Файл: Отчет о прохождении третьей производственной (технологической) практики в условиях открытой разработки Наталкинского золоторудного месторождения.docx
Добавлен: 07.11.2023
Просмотров: 540
Скачиваний: 21
ВНИМАНИЕ! Если данный файл нарушает Ваши авторские права, то обязательно сообщите нам.
6 Система разработки месторождения
Система открытой разработки, принятая для карьера «Наталкинский» характеризуется как углубочная продольная двухбортовая с вывозом вскрышных пород во внешние отвалы автосамосвалами.
Горнотехнические условия разработки месторождения и размещение основных объектов инфраструктуры предопределяют общее направление ведения работ сверху вниз, горизонтальными уступами, при выполнении вскрышных и очистных работ продольными и поперечными заходками. Направление развития работ на уступе выбирают с учетом пространственного расположения рудных тел. Вскрышные породы транспортируют во внешние отвалы автосамосвалами. По числу транспортных выходов фронт работ на уступе, как правило, тупиковый. Элементы системы разработки определены в соответствии с требованиями ФНиП в области промышленной безопасности.
Углы откосов рабочих уступов приняты в зависимости от типа пород и их характеристик. В рабочем положении угол откоса уступа может изменяться в пределах 55-80 град. В предельном положении он равен 55 град.
Таблица 12 – Параметры и показатели системы разработки
Параметры и показатели | Ед. измерения | Значения |
Высота уступа | м | |
- рабочего | | 7,5 – 15 |
- нерабочего | | 15 |
Угол откоса уступа | град. | |
- рабочего | | 60-75 |
- временно нерабочего борта | | 60 |
- в предельном положении | | 55 |
Ширина заходки | м | 22 |
Ширина рабочей площадки | м | 50 |
Ширина транспортных берм | м | 35 |
Ширина предохранительных берм | м | 8-40 |
Число рабочих уступов | ед. | 2-3 |
Длина фронта работ на уступе | м | 500-900 |
Время отработки горизонта | мес. | 3-6 |
Скорость углубки по дну карьера | м/год | 30-45 |
Скорость разноса ВНБ | м/год | 30-45 |
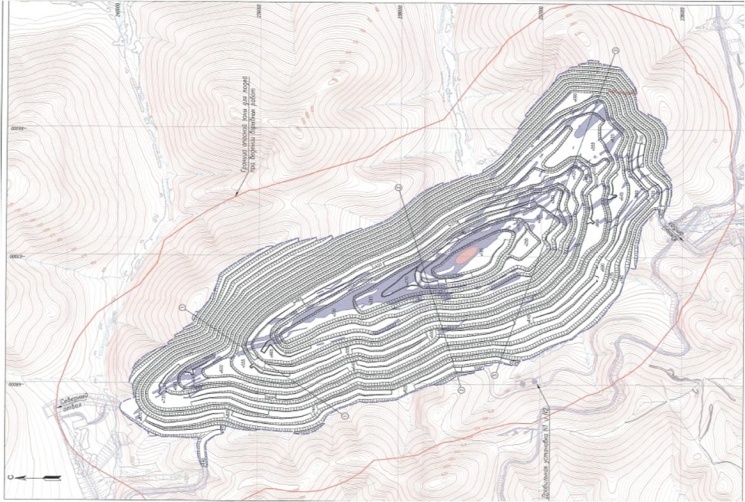
Рис.10 – Общий вид карьера
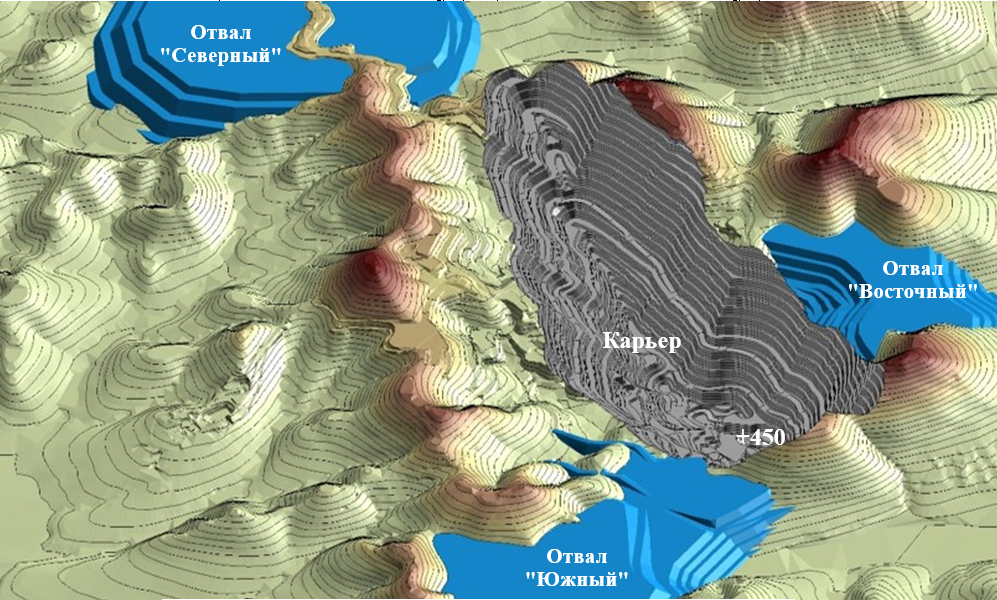
Рис. 11 – Трёхмерная модель месторождения «Наталка»
7 Переработка полезного ископаемого
Рудная залежь отличается преимущественным развитием золото-арсенопирит-анкерит-серицит-альбит-кварцевой ассоциации, для которой характерен диапазон содержания золота 1-200 г/т и серебра – 1-20 г/т; тогда как в надрудных, подрудных и фланговых участках развита кварц-кальцитовая ассоциация, которая отличается низкими содержаниями золота (0,01-0,001 г/т) и повышенными содержаниями серебра (0,1-20 г/т). Золото самородное, относительно крупное (средний размер золотин 0,1–2 мм), высокопробное (730–800 и выше), концентрируется в кварце, а также тонкодисперсное; образует рассеянную вкрапленность в сульфидах, преимущественно в арсенопирите.
