Файл: Программа выпуска, установка типа производства 5 Выбор вида заготовки. Назначение припусков 5.docx
ВУЗ: Не указан
Категория: Не указан
Дисциплина: Не указана
Добавлен: 09.11.2023
Просмотров: 24
Скачиваний: 1
ВНИМАНИЕ! Если данный файл нарушает Ваши авторские права, то обязательно сообщите нам.
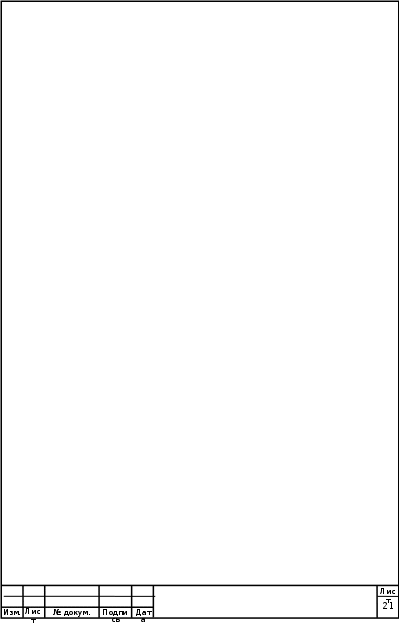
Содержание
Введение 3
1. Анализ рабочего чертежа. Условий производства 4
2. Программа выпуска, установка типа производства 5
3. Выбор вида заготовки. Назначение припусков 5
4. Выбор плана обработки 5
5. Выбор оборудования и оснастки 6
6. Выбор режимов резания 7
Заключение 16
Список литературы 17
Введение
По программе раздела: "Обработка материалов резанием, должен быть разработан процесс:
-
по виду - единичный, т.е. технологический процесс, относящийся к изделиям одного наименования, типоразмера и исполнения независимо от типа производства; -
по степени детализации содержания - маршрутно-операционный.
Разработка технологического процесса изготовления детали включает в себя:
-
Анализ рабочего чертежа детали, условий производства. -
Определение программы выпуска, установление типа производства. -
Выбор вида заготовки. Назначение припусков. -
Установление плана и методов механической обработки. -
Разработку операций (выбор станочного оборудования, приспособлений, режущего и измерительного инструмента, назначение режима резания для каждого перехода, определение нормы времени). -
Оформление документации технологического процесса.
1. Анализ рабочего чертежа. Условий производства
Основными исходными материалами для разработки технологического процесса изготовления детали являются рабочий чертеж самой детали, производственная программа ее выпуска и сведения о наличном оборудовании в мастерской предприятия или цехах ремонтного завода.
Рабочий чертеж детали должен содержать полные данные о материале и термообработке, шероховатости поверхностей и все необходимые размеры.
