Файл: Отчет о прохождении третьей производственной (технологической) практики в условиях открытой разработки Наталкинского золоторудного месторождения.docx
Добавлен: 07.11.2023
Просмотров: 539
Скачиваний: 21
ВНИМАНИЕ! Если данный файл нарушает Ваши авторские права, то обязательно сообщите нам.
Отчет
о прохождении третьей производственной (технологической) практики
в условиях открытой разработки Наталкинского золоторудного месторождения
Магаданской области
СОДЕРЖАНИЕ
Введение………………………………………………………………………………………... | ..3 |
1 Общие сведения о предприятии………………………………………………………....... | ..4 |
2 Характеристика месторождения……………………………………………………………. | ..5 |
2.1 Запасы месторождения…………………………………………………………………... | ..5 |
2.2 Характеристика пород вскрыши и полезного ископаемого…………………………... | ..6 |
2.3 Гидрогеологические условия…………………………………………………………..... | ..8 |
3 Характеристика земельного и горного отвода …………………………………………….. | ..9 |
4 Особенности технологического процесса………………………………………………….. | 11 |
4.1 Подготовка пород к выемке…………………………………………………………….. | 11 |
4.2 Выемочно-погрузочные работы………………………………………………………… | 17 |
4.3 Перемещение карьерных грузов………………………………………………………... | 19 |
4.4 Отвалообразование………………………………………………………………………. | 21 |
4.5 Рекультивационные работы……………………………………………………………... | 23 |
5 Способ вскрытия месторождения ………………………………………………………….. | 25 |
6 Система разработки месторождения ………………………………………………………. | 27 |
7 Переработка полезного ископаемого………………………………………………………. | 29 |
8 Рациональное использование минерального сырья……………………………………….. | 32 |
9 Безопасность ведения горных и взрывных работ………………………………………….. | 35 |
10 Опытно-промышленные испытания оборудования и технологий……………………... | 42 |
11 Экономическая часть ……………………………………………………………………… | 43 |
Заключение…………………………………………………………………………………….. | 45 |
Список использованных источников………………………………………………………… | 46 |
Приложение 1………………………………………………………………………………….. | 47 |
Приложение 2………………………………………………………………………………….. | 48 |
Приложение 3………………………………………………………………………………….. | 49 |
Приложение 4………………………………………………………………………………….. | 50 |
Приложение 5………………………………………………………………………………….. | 51 |
Приложение 6………………………………………………………………………………….. | 52 |
| |
| |
| |
ВВЕДЕНИЕ
Третья производственная (технологическая) практика была пройдена на золоторудном месторождении «Наталка», разрабатываемым открытым способом компанией АО «Полюс Магадан».
Производственная практика является необходимым этапом формирования у обучающихся требуемых компетенций.
Целью прохождения практики являлось закрепление и расширение теоретических знаний, полученных в процессе обучения, приобретение практических знаний и навыков работы по специальности, изучение организации производства, методов и средств обеспечения безопасности технологических процессов, анализ технико-экономических показателей работы горного предприятия.
Задачами практики являлись следующие:
- ознакомление с предприятием, изучение нормативной и технической документации;
-
изучение горнотехнических сведений о районе месторождения; -
ознакомление с основными технологическими процессами добычи полезного ископаемого открытым способом: буровых, выемочно-погрузочных, транспортных и отвальных работ; -
технология и безопасность проведения взрывных работ; -
рассмотрение способа вскрытия, систем разработки месторождения и рекультивационных работ; -
изучение технологической схемы переработки добываемого полезного ископаемого; -
ознакомление с мероприятиями по охране окружающей среды; -
ознакомление с производственно-финансовой деятельностью предприятия; -
изучение методов и форм организации управления охраной труда и промышленной безопасностью; -
сбор, обработка, анализ и систематизация информации о предприятии, необходимой для составления отчета;
По результатам практического обучения представлен настоящий отчет.
1 Общие сведения о предприятии
Золоторудное месторождение «Наталка», входящее в состав Омчакского золоторудного узла, расположено в бассейне реки Омчак – левого притока реки Тенька, являющейся правым притоком реки Колыма.
Месторождение разрабатывается открытым способом Наталкинским горно-обогатительным комбинатом.
По административному делению месторождение относится к Тенькинскому району Магаданской области Российской Федерации, административным центром которого является пос. Усть-Омчуг.
Базовый поселок рудника находится в Тенькинском районе Магаданской области в 130 км к северо-западу от районного центра п. Усть-Омчуг. Расстояние до г. Магадан составляет 395 км.
Лицензией (МАГ 04859 БЭ от 11.07.2018 г.) на освоение месторождения «Наталка» с целью добычи рудного золота, владеет компания «Акционерное общество «Полюс Магадан», входящее в Группу «Полюс».
Юридический адрес АО «Полюс Магадан»:
686070, Магаданская область, Тенькинский район, поселок Омчак, Новая улица, здание 35 корпус 7, помещение 121.
Руководитель компании: генеральный директор Колдунов Григорий Анатольевич
Телефон(ы): +7 (41344) 2-25-72, +7 (41344) 4-13-44.
E-mail (эл.почта): oaorim@polyusgold.com
Сайт: http://polyusgold.com
В двух километрах к востоку от поселка проходит автотрасса III-го класса Магадан-Якутск. Транспортировка грузов и персонала осуществляется круглый год. Район экономически освоен; ведется добыча золота из россыпей и небольших коренных месторождений. В 250 км от рудника имеется угольное месторождение, на базе которого работает Аркагалинская ГРЭС. Энергоснабжение рудника осуществляется через подстанцию Омчак, соединенную с ГРЭС ЛЭП 110 кВ.
2 Характеристика месторождения
2.1 Запасы месторождения
Руды месторождения «Наталка» относятся к одному технологическому типу – к типу бедных тонко вкрапленных золотокварцевых убого сульфидных углисто-мышьяковых руд.
Единственным ценным компонентом, имеющим промышленное значение, является золото. Попутным полезным компонентом является серебро. В рудных телах месторождения запасы серебра самостоятельного промышленного значения не имеют, что предопределяет его извлечение только попутно из золота лигатурного при аффинаже. Серебро является попутным компонентом 3-го класса. Подсчет запасов серебра проведен путем применения к запасам золота коэффициента 0,2796, установленного при аффинаже золота лигатурного.
По состоянию на 31 декабря 2014 года запасы по классификации JORC составили 319 млн. тонн руды (содержание золота 1,6 г/т) и 16,2 млн. унций золота. Ресурсы месторождения были оценены в 777 млн. т руды (содержание золота 1,5 г/т) и 36,8 млн. унций золота.
Балансовые запасы золота составляют 1500,8 тонн при среднем содержании 1,7 г/т, в том числе запасы по категориям А+В+С1 – в количестве 1250,4 т. Кроме того, за контуром карьера государственной экспертизой были учтены забалансовые запасы по категории С2 в количестве 250,4 т золота.
Протоколом ГКЗ Роснедра №3490 от 31.01.2014 утверждено разделение запасов на две части: на запасы, находящиеся в пределах горного отвода выше горизонта +450 м и запасы, находящиеся за пределами горного отвода ниже гор.+450 м (нераспределенный фонд).
Балансовые запасы, расположенные выше гор. +450 м для отработки открытым способом представлены в таблице 1.
Таблица 1 – Балансовые запасы золотосодержащего минерального сырья месторождения «Наталка» (по состоянию на 01.01.2021)
Категория запасов | Минеральное сырье | Золото | Минеральное сырье | Серебро | ||
тыс. т | г/т | кг | тыс. т | г/т | т | |
В | 89 235 | 1,764 | 157 406 | - | - | - |
С1 | 440 678 | 1,651 | 727 356 | - | - | - |
В+С1 | 529 914 | 1,670 | 884 763 | - | - | - |
С2 | 111 624 | 1,891 | 211 103 | 641 538 | 0,478 | 306,6 |
В+С1+С2 | 641 538 | 1,708 | 1 095 866 | 641 538 | 0,478 | 306,6 |
Склады | 33 072 | 0,813 | 26 881 | 33 072 | 0,230 | 7,6 |
В целом созданная разведочная сеть позволила оценить основную часть (87%) балансовых запасов месторождения по категориям В+С1; около 13 % запасов оценены по категории С2. На основе этих данных проведено обоснование кондиций и выполнен подсчет запасов при бортовом содержании золота 0,4 г/т.
