Добавлен: 29.10.2023
Просмотров: 65
Скачиваний: 4
ВНИМАНИЕ! Если данный файл нарушает Ваши авторские права, то обязательно сообщите нам.
Выход охлажденного газа: После охлаждения газа в аппарате охлажденный газ выходит через выходной порт или трубопровод. Он готов к использованию или дальнейшей обработке в зависимости от требований процесса.
1.3 Пылеуловители (ПУ).
Захват пыли: Пылеуловитель газа предназначен для захвата и удаления пыли из газового потока. Газовый поток с пылью поступает в пылеуловитель через входной порт или трубопровод.
Разделение пыли: Внутри пылеуловителя газ проходит через специальные устройства, которые помогают разделить пыль от газа. Обычно это включает использование циклонов, где газовый поток вращается, создавая центробежные силы, которые отделяют пыль от газа. Также могут быть использованы фильтры или электростатические принципы для разделения пыли.
Удержание пыли: Разделенная пыль удерживается внутри пылеуловителя. Это может быть достигнуто с помощью фильтров, сеток или других устройств, которые задерживают пыльные частицы.
Очистка или удаление пыли: Накопившаяся пыль в пылеуловителе должна быть очищена или удалена периодически. Это может включать механическую очистку фильтров или сброс пыли из устройства. Очищенный пылеуловитель готов к следующему циклу захвата пыли.
Выход очищенного газа: После прохождения через пылеуловитель, очищенный газ выходит через выходной порт или трубопровод. Он может быть выведен в атмосферу или направлен для дальнейшего использования в зависимости от требований процесса.
1.4 Камера приёма и запуска поршня (КПП и КЗП).
Подготовка к запуску: Перед запуском поршня необходимо подготовить камеру приема. Это может включать очистку камеры от прежнего материала, проверку работоспособности системы смазки, подготовку поршня и проверку пути движения поршня.
Прием поршня: В этом этапе поршень поступает в камеру приема. Он может быть доставлен с помощью грузового лифта, транспортной системы или других механизмов. Камера приема должна быть достаточно просторной, чтобы вместить поршень.
Фиксация поршня: После приема поршня он должен быть надежно зафиксирован в камере приема. Это может быть достигнуто с помощью специальных зажимов, фиксаторов или других устройств, которые обеспечивают надежное удержание поршня в позиции.
Подготовка к запуску: Перед запуском поршня необходимо выполнить ряд подготовительных операций. Это может включать смазку поверхностей контакта, проверку работоспособности системы запуска и регулировку уровня сжатия внутри камеры запуска.
Запуск поршня: На этом этапе происходит запуск поршня в движение. Это может быть достигнуто с помощью различных механизмов, таких как гидравлика, пневматика или механические приводы. При запуске поршня должны быть обеспечены безопасность и контроль скорости движения.
Движение поршня: Поршень начинает двигаться внутри камеры запуска. Он может совершать линейное движение, вращаться или выполнять другие заданные траектории, в зависимости от конкретного приложения и требований процесса.
Завершение работы: По окончании запуска поршня его движение завершается. Поршень может быть остановлен в определенной позиции, возвращен в исходное положение или переключен на другой этап процесса. Камера приема может быть освобождена от поршня для последующего цикла работы.
1.5 Сепараторы низкого и высокого давления.
Захват и отделение жидкости: В начале работы сепаратора низкого и высокого давления, газово-жидкостная смесь поступает в сепаратор. Внутри сепаратора осуществляется отделение жидкой фазы (обычно воды или других жидкостей) от газовой фазы. Это достигается за счет применения гравитационных или центробежных сил, которые обеспечивают разделение фаз.
Сбор и удаление жидкости: Отделенная жидкая фаза собирается и удаляется из сепаратора. Это может быть осуществлено с помощью сборных емкостей, дренажных клапанов или других устройств для сбора и удаления жидкости. Это важно для обеспечения надлежащей работы газового потока и предотвращения повреждений и коррозии оборудования.