К дробильному комплексу № 1 руда из карьера транспортируется автосамосвалами и выгружается через грохотную решётку на дробилку гирационного типа, производительностью 2800 тонн/час. Крупность куска на выходе из дробильного комплекса составляет не более 150 мм. Дробленая руда подается на ЗИФ через промежуточный бункер пластинчатым питателем к магистральному конвейеру № 1, проложенному по рудному тоннелю № 1. Магистральный конвейер № 1 доставляет дробленую руду на золотоизвлекательную фабрику (ЗИФ) с помощью складского конвейера со штабелеукладчиком.
Дробильный комплекс № 2 (ДК2) в составе второй рудной линии ЦПТ будет введён в 2022 году. Его производительность будет составлять 20 млн. тонн руды в год. Состав комплекса буде аналогичен составу дробильного комплекса № 1. ДК2 будет размещён на одной площадке с ДК1. На второй стадии развития рудных ЦПТ первая и вторая линии вводятся из чаши карьера. Каждая линия оборудуется полустационарной дробильной установкой производительностью 20 млн. тонн руды в год, установленной на берме.
В качестве основных исходных данных для разработки основных технологических решений (ОТР) были приняты следующие условия:
– полная мощность предприятия по добыче и переработке руды – 40 млн. т в год;
– количество вводимых в эксплуатацию очередей – 3 (10, +10 и +20 млн. тонн в год по перерабатываемой руде);
– содержание золота в руде с учетом разубоживания – 1,6 г/т;
– влажность крупнодроблёной руды, поступающей на ЗИФ – 5 %;
– конечная продукция – сплав Доре по ТУ 117-2-7-75.
Схема цепи аппаратов включает в себя основные переделы:
-
отделение измельчения; -
отделение гравитации и флотации; -
отделение сгущения хвостов обогащения и оборотного водоснабжения; -
отделение цианирования, сгущения и фильтрации хвостов цианирования; -
отделение десорбции и регенерации угля с участком электролиза; -
отделение сушки и плавки катодных осадков; -
отделение приготовления реагентов.
Результаты исследований по измельчаемости руды Наталкинского месторождения показали, что для достижения крупности материала 75-80% класса минус 0,074 мм необходимо ведение процесса измельчения в две стадии, а при увеличении тонины помола до 95-98% класса минус 0,074 мм – в три стадии измельчения. По данным научно-исследовательских работ для первой стадии рудоподготовки были рекомендованы мельницы полусамоизмельчения с шаровой нагрузкой до 12 % от массы руды.
Проектом предусмотрено двухстадийное измельчение руды с получением кусков размером 150 мм, до 80% от массы. Крупнодробленая руда (150 мм) системой ленточных конвейеров поступает на ЗИФ со склада и подается на I стадию измельчения в мельницы полусамоизмельчения (ПСИ). При разгрузке мельницы первой стадии измельчения продукт направляется на додрабливание в конусную дробилку и возвращается в мельницу ПСИ. Слив с бутары крупностью -25+0 мм в виде пульпы самотеком попадает в зумпф, из которого насосами подается на виброгрохот. Верхний продукт грохота, крупностью +6 мм, возвращается на додрабливание в конусную дробилку мелкого дробления совместно с галью бутары мельницы, а нижний продукт крупностью минус 6 мм направляется в зумпф слива мельницы МШЦ II стадии.
70% пульпы из общего зумпфа мельниц смешивается с хвостами гравитации и верхним продуктом защитных грохотов центробежных концентраторов подаются на классификацию в кластер гидроциклонов. При классификации происходит разделение пульпы по классу 80% -74 мкм. Пески гидроциклонов подаются в мельницу МШЦ второй стадии измельчения.
