Файл: Вариант 6 Задание 1 Приведите схемы обработки поверхностей 1, 2, 3 детали, чертеж которой дан на рисунке Для каждой схемы укажите название станка, инструмента и приспособления..docx
ВУЗ: Не указан
Категория: Не указан
Дисциплина: Не указана
Добавлен: 07.11.2023
Просмотров: 200
Скачиваний: 6
ВНИМАНИЕ! Если данный файл нарушает Ваши авторские права, то обязательно сообщите нам.
Вариант 6
Задание №1
Приведите схемы обработки поверхностей 1, 2, 3 детали, чертеж которой дан на рисунке 1. Для каждой схемы укажите название станка, инструмента и приспособления. Приведите эскизы инструмента для обработки поверхности 1 и приспособления для закрепления заготовки при обработке поверхности 3.
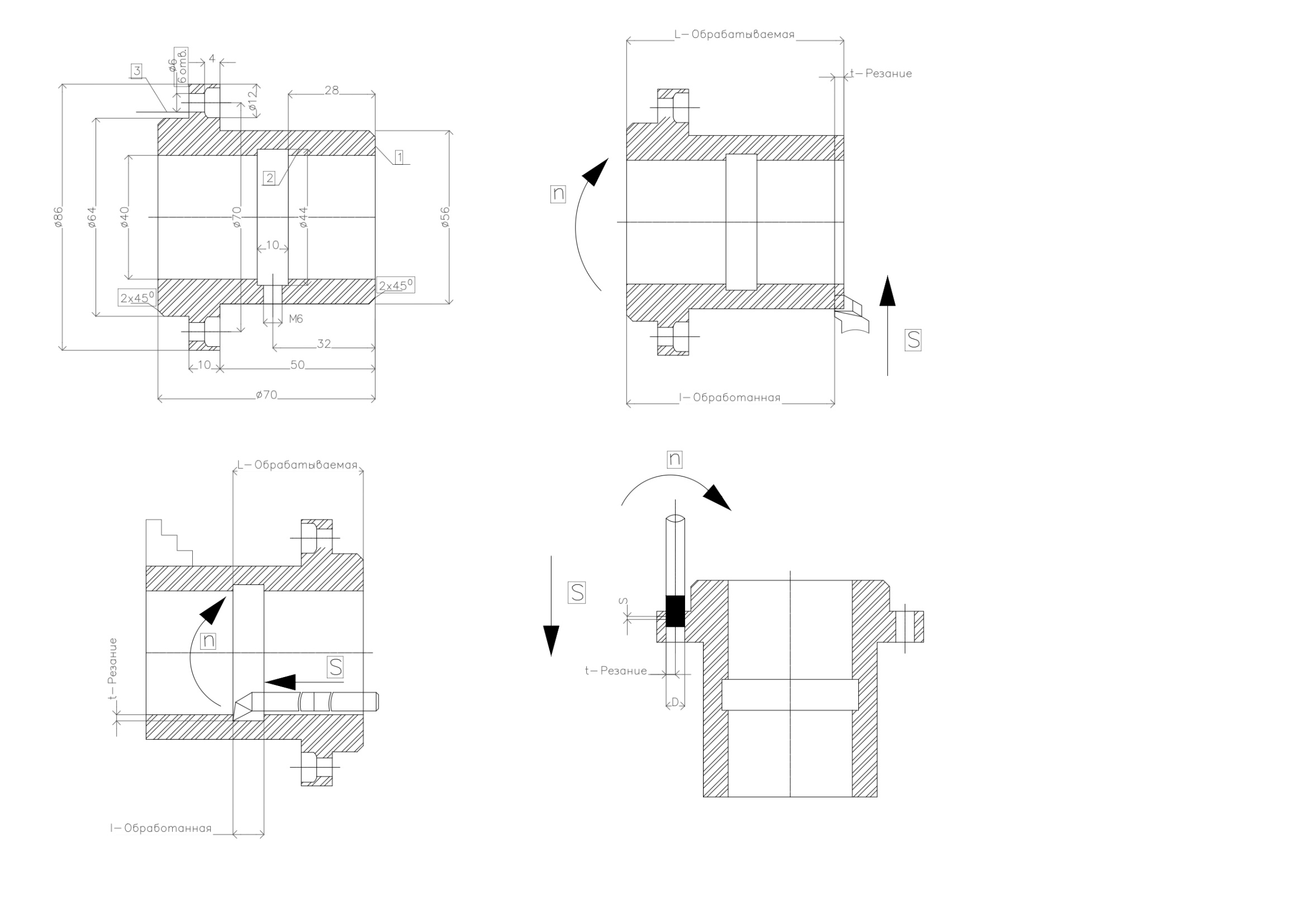
Рисунок 1 - Чертеж детали
Так как деталь является телом вращения, то поверхности 1 и 2 обрабатываются на токарном станке.
