ВУЗ: Не указан
Категория: Не указан
Дисциплина: Не указана
Добавлен: 07.11.2023
Просмотров: 57
Скачиваний: 1
ВНИМАНИЕ! Если данный файл нарушает Ваши авторские права, то обязательно сообщите нам.
АНАЛИЗ ФОРМ И ПОСЛЕДСТВИЙ ОТКАЗОВ
(FMEA-МЕТОДОЛОГИЯ)
Анализ форм и последствий отказов (Failure Mode and Effect Analysis, FMEA-методология), известный также под названием «Анализ рисков», используется в качестве одной из ревентивных мер для системного обнаружения причин, вероятных последствий, а также для планирования возможных противодействий по отношению к отслеживаемым отказам. FMEA-методология обычно применяется в работе межфункциональных команд для анализа форм и последствий отказов продукции и процессов, однако имеются примеры успешного применения этой методологии и в кружках качества.
В настоящее время в международных стандартах ИСО серии 9000 уделяется очень большое внимание этим процессам.
При анализе форм и последствий отказов процессов главным является заблаговременный поиск, для каждого этапа процесса, ответов на следующие вопросы:
-
Каким образом при осуществлении процесса может произойти отказ или неудача? -
Что может быть причиной этой неудачи? -
Что произойдет, если при осуществлении процесса случится неудача? -
Как мы можем предотвратить последствия отказа?
ПРИМЕНЕНИЕ FMEA-МЕТОДОЛОГИИ
Методологию «Анализ форм и последствий отказов» применяют для системной идентификации возможных отказов процессов и для предотвращения их последствий. В результате использования FMEA-методологии появляется список критических пунктов, а также инструкции (предписания) о том, что должно быть сделано, чтобы минимизировать последствия в случае отказа в ходе осуществления процесса.
Применение FMEA-методологии основано на следующих принципах:
Командная работа. Реализация FMEA-методологии осуществляется силами специально подобранной межфункциональной команды специалистов.
Иерархичность. Для сложных технических объектов или процессов их изготовления анализу подвергается как объект или процесс в целом,
так и их составляющие; отказы составляющих рассматриваются по их влиянию на объект (или процесс), в которые они входят.
Итеративность. Анализ повторяют при любых изменениях объекта или требований к нему, которые могут привести к изменению комплексного риска отказа.
РегистрациярезультатовпроведенияFMEA. В соответствующих отчетных документах должны быть зафиксированы результаты проведенного анализа и решения о необходимых изменениях и действиях.
Осуществление FMEA-методологии обычно производится в рамках работы в составе межфункциональной команды. Руководитель (председатель) команды ответственен за следующее:
-
формирование команды; -
сбор релевантной (важной, уместной) информации; -
планирование и организацию заседаний FMEA-команды; -
руководство всесторонним исследованием проблемы; -
регистрацию результатов; -
обеспечение обратной связи относительно исправления или возможного предотвращения отказов.
Для идентификации как можно большего числа проблем FMEA- команда должна представлять собой междисциплинарную и разноплановую композицию из специалистов, имеющих обширный опыт в различных областях знаний.
Продолжительность каждого непрерывного заседания FMEA- команды должна быть в пределах 1,5 часов и выбираться в зависимости от формулировки проблемы, знаний и опыта членов команды, степени их готовности к заседанию.
ЭТАПЫ ОСУЩЕСТВЛЕНИЯ FMEA-МЕТОДОЛОГИИ
Анализ форм и последствий отказов обычно предполагает осуществление трех крупных этапов работы.
-
ПодготовкакработеFMEA-команды
При подготовке к работе и в начале плановых заседаний руководитель FMEA-команды должен выполнить следующее.
Сформировать межфункциональную и квалифицированную команду, состоящую из 5 – 9 специалистов.
Заранее провести короткое предварительное совещание, на котором объяснить членам команды:
-
цели предстоящего заседания; -
основные идеи и подходы к FMEA-анализу; -
основные роли членов FMEA-команды.
Предоставить членам FMEA-команды необходимую информацию, которая должна быть ими заранее тщательно изучена.
Сообщить членам FMEA-команды сведения об основных этапах процесса, который будет исследоваться на предстоящем заседании.
-
ОсновнаяработаFMEA-команды
Во время основных заседаний, на которых будут заполняться FMEA-формы, руководитель команды должен обеспечить выполнение следующего.
Для каждого этапа исследуемого процесса следует определить возможные режимы отказов в работе. В результате этого удается предугадать возможные отказы в протекании процесса и связь этих отказов с другими этапами процесса.
Кратко обозначьте, что является причиной каждого режима отказа. Определите и опишите последствия (влияние) этих режимов отказов на управляемость процесса.
Количественно оцените слабые пункты (узкие места) процесса, определив следующие факторы: значимость потенциального отказа (S), вероятность возникновения дефекта (O), вероятность обнаружения отказа (D). В таблице 3.1 приведены сведения о том, как указанные факторы могут быть количественно оценены. Произведение этих трех факторов представляет собой приоритетное число риска (ПЧР), т.е. количественную оценку отказа с точки зрения его значимости по последствиям, вероятности возникновения и вероятности обнаружения
ПЧР = S O D.
Для отказов (несоответствий, дефектов, пороков), имеющих несколько причин, определяют соответственно несколько ПЧР. Каждое ПЧР может иметь значения от 1 до 1000. Для приоритетного числа риска должна быть заранее установлена критическая граница (ПЧРгр), например, в пределах от 100 до 125. Если какие-то значения ПЧР превышают установленное значение ПЧРгр, значит, именно для них следует вести доработку производственного процесса.
Определите для каждого режима отказа те средства и действия, которые необходимы для преодоления слабых (узких) мест исследуемого процесса.
Поручите ответственному специалисту или группе специалистов заняться выработкой технических решений, которые позволят предотвратить последствия отказов для наиболее рискованных ситуаций.
-
Квалиметрические шкалы: значимости потенциального отказа (S), вероятности возникновения дефекта (O),
вероятности обнаружения дефекта (D)
Фактор S | Фактор O | Фактор D |
(опасность для людей) | 1 – очень низкая; 2 – низкая; 3 – не очень низкая; 4 – ниже средней; 5 – средняя;
к высокой; 8 – высокая; 9 – очень высокая; 10 – 100%-ная |
|
Установите промежуток времени, через который должна производиться периодическая верификация (контроль, проверка, подтверждение) выработанного решения.
-
ДействияпослезавершенияработыFMEA-команды
После завершения работы FMEA-команды должно быть выполнено следующее.
Составлен письменный отчет о результатах работы по выполненному анализу форм и последствий отказов. Этот отчет должен быть передан руководителям организации.
Руководителям организации следует верифицировать и оценить результаты
работы FMEA-команды и проследить, чтобы до членов
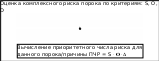





