Файл: Курсовой проект по дисциплине Насосы и перекачивающие станции.docx
ВУЗ: Не указан
Категория: Не указан
Дисциплина: Не указана
Добавлен: 09.11.2023
Просмотров: 194
Скачиваний: 12
ВНИМАНИЕ! Если данный файл нарушает Ваши авторские права, то обязательно сообщите нам.
1.3 ТОР система вентиляции
Периодичность и объем ТОР систем вентиляции приведены в таблице 3.
Таблица 3 – Периодичность и объем ТОР систем вентиляции
Объем работ | Периодичность выполнения работ |
1 | 2 |
1 Вентиляционные камеры, шахты забора и выброса воздуха | |
2 ТО | |
2.1 Проверка плотности соединений переходов от вентилятора в камеру, состояния мест прохода шахт через кровлю | 1 раз в 3 месяца |
2.2 Проверка состояния сеток, жалюзийных решеток и зонтов над шахтами | |
2.3 Очистка сеток и жалюзийных решеток на шахтах | |
2.4 Проверка герметичности строительных конструкций шахт, тепловой и звуковой изоляции, общего состояния шахт | |
2.5 Проверка болтовых креплений | |
2.6 Проверка состояния фундаментов | |
2.7 Осмотр опорных конструкций (выявление вмятин, пробоин, коррозии; проверка качества окраски) | |
3 ТР | |
3.1 Работы в объеме ТО, а также указанные ниже | 1 раз в 12 месяцев |
3.2 Подтягивание соединений с заменой болтов (при ослаблении и наличии дефектов) | |
3.3 Замена неисправных сеток и жалюзийных решеток в шахтах | |
3.4 Восстановление антикоррозионного покрытия элементов | |
4 КР | |
4.1 Работы в объеме ТР, а также указанные ниже | По результатам технического диагностирования |
4.2 Ремонт вентиляционных камер, шахт забора и выброса воздуха | |
5 Вентиляторы | |
6 ТО | |
6.1 Замер переносным прибором вибрации на подшипниковых опорах и фундаментных болтах (при креплении без амортизаторов) до и после ремонтов | 1 раз в 3 месяца |
6.2 Проверка состояния кожуха и соединений отдельных его элементов (выявление вмятин, пробоин, прокорродировавших мест) | |
6.3 Смазка подшипников | 1 раз в 3 месяца |
6.4 Проверка состояния муфт, валов, ременной передачи (натяжение ремней), посадки шкива на валу, правильности направления вращения рабочего колеса на валу | |
6.5 Проверка правильности взаимного расположения электродвигателя и вентилятора (при ременной передаче), а также горизонтальности установки вентилятора на фундаменте или площадке | |
6.6 Подтяжка креплений вентиляторов | |
6.7 Проверка фиксаторов положения дросселей, шиберов | |
6.8 Проверка состояния мягких вставок, виброоснований вентиляторов и целостности рамы вентилятора, внешнее состояние заземления | |
6.9 Кратковременное включение редко используемых и резервных вентиляторов, для проверки срабатывания, с записью в формуляре вентсистемы | |
7 ТР | |
7.1 Работы в объеме ТО, а также указанные ниже | 1 раз в год |
7.2 Исправление вмятин, дефектов сварных швов в кожухе вентилятора, при необходимости – замена кожуха | |
7.3 Подтягивание всех креплений и замена дефектных болтовых соединений | |
7.4 Проверка состояния рабочего колеса (выявление погнутости, загрязнения, некомплектности лопаток) (при наличии недопустимых дефектов лопаток - замена) | |
7.5 Проверка зазора между кромкой входного патрубка центробежного вентилятора и кромкой переднего диска колеса (как в радиальном направлении, так и в направлении оси вала зазор не должен превышать 1 % от диаметра рабочего колеса) | |
7.6 Проверка зазора между лопатками крыльчатки и обечайкой осевых вентиляторов (не должен превышать 0,5 % от диаметра крыльчатки) | |
7.7 Замена отдельных лопаток, заварка трещин в рабочем колесе | |
7.8 Проверка посадки рабочего колеса на валу | |
7.9 Проверка состояния подшипников, вала (при наличии дефектов замена) | |