Выбираем станок 16К20Ф3. Буквенно-цифирный индекс станка 16К20Ф3 обозначает следующее: цифра 1 - это токарный станок; цифра 6 - обозначает токарно-винторезный станок, буква К - поколение станка, цифра 20 - высота центров (200 мм). Наличие «Ф3» в конце индекса говорит о наличии ЧПУ - числового программного управления. Станок представлен на рисунке 2.
Станок предназначен для токарной обработки в автоматическом режиме наружных и внутренних поверхностей деталей типа тел вращения со ступенчатым и криволинейным профилем различной сложности по заранее составленной управляющей программе. Обработка происходит в один или несколько проходов в замкнутом автоматическом цикле. Установка заготовок осуществляется в патроне, а длинных - в центрах. Область применения станка: мелкосерийное и серийное производство.
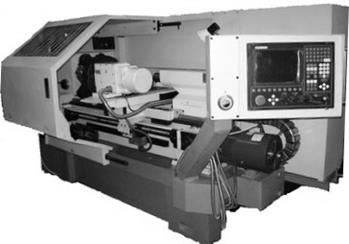
Рисунок 2 - Станок 16К20Ф3
Таблица 1 – Технические характеристики
| |
Технические характеристики | Параметры |
Диаметр обработки над станиной, мм | 500 |
Диаметр обработки над суппортом, мм | 200 |
Наибольшая длина обработки, 6-позиционная головка, мм | 900 |
Наибольшая длина обработки, 8-позиционная головка, мм | 750 |
Наибольшая длина обработки, 12-позиционная головка, мм | 850 |
Наибольшая длина обработки в центрах, мм | 1000 |
Диаметр цилиндрического отверстия в шпинделе, мм | 55 |
Наибольший поперечный ход суппорта, мм | 210 |
Наибольший продольный ход суппорта, мм | 905 |
Максимальная рекомендуемая скорость продольной рабочей подачи, мм | 2000 |
Максимальная рекомендуемая скорость поперечной рабочей подачи, мм | 1000 |
Количество управляемых координат, шт. | 2 |
Количество одновременно управляемых координат, шт. | 2 |
Дискретность задания перемещения, мм | 0,001 |
Пределы частот вращения шпинделя, мин-1 | 20 - 2500 |
Скорость быстрых перемещений суппорта - поперечного, мм/мин | 2 400 |
