Файл: Курсовой проект Введение 4 1 Назначение, типы, устройство и условия работы токоприемников.docx
ВУЗ: Не указан
Категория: Не указан
Дисциплина: Не указана
Добавлен: 06.11.2023
Просмотров: 428
Скачиваний: 6
ВНИМАНИЕ! Если данный файл нарушает Ваши авторские права, то обязательно сообщите нам.
ТО-3 Провести работы в объеме ТО-2. Проверить на слух утечки сжатого воздуха по пневмомагистрали, а также по фланцам пневмоцилиндра. Утечки устранить подтяжкой резьбовых соединений. При одностороннем износе угольных вставок допускается переворачивание полоза. Детали токоприемника с трещинами или изломами восстановить или заменить. Изношенные более чем на 1 мм оси крепления полоза к кареткам заменить.
Проверить состояние шплинтов. При необходимости отрегулировать статичекую характеристику токоприемника и верхнего узла. В зимний период времени в условиях повышенного льдообразования наружные поверхности подвижной рамы, нижнего рычага, пружинного привода и боковых поверхностей полоза обработать смазкой ЦНИИ КЗ ТУ 32 ЦТ 896-82. После проведения работ проверить подъем-опускание токоприемника
ТР-1 Провести работы в объеме ТО-2, ТО-3.. Проверить состояние шунтов. Шунты, имеющие обрыв жил более 15% сечения заменить. Проверить состояние тяг, пружин, тросов, кареток, полоза, привода токоприемника. Трубы рам с вмятинами глубиной более 5 мм, трещинами и прожогами восстановить или заменить. Полозы, имеющие трещины каркасов, погнутость восстановить или заменить. После проведения работ проверить подъем-опускание токоприемника.
ТР-2 провести работы в объеме ТР-1. Проверить состояние чехла пневмопривода, при необходимости заменить. Проверить состояние резиновых буферов гасителей, тросов пружинного привода, при необходимости заменить. Визуально проверить состояние шарнирных узлов синхротяги.
3 Технология проведения текущего ремонта токоприемника по циклу ТР-3
Технологический процесс - является главной составной частью производственного процесса. Под технологическим процессом понимается определенная последовательность операций, предусматривающая изменение размеров, вида, формы, состояния или взаимного расположения и соединения предметов труда с целью получения готовой продукции.
Токоприемники снимаются с электровоза и направляются на участок ремонта электроаппаратуры. Ремонт токоприемников производится в соответствии с технологической инструкцией по техническому обслуживанию и текущему ремонту токоприемников отечественных электровозов постоянного и переменного тока.
Токоприемник устанавливается на опорные тумбы, разбираются его узлы и детали и производится их осмотр. Сварные швы, имеющие трещины, срубаются и накладываются вновь. Обнаруженные вогнутости основания токоприемника выправляются. Расстояние между центрами отверстий под болты опорных изоляторов должно соответствовать чертежным размерам. Разница расстояний между отверстиями по диагонали допускается не более 3 мм.
Проверяется крепление соединительных труб и угольников основания. Поврежденные места присоединения наконечников проводов зачищаются и подвергаются лужению.
Главные валы токоприемников осматриваются. Производится ревизия шариковых подшипников. Негодные подшипники заменяются.
Проверяется состояние деталей рычажно-пружинного механизма. Неисправные пружины и шарнирные подшипники в узле соединения их с главным валом заменяются. Погнутые синхронизирующие тяги выправляются.
Пневматический привод токоприемника разбирается на специализированном месте, ему производится ревизия.
Разбираются каретки, проверяется состояние их деталей, поврежденные детали ремонтируются или заменяются. Ход каретки должен соответствовать нормам допусков и износов.
Трубы верхних рам, имеющие трещины, вмятины, глубиной более 3 мм, изгибы и прожоги, сквозные повреждения коррозией, а также составные трубы с муфтами, заменяются новыми.
Трубы нижних рам цилиндрические или конусные, имеющие трещины, вмятины глубиной более 3 мм на длине более 150 мм более чем в двух местах, изгибы и прожоги, сквозные повреждения коррозией, заменяются.
Разрешается заваривать газовой сваркой трещины в конусных трубах нижних рам токоприемников П-1У, Т-5, оставлять конусные трубы, сваренные из двух половин.
