Файл: Механике (Детали машин и основы конструирования) принадлежит ведущая роль среди других отраслей народного хозяйства. На основе развития механики осуществляется механизация и автоматизация производства.docx
ВУЗ: Не указан
Категория: Не указан
Дисциплина: Не указана
Добавлен: 10.11.2023
Просмотров: 27
Скачиваний: 2
ВНИМАНИЕ! Если данный файл нарушает Ваши авторские права, то обязательно сообщите нам.
Диаметры окружностей вершин da и впадин зубьев df:
-
шестерни da1 = d1 + 2m; df1 = d1 – 2,5m; -
колеса da2 = d2+ 2m;df2 = d2 – 2,5m.
Ширину шестерни в1(мм) принимают по соотношению в1/в2,
где в2 – ширина колеса.
При в2 …….. до 30; св. 30 до 50; св.50 до 80; св.80 до 100
в1/в2…. 1,1; 1,08; 1,06; 1,05.
Полученное значение в1 округляют до целого числа.
Определяем размеры колес:
-
шестерни d1 = 48мм;
-
колеса d2 = 2·150 – 60 = 240 мм.
Диаметры окружностей вершин зубьев:
-
шестерни dа1 = 60 + 2·1,25 = 62,5 мм; -
колеса dа2 = 240 + 2·1,25 = 242,5 мм.
Диаметры окружностей впадин зубьев:
-
шестерни df1 = 60 – 2,5·1,25 = 56,875 мм; -
колеса df2 = 240 – 2,5· 1,25 = 236,875 мм. -
Ширина колеса в нашем случаи в2 = 48 мм, тогда
в1 = 48·1,08 = 51,84 мм.
-
Полученное значение в1 округляют до целого числа в1 = 52 мм. -
Высота головки зуба hа = m= 1,25 мм. -
Высота ножки зуба hf = 1,25·m = 1,25·1,25 = 1,56 мм. -
Высота зуба h = ha + hf = 1,25 + 1,56 = 2,81 мм. -
Окружной шаг ρ = πm = 3,14·1,25 = 3,92 мм. -
Толщина зуба s, равная ширине впадины е, т.е.
s = e = 0,5ρ = 0,5·4,71 = 1,96 мм.
Радиальный зазор между зубьями с = 0,25m = 0,25·1,25 = 0,3125 мм.
Силы в зацеплении
В прямозубом зацеплении действуют окружная


α = 20° – стандартный угол зацепления. Для стандартного угла tgα = tg20° = 0,364.
В результате расчётов получим:
Окружная сила Ft
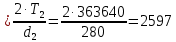
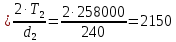
радиальная сила Fr =
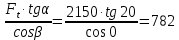
Степень точности зацепления,
Степень точности передачи определяют по таблице 20 [Р. 10] в зависимости от окружной скорости колеса
Окружная скорость прямозубого колеса
V = (3,14·240·110) /60000 = 1,3 м/с,
По окружной скорости определяем 9-ю пониженную степень точности зацепления.
3.5 Проверочный расчет зубьев колеса
Проверочный расчет производится по методикам, определенным ГОСТ 21354-87 «Передачи зубчатые цилиндрические эвольвентные внешнего зацепления. Расчет на прочность».
Проверка зубьев прямозубых колес по напряжениям изгиба зубьев
Условие прочности σF ≤ 1,1 [σ ]F, где σF – расчетное (действительное) напряжение изгиба.
Расчетное напряжение изгиба в зубьях колеса
σF2 =
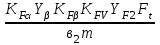
где КFα – коэффициент, учитывающий распределение нагрузки между зубьями, для колес с углом β > 0° принимают КFαв зависимости от степени точности:
степень точности 6 7 8 9
КFα 0,72 0,81 0,91 1,0;
Yβ = 1 – (β°/140) – коэффициент, учитывающий влияние наклона зуба (Yβ = 1-(0/140) 1);
КFβ – коэффициент, учитывающий неравномерность распределения нагрузки по длине контактных линий; для приработанных зубьев колес и скорости V ≤ 15 м/с, КFβ = 1;
КFY – коэффициент, учитывающий внутреннюю динамическую нагрузку, принимают для прямозубых колес при твердости зубьев ≤ 350 НВ – 1,4; > 350 НВ – 1,1;
YF – коэффициент формы (прочности) зуба, принимают по эквивалентному числу зубьев zV = z/cos3β, по таблице.
Для шестерни при zV ≈ 48 – YF1 = 3,65, для колеса zV ≈ 192 – YF2 = 3,59.
Расчетное напряжение изгиба в зубьях шестерни
σF1 =

