатость поверхности 0,02 мкм и точность 5…7 квалитетов. Притирка находит широкое применение при ремонте деталей рабочих клапанов, сальников, запорной арматуры.
Развертывание применяют для чистовой обработки отверстий, например отверстий в бобышках поршня. Развертывание обеспечивает точность 7…9 квалитетов и шероховатость поверхностей 0,16 мкм. Это чистовая обработка поверхностей, когда достигается высокая точность. Развертывание осуществляется с помощью развертки .Высокое качество обработки обеспечивается тем, что развертка имеет большое число режущих кромок и снимает малый припуск.
Развертка – режущий инструмент, который нужен для окончательной обработки отверстий после сверления, зенкерования или растачивания
Механическая обработка применяется как самостоятельный способ восстановления деталей, а также в качестве операций, связанных с подготовкой или окончательной обработкой при восстановлении другими способами. Механическая обработка связана с выбором инструмента и режима обработки. При механической обработке восстанавливаемых деталей необходимо обеспечивать требуемую шероховатость, точность размеров формы и взаимного расположения рабочих поверхностей. Точность взаимного расположения поверхностей на детали зависит от правильного выбора технологической базы при её обработке. Технологическая (обработочная) база – это поверхности на детали, которые определяют положение детали в приспособлении относительно режущего инструмента. В качестве технологической базы рекомендуются поверхности, которые использовались при изготовлении этой детали.
Сущность слесарно-механической обработки заключается в восстановлении правильной геометрической формы и поверхностных свойств деталей, а также обеспечении их первоначальной посадки.
Восстановления деталей способом пластического деформирования
Сущность этого метода восстановления заключается в использовании пластических свойств металла, т. е. в способности под действием приложенных сил перемещаться с нерабочих участков детали к изношенному, чтобы восполнить ту убыль металла, которая произошла в процессе износа.
Метод пластического перераспределения металла отличается простотой восстановления, высокой производительностью и экономичностью.
Он может быть использован для ремонта деталей сравнительно простой конфигурации и осуществляется в горячем и холодном состоянии. Без нагрева можно восстановить детали из цветных металлов и малоуглеродистых сталей.
Осадку Применяют для увеличения наружного диаметра сплошных или уменьшения внутреннего диаметра полых деталей за счет уменьшения их высоты
Осадкой восстанавливаются втулки, толкатели клапанов, полуоси, пальцы и др.
Раздачей пользуются для восстановления наружных размеров полых деталей (например, втулки, поршневые пальцы). Увеличение наружного диаметра детали в этом случае достигается за счет соответствующего увеличения диаметра отверстия при продавливании через него специальной прошивки.
Обжатие применяется для уменьшения внутренних размеров полых цилиндрических деталей путем приложения давления к внешней поверхности. Направления деформации и действующего усилия совпадают Этим способом восстанавливают втулки, сепараторы подшипников качения, муфты с внутренним шлицевым или Зубчатым зацеплением и др.
Широкое применение при восстановлении деталей находят комбинированные способы деформации — осадка-раздача, обжатие-осадка и др.
Вдавливание применяют для увеличения размеров изношенных частей детали посредством перераспределения металла с ее нерабочих поверхностей. Вдавливание применяют при восстановлении изношенных боковых поверхностей шлицев, зубьев некоторых шестерен, шаровых пальцев и др.
Вытяжка и растяжка. При вытяжке увеличивают длину деталей (рычагов, тяг, стержней) за счет местного сужения их поперечного сечения на небольшом участке. Вытяжку выполняют в горячем состоянии с местным нагревом детали до 800—850 °С.
Растяжкой также добиваются увеличения длины детали, не в отличие от вытяжки направление, деформации совпадает с направлением действующей силы.
Накатка деталей, применяемая при восстановлении неподвижных посадок, основана на пластическом деформировании поверхностного слоя изношенной части детали рабочим инструментом — зубчатым роликом. Накатка осуществляется на токарном станке с установкой ролика в суппорте на специальной державке.
Подготовка деталей
Перед восстановлением детали сваркой или наплавкой с поверхности удаляют ржавчину, окалину, грязь металлической щеткой или пескоструйной обработкой до блеска. Обезжиривание выполняют растворителем или нагревом поверхности до 300⁰C. На кромках закрепляемых элементов снимают фаски. У трещин разделывают края под углом 120 — 140⁰, на концах сверлят отверстия диаметром 3 — 4 мм. Глухие трещины углубляют насквозь, чтобы газы при сварке не образовывали поры.
С деталей, которые уже восстанавливались, сначала удаляют остатки нанесенного ранее слоя. Затем проводят процедуру очистки. Если износ не больше 1 мм, с места восстановления снимают слой на глубину 0,5 — 1 мм шлифовальным кругом или резцом. Это обеспечит однородность структуры нанесенного сплава.
Электродуговая сварка и наплавка
Это самая распространенная технология восстановления в промышленности и на дому. Она легко выполняется на обычном сварочном оборудовании. Работу выполняют плавящимися покрытыми электродами и неплавящимися с присадочной проволокой.