Выделение газа: После отделения жидкой фазы, газовая фаза продолжает проходить через сепаратор. В этом этапе газовая фаза подвергается финальной очистке от оставшейся жидкости или твердых частиц, которые могли остаться после предыдущих этапов обработки.
Регулировка давления: В некоторых случаях, сепаратор низкого или высокого давления может быть использован для регулировки давления газа. Это может быть достигнуто путем настройки уровня жидкости в сепараторе или регулировкой клапанов и устройств контроля давления.
Мониторинг и контроль: Во время работы сепаратора осуществляется мониторинг и контроль его параметров и параметров процесса. Это включает измерение давления, температуры, уровня жидкости, потока газа и других параметров. Результаты мониторинга используются для обеспечения безопасной и эффективной работы сепаратора.
Остановка и обслуживание: По окончании работы или при необходимости, сепаратор низкого и высокого давления останавливается. Это может включать постепенное снижение нагрузки и остановку всех компонентов сепаратора. После остановки проводится обслуживание, включая очистку, проверку и замену необходимых элементов, чтобы подготовить сепаратор к следующему циклу работы.
6. Индивидуальное задание
Тема: «Наблюдение за состоянием оборудования и систем по показаниям приборов».
Система автоматики в автоматическом режиме отслеживает:
1) оперативные параметры работы агрегата:
- режим работы агрегата;
- температура в нагнетании и резервуаре;
- давление в нагнетании и резервуаре;
2) счетчики моточасов агрегата;
3) предупреждения о необходимости замены расходных материалов и проведении технического обслуживания;
4) записи о последних аварийных остановах с указанием отметки наработки агрегата на момент останова и причины.
Для отображения информации о состоянии системы, полученной от штатных контроллеров, в диспетчерской используется операторская панель, а в машинном зале - для визуального анализа состояния системы - используются световые индикаторы красного, желтого и зеленого цветов.
Для лучшего восприятия световые индикаторы на шкафу системы разнесены по группам: «КОМПРЕССОРЫ», «ОСУШИТЕЛИ», «СВЯЗЬ RS485».
Группа «КОМПРЕССОРЫ» отображает состояние компрессоров и имеет три световых индикатора:
Зеленый - «НОРМА»– хотя бы один агрегат находится в работе;
Желтый - «ВНИМАНИЕ»– есть предупреждения хотя бы по одному из агрегатов;
Красный - «АВАРИЯ»– есть аварийный сигнал хотя бы от одного из агрегатов.
Группа «ОСУШИТЕЛИ» отображает состояние осушителей сжатого воздуха Donaldson №1 и №2 . Каждая из подгрупп (№1 и №2) имеет по два световых индикатора:
Зеленый - «НОРМА» - осушитель включен в электрическую сеть и температура точки росы находится в пределах нормы;
Красный - «ОТКАЗ» - осушитель включен в электрическую сеть и температура точки росы находится за пределами нормы (как в положительную, так и в отрицательную сторону).
Текущие значения температур можно посмотреть на панели оператора. В случае, когда не горит ни один световой индикатор.
Группа «СВЯЗЬ RS485» имеет три зеленых световых индикатора и отвечает за цифровую связь с оборудованием:
«Панель» - отображает состояние связи с цифровой панелью оператора;
«Агр.1,2» - отображает состояние связи с системами управления компрессорными агрегатами Allegro 60 (№1 и №2);
«Агр.3» - отображает состояние связи с системой управления компрессорным агрегатом Allegro 30.
В случае, когда индикатор соответствующего оборудования светится – цифровая связь с данным оборудованием в норме, когда индикатор соответствующего оборудования не светится – цифровая связь с данным оборудованием отсутствует.
На операторской панели отображается мнемосхема компрессорной станции: два компрессора Allegro 60, один компрессор Allegro 30, два осушителя сжатого воздуха Donaldson. Возле каждого агрегата отображаются основные оперативные параметры, по которым можно быстро определить состояние агрегата в данный момент времени:
- статус агрегата (вкл/выкл, зеленый/красный цвет);
- процент загрузки компрессора (%);
- давление пневмосети (Bar);
- температура масла (°С);
- значения счетчиков сервисных моточасов и установки интервалов моточасов, по каждой группе обслуживания агрегата.