Стратегия разработки месторождения по добыче всех балансовых запасов извлекаемого из недр минерального сырья в количестве на 01.01.2021 г. 641 538 тыс. т в границах лицензионного участка предусматривает отработку до 01.01.2062 в две очереди (рис.1):
-
первая очередь предусматривает отработку балансовых запасов период с 01.01.2021 по 2023г. включительно. -
вторая очередь предусматривает доработку всех оставшихся балансовых запасов с 2024 года до 2062 г.
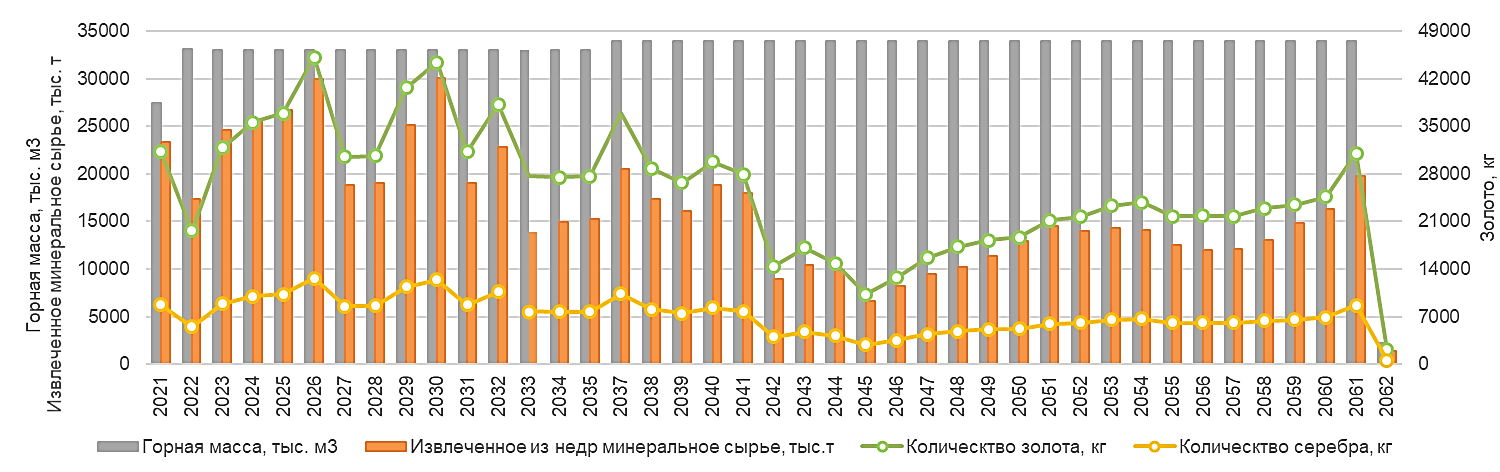
Рис.1 – Стратегия отработки месторождения «Наталка»
2.2 Характеристика пород вскрыши и полезного ископаемого
Месторождение сложено практически монотонной толщей терригенных и вулканогенных отложений общей мощностью около 2 км, в основном, ранне- и позднепермского возраста. По литологическим признакам выделяется ряд свит: тасская (нижняя), атканская (средняя) и нерючинская (верхняя).
Рудовмещающие породы представлены терригенными гидротермально-метаморфизованными осадочными и вулканогенно-осадочными отложениями пермского возраста (алевролиты, песчаники, гравелиты), содержащими значительное количество вулканогенного материала и примесь (1–3%) углерода.
Выделены следующие разновидности пород:
1) алевро-пелитовые и псаммитовые осадочные и осадочно-вулканогенные отложения. К ним отнесены глинистые, углисто-глинистые сланцы и песчаники тасской (Р1-2 ts) и нерючинской (Р2 nr) свит;
2) осадочные и осадочно-вулканогенные отложения с включениями туфового материала или вулканогенных пород псаммитовой и псефитовой размерности до 5% и от 5 до 40% к объему породы. Эти группы пород принадлежат к атканской свите верхней перми (P2at);
3) осадочные и осадочно-вулканогенные отложения с обломками и кластикой вулканогенных пород псефитовой и агломератовой размерности от 5% до 70% к объему породы. Породы часто пространственно совмещены с положением даек основного состава и картируются в виде линз и полос уплощенной формы, вытянутых в северо-западном направлении в пределах атканской свиты.
Месторождение коренное, относится к пирит-арсенопиритовому минеральному типу золото-кварцевой малосульфидной формации. Оруденение не имеет четких геологических границ. При бортовых содержаниях 0,4–0,6 г/т выделяется единая рудная залежь с достаточно условным разделением на отдельные рудные тела и подсчетные блоки (рис. 2). Статистический анализ данных показывает, что основная масса руды, содержащая 75–80 % запасов золота, связана с кварцевым прожилкованием слабой и средней интенсивности.
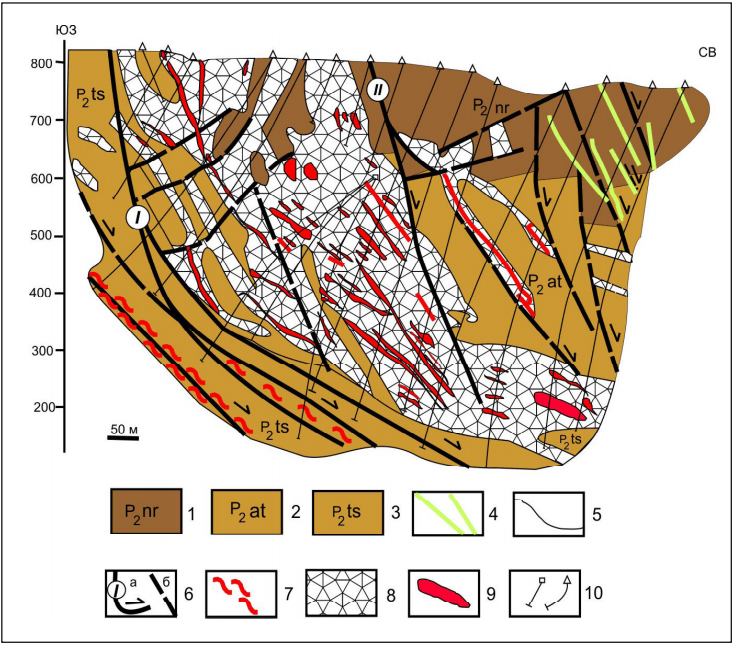
Рис. 2 – Геологический разрез месторождения Наталка, иллюстрирующий морфологию
рудного штокверка, развивавшегося в тектоническом режиме транстенсии:
1 – нерюнчинская свита (P2 nr); 2 – атканская свита (P2 at); 3 – тасская свита (P2 ts); 4 – дайки; 5 – границы геологические; 6 – разломы с направлением смещения: а – главные ( I – главный, II – северо-восточный), б – второстепенные; 7 – зоны смятия и рассланцевания; 8 – контуры рудной залежи (бортовое содержание Au 0,4 г/т); 9 – области повышенного содержания Au (> 2,0 г/т); 10 – буровые скважины
Главные жильные минералы: кварц (60–80%), карбонаты и полевые шпаты; главные рудные минералы – сульфиды (3–5%), представлены в основном арсенопиритом и пиритом (95–99%), а также пирротином, халькопиритом, галенитом и сфалеритом.
Отмечена зональность в распределении основных сульфидов (пирита и арсенопирита): для верхних рудных горизонтов характерна ассоциация золота с крупнозернистым арсенопиритом, часто в гнездовых срастаниях с пиритом, на глубине (глубже отметки 600 м) пирит исчезает. Фиксируется зональность в распределении полиметаллической минерализации: галенит преобладает на верхних горизонтах, а сфалерит и халькопирит – на нижних.
Крупность и пробность золота с глубиной возрастают. Золото самородное, относительно крупное (средний размер золотин 0,1–2 мм), высокопробное (730–800 и выше), концентрируется в кварце, а также тонкодисперсное; образует рассеянную вкрапленность в сульфидах.
2.3 Гидрогеологические условия района работ
В гидрогеологическом отношении район работ расположен в области сплошного распространения многолетнемёрзлых пород (ММП). Устойчивые талики имеют ограниченное распространение. Они прослеживаются в пойме р. Омчак и устьевых частях наиболее крупных её притоков руч. Оротукан, Геологический, Мороз, Павлик, Лев, Вилка. На отдельных участках талики имеют сквозной характер. Верхняя граница ММП, в основном, повторяет наземные формы рельефа. ММП мощностью до 317, возможно, более метров оказывают существенное влияние на динамику и ресурсы подземных вод, концентрируя их основные запасы в пределах таликовых зон.
