ВУЗ: Не указан
Категория: Не указан
Дисциплина: Не указана
Добавлен: 26.10.2023
Просмотров: 227
Скачиваний: 6
ВНИМАНИЕ! Если данный файл нарушает Ваши авторские права, то обязательно сообщите нам.
СОДЕРЖАНИЕ
1 ПРОЕКТИРОВАНИЕ ТЕХНОЛОГИЧЕСКОГО ПРОЦЕССА ЛЕСОСКЛАДСКИХ РАБОТ
1.2 Расчет объемов работ, выхода готовой продукции и отходов
1.3 Расчет суточного и сменного объемов работ по операциям
1.4 Обоснование системы машин, состава и типа технологического оборудования
2. ПРОЕКТИРОВАНИЕ ГЕНЕРАЛЬНОГО ПЛАНА НИЖНЕГО СКЛАДА
2.1 Разработка принципиальной схемы технологического процесса нижнего склада.
2.2 Расчет запасов лесоматериалов, выбор типа штабелей и расчет площади склада.
Кусковые отходы с помощью рубительного станка вырабатывается в технологическую щепу и выносится из цеха пневмотранспортной установкой ПНТУ-2М и отправляется в кучу щепы. Там эта куча выравнивается с помощью бульдозера и с помощью пневмопогрузчика ВО-59 подаётся на баржу и также отправляется к заказчику.
РЕФЕРАТ
на тему: «Шпалорезнотарный цех»
Описание производственного процесса шпалорезнотарного цеха
Шпалорезные цехи.
Производство шпал состоит из продольной распиловки шпальных кряжей и окорки (оправки) шпал. Одновременно с этим в шпалорезных цехах перерабатывают горбыли (получающиеся при производстве шпал) в тарные дощечки или в технологическую щепу.
Сырьем шпалорезных цехов служат шпальные кряжи длиной 2,75 м и диаметром 26 см и более. Продукцией шпалопиления являются обрезные и необрезные шпалы, переводные брусья, шпальные вырезки (доски) и горбыли. Размеры шпал для железных дорог широкой колеи регламентирует ГОСТ 78—65.
Схемы раскроя шпальных кряжей (называемые поставами) зависят в основном от диаметра кряжа. Типичные схемы поставов, предусматривающие выпиловку как шпал, так и досок приведены на рис. В некоторых случаях раскрой шпальных кряжей производится без выпиловки досок, при этом получаются толстые горбыли, распиливаемые на доски на ребровом станке. При такой технологии шпалопиления повышается производительность шпалорезного станка, но требуется дополнительная установка ребрового станка. Средний выход продукции при раскрое шпальных кряжей составляет: шпал 55—60 %, досок и горбылей по 10—15 %.
Для распиловки шпальных кряжей используют автоматические и неавтоматические шпалорезные станки; для окорки шпал — шпалооправочные станки; для переработки горбылей— ребровые, обрезные и торцовочные станки; для выработки щепы — рубительные машины. Окорка шпал может быть заменена окоркой шпальных кряжей. В этом случае в начале технологического потока шпалорезного цеха устанавливают роторный окорочный станок (ОК-63 или ОК-80). При этом горбыли, получающиеся при выпиловке шпал, оказываются окоренными и могут использоваться для выработки технологической щепы. При такой технологии приходится окаривать шпаль-ные кряжи, выпиленные из комлевой части хлыста и имеющие округлую или ребристую закомелистость. Для окорки таких кряжей роторные станки не приспособлены, кроме того, они не устраняют необходимости последующей оправки шпал, так как не дают их чистой окорки, необходимой для пропитки.
Технические схемы цехов включают операции подачи бревен, их окорку на роторных окорочных станках (ОК-80), раскряжевки на бревна длиной 2,75 м на установке ЛО-50А, продольную распиловку на фрезерно-пильном станке (для толстых бревен еще и на ЦДТ- 6-4 или ЛБ-150-1), оправку шпал на станке ЛО-44А, сортировку и пакетирование шпал и пиломатериалов.
Цехи шпалопиления. Выпиловка шпал состоит из продольных пропилов и окорки шпал. Окорка шпал может быть заменена окоркой шпальных кряжей на окорочных станках роторного типа (ОК-63 или ОК-80). В этом случае получаемые горбыли при распиловке оказываются окоренными и могут использоваться для выработки технологической щепы. Однако кряжи, полученные из комлевой части хлыста и имеющие эллипсную или ребристую закомелистость, на этих станках окаривать трудно, а подчас и невозможно. Кроме того, они не дают чистой окорки и не устраняют последующей оправки шпал. В настоящее время разработан фрезерно-пильный станок, позволяющий окоренные шпальные кряжи распиливать на шпалы с одновременным получением технологической щепы.