При анализе рабочего чертежа детали, прежде всего, нужно установить наиболее точные поверхности и размеры, обеспечение заданной точности которых представляет наибольшую сложность и важность. Решающее влияние на перечень и последовательность операций может оказать твердость детали, указанная на чертеже. При сравнительно невысокой твердости (НВ ≤ 350) требуемую по черте
жу точность и шероховатость в большинстве случаев можно обеспечить обработкой резцом, фрезой, протяжкой и разверткой, т.е. лезвийными инструментами. При большей твердости рабочих поверхностей (НВ ≥ 350, HRC ≥ 35) токарные, фрезерные или другие операции проводятся до окончательной термообработки (закалки с отпуском), после чего требуются отделочные операции: шлифование, полирование, доводка, и др.
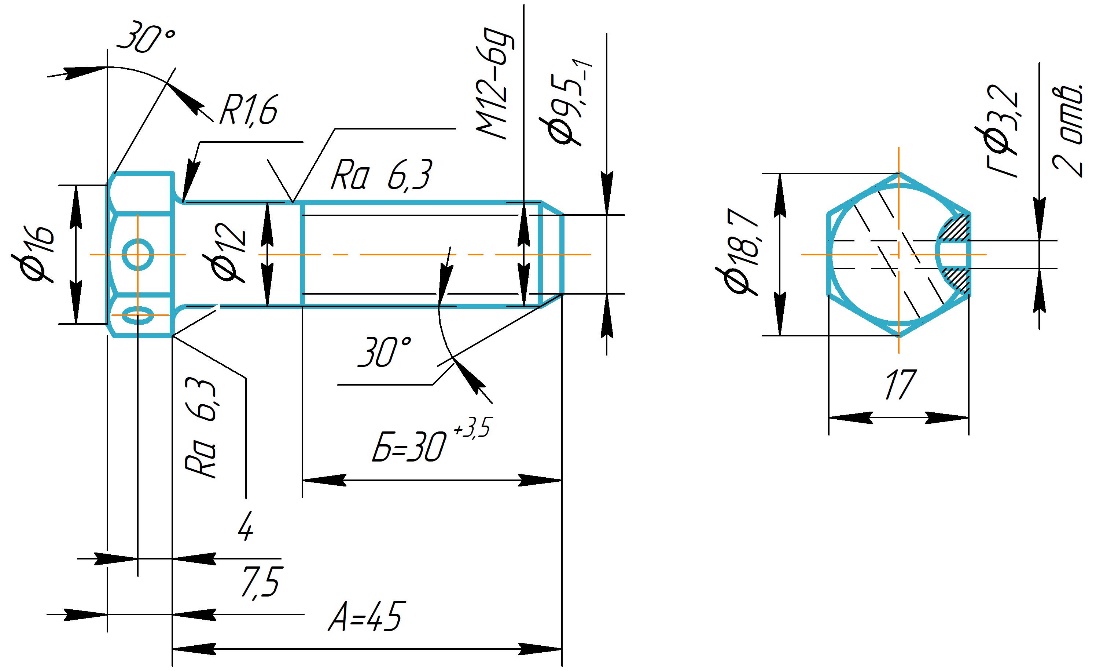
Рис. 1.1 Исходное задание
2. Программа выпуска, установка типа производства
Производство единичное (индивидуальное), форма выполнения маршрутно-операционный процесс.
3. Выбор вида заготовки. Назначение припусков
Заготовка: сталь горячекатаная круглая
Ø 20 ГОСТ 2590-71
L= 56,5 мм (длина заготовки) L=52,5+4=56,5 мм
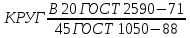
4. Выбор плана обработки
005. ЗАГОТОВИТЕЛЬНАЯ
1. Установить заготовку в зажиме станка;
2. Отрезать заготовку Ø20, L=56,5 мм.
010. ТОКАРНАЯ
1. Закрепить заготовку в трехкулачковый патрон;
2. Точить заготовку Ø20 до Ø18,7;
3. Подрезать торец Ø18,7 в размер 54,5 мм;
4. Перезакрепить заготовку;
5. Подрезать торец Ø18,7 в размер 52,5 мм окончательно;
6. Точить заготовку Ø12 на l = 45 мм;
9. Снять 2 фаски 2х45°
015. ФРЕЗЕРНАЯ
1. Закрепить заготовку в тиски на поворотном столе;
2. Фрезеровать скругление R15
3. Фрезеровать края заготовки шириной 3 мм с двух сторон, скос у основания 30°.
4. Фрезеровать центр заготовки шириной 8 мм, скос у основания 30°.
020. СВЕРЛИЛЬНАЯ
1. Закрепить заготовку в тиски на поворотном столе;
2. Сверлить 2 сквозных отверстия Ø12 на отступ от края 15 мм
025. КОНТРОЛЬНАЯ
1. Произвести контрольные измерения.
5. Выбор оборудования и оснастки
