Файл: Современные требований к производству кабельной продукции позволят снизить риски возникновения пожаров.docx
ВУЗ: Не указан
Категория: Не указан
Дисциплина: Не указана
Добавлен: 29.10.2023
Просмотров: 11
Скачиваний: 2
ВНИМАНИЕ! Если данный файл нарушает Ваши авторские права, то обязательно сообщите нам.
Современные требований к производству кабельной продукции позволят снизить риски возникновения пожаров
Применявшаяся до 2008 г. для ремонта и строительства тягового подвижного состава кабельная продукция «старого поколения» имела изоляцию и оболочки из материалов, подверженных горению. Срок службы этих материалов не более 15 лет для фиксированного монтажа и 6 — 8 лет — для присоединения к подвижным токоприемникам. При этом требования пожаробезопасности при групповой прокладке кабелей предусмотрены не были, что повышало риск возникновения пожара. Данный срок службы продукции требовал 100%-ной замены высоковольтных кабелей и частично низковольтной кабельной продукции в зависимости от ее технического состояния при проведении средних ремонтов и полной ее замены на всех локомотивах при их капитальном ремонте. Необходимо отметить, что всего за период с 2008 по 2019 гг. произошло 147 случаев пожаров (78 — тепловозы, 69 — электровозы), причиной которых стала кабельно-проводниковая продукция (рис. 1). Анализируя более детально период с 2016 по 2019 гг., установлено, что всего произошло 166 случаев пожаров на локомотивах. Так, в 2016 г. совершилось 47 случаев, 2017 г. — 54,2018 г. — 35,2019 г. — 30 (рис. 2). Из всех указанных случаев за этот период времени — 18 пожаров допущено на тяговом подвижном составе по причине кабельно-проводниковой продукции, что составляет 11 % от общего числа случаев. По данной причине в 2016 г. произошло 4 случая (2,4 %), в 2017 г. — 6 (3,6 %), в 2018 г. — 5 (3,0 %), в 2019 г. — 3 (1,8 %). Из 18 случаев пожаров, допущенных по причине возгорания кабельно-проводниковой продукции, 9 — возникли в электрич цепях управления и 9 — в силовых электрических цепях. Так, в 2016 г. произошло 4 случая в электрических цепях управления, в 2017 г. — 4 случая в силовых электрических цепях и 2 случая электрические цепи управления, в 2018 г. — 3 случая в силовых электрических цепях и 2 случая в электрических цепях управления, в 2019 г. — 2 случая в силовых электрических цепях и один случай в электрической цепи управления (см. рис. 2). Для формирования единой технической политики ОАО «РЖД», в соответствии с требованиями Федерального закона от 22.07.2008 №ФЗ-123, разработаны и утверждены 6 марта 2009 г. «Технические требования к новой кабельной продукции для подвижного состава ОАО "РЖД"». В них учтены условия эксплуатации
, современный уровень пожарной безопасности и рекомендуемые сроки службы кабельно-проводниковой продукции. Одновременно с этим, распоряжением Компании в 2010 г. было принято решение о переходе на новые марки кабельно-проводниковой продукции. Для поддержки технических требований к новой кабельной продукции для подвижного состава ОАО «РЖД» в 2010 - 2011 гг. разработан ГОСТ Р 54965—2012 «Кабели и провода для подвижного состава железнодорожного транспорта. Общие технические условия». За основу документа взяты вышеуказанные технические требования и технические условия в зависимости от параметров эксплуатации и мест прокладки кабельно-проводниковой продукции. Результатом работ по этому направлению стал введенный в действие приказом Росстандарта от 10.09.2015 № 1322-ст ГОСТ 33326—2015 «Кабели и провода для подвижного состава железнодорожного транспорта. Общие технические требования». Так, за пять лет работы над повышением качества и безопасности кабельно-проводниковой продукции для железнодорожного транспорта удалось сформировать и обеспечить следующие параметры данной продукции:
Ф диапазон рабочих температур на жиле высоковольтных проводов и кабелей установлен от -60 до +155 °C; ® стойкость к вибрациям и многократным ударам проводов и кабелей установлена согласно требованиям, ГОСТ 17516.1 —90 (с изменениями №1,2) (для группы М27) и ГОСТ 16962.2—90 (с изменением № 1); ® стойкость к изгибам проводов и кабелей с одновременным закручиванием при температуре -50°C для присоединения к токоприемникам; © стойкость к воздействию на оболочку кабелей и проводов масла и дизельного топлива; ® озоностойкость и стойкость к воздействию солнечной радиации; ® нераспространение горения при прокладке в пучках и дымогазовыделение при горении и тлении; ® эквивалентный показатель токсичности продуктов горения кабельного изделия; ® огнестойкость — работоспособность в пламени 90 мин при температуре 750°C для систем пожаротушения и пожарной сигнализации, системы оповещения, системы открывания и закрывания дверей. Соблюдение вышеуказанных требований позволяет достичь следующих результатов: увеличение срока службы кабельно-проводниковой продукции с 15 до 30 лет и выше; & повышение безопасности эвакуации людей, а также эффективности тушения пожара путем сохранения видимости при возникновении пожара; & повышение безопасности жизни и здоровья людей в случае возникновения пожара, что стало возможным благодаря минимизации негативного воздействия продуктов горения; сохранение работоспособности систем пожарной автоматики при возникновении пожара. Важным направлением в повышении пожарной безопасности кабельно-проводниковой продукции является стандартизация, которая посредством разработанных стандартов,
реализованных в производстве, позволяет достичь необходимых показателей.