Межмерзлотные водоносные зоны, суммарной мощностью 13-15 м, вскрыты скважинами в интервале абсолютных отметок 547-532,7 м. Подмерзлотные воды залегают ниже подошвы ММП и являются напорными, величина напора 99,4-140,6 м.
Гидрогеологические условия на месторождении на уровне горизонтов 550 м в талых обводненных породах под толщей ММП определены как сложные (тип III), что обусловлено наличием на месторождении мощной толщи многолетнемерзлых пород, ниже которой залегает локальная водоносная зона трещиноватости, содержащая напорные воды.
До выхода горных работ из зоны распространения ММП, ориентировочно на гор. +645 м, обводнение карьера будет происходить в основном за счет атмосферных осадков в период положительных температур. При отработке нагорной части карьера (до абс. отметки +731 м) атмосферные осадки, выпадающие на площадь карьера, удаляются самотеком, для чего бермы делаются наклонными как в сторону массива, так и в продольном направлении.
При ведении горных работ ниже отм. +645 м водопритоки в карьер будут формироваться как за счет атмосферных осадков, так и за счет подземных вод ЛВЗТ. Основными источниками формирования водопритоков здесь являются естественные запасы и естественные ресурсы локально-водоносной зоны трещиноватости пермских пород.
Возможный водоприток в карьер при отработке месторождения открытым способом, ожидается за счет подмерзлотных вод и оценивается в 50 м3/час. Максимальные водопритоки с поверхности возможны до 1300 м3/час.
3 Характеристика земельного и горного отвода
Наталкинское месторождение представляет собой крупную рудную залежь, протяженность которой достигает 5000 м при средней мощности около 200 м. Размеры карьера достигнут к концу отработки длины 4400 м, ширины 1500 м при глубине 866,7 м.
Генеральный план размещения объектов карьера определен с учетом технологических связей, удобства транспортных и пешеходных связей, санитарных и противопожарных требований, рельефа местности, розы ветров и инженерно-геологических условий. Зонирование территории выполнено с учетом занятия минимально-возможных площадей под разработку месторождения.
Земельный отвод карьера включает в себя территорию непосредственно карьера и объектов, связанных с отработкой карьера. Существующий земельный отвод располагается на землях лесного фонда Тенькинского участкового лесничества, Кулинского участкового лесничества, арендуемых на основании утвержденных правоустанавливающих документов. и землях населенных пунктов:
– земли лесного фонда – 70204,47 га;
– земли населенных пунктов – 446,62 га
Общая площадь предприятия составляет 7651,09 га
Территория, нарушенная разработками месторождения, представлена карьерными выемками, траншеями, отвалами вскрышных пород, линейными объектами, производственными площадками.
Конечный контур карьера построен с углами откосов уступов в конечном положении по юго-западному борту – 70°, северо-восточному - 60°, что подтверждено заключением ВНИМИ об устойчивости бортов (Приложение 5).
Нижняя граница горного отвода ограничена по глубине разработки горизонтом +450 м. Площадь участка недр составляет 22,1 км2.
Основные планировочные решения по организация земельного участка действующего горнодобывающего предприятия на базе месторождения «Наталка» выполнены на основании разработанного генерального плана с учетом технологической схемы производства, с обеспечением наиболее благоприятных условий для производственного процесса и труда на предприятии, рационального и экономного использования земельных участков и наибольшей эффективности капитальных вложений (Приложение 1).
Перечень основных и вспомогательных объектов в границах земельного отвода:
- карьер;
- отвал Северный;
- отвал Восточный;
- отвал «Южный»;
- основной склад руды
;
- склад руды Южный;
- склад руды Северный;
- площадки насосных станций;
- площадка отстоя и ремонта техники;
- площадка отстоя карьерного транспорта;
- площадка вспомогательных служб;
- основное хвостохранилище;
- временное хвостохранилище;
- хвостохранилище на ручье Глухарь;
- площадка ЗИФ;
- склад взрывчатых материалов (ВМ);
- рудный дробильно-конвейерный комплекс (РДКК);
Месторасположение объектов представлено на рисунке 3.
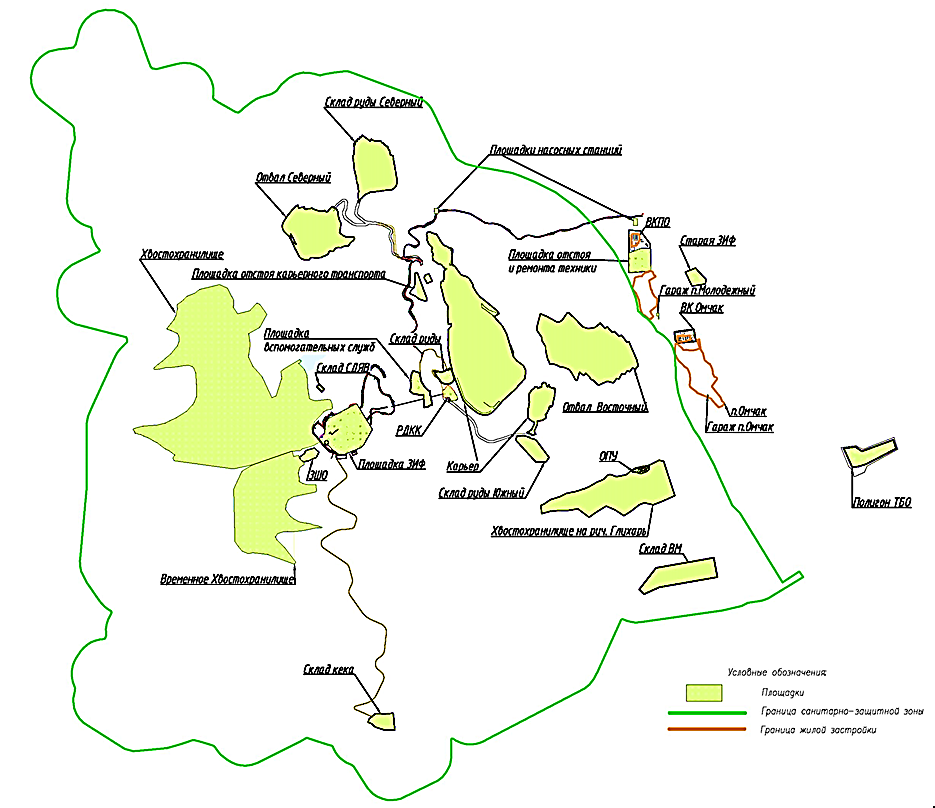
Рис.3 – Объекты предприятия на территории земельного отвода
4 Особенности технологического процесса
4.1 Подготовка пород к выемке
Вскрывающие породы месторождения относятся к III-ей категории (крепкие) по шкале проф. М.М. Протодьяконова с коэффициентом крепости f = 8, поэтому подготовка горной массы к выемке осуществляется буровзрывным способом.
В условиях сравнительно узких зон минерального сырья месторождения буровзрывные работы целесообразно вести с использованием скважин малого диаметра при небольшой высоте уступа, что позволит эффективно контролировать разубоживание минерального сырья и сократить его потери. При этом рациональные диаметры зарядов для взрывания минерального сырья проектными решениями приняты в среднем 140-170 мм, для взрывания пород вскрыши около 250 мм.
Бурение скважин выполняют станками FlexiROC D65 и DML. Станки FlexiROC D65 обеспечивают бурение скважин по минеральному сырью, станки DML – скважин по минеральному сырью и по породам вскрыши. При расширении производственной мощности предприятия и увеличении объемов обуриваемой вскрыши проектом предусматриваются станки СБШ-250/270-60 или СБШ-250 МНА с диаметром долота 250-270 мм. Ввод в эксплуатацию этих станков обусловлен экономичностью и положительным опытом по разработке рудных месторождений Компании в суровых климатических условиях. Расположение буровых станков на уступе показано на рисунке 4.
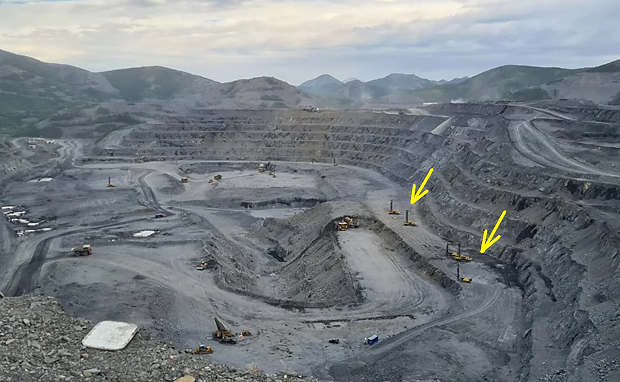
Рис. 4 – Расположение буровых станков на уступе (фото)
Режим работы станков круглогодичный, в две смены по 12 часов. График работ учитывает проведение планово-предупредительных ремонтов (ППР), организационно-технических мероприятий (ОТМ) – перегоны и подключения, в соответствии с нормативами (таблица 2).