Максимальная скорость быстрых продольных перемещений, мм/мин | 15000 |
Максимальная скорость быстрых поперечных перемещений, мм/мин | 7500 |
Количество позиций инструментальной головки | 8 |
Мощность электродвигателя главного движения, кВт | 11 |
Класс точности по ГОСТ 8-82 | П |
Габаритные размеры станка (Д х Ш х В), мм | 3700 Ч 2260 Ч 1650 |
Масса станка, кг | 4000 |
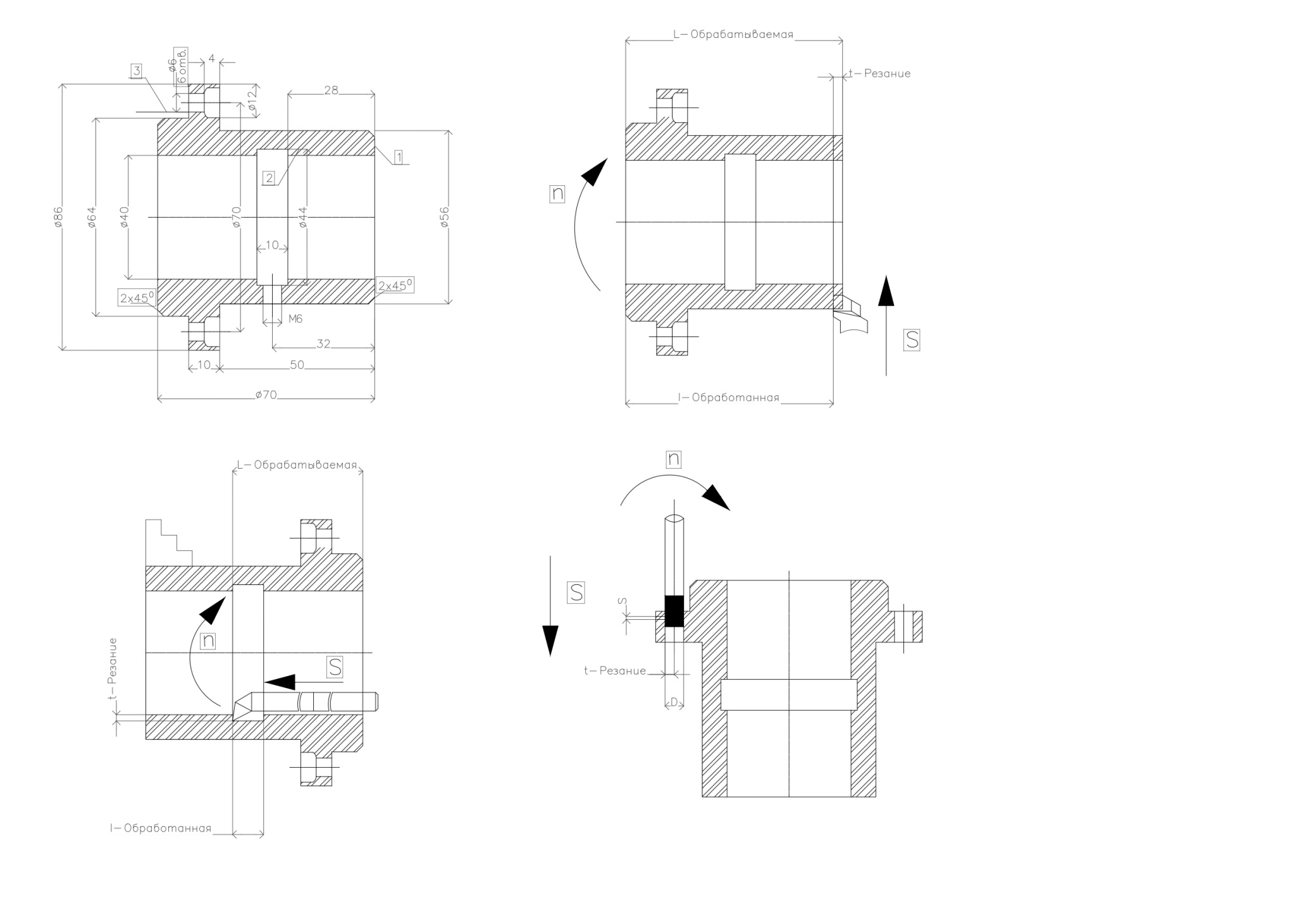
Рисунок 3 - Схема резания торцевой поверхности 1
L - обрабатываемая поверхность, l - обработанная поверхность, t - плоскость резания.
Для осуществления процесса резания при токарной обработке необходимо иметь два одновременно действующих рабочих движения, одно из которых вращательное, а второе - поступательное. Вращение обрабатываемой заготовки называется главным движением - движением резания. Поступательное перемещение инструмента называют движением подачи
Торцы и уступы обрабатывают подрезными, проходными отогнутыми или проходными упорными резцами.
С учетом материала детали - спец. чугун СЧ 20 применяем резец подрезнойой по ГОСТ 18897-73 из быстрорежущей стали ВК8; Н=25мм; В=16мм; r =1мм. Геометрические параметры режущей части гс =12…180; б0 = 8…120; л0=-4…+40; ц=300.
Подрезной резец предназначен для обработки наружных торцовых поверхностей. При подрезании торца движение подачи резца осуществляется перпендикулярно к оси обрабатываемой заготовки. Подрезной резец позволяет обрабатывать различные торцовые и другие поверхности с продольным и поперечным движениями подачи.
Для крепления детали используем самоцентрирующийся 3-х кулачковый патрон. самоцентрирующийся 3-х кулачковый токарные патроны из стали и чугуна предназначены для установки на универсальные токарные, револьверные, внутришлифовальные станки, делительные головки и различные приспособления. Представлен на рисунке 4.