7.10 Проверка балансировки рабочего колеса (при правильной балансировке рабочее колесо должно останавливаться в любых положениях, не возвращаясь в исходное) | |
7.11 Проверка вращения рабочего колеса (легкость вращения, отсутствие задевания о кожух, биения или смещения на валу) | |
7.12 Замена ремня | |
7.13 Проверка состояния рамы, при необходимости ремонт | |
7.14 Очистка вентилятора от загрязнений. Восстановление антикоррозионного покрытия в соответствии с разделом 27 настоящего документа | |
8 КР | |
8.1 Работы в объеме ТР, а также указанные ниже | 1 раз в 6 лет |
8.2 Замена вала, подшипников | |
8.3 Балансировка рабочего колеса на балансировочном станке | |
8.4 Ремонт рамы, оснований | |
8.5 Полная окраска вентилятора и установочной площадки | |
9 Воздуховоды, клапана обратные и противопожарные (огнезадерживающие) | |
10 ТО | |
10.1 Проверка плотности всех соединений с подтяжкой болтов | 1 раз в 3 месяца |
10.2 Выявление вмятин, пробоин, прокорродировавших мест | |
10.3 Проверка состояния элементов жесткости воздуховодов и каркасов местных отсосов | |
10.4 Проверка элементов крепления (подвесок, хомутов, кронштейнов) | |
10.5 Проверка работоспособности шиберов, дроссель-клапанов и других запорных и регулирующих устройств (все дросселирующие устройства должны быть снабжены указателями степени их закрытия и закрепления в положениях, установленных при регулировке установки) | |
10.6 Визуальная проверка технического состояния клапанов обратных и огнезадерживающих на наличие трещин и других дефектов. Визуальный контроль положения заслонки по указателю на приводе или технологические отверстия. Проверка крепления клапанов к воздуховоду | |
10.7 Проверка действия воздуховыпускных и воздухозаборных устройств на сети воздуховодов | |
10.8 Проверка качества антикоррозионного покрытия | |
10.9 Поверка состояния проходов воздуховодов через стены и перекрытия | |
10.10 Отвод конденсата в канализацию, на вытяжных системах, в которых происходит выпадение конденсата, выполняется при обнаружении конденсата | |
10.11 Проверка заземления | |
11 ТР | |
11.1 Все работы выполняемые при ТО, а также указанные ниже | 1 раз в 12 месяцев |
11.2 Проверка функционирования огнезадерживающих и обратных клапанов. Устранение возникших неисправностей | |
11.3 Исправление вмятин, устранение погнутостей, заделка пробоин | |
11.4 Замена отдельных негодных элементов конструкций | |
11.5 Восстановление исправности сеток и решеток | |
11.6 Устранение неисправностей в запорных и регулирующих устройствах | |
11.7 Регулировка положения установленных местных отсосов | |
11.8 Очистка воздуховодов и местных отсосов в доступных без разборки местах | |
11.9 Замена теплоизоляции воздуховодов | |
11.10 Ремонт антикоррозионного покрытия (при необходимости) | |
12 Дефлекторы | |
12.1 Контроль исправности управления заслонками | 1 раз в 3 месяца |
12.2 Контроль технического состояния мест крепления дефлекторов | |
Примечания 1 На всем оборудовании при выполнении ТО проводится восстановление знаков присоединения заземляющих проводников на корпусах, рамах и площадках обслуживания, проверка и восстановление гибких токопроводящих перемычек на фланцевых соединениях. 2 При организации работ по ТО, ТР и КР вентиляционных систем в части периодичности и объемов выполняемых работ необходимо также учитывать требования завода-изготовителя конкретной системы. |
При обнаружении коррозии на элементах вентиляционных шахт, воздуховодов необходимо провести зачистку соответствующих мест до металлического блеска и толщинометрию материала. Допускаемое утонение стенок – не более 50 % от начальной толщины.