Таблица 2 – Режим работы буровых станков
Наименование бурового станка | Годовой календарный фонд работы станков | Расчет 1-й единицы | Коэффициент технической готовности | Коэффициент использования оборудования | ||||
Плановые простои | Количество рабочих смен | |||||||
ППР | ОТМ | |||||||
см | см | см | см | д. ед | д. ед | |||
- СБШ-250/270-60 | 700 | 90 | 50 | 550 | 0,79 | 0,65 | ||
- DML | 700 | 90 | 50 | 540 | 0,77 | 0,64 | ||
- FlexiROC D65 | 700 | 90 | 50 | 560 | 0,80 | 0,67 |
Достигнутая на предприятии и расчетная производительность буровых станков в соответствии с инженерно-геологической характеристикой пород и углом бурения скважин к горизонту представлена в таблице 3.
Таблица 3 – Сменная производительность буровых станков
Наименование | Сменная производительность в зависимости от наклона скважин, м/см | ||
900 | 700 | 600 | |
Зоны выветривания и зоны тектонических нарушений (категория по буримости - VI) | |||
СБШ-250/260-60 | 160 | 144 | 128 |
DML | 330 | 297 | 264 |
FlexiROC D65 | 270 | 243 | 216 |
Метаморфизованные породы (категория по буримости - X) | |||
СБШ-250/260-60 | 150 | 135 | 120 |
DML | 300 | 270 | 240 |
FlexiROC D65 | 250 | 225 | 200 |
Метаморфизованные породы (категория по буримости - XII) | |||
СБШ-250/260-60 | 140 | 126 | 112 |
DML | 270 | 243 | 216 |
FlexiROC D65 | 220 | 198 | 176 |
Объемы бурения и расчетное количество буровых станков с учетом срока их эксплуатации представлены в таблице 4
Таблица 4 – Объемы бурения, потребное количество буровых станков
Показатели | Значения по годам | Итого за период 2021-2023 гг. | ||
2021 | 2022 | 2023 | ||
1 | 2 | 3 | 4 | 5 |
Горная масса, тыс.м3 | 27 415 | 33 176 | 33 000 | 93 591 |
Минеральное сырье, тыс.т | 23 340 | 17 343 | 24 605 | 65 288 |
Вскрыша, тыс.м3 | 18 131 | 26 177 | 23 607 | 67 914 |
Выход горной массы DML, м3/п.м | 25 | 25.2 | 25.2 | |
Выход горной массы FlexiROC D65, м3/п.м | 14.7 | 14.7 | 14.7 | |
Объём бурения скважин рыхления, п.м. | 1 864 944 | 2 256 886 | 2 244 898 | 6 366 728 |
- DML, п.м. | 1 486 011 | 1 923 575 | 1 893 456 | 5 303 042 |
- FlexiROC D65, п.м. | 378 933 | 333 312 | 351 442 | 1 063 686 |
Объём бурения контурных скв. FlexiROC D65, п.м. | 109 697 | 253 360 | 183 529 | 546 585 |
Объём RC бурения FlexiROC D65, п.м. | 143 386 | 106 544 | 151 162 | 401 093 |
ВСЕГО ОБЪЕМ БУРЕНИЯ DML, п.м. | 1 486 011 | 1 923 575 | 1 893 456 | |
ВСЕГО ОБЪЕМ БУРЕНИЯ FlexiROC D65, п.м. | 632 016 | 693 216 | 686 132 | |
Средняя производительность бурового станка, м/см | | | | |
- DML | 465 | 470 | 460 | |
- FlexiROC D65, м/см | 310 | 317 | 330 | |
Количество рабочих смен на 1 единицу | | | | |
- DML, см | 560 | 560 | 560 | |
- FlexiROC D65, см | 560 | 560 | 560 | |
Потребное количество буровых станков | | | | |
- DML, ед | 6 | 9 | 9 | |
- FlexiROC D65, ед | 4 | 4 | 4 | |
Параметры буровых работ при контурном взрывании приведены в таблице 5.
Таблица 5 – Параметры буровых работ при контурном взрывании
Наименование | Значение | ||
Угол наклона скважин, град | 60 | 70 | |
Диаметр скважин на контурном взрывании, м | 0,110 | ||
Удельная площадь заоткоски (на 1000 м3 горной массы), м2/1000м3 | 1,5 | ||
Расстояние между скважинами отрезной щели, м | 2,0 | ||
Перебур, м | 1,0 | ||
Глубина отрезной щели, м | 52,9 | 48,9 | |
Удельный расход бурения при контурном взрывании | пог. м/1000м2 | 617,88 | 570,36 |
пог. м/1000м3 | 0929 | 0,857 |
Для снижения сейсмического воздействия на законтурный массив предусматривается бурение и взрывание скважин заоткоски буровыми станками FlexiROC D65 долотами диаметром 134 мм.
Для снижения пылеобразования при взрывных работах при необходимости рекомендуется применять комбинированную гидрозабойку скважин (комбинация внутренней и внешней гидрозабойки).
При формировании уступов в предельном положении применяют скважины предварительного щелеобразования.
Конструкции скважинных зарядов представлены на рисунке 5.
Схемы короткозамедленного взрывании (КЗВ) представлены в Приложении 2.
Для производства взрывных работ предусмотрено использовать гранулированные и порошкообразные ВВ, как промышленного производства, так и местного изготовления, применяющиеся в настоящее время: гранулит РП, Фортис, граммонит 30/70, колымит Б.
Инициирование скважинных зарядов осуществляется с помощью ДШЭ и системы ИСКРА (или аналог) с использованием электродетонаторов ЭДКЗ-ПКМ и ЭД-1-8-Т. Промежуточные детонаторы – шашки-детонаторы ТГ-500, ТГФ-850Э или ТГ-П850.
Взрывание скважин короткозамедленное, при использовании ДШЭ достигается с помощью пиротехнических реле РП-Д-30, 45, 60. [3].
Доставка ВМ для производства взрывных работ осуществляется специализированным транспортом с поверхностного постоянного расходного склада ВМ.