Схемы раскроя шпальных кряжей (постава на шпалы) зависят от диаметра кряжей. Типичные схемы поставов при выпиловке шпал и досок приведены на рис. 13.13, а, б, в. В большинстве случаев доски не выпиливают, а получают толстые горбыли, которые затем перерабатывают на мелкие пиломатериалы (например, тарную дощечку). В этом случае производительность шпалорезного станка повышается.
Рассмотрим технологический процесс шпалорезного цеха на базе одного станка, как наиболее приемлемый для условий нижних складов с небольшим объемом шпального сырья (рис. 13.13).
Шпальные кряжи продольным лесотранспортером 1 подаются в цех и сталкиваются автоматическим сбрасывателем 2 на буферную площадку 4. С площадки кряжи попадают на шпалорезный станок 5 (ЦДТ-6-3). Выпиленные на этом станке шпалы, доски и горбыли поступают на рольганг 10, с которого шпалы поперечным питателем 8 подаются на шпалооправочный станок 7 (ЛО-44А), а горбыли и доски поступают в тарное отделение цеха. Окоренные шпалы по лотку 9 выносятся за пределы цеха, где их сортируют и транспортируют на склад готовой продукции. Толстые горбыли торцуются на станке 12 (ЦКБ-40-1 или ЦКБ-63-1), проходят через ребровый 13 (ЦР-4) и обрезной 14 (например, Ц2Д-5А) станки и полученные доски выносятся из цеха транспортером 15. Этим же транспортером выносятся из цеха доски, полученные при выпиловке шпал и прошедшие через обрезной станок, а также тонкие горбыли, не прошедшие обработку на станках. Опилки, стружки, обрезки скребковыми транспортерами 3 и 11 доставляются в бункер 6. Сменная производительность такого цеха 400...500 шпал (или 70 м3 по сырью).
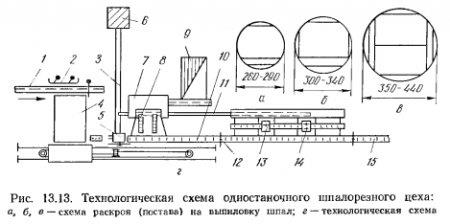
Шпалы (чертеж 13)- двухкантные, трехкантные или четырехкантные брусья специальных размеров по ГОСТ 78-2004
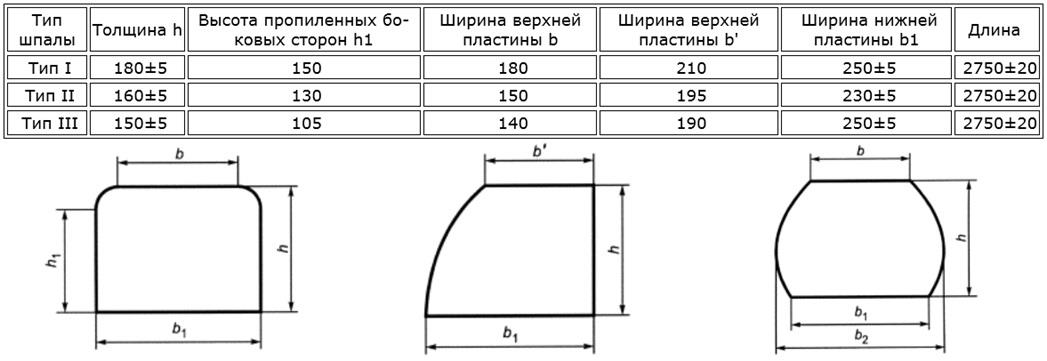
Описание технологического процесса производства тарной дощечки.
Низкокачественная древесина, имеющая внутреннюю гниль, короткомерные деловые отрезки, остающиеся от раскряжевки хвойных и особенно лиственных хлыстов, а также горбыли, получающиеся в шпалорезных цехах, перерабатывают на лесных складах в мелкие пиломатериалы — тарные дощечки. В цехи по переработке низкокачественной древесины в мелкие пиломатериалы (так называемые тарные цехи) поступают хвойные и лиственные кряжи диаметром 12 см и больше, длиной от 1 до 5 м, имеющие внутреннюю гниль не более половины диаметра. Продукцией этих цехов являются обрезные дощечки длиной от 0,3 до 1,3 м, толщиной 4—25 мм и шириной 40—180 мм, а также бруски таких же размеров по длине и ширине при толщине до 100 мм. Тарные дощечки отгружают потребителям комплектами, увязанными проволокой. Выход готовой продукции при переработке низкокачественной древесины в мелкие пиломатериалы составляет 25—35 % в зависимости от качества сырья и толщины выпиливаемых дощечек.
