ВУЗ: Не указан
Категория: Не указан
Дисциплина: Не указана
Добавлен: 22.11.2023
Просмотров: 59
Скачиваний: 1
ВНИМАНИЕ! Если данный файл нарушает Ваши авторские права, то обязательно сообщите нам.
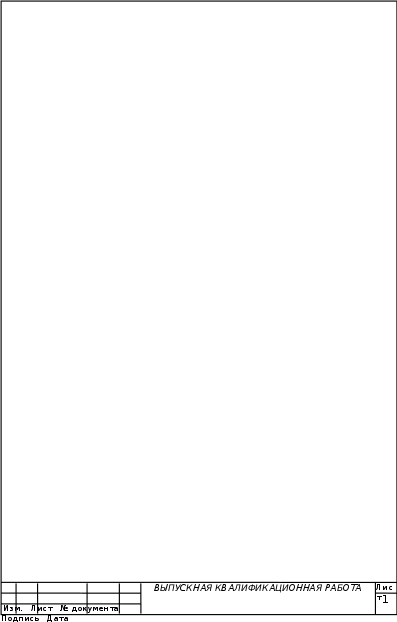
1. Требования морского регистра судоходства
1.1Электрические приводы судовых механизмов и устройств
Электроприводы механизмов и устройств
В зависимости от назначения и комплектации электроприводов в их состав входят электродвигатели, статические или вращающиеся преобразователи, аппаратура управления и защиты, тормоза, другое оборудование.
При подготовке автоматизированных электроприводов к действию должна быть проверена работоспособность устройств автоматизации, включая устройства АПС и защиты.:
Перед постановкой электроприводов в режим автоматического резерва должны быть выполнены необходимые проверки согласно назначению приводных механизмов, обеспечивающие надежное включение их электроприводов в действие по сигналу автоматического пуска.
При подготовке электроприводов к действию после продолжительного нерабочего периода необходимо выполнить проверки, измерить сопротивление изоляции и проверить в действии.
При использовании электроприводов необходимо контролировать:
нагрузку электродвигателей (при наличии амперметров);
работу щеточного аппарата;
температуру нагрева корпусов, подшипников и электромагнитных тормозов;
отсутствие постороннего шума и недопустимой вибрации;
состояние электрической аппаратуры и электрических устройств автоматизации электроприводов.
Для отдельных электроприводов с асинхронными короткозамкнутыми электродвигателями с прямым пуском, в том числе с полюсопереключаемыми, могут существовать ограничения по продолжительности работы, количеству пусков или переключений с одной скорости на другую по условиям нагрева. При использовании таких электроприводов в каждом отдельном случае следует руководствоваться заводскими инструкциями.
Электроприводы должны быть остановлены и все цепи питания обесточены при возникновении аварийных или опасных ситуаций:
несчастных случаях с людьми;
появлении дыма или огня из электрических машин, пусковой аппаратуры, тормозов и др.;
сильной вибрации электрических машин из-за неисправности подшипников;
поломке тормозов, редукторов и других узлов привода;
недопустимом нагреве корпусов и подшипников электрических машин, катушек тормозов и др.;
сильном искрении под щетками электрических машин;
резком снижении частоты вращения, сопровождающимся быстрым нагревом приводного электродвигателя.
Возобновление работы разрешается только после устранения неисправности.
Отключение электроприводов ответственных механизмов допускается только с разрешения вахтенного механика (вахтенного помощника капитана), кроме случаев, когда промедление может вызвать аварию судна или несчастный случай. В таких случаях о выполненном отключении необходимо немедленно известить вахтенного механика.
При самопроизвольной остановке приводного электродвигателя работающего механизма необходимо отключить питание, выяснить и устранить причину остановки. Производить повторный пуск до устранения причины остановки запрещается, за исключением случаев, когда длительная остановка электропривода может вызвать аварию судна или угрожать человеческой жизни.
Электроприводы грузоподъемных и якорно-швартовных устройств, шлюпочных лебедок.
При подготовке к действию электроприводов необходимо:
проверить состояние электродвигателей, тормозов, пусковой аппаратуры, устройств управления; удалить конденсат;
проверить исправность защитных заземлений;
измерить сопротивление изоляции;
установить рукоятки командоаппаратов в нулевые положения;
открыть вентиляционные каналы для охлаждения электродвигателей и ящиков сопротивлений; включить вентиляцию в помещениях аппаратуры управления;
включить на ГРЩ, РЩ питание электроприводов, а также средств дистанционного управления брашпилем и контроля длины вытравленной якорной цепи;
с ведома вахтенного помощника капитана и вахтенного механика опробовать электроприводы в действии, в том числе тормоза с электромагнитным или электрогидравлическим управлением, предусмотренные защиты, конечные выключатели и блокировки, измеритель натяжения троса автоматических швартовных лебедок, а также органы аварийного отключения.
В процессе работы, при возникновении неисправности электродвигателей, тормозов и аппаратуры управления, срабатывании устройств защиты и блокировок работа электроприводов должна быть немедленно прекращена. Возобновление работы разрешается только после устранения неисправности.
При использовании электроприводов запрещается:
шунтировать аварийные выключатели;
шунтировать конечные выключатели, ограничивающие максимально допустимый вылет или угол поворота стрелы;
заклинивать рукоятки командоаппаратов в рабочем положении;
выключать вентиляторы (при их наличии) при непродолжительных перерывах в работе;
выводить из действия конечные, путевые и дверные выключатели, а также устройства защиты и блокировки.
После использования электроприводов необходимо:
установить рукоятки командоаппаратов в нулевые положения;
отключить на ГРЩ, РЩ питание электроприводов, а также средств управления и контроля;
закрыть все вентиляционные отверстия и выключить вентиляцию помещений аппаратуры управления.