Расчетные напряжения изгиба могут отклоняться от допускаемых
σF ≤ 1,1 [σ]F.
Используя формулы (2.31) и (2.32), получим
σF2 =
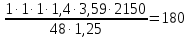
σF1 =
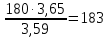
Условия прочности для прямозубых зубьев по напряжениям изгиба выполняются так как
σF2 = 180 Н/мм2< [σ]F2 = 242 Н/мм2;
σF1 = 183 Н/мм2< [σ ]F1 = 242 Н/мм2.
Проверка зубьев прямозубых колес по контактным напряжениям
Условие прочности σН = (0,9...1,05) [σ]Н.
Расчетное контактное напряжение для прямозубых колес
σН = 436
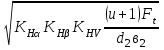
где КНα – коэффициент, учитывающий распределение нагрузки между зубьями для прямозубых колес КНα = 1;
КНβ – коэффициент концентрации нагрузки, для приработанных зубьев колес и скорости V ≤ 15 м/с, К
Нβ = 1;
КНV – коэффициент динамической нагрузки, для прямозубых колес при твердости зубьев ≤ 350 НВ – 1,2; > 350 НВ – 1,05;
u - передаточное число.
Используя формулу, получим для косозубой передачи
σН = 436
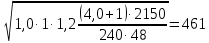
σН = (0,9...1,05) [σ ]Н = (0,9.. 1,05) 490 = (441…515) Н/мм2.
Условие прочности зубьев по контактным напряжениям для прямозубой передачи выполняется, так как расчётное напряжение укладывается в диапазон допускаемого.
Результаты расчета цилиндрической прямозубой передачи приведены в таблице 3.5.1.
Таблица 3.5.1 - Результаты расчета прямозубой передачи
Наименование параметров и размерность | ООбозначение | ВВеличина |
Допускаемое контактное напряжение, Н/мм2 | [σ]н | 490 |
Допускаемое напряжение изгиба для колеса, Н/мм2 | [σ]F2 | 242 |
Допускаемое напряжение изгиба для шестерни, Н/ мм2 | [σ]F1 | 242 |
Межосевое расстояние, мм | а | 150 |
Модуль передачи (зацепления), мм | m | 1,25 |
Угол наклона зубьев колес, град | β | 0 |
Число зубьев шестерни | z1 | 48 |
Число зубьев колеса | z2 | 192 |
Фактическое передаточное число | иф | 4,0 |
Делительный диаметр шестерни, мм | d1 | 60 |
Делительный диаметр колеса, мм | d2 | 240 |
Диаметр окружности вершин зубьев шестерни, мм | dа1 | 62,5 |
Диаметр окружности вершин зубьев колеса, мм | dа2 | 242,5 |
Диаметр окружности впадин зубьев шестерни, мм | df1 | 56,875 |
Диаметр окружности впадин зубьев колеса, мм | df2 | 236,875 |
Ширина зубчатого венца шестерни, мм | в1 | 52 |
Ширина зубчатого венца колеса, мм | в2 | 48 |
Высота головки зуба, мм | ha | 1,25 |
![]() Высота ножки зуба, мм | hf | 1,56 |
![]() Высота зуба, мм | h | 2,81 |
Окружной шаг, мм | ρ | 3,92 |
Толщина зуба, ширина впадины, мм Радиальный зазор, мм | s = e с | 1,96 0,3125 |
Окружная сила, Н | Ft | 2150 |
Радиальная сила, Н | Fr | 782 |
Расчетное напряжение изгиба, Н/мм2: | | |
зубьев шестерни | σF1 | 183 |
зубьев колеса | σF2 | 180 |
Расчетное контактное напряжение зубьев, Н/мм2 | σн | 461 |
3.5 Проектировочный расчет входного вала.
3.6.1 Расчетная схема.
Исходные данные:
вращающий момент на входном валу Т1 = 66,7 Н·м;
ширина шестерни в1 = 52 мм – для прямозубой передачи.
3.6.2 Геометрические размеры входного вала
Минимальный диаметр вала рассчитывается из условия только на кручение, по пониженным допускаемым касательным напряжениям [τ] по формуле:
d =