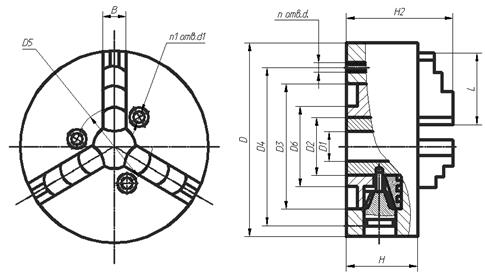
Рисунок 4 - Самоцентрирующийся 3-х кулачковый токарный патрон
Поверхность 2 (Рисунок 5) выполняется так же на токарном станке 16К20Ф3. В качестве приспособления применяется самоцентрирующийся 3-х кулачковый токарный патрон. В качестве режущего инструмента расточной резец.
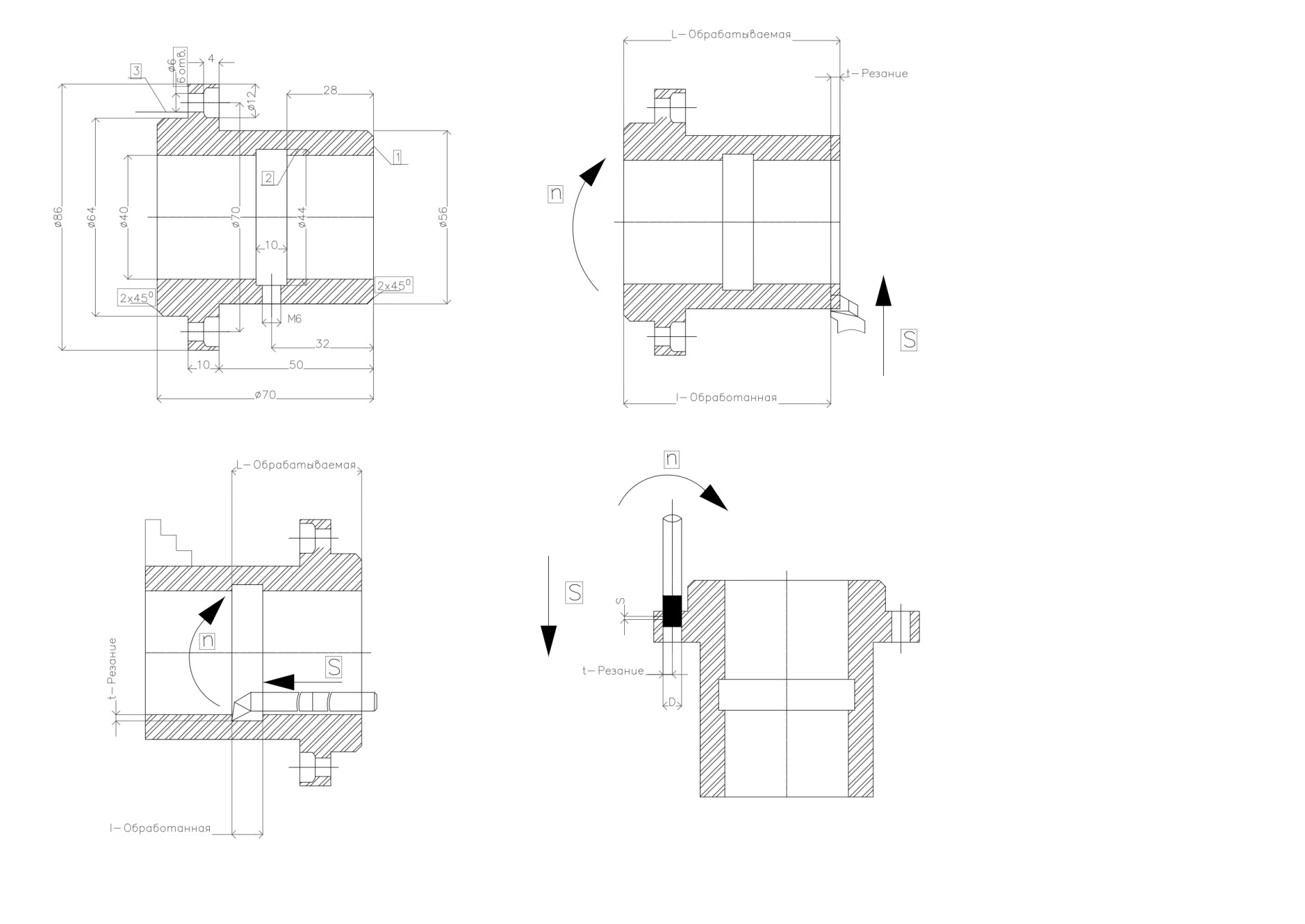
Рисунок 5 - Схема резания поверхности 2
Заданную глубину отверстия обеспечивают в процессе растачивания измерением линейкой, штанген-глубиномером, шаблоном или настройкой при помощи лимбапродольной подачи. Для облегчения обработки на резце наносят риску,соответствующую заданной глубине отверстия.