Основным оборудованием, используемым в тарных цехах, являются круглопильные станки для продольной и поперечной распиловки и тарные лесопильные рамы.
Технологический процесс тарных цехов строится по следующей схеме. Кряжи длиной более 1,8 м и диаметром свыше 25 см (рис. 13.9, а) распиливают шпалорезным станком на сегменты и лафеты, а затем на бруски, которые пропускают через тарную лесопильную раму; полученные при этом дощечки торцуются на педальной торцовке или концеравнителе. Из кряжей тоньше 25 см (рис. 13.9, б) на шпалорезном станке выпиливают двухкантный брус, поступающий сразу же на тарную лесопильную раму. Кряжи короче 1,8 м распиливают по тем же схемам; сегменты и лафеты выпиливают на развальном станке, бруски— на тарно-брусующем, а дощечки — на тарно-делительном или на коротышевой лесопильной раме. Горбыли перерабатывают в мелкие пиломатериалы на ребровых и обрезных станках.
В тарный цех производительностью 30—35 м3 в смену по сырью (рис. 13.9, в) кряжи длиной от 2 до 5 м и диаметром до 60 см, подсортированные по породам, поступают по продольному лесотранспортеру 1 и через буферную площадку 2 подаются на тележку шпалорезного станка 13 (ЦДТ-6-3). Сегменты и лафеты, полученные на этом станке при распиловке толстомерных кряжей, накапливаются на поперечном транспортере 4 и при помощи тельфера 3 подаются на площадку 2 для повторного пропуска через шпалорезный станок с распиловкой на бруски. Бруски поперечным транспортером подаются к тарной лесопильной раме 5 (РТ-36) для распиловки на дощечки. Лафеты, выпиленные из кряжей диаметром меньше 25 см, вторично через шпалорезный станок не пропускаются, а сразу подаются к тарной лесопильной раме. Торцовка доще-чек производится на станке 7 (ЦКБ-4). Часть сегментов и лафетов от шпалорезного станка по роликовому транспортеру 12 подается к торцовочному станку 11 (ЦКБ-4), которым распиливается на заготовки длиной до 1,2 м; последние проходят тарно-брусующий станок 10 (ТБС-2) и тарно-делительный 9 (ТДС-2). Дощечки от тарной лесопильной рамы и тарно-делительного станка укладываются в пакеты 8, которые подаются в сушильное отделение или на склад готовой продукции. Кусковые отходы выносятся из цеха ленточным транспортером 6; опилки удаляются пневмотранспортной установкой.
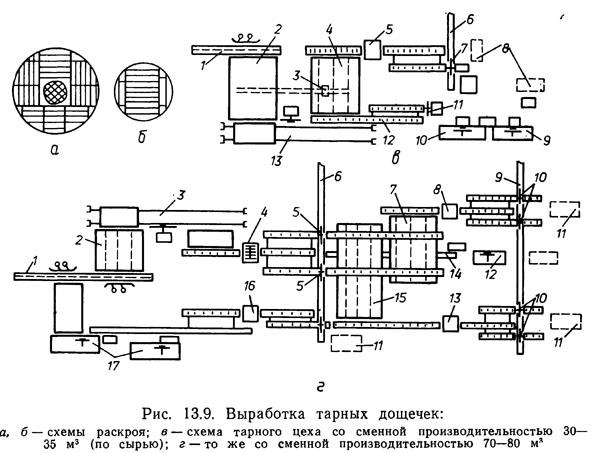
Выработка технологической щепы.
Для выработки технологической щепы на лесных складах используют низкокачественную древесину, отходы шпалопиления.
Кряжи низкокачественной древесины, перерабатываемые в технологическую щепу, имеют длину 1—2 м и могут быть разделены на две группы: тонкомерные диаметром до 20 см, без гнили или с малым ее содержанием; толстомерные диаметром более 20 см с внутренней гнилью, занимающей до половины площади торца. Каждая из этих групп требует особых приемов переработки. Кряжи первой группы подлежат окорке и измельчению; кряжи второй группы следует раскалывать, очищать от гнили и лишь после этого измельчать в щепу.
Отходы лесопиления и шпалопиления, используемые в качестве сырья для выработки технологической щепы, представляют собой в основном горбыли и рейки, длина которых примерно равняется или несколько меньше длины пиловочных бревен, а толщина и ширина зависят от диаметра распиливаемых бревен и схемы постава. При распиловке неокоренных бревен горбыли содержат 20—25 % коры. Окорка горбылей весьма трудоемка, поэтому производство технологической щепы из отходов лесопиления становится эффективным только при предрамной окорке пиловочника и поступлении на переработку окоренных горбылей и реек или при использовании дополнительных установок по облагораживанию щепы. Таким образом, выработка технологической щепы из отходов лесопиления заключается в основном только в ее измельчении, а иногда и в облагораживании щепы.
