Файл: Контрольная работа Технология конструкционных материалов.rtf
ВУЗ: Не указан
Категория: Не указан
Дисциплина: Не указана
Добавлен: 06.11.2023
Просмотров: 46
Скачиваний: 1
ВНИМАНИЕ! Если данный файл нарушает Ваши авторские права, то обязательно сообщите нам.
Блюминг является двухвалковым реверсивным станом. На блюминге стальные слитки весом 5 - 15 т прокатываются на блумы (квадратные заготовки) сечением от 150х150 мм до 450х450 мм.
На слябинге слитки весом 7 - 25 т прокатываются на слябы (листовые заготовки) толщиной от 125 до 225 мм и длиной до 5000 мм. Средняя годовая производительность блюминга или слябинга около 1.5 млн. т.
Сортовые станы предназначены для прокатки сортовых и фасонных профилей. В соответствии с размерами проката сортовые станы делят крупносортовые, среднесортовые и мелкосортовые. У сортовых станов в отличие от блюминга не одна, а несколько рабочих клетей с валками.
В цехах холодной прокатки рулоны горячекатаной листовой стали сначала разматывают для травления (обычно серной кислотой), чтобы снять окалину. После холодной прокатки листы отжигают для устранения наклепа, затем дрессируют и разрезают. Дрессировкой называют операцию холодной прокатки с малыми (2-3%) обжатиями для правки и получения гладкой поверхности.
К числу специальных относят станы для прокатки бесшовных труб -трубопрокатные, станы для прокатки железнодорожных колес и бандажей, цепей и др.
Станы для производства сварных труб - трубосварочные станы представляют систему машин для формовки заготовки в трубу и последующей сварки (электродуговой или электроконтактной)[4].
. Сварка в углекислом газе. Свариваемые материалы. Способы Оборудование
Сущность способа состоит в следующем: голая электродная проволока диаметром 0,5-2 мм подается с постоянной скоростью в зону сварки. Одновременно в зону сварки поступает углекислый газ, который защищает переплавляемый электродный и основной металл от окружающего воздуха. Окислительное действие углекислого газа на расплавленный металл компенсируется повышенным содержанием в электродной проволоке элементов раскислителей (марганца, кремния и др.) [5].
Оборудование. Сварка плавящимся электродом в среде углекислого газа выполняется автоматами и полуавтоматами. Наибольшее распространение в промышленности нашли полуавтоматы. Полуавтомат А-537 показан на рис.
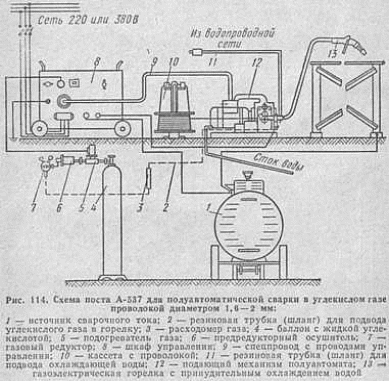
Рис. Схема поста А-537 для полуавтоматической сварки в углекислом газе поволокой диаметром 1,6-2мм: 1-источник сварочного тока; 2- резиновая трубка (шланг) для подвода углекислого газа в горелку; 3-расходомер газа; 4- баллон с жидкой углекислотой; 5-подогреватель газа; 6- предредукторный осушитель; 7-газовый редуктор; 8-шкаф управления; 9-спецпровод с проводами управления; 10-кассета с проволокой; 11-резиновая трубка (шланг) для подвода охлаждающей воды; 12-подающий механизм полуавтомата; 13-газоэлектрическая горелка с принудительным охлаждением водой.
Для сварки в среде углекислого газа применяют следующие источники постоянного тока:
-
преобразователи ПСО-ЗОО, ПС-500-3, ПС-500, ПСМ-1000, предназначенные для питания сварочной дуги при ручной дуговой сварке и сварке под флюсом; -
сварочные преобразователи ПСГ-350, ПСГ-500 и ПСУ-500, специально разработанные (с жёсткой вольт-ампер ной характеристикой) для сварки в защитных газах, в том числе в углекислом газе; -
генераторы, обычно используемые не для целей сварки, но характеристика которых позволяет использовать их для сварки в среде углекислого газа (зарядные агрегаты АЗД, ЗП и генераторы ГСР); -
выпрямители селеновые ВС-200, ВС-400, ВС-600, специально разработанные для автоматической и полуавтоматической сварки и в том числе для сварки в углекислом газе.