Точность диаметра растачиваемого отверстия обеспечивается так же, как и при наружном точении: пробными проходами с замером штангенциркулем, настройкой по лимбу поперечной подачи, по линейке поперечных салазок суппорта, при помощи индикатора, по поперечному упору.
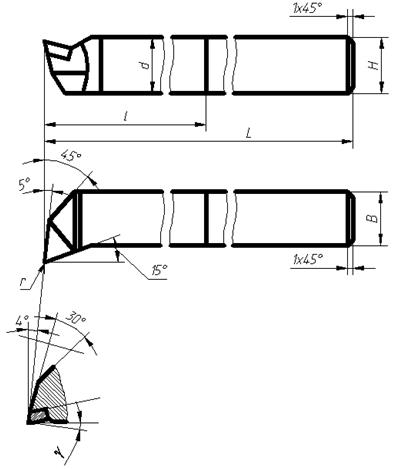
Рисунок 6 - Эскиз расточного резца
Обработку поверхности 3 выполняем путем сверления на сверлильном станке.
Сверлильный станок с ЧПУ модели 2Р135Ф2-1
-
- Наибольший условный диаметр сверления в стали 35 -
- Рабочая поверхность стола 400x710 -
- Число скоростей шпинделя 12 -
- Частота вращения шпинделя, мин-1 45-2000 -
- Число подач шпинделя (револьверной головки) 18 -
- Подача шпинделя, мм/мин 10- 500 -
- Мощность, кВт 3,7
На сверлильном станке с ЧПУ базой служит торец детали и центральное отверстие. Деталь устанавливается на оправке и закрепляется специальным приспособлением.