30% пульпы из общего зумпфа мельниц перекачивается в зумпф центробежных концентраторов и далее подается на защитные грохота, установленные на питании центробежных концентраторов. Подрешетный продукт крупностью минус 1,6 мм подается на центробежные концентраторы с периодической разгрузкой. Хвосты центробежной концентрации сливаются в отдельный зумпф хвостов и далее перекачиваются в общий зумпф мельниц. Первичный гравиоконцентрат через зумпф подается на установку интенсивного цианирования, на которой, после проведения
подготовительных операций по сгущению и стратификации, подвергается цианидному выщелачиванию. Кек процесса цианирования после промывки водой подается в зумпф хвостов центробежных концентраторов, и направляется на доизмельчение. Промывная вода направляется на приготовление цианидных растворов, а её избыток - в первый пачук каскада цианирования флотоконцентрата. Насыщенные по золоту цианидные растворы перерабатываются электролизом на электролизном участке.
Слив гидроциклонов крупностью 80 % класса минус 74 мкм направляют на высокочастотные грохота для отделения щепы. После отделения щепы, пульпа подается в контактный чан, куда добавляется флотомасло (Т-80), растворы соды и бутилового ксантогената натрия. Далее пульпа поступает на флотацию. Флотация проводится в механических и пневмомеханических чановых флотомашинах. Пенный продукт основной флотации через зумпф насосами подается на центробежные концентраторы с периодической разгрузкой. Хвосты с этой операции направляются в питание первой перечистной флотации. Пенный продукт первой перечистной флотации через зумпф поступает на вторую перечистку, пенный продукт второй перечистной флотации направляется на обогащение на свой центробежный концентратор. Хвосты обогащения с этого концентратора направляют на сгущение флотоконцентрата. Пенный продукт контрольной флотации объединяется в зумпфе с песковым продуктом первой перечистной флотации и далее объединенный промпродукт насосами перекачиваются на центробежные концентраторы. Хвосты этой стадии гравитации направляют в голову флотационного передела в контактный чан.
Объединенные сульфидные гравиоконцентраты со всех стадий подаются на установки интенсивного цианирования, где после сгущения подвергаются цианидному выщелачиванию. Насыщенные по золоту цианидные растворы перерабатываются электролизом на электролизном участке, кек цианирования, полученный после окончания процесса, распульповывается обеззолоченным раствором и направляется в головной пачук каскада цианирования в качестве дополнительного питания в угольносорбционное выщелачивание (CIL-процесс).
Угольно-сорбционное выщелачивание проводится в реакторах с добавлением известкового молока и крепкого раствора цианида натрия. Насыщенный по золоту уголь подается на установку десорбции и регенерации, а обезметалленная пульпа сгущается и поступает на фильтрацию. Кек хвостов цианирования вывозится на склад полусухого складирования.
Установка десорбции предназначена для выделения золота в виде цианидного комплекса и восстановления сорбционных свойств угля. Угольная пульпа собирается в баке, где отстаивается. Жидкая фаза сливается, а оставшийся уголь промывается сначала чистой водой, затем соляной кислотой, после чего снова водой, а в последнюю очередь раствором едкого натра. Уголь в виде пульпы передается в колонну десорбции. Богатый раствор, выходящего из десорбции, направляется на участок электролиза для выделения катодного осадка.
Катодный осадок в виде пульпы, выгружается на фильтр. Отфильтрованный и промытый на фильтре водой катодный осадок золота передают в плавильное отделение для дальнейшей сушки и плавки с получением слитков сплава Доре по ТУ 117-2-7-75.
8 Рациональное использование минерального сырья
Принятый открытый способ разработки позволяет исключить выборочную отработку месторождения, а также включить в добычу часть руды, отнесенной к забалансовой.
Эксплуатационные потери при извлечении минерального сырья из недр в период отработки запасов c 2021 по 2023 год (включительно) на месторождении «Наталка» в связи вовлечением в отработку дополнительных горизонтов и корректировкой объемов извлечения минерального сырья составят 2,2 % или 1358 тыс. т, разубоживание – 7,8 % или 5113 тыс. т.
В целом, при отработке всех учтенных Госбалансом запасов 1-ой и 2-ой очередей эксплуатационные потери составят 2,3% (14923 тыс. т), разубоживание – 8,2 % (56224 тыс. т) (табл. 13).
Таблица 13 – Сводная таблица эксплуатационных потерь и разубоживания при извлечении минерального сырья из недр
Наименование показатели | Значения показателей |
Балансовые запасы: | |
Объем, тыс. т | 641538 |
Среднее содержание золота, г/т | 1,708 |
Масса золота, кг | 1095866 |
Среднее содержание серебра, г/т | 0,478 |
Масса серебра, кг | 306,6 |
Эксплуатационные потери, тыс. т (%) | 14923 (2,3 %) |
Разубоживание, тыс. т (%) | 56224 (8,2 %) |
Извлекаемое из недр минеральное сырье: | |
Объем, тыс. т | 682839 |
Среднее содержание золота, г/т | 1,584 |
Масса золота, кг | 1081906 |
Среднее содержание серебра, г/т | 0,443 |
Масса серебра, кг | 302,5 |