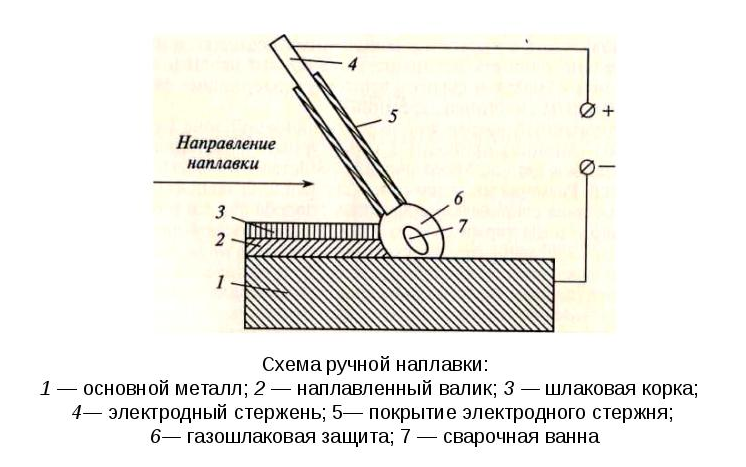
Качество конечного результата определяется параметрами электродов. Для ремонта сваркой площадь поперечного сечения стержней выбирают в зависимости от размера повреждения, толщины металла. Для создания слоя с заданными параметрами выбирают марки электродов с легирующими присадками. Они могут содержаться в металле и обмазке стержней. Важно!
Для предотвращения деформирования, детали из высокоуглеродистой легированной стали предварительно нагревают до 300⁰C.
После окончания работы проводят отпуск для снятия внутренних напряжений в сварочных швах. Для низкоуглеродистой, низколегированной стали предварительный нагрев не требуется.
На цилиндрическую поверхность валики накладывают тремя способами:
-
в виде спиралей; -
в форме замкнутых окружностей; -
параллельно оси вращения.
На плоские поверхности наплавляют рядом расположенные широкие валики либо узкие с перекрытием 0,3 — 0,5 по ширине. На место большого износа сначала накладывают слой из низколегированной стали. Наплавку и сварку элементов небольшой толщины выполняют на постоянном токе обратной полярности. Толстостенные детали сваривают переменным или постоянным током с прямой полярностью.
Сварка и наплавка под слоем флюса
Восстановление этим способом проводят электрической дугой, которая горит под расплавленным флюсом. Таким образом, создается эластичная оболочка, защищающая расплавленный металл от соприкосновения с воздухом. Флюсы также поддерживают стабильность горения дуги, раскисляют, легируют, рафинируют наплавляемый металл.
Для сварки и наплавки применяют два вида флюсов:
-
Керамические, состоящие из металлических и неметаллических компонентов, что позволяет проводить легирование в большом диапазоне. -
Плавленые не содержат металлических компонентов, поэтому возможности легирования ограничены десятыми долями процента. По сравнению с керамическими видами эти флюсы дешевле, лучше защищают, со швов легче отделяется шлак. Плавлеными флюсами с высоким содержанием кремния пользуются при нанесении слоев из углеродистых, низколегированных сортов стали.
Наплавку металла под флюсом проводят сварочной проволокой без покрытия. Диаметр (1 — 6 мм) определяют по толщине создаваемого слоя, формы валиков, габаритов деталей. Чтобы увеличить производительность, восстановление ведут ленточными электродами шириной до 10 см или одновременно двумя проволоками с подачей разными механизмами.
Восстановление выполняют на постоянном токе с обратной полярностью. На круглых деталях валики располагают с шагом 2 — 6 диаметра проволоки. Для уменьшения деформации на плоской поверхности наплавку ведут через валик или поочередно на разных участках.
Пайкой (паянием) называют процесс получения неразъемного соединения металлов, находящихся в твердом состоянии, при помощи расплавленного вспомогательного (промежуточного) металла или сплава, имеющего температуру плавления ниже, чем соединяемые металлы.
При ремонте автомобилей пайку применяют для устранения трещин и пробоин в радиаторах, топливных и масляных баках и трубопроводах, приборах электрооборудования, кабин, оперения и т.д.
Пайка как способ восстановления деталей имеет следующие преимущества: простота технологического процесса и применяемого оборудования; высокая производительность процесса; сохранение точной формы, размеров и химического состава деталей (а при пайке легкоплавкими припоями — сохранение структуры и механических свойств металла); простота и легкость последующей обработки, особенно после пайки тугоплавкими припоями; небольшой нагрев деталей (особенно при низкотемпературной пайке); возможность соединения деталей, изготовленных из разнородных металлов; достаточно высокая прочность соединения деталей; низкая себестоимость восстановления детали.
Основной недостаток пайки — некоторое снижение прочности соединения деталей по сравнению со сваркой.
Припой в процессе паяния в результате смачивания образует с поверхностью спаиваемой детали зону промежуточного сплава, причем качество паяния в таком случае при наличии чистых металлических поверхностей будет зависеть от скорости растворения данного металла в припое: чем скорость растворения больше, тем качество пайки лучше. Иначе говоря, качество паяния зависит от скорости диффузии. Увеличению степени диффузии способствуют:
наличие чистых металлических поверхностей спаиваемых деталей. При окисленной поверхности степень диффузии припоя значительно уменьшается или полностью отсутствует;