Для обработки отверстий на сверлильном станке с ЧПУ применяются следующие режущие инструменты:
-
- сверло спиральное Ш5мм с коническим хвостовиком ГОСТ 886-77, -
- L = 132мм, 1= 87мм Р6М5;
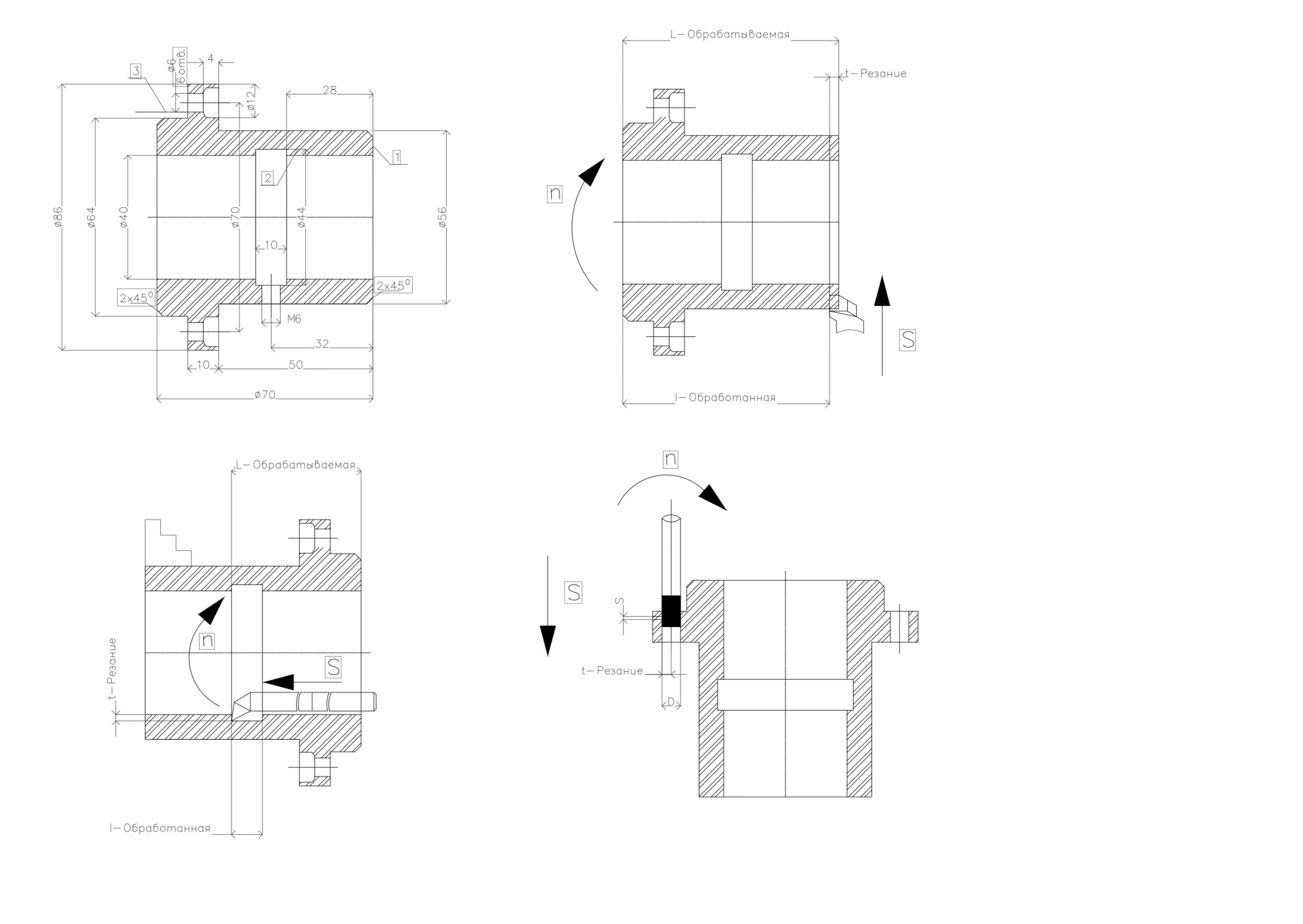
Рисунок 7 - Схема резания поверхности 3.
Задание №2
Приведите схемы, опишите физическую сущность, назначение и область применения электроискрового и электроимпульсного методов обработки.
Электроискровая обработка
Схема электроискрового станка представлена на рисунке 1.
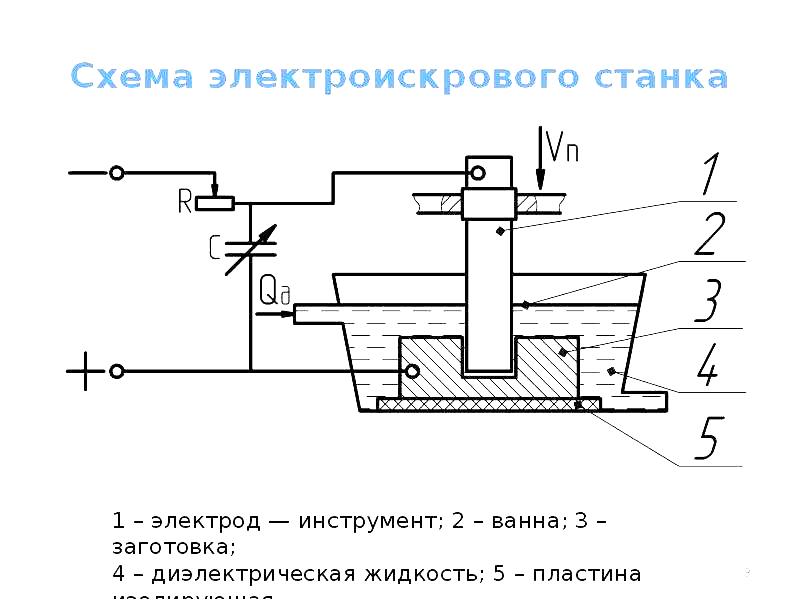
Рисунок 1 - Схема электроискрового станка:
1 – электрод-инструмент; 2 – ванна; 3 – заготовка-электрод; 4 – диэлектрическая жидкость; 5 – изолятор
При электроискровой обработке – используют импульсные искровые разряды между
электродами ( обрабатываемая заготовка (анод) – инструмент (катод)).