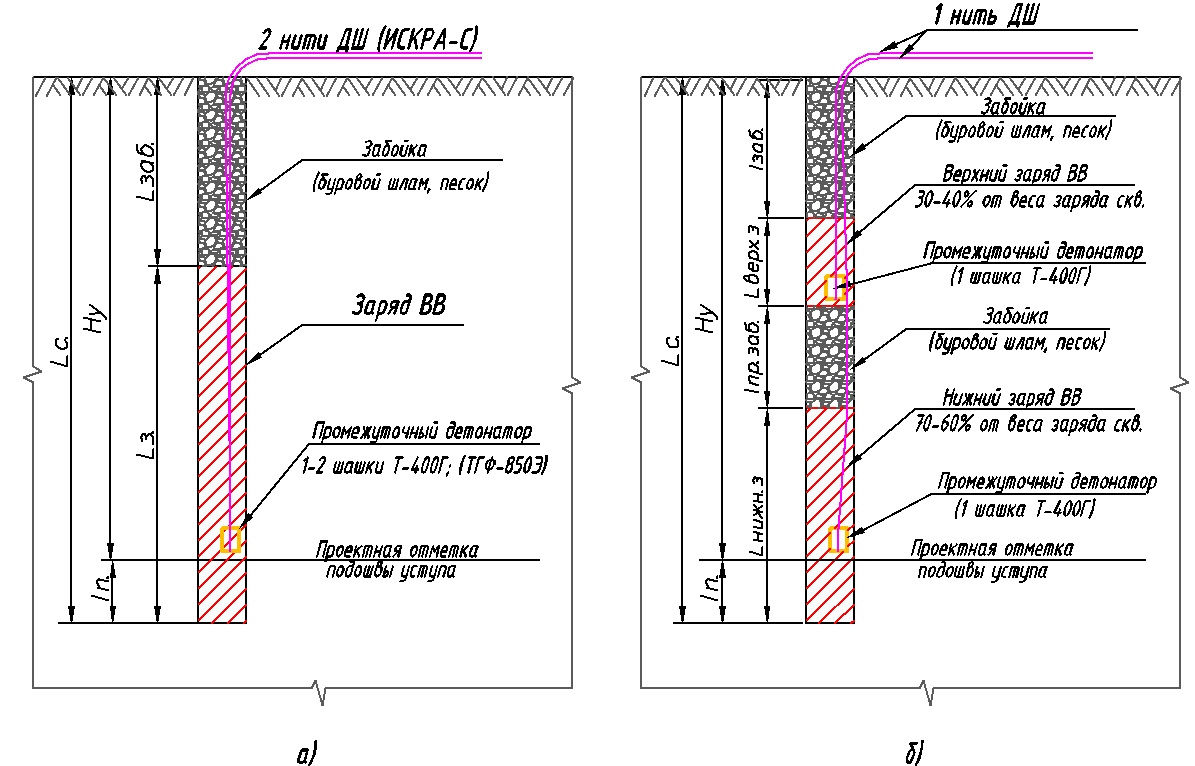
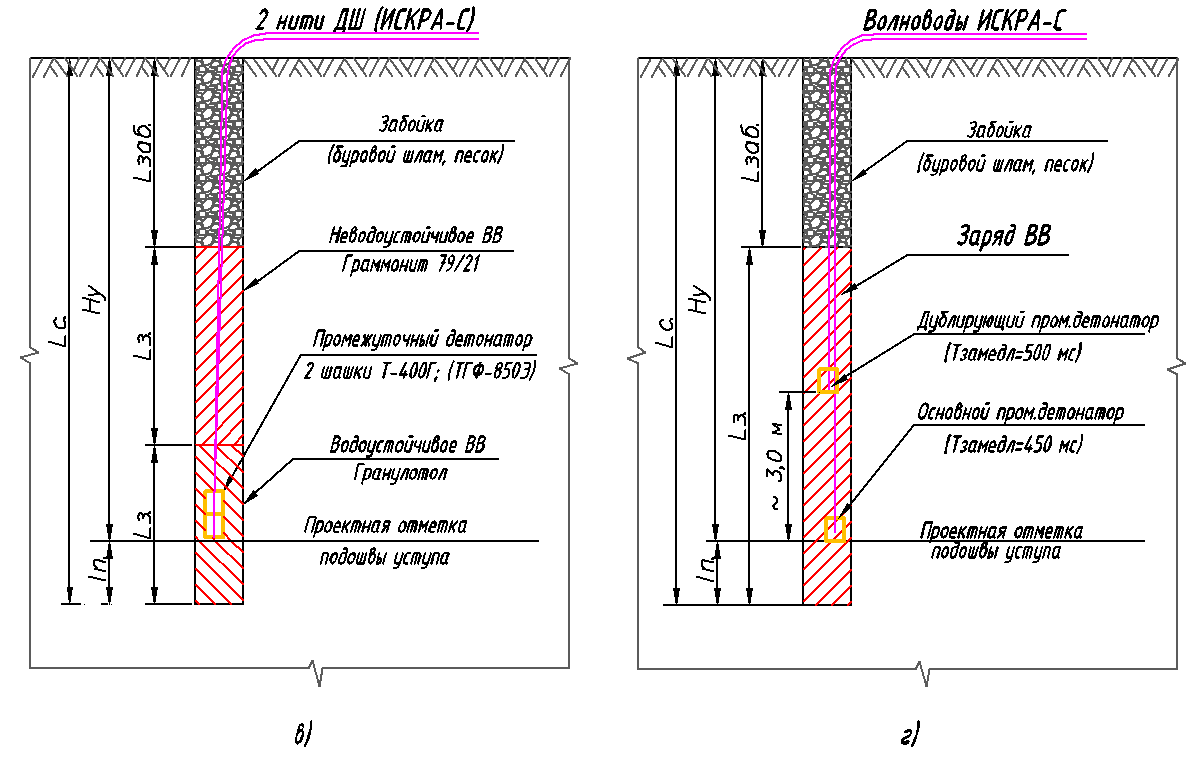
а) сплошной колонковый заряд (применяется в вертикальных и наклонных скважинах);
б) рассредоточенный заряд (сухие вертикальные скважины);
в) комбинированный заряд (частично обводненные скважины);
г) патронированный заряд (в скважинах «заоткоски»)
Рис. 5 – Конструкции скважинных зарядов
Параметры буровзрывных работ по вскрыше и по руде представлены в таблице 6.
Таблица 6 – Параметры буровзрывных работ
Наименование | Вскрыша | Руда |
1 | 2 | 3 |
Высота уступа, м | 15 | 7,5 |
Наименование применяемого ВВ | Игданит | Игданит |
Удельная энергия ВВ, кДж/кг | 3200 | 3200 |
Скорость детонации, м/с | 4300 | 4300 |
Плотность ВВ, кг/м3 | 850 | 850 |
Диаметр взрывных скважин, м | 0,250 | 0,170 |
Угол наклона взрывных скважин, град | 90 | 90 |
Периодичность отбойки, суток | 3,5 | 3,5 |
Объем взрываемого блока, т | 1343515 | 474576 |
Удельный расход ВВ, кг/м3 | 0,875 | 0,913 |
Параметры первого ряда скважин: | ||
Линия сопротивления по подошве уступа | 6,0 | 4,0 |
Вместимость 1м скважины, кг | 58,4 | 25,4 |
Параметры взрывания скважин первого ряда: | ||
- расстояние между скважинами в ряду, м | 6,9 | 4,6 |
- длина перебура, м | 2,5 | 1,7 |
- длина скважины, м | 17,5 | 9,2 |
- длина забойки, м | 8,2 | 4,2 |
- длина заряда, м | 9,3 | 5,0 |
- общая масса заряда в скважине, кг | 543,5 | 126 |
- коэффициент заполнения скважин | 0,53 | 0,54 |
Параметры взрывания скважин последующих рядов: | ||
- расстояние между скважинами в ряду, м | 6,9 | 4,6 |
- расстояние между рядами скважин, м | 6,0 | 4,0 |
- длина перебура, м | 2,5 | 1,7 |
- длина скважины, м | 17,5 | 9,2 |
- длина забойки, м | 8,2 | 4,2 |
- длина заряда, м | 9,3 | 5,0 |
- общая масса заряда в одной скважине, кг | 543,5 | 126 |
- коэффициент заполнения скважин | 0,53 | 0,54 |
Продолжение таблицы 6
1 | 2 | 3 |
Объемные показатели: | | |
- средний объем пород, отбиваемый одним зарядом, м3 | 621 | 138 |
- количество скважин на объем взрываемого блока | 807 | 1283 |
- длина скважин на объем взрываемого блока, м | 14127 | 11741 |
- средний выход породы с 1м скважин, м3 | 35,5 | 15,08 |
- объем бурения на: | | |
- 1000 м3 отбиваемых пород, м | 28,2 | 66,3 |
- 1000 т отбиваемых пород, м | 10,5 | 24,74 |
Расходные показатели: | ||
- расход ВВ на объем взрываемого блока, кг | 438723 | 161669 |
- общий удельный расход ВВ, кг/м3 | 0,88 | 0,913 |
Радиус по разлету кусков, м | 249 | 270 |
Безопасное расстояние по действию УВВ, м | 1125 | 817 |
При рыхлении вскрышных пород производство взрывных работ осуществляется каждые 3,5 суток (92 взрыва в год). Взрывные работы при добыче руды осуществляются так же.
Учитывая III категорию трещиноватости, выход негабарита составит 1% от горной массы. Дробление негабарита предусмотрено кумулятивными и накладными зарядами с применением патронированного аммонита №6ЖВ диаметром 32 мм.
4.2 Выемочно-погрузочные работы
Оптимальная вместимость ковша для выемочно-погрузочных работах в карьере в среднем должна быть равна около 20 м3. Для выемки и погрузки минерального сырья в карьере преимущественно предусматриваются экскаваторы Komatsu PC 1250, Komatsu PC 4000 и погрузчики CAT 994H, Komatsu WA 900, также допускается применение WK-20 и P&H-2300. Выемка вскрышных пород предусмотрена преимущественно экскаваторами WK-20 и P&H-2300. При необходимости допускается частичное использование гидравлического оборудования.
При годовом объеме вскрышных работ 40 млн. т количество уступов в одновременной отработке: 2 уступа по руде и 2 по породе. Количество экскаваторов в зоне вскрышных работ – 8 штук и в рудо-породной зоне –11. В соответствии с транспортной схемой карьера доступ автотранспорта обеспечивается к каждому забою [8].
Основные параметры вскрышного и добычного забоев сведены в таблицу 7.