005. ОБОРУДОВАНИЕ:
Механическая ножовка 8Б72.
ПРИСПОСОБЛЕНИЕ:
Тиски механические станочные специальные, линейка металлическая.
010. ОБОРУДОВАНИЕ:
Токарный станок 16К20.
ПРИСПОСОБЛЕНИЯ:
Патроны: 3-х кулачковый;
РЕЖУЩИЕ ИНСТРУМЕНТЫ:
Резцы: Проходной отогнутый;
Штангенциркуль ШЦ-1, 150-0,1, ГОСТ 160-80.
015. ОБОРУДОВАНИЕ:
Вертикально-фрезерный станок 6Р12.
ПРИСПОСОБЛЕНИЯ:
Тиски механические станочные специальные
РЕЖУЩИЕ ИНСТРУМЕНТЫ:
Фреза дисковая мелкозубая. Фреза кромочная.
Штангенциркуль ШЦ-1, 150-0,1, ГОСТ 160-80.
020. ОБОРУДОВАНИЕ:
Вертикально-сверлильный станок 2Н135.
ПРИСПОСОБЛЕНИЯ:
Тиски механические станочные специальные
РЕЖУЩИЕ ИНСТРУМЕНТЫ:
Сверло спиральное Ø12 мм;
Штангенциркуль ШЦ-1, 150-0,1, ГОСТ 160-80.
025. ОБОРУДОВАНИЕ:
Круглошлифовальный станок 3М151
ПРИСПОСОБЛЕНИЯ:
Тиски механические станочные специальные
РЕЖУЩИЕ ИНСТРУМЕНТЫ:
Круг шлифовальный ГОСТ 2424-83
Эталон (образец) шероховатости ГОСТ 9378-93
6. Выбор режимов резания
010. Переход 2.
Принимаем резец токарный проходной отогнутый правый. Материал пластины Т15К6 [14, с. 149]. Материал державки - сталь 45, сечение державки резца НхВ=25х16, R=1mm ГОСТ 18879-73 [2, с. 112].
Геометрические параметры резца: форма передней поверхности: плоская с фаской [1, с. 27]. γ = 10°, α =8°, λ = 0, φ = 45°, φ1 = 45°.
Назначаем режимы резания.
1. Устанавливаем глубину резания при снятии припуска за один проход: t=n=2мм.
2. Назначаем подачу [1, стр.147 табл. 10,25] S = 0,35 - 0,6. Принимаем максимальную и корректируем по паспорту станка Sл=0,4 мм/об.
3. Назначаем период стойкости резца при одноинструментной обработке Т=50 мм [2, с. 42].
4. Определяем скорость резания, допускаемую режущими свойствами резца. Выбираем скорость резания [2, табл. 7.8] V, = 167 м/мин, умножаем табличную скорость на поправочные коэффициенты [2, табл. 7.9] К1 = 1; К2 = 0,88; К3 = 0,8; К4 = 1; К5 = 1.
V = 167∙1∙0,88∙0,8∙1∙1 = 126,7 м/мин.
5. Частота вращения шпинделя, соответствующая найденной скорости резания:

Корректируем частоту вращения шпинделя по паспортным данным и устанавливаем действительную частоту вращения nД =1200 мин-1 [2, табл. 1.1].
6. Действительная скорость резания:

7. Мощность, затрачиваемая на резание:

PZ = Cp∙t∙S0,75 = 2000∙5∙0,5 = 5000 Н
СР=2000 [2, табл. 4.1].
Мощность двигателя станка NД = 10кВт, КПД станка η = 0,75, тогда мощность на шпинделе составит Nшп = NД∙0,75 = 10∙0,75 =7,5 кВт.
8. Основное время
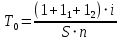
Длина прохода резца:
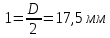
Величина врезания: l1 = t∙ctg φ = 2∙1 = 2 мм.
Перебег принимаем равным: 12 = 0,5∙2 = 1 мм

Переход 3.
Принимаем резец токарный проходной отогнутый правый. Материал пластины Т15К6 [14, с. 149]. Материал державки - сталь 45, сечение державки резца НхВ=25х16, R=1mm ГОСТ 18879-73 [2, с. 112].
Геометрические параметры резца: форма передней поверхности: плоская с фаской [1, с. 27]. γ = 10°, α =8°, λ = 0, φ = 45°, φ1 = 45°.
Назначаем режимы резания.
1. Устанавливаем глубину резания при снятии припуска за один проход: t=n=4мм.
2. Назначаем подачу [1, стр.147 табл. 10,25] S = 0,35 - 0,6. Принимаем максимальную и корректируем по паспорту станка Sл=0,4 мм/об.
3. Назначаем период стойкости резца при одноинструментной обработке Т=50 мм [2, с. 42].
4. Определяем скорость резания, допускаемую режущими свойствами резца. Выбираем скорость резания [2, табл. 7.8] V, = 167 м/мин, умножаем табличную скорость на поправочные коэффициенты [2, табл. 7.9] К1 = 1; К2 = 0,88; К3 = 0,8; К4 = 1; К5 = 1.
V = 167∙1∙0,88∙0,8∙1∙1 = 126,7 м/мин.
5. Частота вращения шпинделя, соответствующая найденной скорости резания:

Корректируем частоту вращения шпинделя по паспортным данным и устанавливаем действительную частоту вращения nД =1200 мин-1 [2, табл. 1.1].
6. Действительная скорость резания:

7. Мощность, затрачиваемая на резание:

PZ = Cp∙t∙S0,75 = 5000∙5∙0,5 = 5000 Н
СР=2000 [2, табл. 4.1].
Мощность двигателя станка NД = 10кВт, КПД станка η = 0,75, тогда мощность на шпинделе составит Nшп = NД∙0,75 = 10∙0,75 =7,5 кВт.
8. Основное время
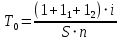
Длина прохода резца:

Величина врезания: l1
= t∙ctg φ = 4∙1 = 4 мм.
Перебег принимаем равным: 12 = 0,5∙4 = 2 мм
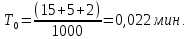
Переход 5.
Принимаем резец токарный проходной отогнутый правый. Материал пластины Т15К6 [14, с. 149]. Материал державки - сталь 45, сечение державки резца НхВ=25х16, R=1mm ГОСТ 18879-73 [2, с. 112].
Геометрические параметры резца: форма передней поверхности: плоская с фаской [1, с. 27]. γ = 10°, α =8°, λ = 0, φ = 45°, φ1 = 45°.
Назначаем режимы резания.
1. Устанавливаем глубину резания при снятии припуска за один проход: t=n=5мм.
2. Назначаем подачу [1, стр.147 табл. 10,25] S = 0,35 - 0,6. Принимаем максимальную и корректируем по паспорту станка Sл=0,4 мм/об.
3. Назначаем период стойкости резца при одноинструментной обработке Т=50 мм [2, с. 42].
4. Определяем скорость резания, допускаемую режущими свойствами резца. Выбираем скорость резания [2, табл. 7.8] V, = 167 м/мин, умножаем табличную скорость на поправочные коэффициенты [2, табл. 7.9] К1 = 1; К2 = 0,88; К3 = 0,8; К4 = 1; К5 = 1.
V = 167∙1∙0,88∙0,8∙1∙1 = 126,7 м/мин.
5. Частота вращения шпинделя, соответствующая найденной скорости резания:

Корректируем частоту вращения шпинделя по паспортным данным и устанавливаем действительную частоту вращения nД =1200 мин-1 [2, табл. 1.1].
6. Действительная скорость резания:

7. Мощность, затрачиваемая на резание:

PZ = Cp∙t∙S0,75 = 5000∙5∙0,5 = 5000 Н
СР=2000 [2, табл. 4.1].
Мощность двигателя станка NД = 10кВт, КПД станка η = 0,75, тогда мощность на шпинделе составит Nшп = NД∙0,75 = 10∙0,75 =7,5 кВт.
8. Основное время

Длина прохода резца:

Величина врезания: l1 = t∙ctg φ = 4∙1 = 5 мм.
Перебег принимаем равным: 12 = 0,5∙4 = 2 мм
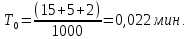
Переход 6.
Принимаем резец токарный проходной отогнутый правый. Материал пластины Т15К6 [14, с. 149]. Материал державки - сталь 45, сечение державки резца НхВ=25х16, R=1mm ГОСТ 18879-73 [2, с. 112].
Геометрические параметры резца: форма передней поверхности: плоская с фаской [1, с. 27]. γ = 10°, α =8°,