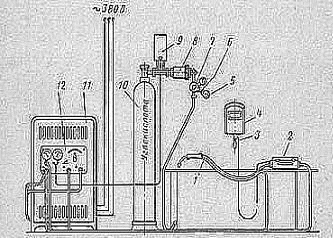
Рис. Схема поста А-547Р для полуавтоматической сварки в среде углекислого газа проволокой диаметром 0,8-1,0 мм; 1 - газоэлектрическая горелка; 2 - подающий механизм; 3 кнопка включения; 4 - щиток для защиты дуги; 5 - ацетиленовый манометр; 6 - переходный штуцер для установки ацетиленового манометра; 7 - редуктор кислородный; 8 - осушитель газа (на случай работы с неосушенной углекислотой); 9 подогревательгаза; 10 - баллон с жидкой углекислотой; 11 - источник сварочного тока (выпрямитель или генератор); 12 - пульт управления
Для сварки тонкого металла применяют полуавтомат А-547Р, предназначенный для сварки металла толщиной до 3 мм и угловых соединений при катетах шва до 4 мм. Сварку можно выполнить во всех пространственных положениях электродной проволокой диаметром 0,8-1,0 мм постоянным током обратной полярности. Общий вид полуавтомата А-547Р показан на рис.
Институтом электросварки имени Е. О. Патона и ЦНИИТМАШем к полуавтоматическим постам газоэлектрической сварки спроектированы рукава для одновременной подачи тока 500-600 А и охлаждающей воды и рукава обычного исполнения (без принудительного охлаждения) для силы тока до 300 А. Газоэлектрические горелки для автоматической и полуавтоматической сварки в среде углекислого газа показаны на рис. 3 и 4.
Автоматическую сварку в углекислом газе можно выполнять специальными автоматами, а также сварочными тракторами ТС-17М, АДС-1000-2 после комплектования их специальными приставками (конструкции приставок разработаны в Институте электросварки и в ЦНИИТ- МАШе).
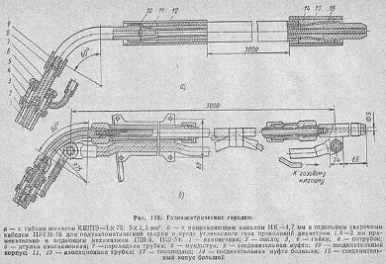
Рис. Газоэлектрические горелки: а-с гибким шлангом КШПЭ-1х75; 3х1,5 мм2; б- с направляющим концом НК-4,7 мм и отдельным сварочным кабелем ПРГН-70 для полуавтоматической сварки в среде углекислого газа проволокой диаметром 1,5-2 мм применительно к падающим механизмам ПШ-5, ПШ-54; 1 - наконечние; 2 - сопло; 3,6 - гайка; 4 - патрубок; 5 -втулка изоляционная;7 - переходная трубка; 8 - мундштук; 9 - соединительная муфта; 10 - соединительный корпус; 11, 13 - изоляционная трубка; 12 - токоподвод; 14 - соединительная муфта большая; 15 - сединительный конус большой
Горелки для полуавтоматической и автоматической сварки разделяют на горелки для сварки на малых силах тока (250-300 А) без водяного охлаждения и горелки для сварки на больших силах тока.