Полоз разбирается и ремонтируется. Каркас полоза проверяется по шаблону, погнутый каркас выправляется на специальной оправке. Каркас полоза, имеющий толщину стенок менее 1,3 мм, заменяется новым. Разрешается заваривать трещины и отверстия в полозе под винты, а также в угловых вырезах отбортовки склонов для получения соответствующей конфигурации и длины полоза.
Угол наклона концов полоза должен соответствовать требованиям утвержденных чертежей. Антикоррозионное покрытие должно соответствовать требованиям чертежей.
На полоз устанавливается комплект новых угольных вставок и подгоняется в соответствии с требованиями чертежей.
Проверяется состояние амортизаторов токоприемника, негодные резиновые и другие детали заменяются.
Токоприемник собирается, предварительно смазываются все шарнирные и трущиеся соединения. По окончанию сборки токоприемника проверяется:
- максимальная высота подъема токоприемника;
- смещение центра полоза относительно центра основания токоприемника поперек его оси;
- отклонение верхней поверхности полоза от горизонтали;
- разница в длине подъемных пружин на отрегулированном токоприемнике в опущенном положении, которая должна быть для всех типов токоприемников, кроме Т-5М, не более 6 мм;
- угол поворота полоза вокруг оси его крепления, который должен быть 5 - 7 в каждую сторону относительно среднего положения;
- отклонение контактных поверхностей обоих полозов двухполозных токоприемников относительно друг друга, которое должно быть не более 2 мм;
- активное и пассивное статическое нажатие токоприемника на контактный провод в диапазоне рабочей высоты;
- разница между наибольшим и наименьшим нажатием полоза при одностороннем его движении в рабочем диапазоне;
- разница между пассивным и активным нажатием в любой точке при подъеме и опускании в диапазоне рабочей высоты;
- время подъема и опускания токоприемника.
Указанные параметры должны соответствовать нормам допусков.
Все трубчатые рамы и основание токоприемника, за исключением электрических и шарнирных соединений, шунтов, силуминовых рычагов и полозов, полиэтиленовых рукавов, резиновых буферов, окрашиваются.
Опорные изоляторы под один токоприемник должны подбираться с разницей по высоте не более 2 мм. Для устранения перекоса токоприемника разрешается установка шайб между токоприемником и опорными изоляторами.
Воздушные полиэтиленовые рукава снимаются для ревизии, промываются теплой водой с мылом. Удаляется влага из рукава путем продувки сжатым воздухом. Поверхность рукава должна быть гладкой, не иметь трещин, надрывов и вмятин. Бурты, имеющие трещины, толщину менее 4 мм и вмятины, обрезаются и вновь формуются. При этом уменьшение длины рукава не должно быть более чем на 50 мм от чертежного размера. После ремонта рукав испытывается давлением сжатого воздуха 700 кПа (7кгс/см2) и на электрическую прочность изоляции напряжением 60 кВ переменного тока, частотой 50 Гц в течение 1 мин. На испытанный рукав наносится дата, место и параметры испытаний.
4 Основные неисправности, контрольные параметры виды послеремонтных испытании ТКП
Из всех аппаратов электровоза токоприемники работают в наиболее сложных условиях. Они воспринимают разнообразные динамические нагрузки, подвергаются сильному действию электрического тока, в зимнее время их работоспособности отрицательно сказывается низкая температура, снегопад, гололед. Конструкция токоприемника отражает противоречивые требования: легкость и прочность, большую подвижность и необходимость сохранения постоянного контакта между полозом и контактным проводом. На электровозах постоянного тока установлены токоприемники тяжелого типа. По сравнению с токоприемниками электровозов переменного тока и электропоездов они воспринимают значительно большие токи (до 2000 А при продолжительном режиме) и имеют самое большое статическое нажатие.
Из всех повреждений аппаратов электровозов, имевших своим следствием порчи или неплановый ремонт, на долю токоприемников приходится 10-20%. Неисправности приемников приводят к повышенному износу контактного провода, его пережогу, повреждениям воздушных стрелок, фиксаторов и изоляторов контактной сети. Перед разборкой осматривают все узлы и детали и проверяют статическую характеристику, время подъема и опускания при нормальном давлении воздуха в пневматическом приводе. Обнаруженные при этом дефекты определяют в первом приближении характер последующего ремонта и степень разборки агрегатов.