Признаки и причины неработоспособности систем вентиляции приведены в таблице 4.
Таблица 4 Признаки и причины неработоспособности систем вентиляции
Признаки неработоспособности | Причины неработоспособности |
1 | 2 |
1 Повышенная вибрация, шум | Неудовлетворительная центровка вентилятора и электродвигателя. Дисбаланс крыльчатки вентилятора из-за деформации или поломки лопастей. Ослабление крепления фундаментных болтов или болтов крепления корпуса подшипника. Износ подшипников |
2 Недостаточная кратность воздухообмена, снижение напора воздуха в контролируемых точках отбора по сравнению с предыдущими замерами (по результатам аэродинамических испытаний при проверке эффективности работы системы вентиляции) | Трещины и сквозные коррозионные износы материала воздуховодов и кожуха вентилятора. Засорение проточной части воздуховодов. Выход воздуха в местах соединений отдельных частей воздуховода. Поломка лопастей вентилятора. Несоответствие частоты вращения электродвигателя вентилятора значению, указанному в проектной документации |
3 Изменение шума с появлением высокочастотных составляющих (свиста) | Нарушение герметичности соединений вентилятора с воздухозаборной шахтой или воздуховодом; наличие трещин или сквозных коррозионных язв в воздуховоде |
4 Снижение температуры воздуха в помещении | Дефекты калорифера (утечка горячей воды или воздуха из-за негерметичности труб или соединений). Засорение нагнетательной части воздуховода (от калорифера к помещению). Недостаточная температура горячего теплоносителя |
5 Стук внутри механизма | Попадание посторонних предметов в корпус вентилятора Задевание вращающихся частей о неподвижные. Дефект подшипников |
Вибродиагностический контроль вентиляционных агрегатов проводится в соответствии с требованиями заводов-изготовителей, но не реже чем через 3000 ч эксплуатации и перед вводом в эксплуатацию после проведения ТР (в период обкатки) или при появлении посторонних шумов и включает в себя:
-
вибродиагностический контроль на подшипниковых опорах вентилятора; -
вибродиагностический контроль на раме и подшипниковых опорах двигателя.
Точки замера вибрации на вентиляционных агрегатах показаны на рисунке 1.
Допустимое значение вибрации на вентиляционных агрегатах в точках 1, 2,
7 – 10 составляет 6,3 мм/с; в точках 3, 4, 5, 6 – 1,8 мм/с.
На открытых осевых вентиляторах – в точках 3, 4, 5, 6 (рамы, болты) и в точках 2, 8 (задний подшипник), на канальных вентиляторах – замер вибрации не производится из-за отсутствия доступа.
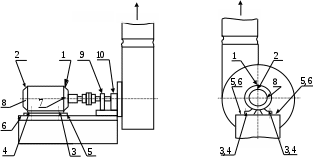
Рисунок 1 – Схема точек измерения вибрации на вентиляционных агрегатах
При обнаружении признаков неработоспособности проводится ремонт
1, 2 – точки измерения вертикальной составляющей вибрации на верхней части крышки переднего и заднего подшипника над серединой длины его вкладыша или точки наиболее приближенной к этому месту;
3, 4 – точки измерения вертикальной составляющей вибрации на болтах, крепящих электродвигатель к раме;
5, 6 – точки измерения вертикальной составляющей вибрации на раме рядом с болтами крепления электродвигателя;
7, 8 – точки измерения горизонтальной составляющей вибрации (условия замера, как для 1 и 2 точек);
9, 10 – точки измерения вертикальной составляющей вибрации на выносных подшипниковых опорах.
-
Перечень проверок и замеров при контроле технического состояния приведен в таблице 15.4. Выявленные дефекты и неполадки фиксируются в паспорте (формуляре), как подлежащие устранению при ремонте.