Именно нормативная документация определяет требования к выпуску продукции, образующая своеобразный потолок безопасности при эксплуатации, а именно: > высоковольтное оборудование и вспомогательные электроприводы, включая соединительные провода и кабели, не должны создавать уровень напряженности радиопомех как в движении, так и на стоянке локомотива, превышающий требования ГОСТ 33436.3-1—2015; > кабели и провода, применяемые на локомотиве, должны выбираться на основе условий эксплуатации тягового подвижного состава. При этом кабели и провода должны соответствовать ГОСТ 33326—2015 (с изменением № 1), ГОСТ 33798.1—2016 (IEC 60077-1:1999) и ГОСТ 33798.2—2016 (IEC 60077-2:1999); > прокладка силовых кабелей к тяговым электродвигателям должна исключать перетирание при возможных взаимных перемещениях кузова и тележки; > каждый конструктивный узел электрической аппаратуры и подводящие провода должны иметь четкую, долговечную и несмываемую маркировку по ГОСТ 18620—86 (с изменением № 1, с поправкой) в соответствии с электрической и монтажной схемой локомотива; > минимальная длина пути тока утечки и минимально допустимые расстояния между разнопотенциальными частями оборудования локомотива должны соответствовать требованиям стандарта ГОСТ33798.1—2016 (IEC 60077-1:1999) и ГОСТ 33798.2—2016 (IEC 60077-2:1999); > электрооборудование локомотива должно обеспечивать реализацию длительного режима работы без превышения предельно допустимых температур нагревания оборудования; > с учетом особенностей профиля пути Восточного региона, предполагающего высокую тепловую нагрузку электрооборудования, устанавливаемые на локомотиве компоненты тягового электрооборудования, а также применяемые провода и кабели должны иметь электрическую изоляцию повышенной нагревостойкости; > кузов, тележки и подкузовное оборудование, в том числе закрепленное на тележках, включая подводящие кабели, провода и трубопроводы, должны выдерживать удары от щебня по ГОСТ 7392—2014 без механических повреждений. Вышеуказанные мероприятия по разработке стандартов и реализации их требований в производстве позволили снизить
риски возникновения нежелательных событий, пожаров, а также уменьшить стоимость технического обслуживания и ремонтов.
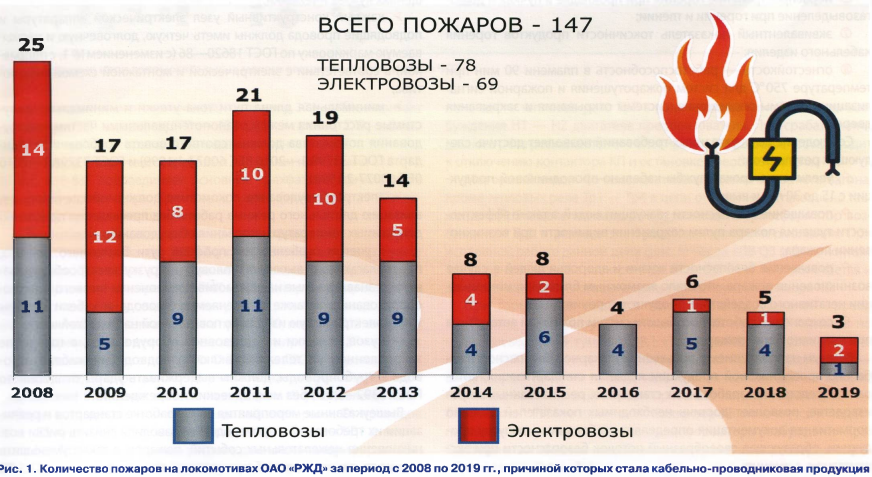
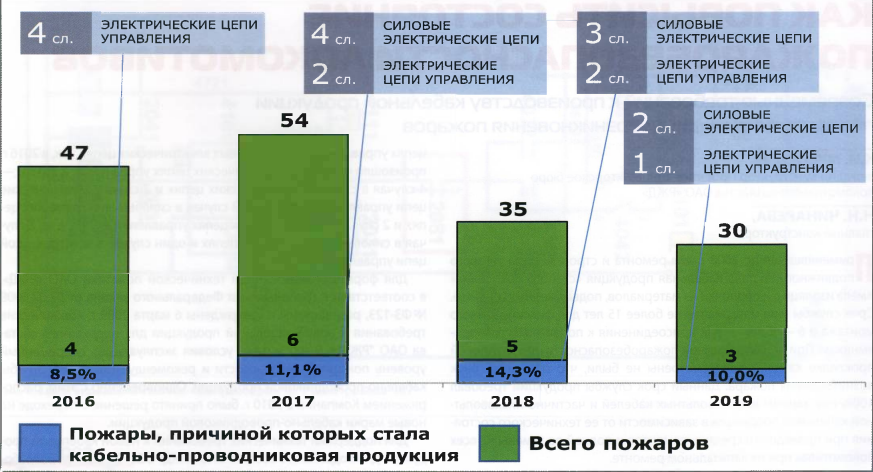