Таблица 7 – Основные параметры забоя
Параметр | Вскрыша | Добыча |
Высота уступа, м | 15 | 7,5 |
Угол откоса рабочего уступа, град | 75 | 75 |
Ширина рабочей площадки, м | 99,1 | 67,5 |
Учитывая количество взрывов в год, годовой объем выемки вскрышных пород и количество экскаваторов, объем экскаваторного блока на 1 единицу выемочно-погрузочного оборудования составляет 57,8 тыс.м3. При высоте уступа 15 м и ширине заходки экскаватора – 23,6 м длина активного фронта на 1 экскаватор составляет 200 м. При высоте добычного уступа 7,5 м и ширине заходки погрузчика – 5,6 м длина фронта работ составит 260 м. Показатели производительности экскаваторов представлены в таблице 8.
Таблица 8 – Потребное количество выемочно-погрузочного оборудования
Показатели | Ед. изм. | Значения по годам | Итого в период 2021-2023 гг. | ||
2021 | 2022 | 2023 | |||
1 | 2 | 3 | 4 | 5 | 6 |
Горная масса | тыс. м³ | 27415 | 33176 | 33000 | 93591 |
Средняя производительность | | | | | |
- WK-20, P&H-2300 | тыс. м³/см | 8,3 | 8,2 | 8,1 | |
- Komatsu РС 4000 | тыс. м³/см | 8,6 | 8,5 | 8,3 | |
- CAT 994H | тыс.м³/см | 6,6 | 6,5 | 6,4 | |
- Komatsu WA 900 | тыс.м³/см | 3,3 | 3,3 | 3,3 | |
- Komatsu PC 1250 | тыс.м³/см | 2,6 | 2,6 | 2,5 | |
Количество рабочих смен | | | | | |
- WK-20, P&H-2300 | см | 570 | 570 | 570 | |
- Komatsu РС 4000 | см | 570 | 570 | 570 | |
- CAT 994H | см | 580 | 580 | 580 | |
- Komatsu WA 900 | см | 590 | 590 | 590 | |
- Komatsu PC 1250 | см | 600 | 600 | 600 | |
Потребное количество экскаваторов и погрузчиков в карьере | | 7 | 9 | 7 | |
- WK-20, P&H-2300 | ед | 2 | 4 | 4 | |
- Komatsu PC 4000 | ед | 1 | 1 | 1 | |
Продолжение таблицы 8
1 | 2 | 3 | 4 | 5 | 6 |
- CAT 994H | ед | 2 | 2 | 1 | |
- Komatsu WA 900 | ед | 1 | 1 | 0 | |
- Komatsu PC 1250 | ед | 1 | 1 | 1 | |
Процесс выемочно-погрузочных работ показан на рисунке 6.
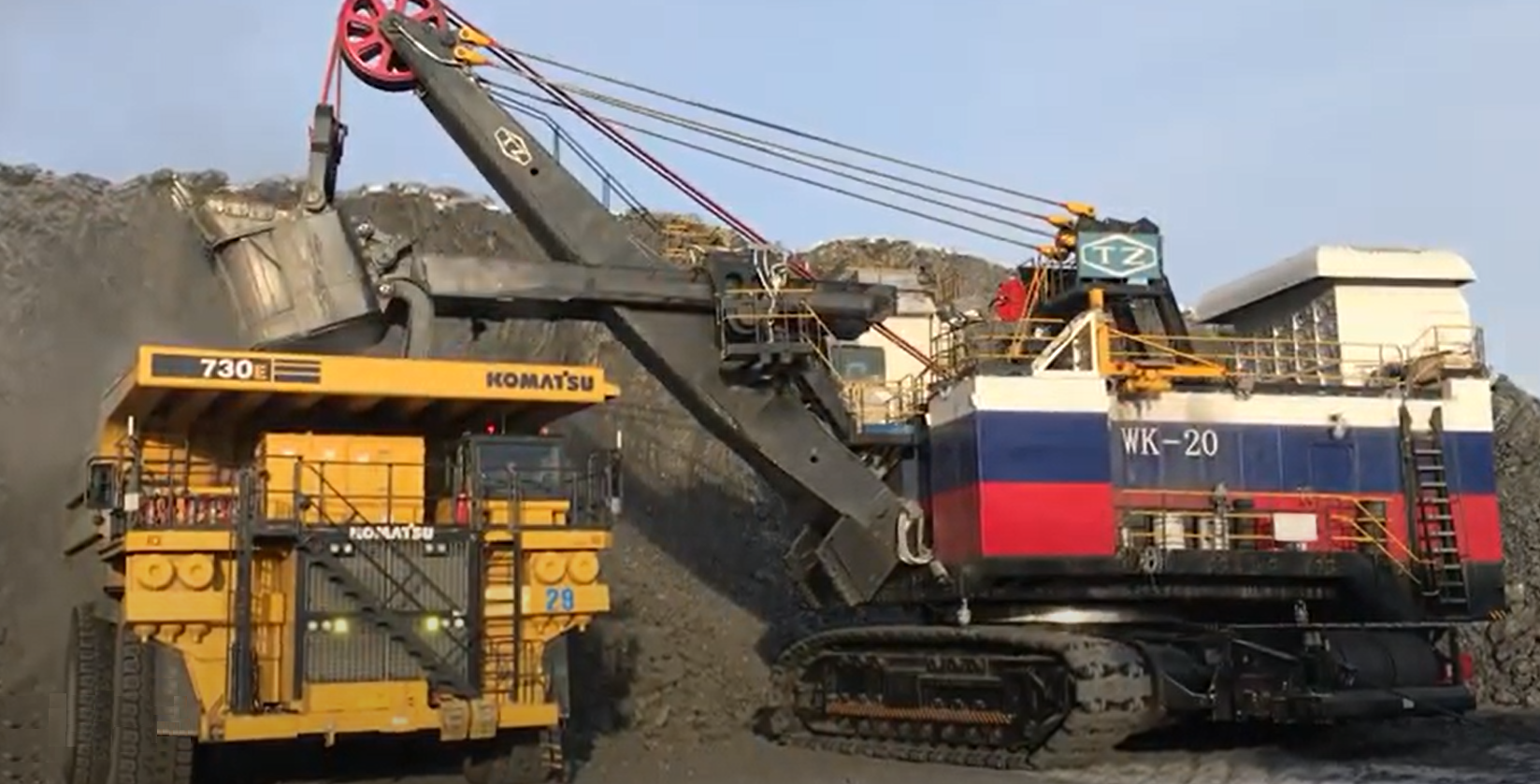
Рис. 6 – Технологическое оборудование на выемочно-погрузочных работах
Экскавацию вскрышных пород осуществляют уступами высотой 15 м и 7,5 м, экскавацию минерального сырья уступами высотой 7,5 м.
Паспорт вскрышного забоя представлен в Приложении 3, паспорт добычного забоя – в Приложении 4.
4.3 Перемещение карьерных грузов
Транспортирование руды производится автосамосвалами типа CAT 793D (грузоподъемность 218 т), породы – автосамосвалами типа CAT 795F (грузоподъемность 313 т) по временным и постоянным транспортным съездам шириной 35 м с продольным уклоном 80 ‰ и площадками примыкания (виражами) между съездами 50 м.
Работы ниже горизонта +731 м предусматривается вести с применением циклично-поточной технологии транспортирования горной массы.
Окончательная общая схема транспортировки породы выглядит следующим образом: вскрышной забой – экскавация – транспортирование автосамосвалами на дробилку крупного дробления – наклонный конвейерный ствол – отвалообразователь – отвал вскрышных пород.
Производительность автосамосвалов на транспортировке пород вскрыши и полезного ископаемого представлена в таблице 9.
Таблица 9 – Сводная таблица производительности автосамосвалов
Наименование | Вскрыша (CAT 795F) | Добыча (CAT 793D) |
Сменная производительность, т/ч | 2609 | 2740 |
Суточная производительность, т/ч | 5219 | 5480 |
Годовая производительность, т/год | 1904762 | 2000000 |
Трассировка двух рудных конвейерных тоннелей, выполнена с учетом трассировки двух наклонных рудных стволов, которые обеспечивают рудную поточную технологию с глубоких горизонтов и, которые имеют с ранее пройденными тоннелями технологические «сбойки». Таким образом, после «оформления» технологических сбоек выстраивается законченная схема рудного потока: рудный забой – автотранспорт – дробилка – наклонный конвейерный ствол – конвейерный тоннель – рудный склад ЗИФ.
Таким образом, в период, когда с понижением дна карьера грузовая работа становится объективно максимальной, оптимизируется транспортная схема рудных потоков, отсутствует необходимость выезда большегрузных самосвалов за пределы карьера, плечи транспортирования горной массы максимально короткие. Руда направляется на дробильный комплекс крупного дробления, расположенный на западном борту, далее, после дробления, ленточным конвейером транспортируется на ЗИФ.