Неисправность верхнего узла токоприёмника и контактной системы, прежде всего кареток, приводят к резкому перекосу полоза и повреждению контактной сети. Осматривая детали кареток, убеждаются в отсутствии изломов, искривлений, трещин и чрезмерной выработки. Трещины в кронштейнах и держателях кареток токоприёмников электровозов обычно возникают в местах концентрации напряжении на резких переходах, в верхнем узле нередко наблюдаются износ стенок стакана, продавливание дна, излом шпильки и трещины в местах приварки проушины под полоз.
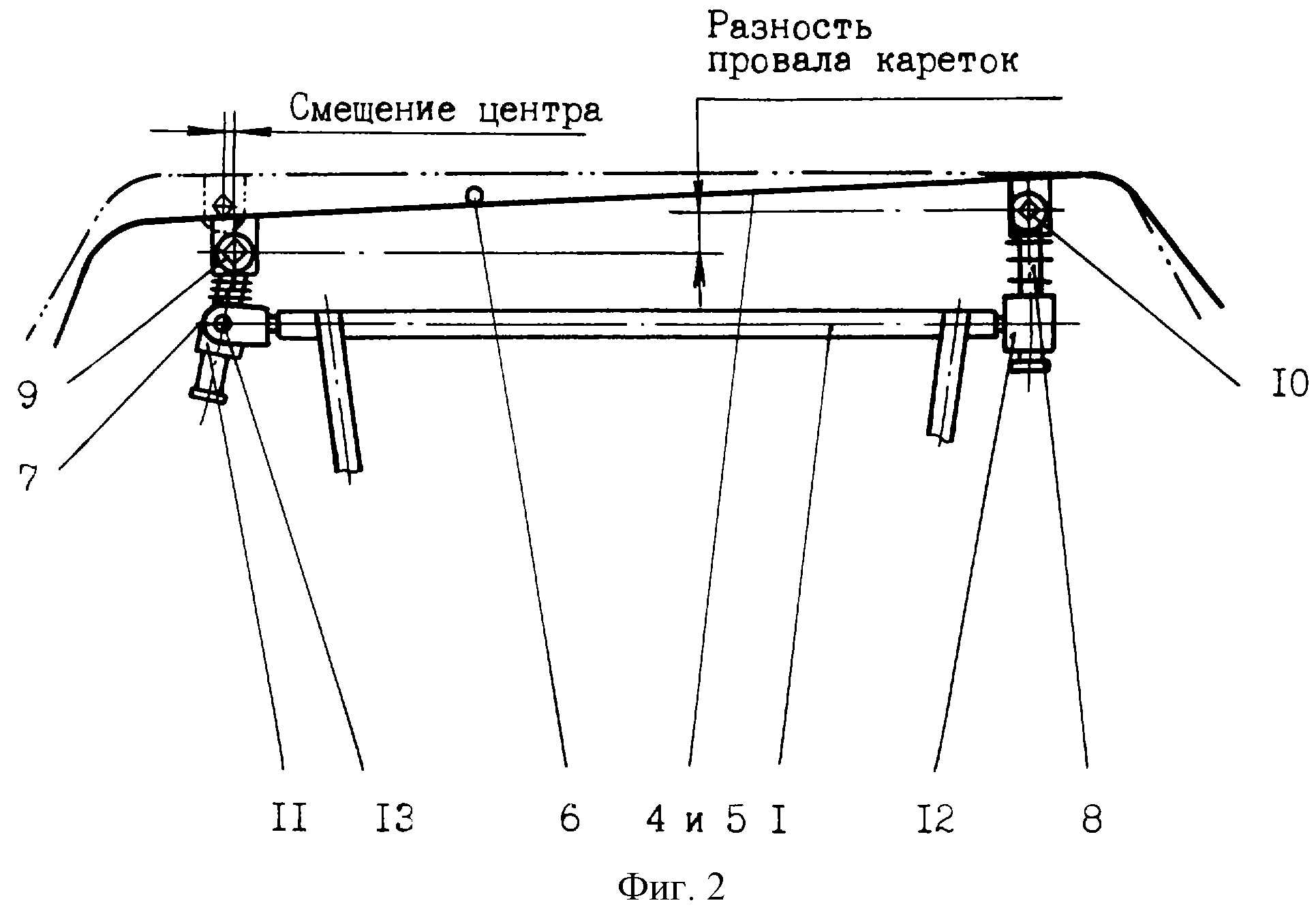
Рисунок 10 Неисправность кареток токоприемника
При размещении контактного провода 6 по средине полозов 4 и 5 провал (ход) штоков 7 и 8 кареток от контактного нажатия будет одинаков и вероятность заклинивания штоков 7 и 8 исключена. При размещении контактного провода 6 ближе к одной из кареток, например 2, большая часть контактного нажатия будет приходиться на штоки 7 (рисунок 10). При этом штоки 7 и 8 просядут на разную величину. Разность провала штоков 7 и 8 кареток 11 и 12 могла бы привести к тому, что появилось относительное смещение центров шарниров полозов и осей 13 направляющих обойм кареток, однако заклинивания штоков 7 и 8 в обоймах 11 и 12 не произойдет, шарнир полозов уведет ось штоков 7 на себя за счет поворота обойм 11 на оси 13, исключая разницу смещений и возможность заклинивания.