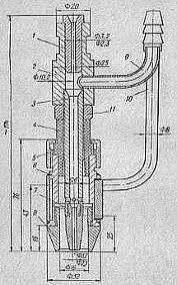
Рис. Газоэлектрическая горелка для авоматической сварки в среде углекислого газа с принудительным водяным охлаждением: 1 - вставка стальная сменная; 2 - втулка бронзовая; 3 - трубка токоподводящая; 4 - втулка изоляционная; 5 - гайка накидная; 6 - корпус горелки; 7 - мундштук токоподводящий; 8 - сопло; 9 - трубка для подвода защитного газа; 10 - трубка для подвода охлаждающей воды в горелку; 11 - гайка специальная
Материалы. Углекислый газ или углекислота (С02) - бесцветный газ с едва ощутимым запахом; при растворении в воде придает ей слабый кисловатый вкус. При 0° С и давлении 760 мм рт. ст. плотность 1,97686 г/л, плотность по отношению к воздуху 1,524. Жидкую углекислоту транспортируют в стальных баллонах или специальных контейнерах. Обычно в стандартный баллон емкостью 40 л заливают 25 кг углекислоты, образующей при испарении 12,725 м3 газа. Для сварки используют сварочную углекислоту 1 и 2-го сорта и в силу необходимости (с условием осушения) пищевую углекислоту по ГОСТ 8050-64.
Электродная проволока для сварки в среде защитных газов плавящимся электродом обеспечивает необходимый состав металла шва только при повышенном содержании в ней. элементов раскислителей. Для получения качественных швов при сварке в углекислом газе углеродистых и некоторых низколегированных и легированных сталей применяют проволоку, регламентированную по ГОСТ 2246-70. Сварочную проволоку непосредственно перед использованием тщательно очищают до металлического блеска.
. Обработка на шлифовальных станках. Характеристика и маркировка шлифовальных кругов. Выбор шлифовальных кругов. Классификация шлифовальных станков
Шлифование - один из прогрессивных методов обработки металлов резанием. При шлифовании припуск на обработку срезают абразивными инструментами - шлифовальными кругами. Шлифовальный круг представляет собой пористое тело, состоящее из большого числа абразивных зерен, скрепленных между собой связкой. Между зернами круга и связкой расположены поры. Материалы высокой твердости, из которых образованы зерна шлифовального круга, называют абразивными.
Шлифование состоит в том, что шлифовальный круг, вращаясь вокруг своей оси, снимает тонкий слой металла (стружку) вершинами абразивных зерен, расположенных на режущих поверхностях шлифовального круга (периферия круга).
Число абразивных зерен, расположенных на периферии круга, очень велико; у кругов средних размеров оно достигает десятков и сотен тысяч штук. Таким образом, при шлифовании стружка снимается огромным числом беспорядочно расположенных режущих зерен неправильной формы, что приводит к очень сильному измельчению стружки и большому расходу энергии.
Режущая поверхность шлифовального круга состоит из множества абразивных зерен, расположенных на его поверхности на некотором расстоянии друг от друга и выступающих на различную высоту. Этим объясняется то, что не все абразивные зерна работают одинаково.
Абразивное зерно, вращаясь с очень большой скоростью (90 м/с и более), срезает металл с поверхности заготовки, следовательно шлифование необходимо рассматривать как сверхскоростное резание (царапанье) поверхностных слоев заготовки большим числом мельчайших шлифующих зерен (резцов), соединенных в круге с помощью связки. Полученная таким образом шлифованная поверхность представляет собой совокупность шлифовочных рисок, оставляемых вершинами абразивных зерен круга. Образование каждой шлифовочной риски происходит в результате последовательного внедрения режущей кромки зерна в обрабатываемую поверхнос ть.
Детали современных машин представляют собой сочетание плоских и круговых цилиндрических, конических наружных и внутренних поверхностей. Другие поверхности встречаются редко. В соответствии с формами деталей машин наиболее распространены схемы шлифования, приведенные на рис.
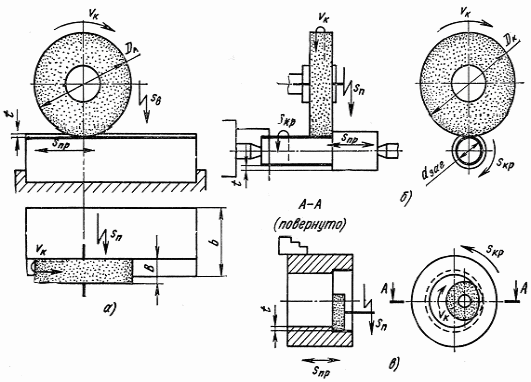
Рис. Основные схемы шлифования: а - плоское; б - круглое; в - внутреннее
Для всех технологических способов шлифовальной обработки главным движением резания Vк (в м/с) является вращение круга.