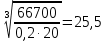
округляем до стандартной величины по таб. 1 в большую сторону d = 26 мм, где [τ] = 15…25 Н/мм2;
Т1– вращающий момент на входном валу в Н·мм.
Диаметр вала для установки подшипников dП
dП = d + 2tцил = 26 + 2·3,5 = 33 мм, принимаем dП = 35 мм,
где tцил = 3,5 мм определяется по таблице 35.
Рассчитанный диаметр цапфы вала под подшипники dП округляется до значения, кратного 5.
Диаметр буртика подшипников dБП
dБП = dП + 3r = 35 + 3·2 = 41 мм, округляем до dБП = 42 мм,
где r = 2 мм определяется по таблице 35.
Для эскизной компоновки передачи можно принимать (с последующим уточнением):
длину посадочного конца вала ℓМБ = 1,5d = 1,5 · 26 = 39 мм;
длину промежуточного участка ℓКБ = 1,4dП = 1,4 · 35 = 49 мм.
Ширина буртиков подшипников уточняется после определения размеров вала; окончательные размеры ℓКБ, ℓМБ – определяются при конструировании крышек подшипников, выбора типа уплотнения и муфты, конструировании корпуса редуктора.
3.6.3 Проектировочный расчет выходного вала
Тихоходные валы имеют концевые участки, участки для установки подшипников, колес и распорной втулки, буртики подшипников и колеса. Выходной вал В2 имеет цилиндрический консольный концевой участок длиной ℓМТ диаметром d, промежуточный участок ℓКТ диаметром dП, участок (цапфу) для установки подшипников диаметром dП, участки диаметром буртика dБП для упора во внутренние кольца подшипников. В средней части вала на шпонке установлено цилиндрическое косозубое колесо z2, которое с одной стороны упирается в буртик вала dБК, а с другой - во втулку.
3.6.4 Расчетная схема. Исходные данные:
вращающий момент на выходном валу Т2 = 258 Н·м;
ширина венца косозубого колеса
в2 = 48 мм.
3.6.5 Геометрические размеры выходного вала
Диаметр вала
d =

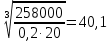
округляем диаметр вала до 42 мм, в большую сторону до стандартного числа по табл. 1;
где Т2 – вращающий момент на выходном валу в Н·мм;
[τ] – 15…25 Н/мм2 – допускаемое напряжение на кручение, принимаем
[τ] = 20 Н/мм2.
Диаметр вала для установки подшипников dП
dП = d + 2tцил = 42 + 2 · 3,5 = 49 мм,
где tцил = 3,5 мм определяется по таблице 35 .
Рассчитанный диаметр dП округляется до значения, кратного 5, т.е.
dП = 50 мм.
Диаметр буртика для подшипников dБП:
dБП = dП + 3r = 50 + 3 · 2,5 = 57,5 мм,
где r = 2,5 мм определяется по таблице 35.
Диаметр буртика для колеса dБК = dК + 3f = 58 + 3 · 1,2 = 61,6 мм,
где dК = dБП = 58 мм – диаметр участка вала для посадки колеса;
f = 1,2 мм определяется по таблице 35.
Длина посадочного конца вала
ℓМТ = 1,5 d = 1,5 · 42 = 61 мм.
Длина промежуточного участка
ℓКТ = 1,2 dП = 1,2 · 50 = 60 мм.
Чтобы поверхности вращающихся колес не задевали за внутренние поверхности стенок корпуса, между ними оставляется зазор а(рис. 2.5),определяемый по формуле: а =

Для прямозубой передачи d1 = 60 мм, d2 = 240 мм,
а =

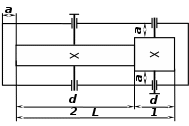
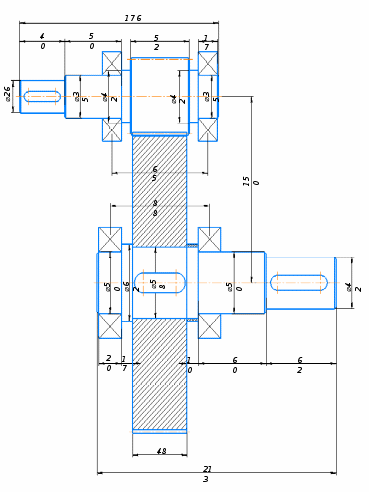
Рисунок 3.1 - Схема компоновки редуктора
3.6.6 Выбор подшипников валов
В соответствии с установившейся практикой проектирования и эксплуатации машин для опор валов прямозубых колес, в зацеплении которых действуют окружная и радиальная сила, цилиндрических редукторов применяют чаще всего шариковые радиальные однорядные подшипники (ГОСТ 8338-75). Первоначально принимают подшипники легкой серии. Если при последующем расчете грузоподъемность подшипника легкой серии окажется недостаточной, принимают подшипник средней серии (таблица 38).
В цилиндрической прямозубой передаче действуют окружная