Образование FMEA-команды Выбор ведущего
Ознакомление с предложенными проектами технического процесса
Выбор «наихудшего» последствия с максимальным баллом S |
|
Оценка для данной причины баллов O и D |

Составление окончательного протокола по результатам работы FMEA-команды и его подписание

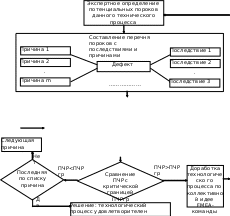
ПРИМЕР ПРОВЕДЕНИЯ АНАЛИЗА ФОРМ И ПОСЛЕДСТВИЙ ОТКАЗОВ
Рассмотрим пример практического применения FMEA- методологии для улучшения процесса градуировки электронных весов, который по результатам анализа деятельности завода, был определен высшим руководством как критический (дефектоносный).
Процесс градуировки весов осуществляется с использованием имеющегося на предприятии универсального стенда нагружения, который состоит из основного и подвижного каркасов. Последний оснащен левой и правой гребенками, на которые навешиваются гири в необходимой последовательности.
Алгоритм процесса градуировки весов представлен на рис. 3.8 и заключается в следующем. После транспортировки весов с предыдущего участка производства их помещают на столешницу стенда и по уровню устанавливают в горизонтальное положение. Затем посредством нажатия соответствующей клавиши на клавиатуре весы переводят в режим градуировки и при этом на табло жидкокристаллического индикатора (ЖКИ) выводится значение веса, которым необходимо нагрузить платформу весов.