Таблица 15.4 – Перечень проверок и замеров при контроле технического состояния
систем вентиляции
Проверки и замеры при контроле технического состояния систем вентиляции | Периодичность выполнения работ |
1 | 2 |
1 Проверка эффективности поддержания температуры | 1 раз в 3 месяца |
2 Замер вибрации подшипниковых опор вентилятора, двигателя и рамы | 1 раз в 3 месяца |
3 Проверка соосности приводов вентиляторов | 1 раз в 3 месяца |
4 Проверка состояния шкивов и ремней и их натяжения | 1 раз в 3 месяца |
5 Проверка герметичности секции вентилятора (корпуса, фланцевых соединений, мягкой вставки) | 1 раз в 3 месяца |
6 Проверка правильности направления вращения рабочего колеса вентилятора, отсутствие посторонних шумов, подсосов, температура подшипников | 1 раз в 3 месяца |
7 Проверка правильности положения шиберов и положения огнепреградительного клапана (взведен/не взведен), отсутствие конденсата в вытяжных воздуховодах | 1 раз в 3 месяца |
8 Проверка калориферов на отсутствие течи | 1 раз в 3 месяца |
9 Проверка работы створок воздушных заслонок, перекидных клапанов | 1 раз в год |
10 Аэродинамические испытания (определение фактической кратности воздухообмена, давление, развиваемое вентиляторами в соответствии с утвержденной программой) | 1 раз в год |
2 ОПРЕДЕЛЕНИЕ ТРЕБУЕМЫХ ХАРАКТЕРИСТИК НАСОСНЫХ АГРЕГАТОВ И НПС
2.1 Определение часовой производительности перекачки (подачи насоса)
Исходные данные
Заданная пропускная способность трубопровода G, млн.т/год: 14,2
Коэффициент неравномерности перекачки: k = 1,0
Плотность нефти: ρ = 850 кг/м3
Часовая производительность нефтепровода расчётная, м3/час определяется по формуле:
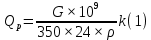

2.2 Выбор типоразмера насосов
По диаметру и часовой производительности нефтепровода и диапазону изменения подачи насоса по таблице 4 определяется марка насоса и тип ротора.
Таблица 4
Основные параметры магистральных насосов серии НМ
Марка насоса | Ротор | Диапазон изменения подачи насоса, м3/ч | Номинальные параметры | |||
Подача, м3/ч | Напор, м | Доп. Кавит. запас, м | К.П.Д.,% | |||
НМ 1250-260 | 0,7·Qн | 650 – 1150 | 900 | 260 | 16 | 82 |
1,0·Qн | 820 – 1320 | 1250 | 20 | 82 | ||
1,25·Qн | 1100 – 1800 | 1565 | 30 | 80 | ||
НМ 2500-230 | 0,5·Qн | 900 – 2100 | 1250 | 230 | 24 | 80 |
0,7·Qн | 1300 – 2500 | 1800 | 26 | 82 | ||
1,0·Qн | 1700 – 2900 | 2500 | 32 | 85 | ||
1,25·Qн | 2400 – 3300 | 3150 | 48 | 85 | ||
НМ 3600-230 | 0,5·Qн | 1300 – 2600 | 1800 | 230 | 33 | 82 |
0,7·Qн | 1600 – 2900 | 2500 | 37 | 85 | ||
1,0·Qн | 2700 – 3900 | 3600 | 40 | 87 | ||
1,25·Qн | 3600 – 5000 | 4500 | 45 | 84 | ||
НМ 7000-210 | 0,5·Qн | 2600 – 4800 | 3500 | 210 | 50 | 80 |
0,7·Qн | 3500 – 5400 | 5000 | 50 | 84 | ||
1,0·Qн | 4500 – 8000 | 7000 | 60 | 89 | ||
1,25·Qн | 7000 – 9500 | 8750 | 70 | 88 | ||
НМ 10000-210 | 0,5·Qн | 4000 – 6500 | 5000 | 210 | 42 | 80 |
0,7·Qн | 5500 – 8000 | 7000 | 50 | 85 | ||
1,0·Qн | 8000 – 11000 | 10000 | 70 | 84 | ||
1,25·Qн | 10000 – 13000 | 12500 | 80 | 88 |