Испытания после ремонта проверяют статическую характеристику - нажатие полоза на контактный провод в пределах рабочей высоты при поднятии и опускании токоприёмника. При этом испытании токоприёмник соединяют с воздушной магистралью и поднимают. Затем, зацепив за распорки верхних рам динамометр, плавно, без рывков, опускают токоприёмник, контролируя показания динамометра через 100 - 150 мм. После чего, сдерживая, позволяют ему так же плавно, без ускорения, подняться до предельной высоты, продолжая следить за показаниями динамометра. Испытания редукционного клапана, о чёткости работы которого судят по времени и характеру подъёма и опускания токоприёмника. Включение производят с пульта управления.
Плавный подъём должен несколько замедляться в зоне подхода к контактному проводу, чтобы избежать удара о контактный провод. При включении, быстро начав опускаться, пантограф должен плавно замедлить движение при подходе к упорам и без ударов садиться на амортизаторы. Время подъема и опускания пантографа проверяют хронометром.
Время подъема и опускания токоприемника и его правильная работа во многом зависят от регулировки и исправности редукционного клапана. Определяют время подъема полоза токоприемника, произведя отсчет с момента начала движения полоза от сложенного положения до подъема его на наибольшую рабочую высоту при номинальном давлении сжатого воздуха 0,5 МПа (5 кгс/кв. см). Определяют время опускания.
Время подъема полоза должно быть от 7 до 10 с, время опускания - от 3,5 до 6,0 с.
Угольные вставки (рисунок 11) изготовляют из угольно-графитовых обожженных композиций. Срок службы угольных вставок превосходит срок службы медных накладок. Однако угольные вставки имеют относительно высокое удельное сопротивление. Это вызывает увеличение потерь энергии в контакте и повышает опасность пережога контактного провода при коротких замыканиях на МВПС во время стоянки, когда происходит местный нагрев провода.
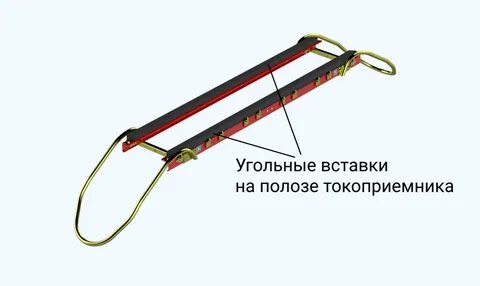
Рисунок 11 Угольные вставки на ТКП
При сдаче отрегулированного токоприемника мастеру или приемщику локомотивов еще раз проверяют соответствие его геометрических размеров установленным нормам. Убеждаются в отсутствии утечек воздуха при максимальном рабочем давлении 675 кПа (6,75 кгс/см2) и четкой работе аппарата при минимальном давлении 375 кПа (3,75 кгс/см2).
При ремонте токоприёмника используются следующие материалы и инструмент: регулируемые тумбы; моечная корзина; газовая горелка; ограничители размеров (втулки, валики, прокладки из красной меди); шлифовальный станок; пресс-форма; шаблон; уровень, опущенный на линейку; графитовая смазка СГС-0; молоток; зубила; гаечные ключи.