Необходимость строительства конвейерного тоннеля от борта карьера до рудного склада ЗИФ продиктована следующими обстоятельствами: ЗИФ находится от границы карьера на расстоянии порядка 1,7-2 км по прямой. Между промплощадкой ЗИФ и карьером расположен горный хребет с максимальными отметками выше отметки карьера на 300м и промплощадки ЗИФ на 250 м. Поэтому транспортировка руды на фабрику по рельефу может быть организована или с преодолением горного хребта, т.е. на подъеме, при движении из карьера и затем под уклон, или в объезд горного хребта, что удлиняет расстояние транспортирования до 10 км. Очевидно, что в первом случае будет выполняться излишняя работа по подъему руды при преодолении хребта, а во втором случае – расстояние транспортирования слишком велико и связано с выполнением весьма большого объема грузовой работы.
Добытая руда по системе транспортных берм карьера направляется на дробильный комплекс, расположенный на Западном борту карьера, далее конвейерным транспортом на площадку фабрики. Конвейер уложен в штольне с отметкой устья +850 м, длина конвейера 1650 м. Прокладка конвейера в тоннеле позволяет с целью минимизации капитальных и эксплуатационных затрат получить уменьшение длины транспортирования руды с карьера до ЗИФ, укрытие конвейера от крайне неблагоприятных погодных условий, чем обеспечивается его надежная работа. В этом случае схема транспортирования руды является оптимальной и выглядит следующим образом: добычной забой – экскавация – транспортирование автосамосвалами на борт карьера – дробилка крупного дробления – конвейер (в тоннеле) – склад руды на площадке ЗИФ (рис.7).
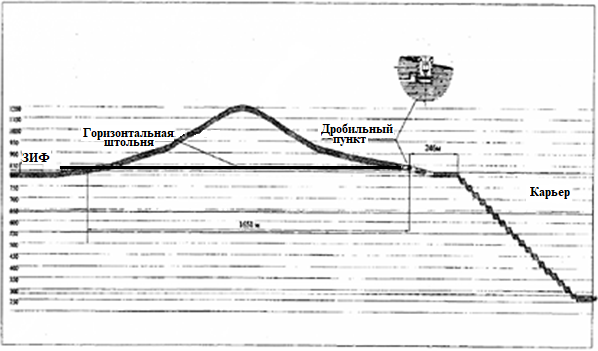
Рис.7 – Схема размещения рудного конвейера на борту карьера
Для первичного дробления и транспортировки руды от места ведения горных работ до склада, проектом предусматривается применение рудного дробильно-конвейерного комплекса (РДКК), состоящего из двух независимых рудных линий.
Горнотехнические условия карьера достаточно благоприятны для использования конвейеров. Это связано с тем, что в торцах карьера на предельном контуре, где намечено их размещение с учетом строения рудного тела остаются площадки, которые выполаживают борта на данных участках до 25-26. Это позволяет построить здесь траншеи под конвейерные подъемники с углом наклона 15-16о и разместить дробильно-перегрузочные пункты (ДПП) при минимальных дополнительных объемах горно-капитальных работ. По предварительным оценкам использование конвейерного транспорта может быть начато на 11-12 годы ведения горных работ в карьере, поскольку именно к этому периоду начнется отработка глубинной части месторождения.
4.4 Отвалообразование
На карьере принята транспортная система разработки с внешним отвалообразованием. Складирование вскрышных пород предусмотрено в многоярусные отвалы: Восточный, Северный и Южный. Северный отвал находится к северо-западу от поля карьера на расстоянии 1,1км, Южный – к югу на расстоянии 1,2 км. Территория, принятая для размещения пород вскрыши – нагорная с абсолютными отметками от 730 м до 960 м (Северный отвал) и от 735 до 1020 м (Южный отвал). Абсолютные отметки поверхности составляют: Северного отвала 980 м, Южного – 1000 м, площади отвалов составляют: Северный – 617 га, Южный – 530 га.
За период строительства и эксплуатации из карьера во внешние отвалы будет направлено 1066948 тыс. м³ породы в целике, часть пойдет для строительства дамбы хвостохранилища, водоотводных дамб, автодорог и промплощадок. Распределение объема породы по отвалам на конец отработки карьера приведено в таблице 10.
Таблица 10 – Распределение объёма породы по отвалам
Наименование показателей | Объемы вскрыши, тыс. м³ | |
Северный отвал | Южный отвал | |
Объем, тыс. м³ | 588386,5 | 478561,5 |
Коэффициент остаточного разрыхления | 1,2 | 1,2 |
Итого в отвале в конечном положении, тыс. м³ | 706063,8 | 574273,8 |
На карьере применяется способ бульдозерного отвалообразования: 1-й ярус Северного и Южного отвалов формируется бульдозером CAT D11 снизу вверх с доставкой породы автосамосвалами CAT 795F. Ярус намечено отсыпать двумя подъярусами. Высота подъяруса составляет 45 м, общая высота яруса составит 90 м (отметка верха 800 м на Северном отвале и 820 м на Южном отвале), угол откоса 36º.
Отсыпка вскрышных пород на отвале производится заходками. Длина каждой заходки равняется длине фронта непосредственной разгрузки, которая зависит от грузоподъемности автосамосвала (типа CAT 795F) и составляет 100-150 м.
Площадка разгрузки имеет поперечный уклон по всему фронту не менее 3º, направленный от бровки откоса в глубину отвала. Вся остальная площадь рабочей зоны отвала имеет поперечный уклон от площадки разгрузки к въезду на отвал менее 1º.
Разгрузка производится автосамосвалами по всему фронту участка разгрузки, длина которого составляет 100-150 м, с отступлением в глубину рабочей площадки, но не более чем на 15-20 м от предохранительного вала, который создается бульдозером по всей протяженности бровки отвала при планировании разгрузочной площадки. Высота вала принимается в соответствии с требованиями Правил безопасности и для автосамосвалов типа CAT 795F составляет не менее 2 м.
При отсыпке и формировании предохранительного вала, а также планировке подъездов к нему, расстояние от ножа бульдозера до бровки отвала принято не меньше ширины основания вала и составляет 6м.
На разгрузочной площадке при одновременной разгрузке нескольких автосамосвалов расстояние между ними должно быть не менее 5 м. После засыпки откоса отвала через породный предохранительный вал (заработка вала) разгрузка на этом участке прекращается, и бульдозер производит перемещение на откос отвала излишней породы с одновременным формированием на его бровке нового предохранительного вала.
Технологическая схема формирования бульдозерного отвала показана на рисунке 8.
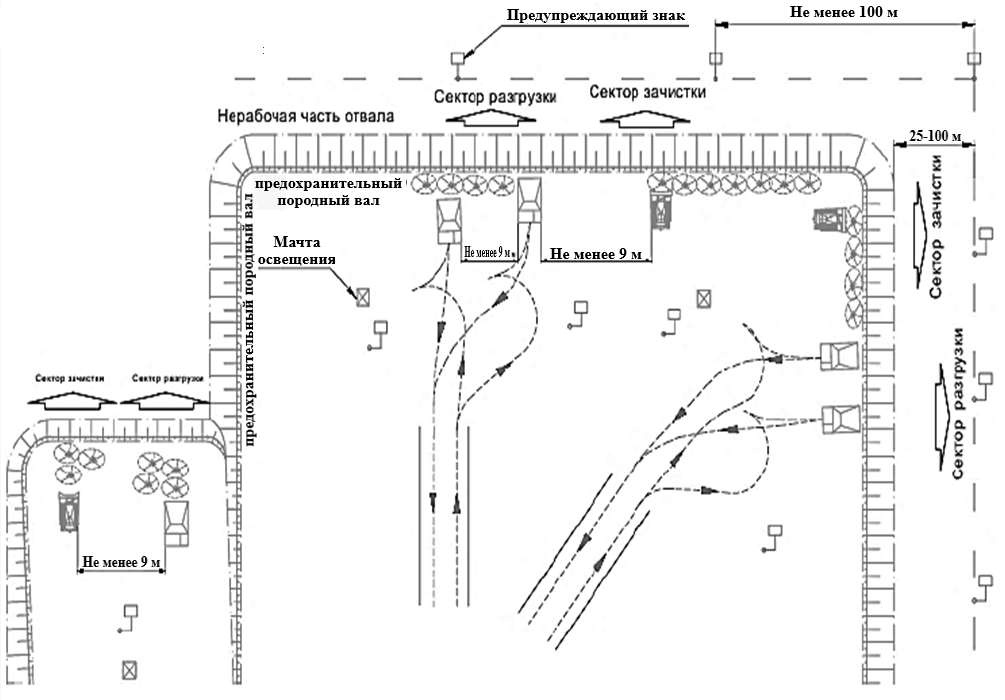
Рис. 8 – Схема отвалообразования и схема движения автосамосвалов на отвале
4.5 Рекультивационные работы
Территория, нарушенная разработками месторождения, представлена карьерными выемками, траншеями, отвалами вскрышных пород, линейными объектами, производственными площадками.