К параметрам осушителей относятся:
- статус агрегата (вкл/выкл, зеленый/красный цвет);
- температура испарителя (°С).
Контроллер содержит информацию о периоде эксплуатации расходных материалов (фильтр, масло и т.д.) и сообщает через индикаторы о необходимости их замены. При этом контролирует процесс очередной регламентной замены и правильность установки новых интервалов.
Индикаторы заблаговременно предупреждают персонал о необходимости технического обслуживания.
Интервалы обслуживания для данного типа оборудования установлены заводом изготовителем на отметке в 4000 часов:
- 4000 часов – 300 часов – зеленый цвет (норма) индикатора;
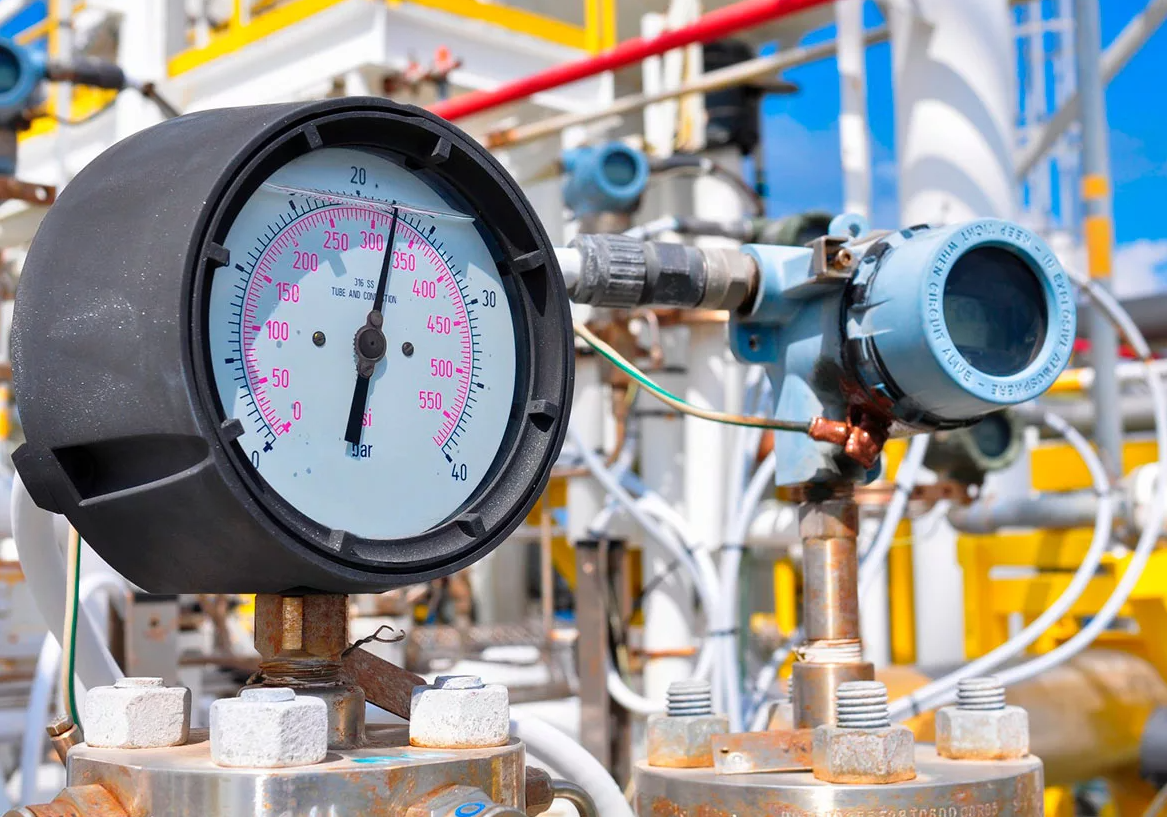
Рисунок 2 – Цифровой измеритель давления (манометр)