При плоском шлифовании возвратно-поступательное перемещение заготовки является продольной подачей Sпр (в м/мин). Для обработки поверхности на всю ширину b заготовка или круг должны перемешаться с поперечной подачей Sп (в мм/дв. ход). Это движение происходит прерывисто (периодически) при крайних положениях заготовки в конце продольного хода. Периодически производится и подача Sв (в мм) на глубину резания, которая осуществляется также в крайних положениях заготовки, но в конце поперечного хода.
При круглом шлифовании продольная подача происходит за счет возвратно-поступательного движения заготовки. Подача Sпр (в мм/об) соответствует осевому перемещению заготовки за один ее оборот. Вращение заготовки является круговой подачей Sкр(в м/мин)
Sкр = π · Dзаг · nзаг/1000
где nзаг - частота вращения заготовки, об/мин;заг - диаметр заготовки, мм.
Подачу Sп (в мм/дв.ход, мм/ход) на глубину резания для приведенной схемы обработки производят при крайних положениях заготовки.
Движения, осуществляемые при внутреннем шлифовании (рис. 1. в).
Некоторые трудности вызывает шлифование отверстий малого диаметра. Для обеспечения необходимой скорости резания шлифовальный круг имеет частоту вращения, доходящую до десятков и сотен тысяч в минуту. Шлифование на более низких скоростях не обеспечивает необходимого качества обработки и снижает стойкость кругов.
Характеристика и маркировка шлифовальных кругов
Шлифовальные круги характеризуются геометрической формой (типом), видом абразивного материала, его зернистостью, типом связки, твердостью.
Для производства зёрен шлифовальных кругов используют:
- традиционные абразивы - электрокорунд и карбид кремния;
сверхтвёрдые материалы - алмаз и кубический нитрид бора (эльбор).
Твёрдость круга характеризует способность связки удерживать абразивные зёрна от вырывания их с рабочей поверхности круга в процессе шлифования под действием силы резания. По степени твёрдости различают круги: мягкие (М1, М2, М3); среднемягкие (СМ1, СМ2); средние (С1, С2); среднетвёрдые (СТ1, СТ2, СТ3); твёрдые (Т1, Т2); весьма твёрдые (ВТ1, ВТ2) и чрезвычайно твёрдые (ЧТ1, ЧТ2) [8].
Полная маркировка шлифовальных кругов содержит:
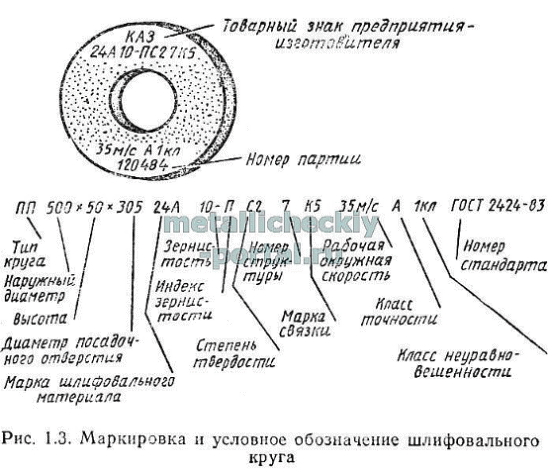
Выбор шлифовальных кругов.
При выборе шлифовального круга такие характеристики как степень твердости или структура могут оказаться более значимыми, чем вид абразива.
Твёрдость круга выбирают в зависимости от свойств обрабатываемого материала, припуска на обработку и жёсткости шпиндельного узла станка. При назначении твёрдости учитывают следующее основное правило: чем твёрже обрабатываемый материал, тем мягче должен быть круг. Это правило не распространяется на весьма мягкие и вязкие материалы и сплавы (алюминий, медь, свинец, латунь и др.). Их лучше обрабатывать мягкими кругами (М1, М2, М3). Рекомендации по выбору твёрдости круга для основных видов шлифовальных работ приведены в таблице 1.