Отходы лесозаготовок, доставляемые на нижний склад и являющиеся сырьем для выработки технологической щепы, представляют собой вершины и сучья длиной от 0,5 до 5 м. Сучья содержат до 20 % коры, обладающей значительной механической прочностью. Окорка тонких сучьев и вершин связана с большими трудностями, поэтому такие отходы следует использовать Для выработки технологической щепы только для производств, в которых допускается наличие коры (производство древесноволокнистых плит, арболита, использование в энергохимических установках). Окорка толстых сучьев и вершин практически выполнима, однако выделение их из общей массы сучьев экономически нецелесообразно. Таким образом, переработка вершин и сучьев в щепу в основном состоит только из их измельчения (без окорки).
Щепа, вырабатываемая из низкокачественной древесины и отходов лесопиления (из стволовой древесины), должна удовлетворять требованиям ГОСТ 15815—70. Оптимальными являются следующие размеры щепы: для производства целлюлозы, древесноволокнистых плит и гидролизного производства — длина по волокну 20—25 мм, толщина не более 5 мм; для производства древесностружечных плит — длина 20—40 мм, "толщина (учитывая вторичное измельчение в цехах ДСП) до 30 мм. Практически рубительные машины дают значительные колебания длины получаемой щепы, поэтому ГОСТ регламентирует фракционный состав щепы, т. е. процентное содержание щепы различных размеров. Фракционный состав проверяется просеиванием щепы через сита с отверстиями разных диаметров. При этом должно пройти-через сито с отверстиями диаметром 30 мм, но задержаться на сите диаметром 10 мм не менее 85—90 % щепы для сульфитной целлюлозы, 80—85 % — для сульфатной целлюлозы, 80 % для древесноволокнистых плит. Не менее 90 % щепы, предназначенной для производства древесностружечных плит, должно задерживаться на обоих этих ситах. Торцы щепы для производства целлюлозы и древесноволокнистых плит должны быть чистыми, 9срезанными под углом 30—60°. Для других производств качество среза не регламентируется. В технологической щепе допускается некоторое количество коры и гнили: для сульфитной целлюлозы— коры до 1,5%, гнили до 1 %; для сульфатной целлюлозы — соответственно 3 и 5 %; для древесноволокнистых и стружечных плит 15 и 5%; для гидролизного производства И и 2,5%. Щепа должна быть рассортирована по породам (хвойная отделена от лиственной).
Процент выхода технологической щепы зависит от вида перерабатываемого сырья, способа переработки и назначения готовой продукции. При переработке отобранной низкокачественной древесины выход щепы для сульфитной целлюлозы составляет 60—63 %, для сульфатной целлюлозы 65—70 %, для древесноволокнистых и древесностружечных плит 80%. При переработке отходов лесопиления выход технологической щепы составляет 90—92 %, а при использовании в качестве сырья сучьев и вершин 70—75 % (для производства древесностружечных плит и арболита).
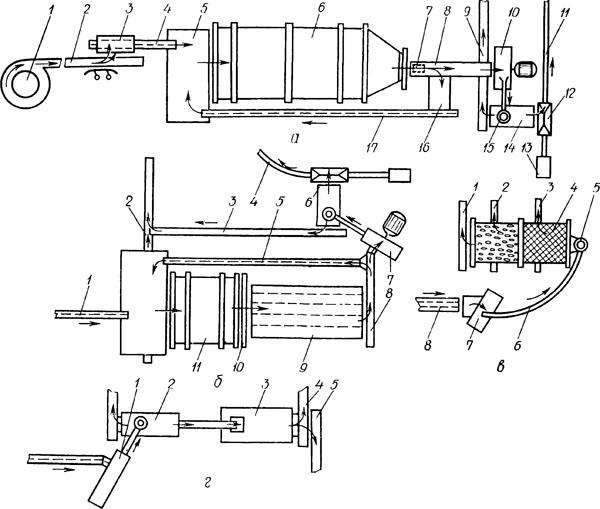
Рис. 13.10. Схемы цехов по выработке технологической щепы:
а — для переработки низкокачественной древесины со сменной производительностью 60 м3 (по сырью); б — то же 30 м3; в —для переработки сучьев и вершин; г—для измельчения неокоренного сырья с последующим облагораживанием щепы.