Конденсатор


от источника постоянного тока напряжением 100…200 В. Когда напряжение на электродах 1 и 3 достигает пробойного образуется канал, через который осуществляется искровой разряд энергии, накопленной конденсатором.
Продолжительность импульса 20…200 мкс.
Точность обработки до 0,002 мм,

Для обеспечения непрерывности процесса ( зазор =const) станки снабжаются следящей системой и системой автоматической подачи инструмента.
Получают сквозные отверстия любой формы поперечного сечения, глухие отверстия и полости, отверстия с криволинейными осями, вырезают заготовки из листа, выполняют плоское, круглое и внутреннее шлифование.
Изготовляют штампы и пресс-формы, фильеры, режущий инструмент.
Схемы электроискровой обработки представлены на рисунке 2.
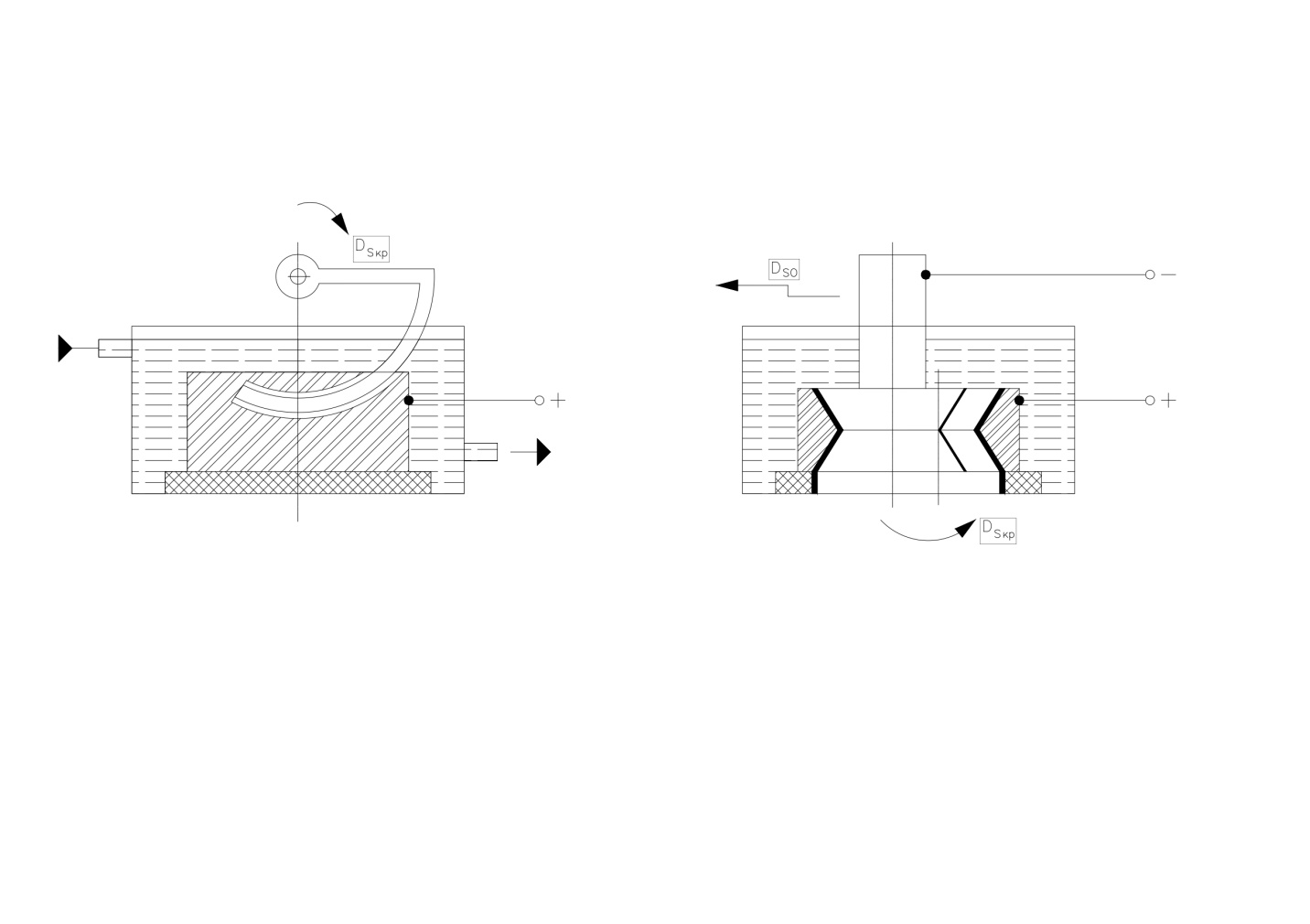
Рисунок 2 - Схемы электроискровой обработки:
а – прошивание отверстия с криволинейной осью; б – шлифование внутренней поверхности фильеры
Электроискровую обработку применяют для упрочнения поверхностного слоя металла. На поверхность изделия наносят тонкий слой металла или композиционного материала. Подобные покрытия повышают твердость, износостойкость, жаростойкость, эрозионную стойкость и так далее.