Учитывая природные условия и месторасположение нарушенного участка, а также хозяйственные и социально-экономические условия данного района, принято лесохозяйственное направление рекультивации.
Для восстановления нарушенных земель предусматривается снятие плодородного слоя почвы (ПСП) и потенциально плодородных пород (ППП), в случае наличия, их хранение и дальнейшее использование при рекультивации нарушенных земель. Для размещения снятого объема ПСП и ППП на территории месторождения предусмотрены склады.
Рекультивация осуществляется последовательно в два этапа: первый этап – технический, второй – биологический.
Технический этап рекультивации включает следующие основные операции:
– снос/демонтаж зданий и сооружений;
– грубая и чистовая планировка рекультивируемых участков. Грубая планировка земель предусматривает предварительное выравнивание поверхности с выполнением основного объема земляных работ. Чистовая планировка земель предусматривает окончательное выравнивание поверхности и исправление микрорельефа при незначительных объемах земляных работ;
– освобождение рекультивируемой поверхности от крупногабаритных обломков пород, производственных конструкций и строительного мусора с последующим их захоронением или организованным складированием;
– устройство подъездных путей к рекультивируемым участкам, устройство въездов и дорог на них с учетом прохода сельскохозяйственной, лесохозяйственной и другой техники;
– нанесение потенциально плодородных пород и/или плодородного слоя почвы на рекультивируемые участки.
Свойства вскрышных пород позволяют использовать их для технического этапа рекультивации и собственных нужд предприятия.
Биологическая рекультивация включает в себя работы по восстановлению плодородия нарушенных земель, возвращение в лесное или иное пользование. Результатом биологического этапа рекультивации является окончательное восстановление плодородия и биологической продуктивности нарушенных земель. Для отвала вскрышных пород «Восточный» предусмотрен биологический этап рекультивации путем гидропосева. Посев осуществляется ежегодно по мере формирования каждого яруса отвала, что способствует укреплению откосов и предотвращает пыление и дает возможность в кратчайшие сроки восстановить плодородие нарушенных земель.
1 2 3 4
5 Способ вскрытия месторождения
Карьер характеризуется наличием глубинной и нагорной частей. Вскрытие нагорной части карьера с гор. +1050 м до гор. +735 м произведено внешними автосъездами и поперечными полутраншеями – на склонах и, после создания первоначальной рабочей площадки на горизонте – траншеями полного профиля. Эти траншеи, являющиеся разрезными, проходятся по контакту рудного тела со стороны висячего бока и служат первоначальными горными выработками для дальнейшего развития фронта добычных работ на рабочем уступе.
Глубинная часть карьера с гор. +735 м до дна вскрывается внутренней траншеей c петлевой и спиральной формой трассы.
В соответствии с данной схемой вскрытия с использованием автотранспорта глубинная часть месторождения вскрывается наклонными траншеями внутреннего заложения, которые переходят в разрезные траншеи по достижении принятой высоты уступа. Данные уступы дорабатываются до промежуточных, а затем и конечных контуров [1].
Учитывая значительные размеры карьера (длина – 4,4 км, ширина – 2,0 км), большие годовые объемы горной массы, достигающие порядка 60,0 млн. м3, схема вскрытия предусматривает 5 выездных траншей – две для вывозки руды (годовой объем – 40 млн. т) и три для вскрыши.
Вскрышные выездные траншеи располагаются в торцах и одна на восточном борту карьера. Постоянная автодорога устроена в виде спирально-петлевого съезда (рис.9).
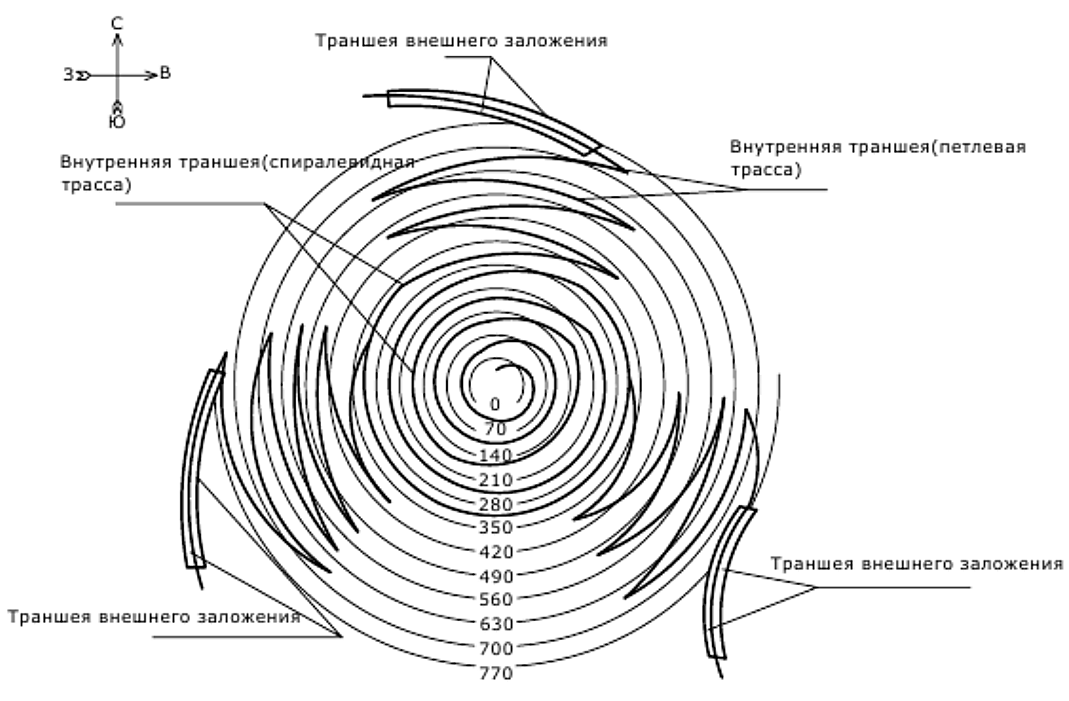
Рис. 9 – Схема вскрытия карьера Наталкинского месторождения
Перспективный план Наталкинского карьера в отработанном виде со схемой вскрытия показан в Приложении 6.
При отработке нагорной части карьера (выше замкнутого контура, до отметки +735 м) проводится вскрытие полутраншеями внешнего и внутреннего заложения, через каждые 15-30 м по вертикали. Полутраншеи примыкают к основной автодороге, по которой осуществляется связь карьера с отвалами и промплощадкой, каждая внешняя полутраншея, примыкающая к карьеру, используется для вскрытия рабочих горизонтов вверх и вниз относительно отметки примыкания к технологической дороге. Вскрытие уступов в рабочей зоне карьера производится посредством временных автомобильных съездов и разрезными траншеями.
Общий уклон спирального съезда – 65‰, уклон отдельных съездов на рабочие горизонты 80‰, горизонтальная длина отдельного съезда 125 м, длина горизонтальных площадок примыкания - 30 м. Положение горных работ на 01.01.2021 г представлено в Приложении 5.
Таблица 11 – Основные параметры карьера первой очереди по состоянию на 01.01.2024г.
Наименование | Ед. измерения | Карьер «Наталкинский» |
Длина | | |
- по поверхности | м | 2320 |
- по дну | м | 155 |
Ширина | | |
- по поверхности | м | 1160 |
- по дну | м | 40 |
Глубина ср. | м | 287 |
Отметка дна карьера | м | +585 |
Высота уступа | м | 15 |
Площадь | | |
- по поверхности | га | 196,0 |
- по дну | га | 0,5 |
Угол откоса бортов карьера | | |
- северный | град. | 31 |
- южный | град. | 29 |
- западный | град. | 32 |
- восточный | град. | 31 |
Объем горной массы | тыс.м3 | 93591 |
- минеральное сырье | тыс.т | 65288 |
- вскрыша | тыс.м3 | 67914 |
Средний коэффициент вскрыши | м3/т | 1,04 |