Электроимпульсная обработка
При электроимпульсной обработке используют электрические импульсы большой длительности (5…10 мс), в результате чего происходит дуговой разряд.
Большие мощности импульсов от электронных генераторов обеспечивают высокую производительность обработки.
Электроимпульсную обработку целесообразно применять при предварительной обработке штампов, турбинных лопаток, фасонных отверстий в детали из коррозионно-стойких и жаропрочных сплавов.
Схема обработки показана на рисунке 3.
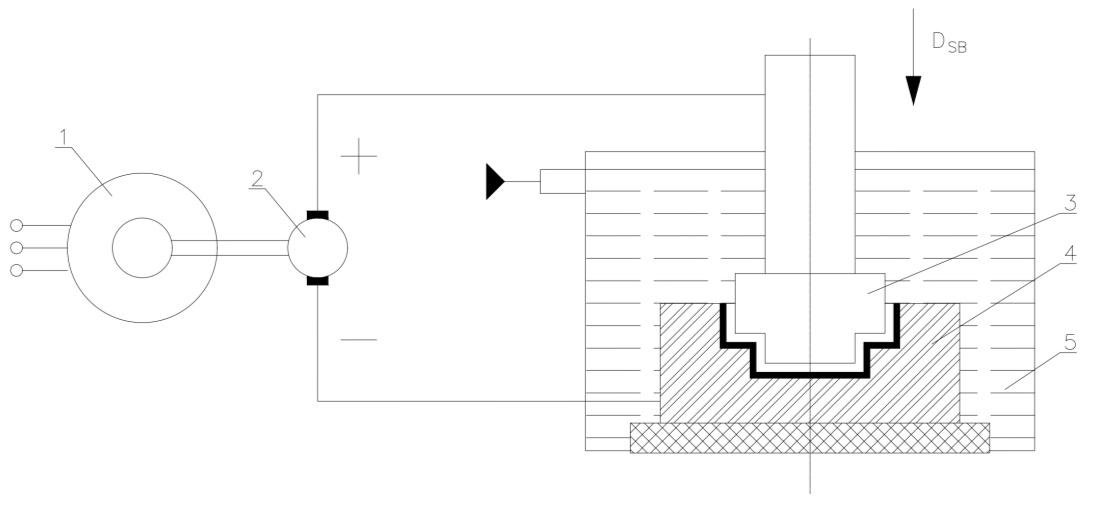
Рисунок 3 - Схема электроимпульсной обработки:
1 – электродвигатель; 2 – импульсный генератор постоянного тока; 3 – инструмент-электрод; 4 – заготовка-электрод; 5 – ванна.
Электроконтактная обработка.
Электроконтактная обработка основана на локальном нагреве заготовки в месте контакта с электродом-инструментом и удалении размягченного или расплавленного металла из зоны обработки механическим способом: относительным движением заготовки или инструмента.
Источником теплоты служат импульсные дуговые разряды.
Этот вид обработки рекомендуется для крупных деталей из углеродистых и легированных сталей, чугуна, цветных сплавов, тугоплавких и специальных сплавов ( Рисунок 4).
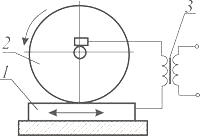
Рисунок 4 - Схема электроконтактной обработки плоской поверхности:
1 – обрабатываемая заготовка; 2 – инструмент-электрод; 3 – трансформатор
Этот метод применяют для зачистки отливок от заливов, отрезки литниковых систем, зачистки проката, шлифования коррозионных деталей из труднообрабатываемых сплавов.