1.2 Классификация режимов работы кранов и их механизмов
Грузоподъемные краны являются массовыми общепромышленными механизмами, они применяются практически во всех отраслях промышленности, транспорта и строительства. Поскольку, в зависимости от области применения интенсивность работы кранов может быть различной, режимы работы кранов и крановых механизмов регламентируются.
В России для определения режима работы крановых механизмов действует ГОСТ 25835" 83, для определения группы режима работы крана " ГОСТ 25546"82. В значительной степени эти ГОСТы увязаны с международным стандартом ИСО 4301/1"86.
Режим работы крана учитывается при расчете мощности и выборе типа двигателя и аппаратуры управления.
ГОСТ 25835"83 предусматривает шесть групп режима работы, каждая из которых характеризуется определенным сочетанием классов использования и нагружения. Классы использования устанавливают в зависимости от нормы времени работы механизма. Ориентировочная характеристика класса использования механизма представлена в таблице 1, ориентировочная характеристика классов нагружения в таблице 2.
Таблица 1
Ориентировочные классы использования крановых механизмов
Класс использования | Использование во времени |
А0 | Редкое |
А1 | Нерегулярное |
А2 | Регулярное малой интенсивности |
А3 | Регулярное средней интенсивности |
А4 | Нерегулярное интенсивное (двухсменная работа) |
А5 | Интенсивное при трехсменной работе |
А6 | Весьма интенсивное при трехсменной работе |
Таблица 2
Ориентировочные классы нагружения крановых механизмов
Класс нагружения | Характеристика действующих нагрузок | |
Механизм подъема крана | Механизм горизонтального перемещения | |
В1 | Преобладают минимальные нагрузки; максимальные нагрузки редки, например, при монтажных и ремонтных работах | Редкие пуски и торможения, значительные рабочие и холостые пробеги; малые массы грузов; производства с малой интенсивностью работы и большими площадями обслуживания |
В2 | Преобладают средние и минимальные нагрузки; максимальные нагрузки относительно редки | Редкие, но регулярные пуски и торможения; небольшие рабочие и холостые пробеги; незначительные массы грузов; производства с постоянной, но ограниченной интенсивностью работы и площадями обслуживания |
В3 | Преобладают средние и минимальные нагрузки; минимальные нагрузки носят эпизодический характер; характерно для производств с разнообразными массами грузов | Регулярные пуски и торможения; малые рабочие и холостые пробеги; сравнительно большие массы грузов; производства с высокой интенсивностью работы и малыми площадями обслуживания |
В4 | Преобладают максимальные нагрузки и близкие к максимальным; средние нагрузки носят эпизодический характер; характерно для производств с относительно постоянной массой груза | Частые пуски и торможения с очень редким выходом на установившийся режим; большие массы грузов; производства с высокой интенсивностью работы и ограниченными площадями обслуживания |
Группы режимов работы механизмов представлены в таблице 3.
Таблица 3
Группы режимов работы крановых механизмов
Класс использования | Норма времени работы механизма, ч | Класс нагружения | |||
В1 | В2 | В3 | В4 | ||
А0 | До 800 | 1М | 1М | 1М | 1М |
А1 | От 800 до 1600 | 1М | 1М | 2М | 3М |
А4 | От 6300 до 12500 | 3М | 4М | 5М | 6М |
А5 | От 12500 до 25000 | 4М | 5М | 6М | - |
А6 | От 25000 до 50000 | 5М | 6М | - | - |
На практике группу режима работы механизмов часто устанавливают по группе режима работы крана. Ориентировочное соответствие групп режима работы крана и механизмов представлено в таблице 4.
Таблица 4
Ориентировочное соответствие групп режимов работы кранов и механизмов
Группа режима крана | Группа режима механизма | |
Механизмы, действующие при каждом цикле работы крана | Механизмы для установочных операций или используемые не при каждом цикле работы крана | |
1К | 1М | 1М |
2К | 1М | 1М |
3К | 1М – 2М | 1М |
4К | 2М – 3М | 1М – 2М |
5К | 3М – 4М | 1М – 2М |
6К | 4М – 5М | 2М – 3М |
7К | 5М – 6М | 3М – 4М |
8К | 6М | 5М – 6М |
1.3 Область нагрузок и требования к механическим характеристикам крановых электроприводов
Электропривод грузоподъемных кранов имеет ряд особенностей, отличающих его от электроприводов других общепромышленных и специальных механизмов:
механические характеристики электропривода расположены во всех четырех квадрантах; желательно обеспечить плавный переход приводной электрической машины из двигательного режима работы в генераторный режим при спуске;
относительно невысокий диапазон регулирования скорости (в большинстве случаев не выше 10:1 при однозонном регулировании скорости);
отсутствие высоких требований к жесткости механических характеристик;
отсутствие высоких требований к быстродействию;
температура окружающей среды изменяется от "40 до +40 °С. В металлургических цехах интервал изменения температуры окружающей среды составляет от "10 до +50 °С;
относительная влажность воздуха характеризуется средним уровнем 90% при температуре окружающей среды +25 °С;
осаждение пыли из воздуха 5 г/м2 в сутки;
осаждение паров кислот из воздуха 500 мг/м2 в сутки;
механические воздействия: вибрации и удары, вызванные передвижением механизмов; характеризуются частотой 1"50 Гц и ускорением 5 м/с2; одиночные повторяющиеся удары с ускорением до 30 м/с2;
частое отсутствие квалифицированного обслуживания;
жесткие требования в отношении простоты эксплуатации и надежности работы.
Электроприводы крановых механизмов по характеру нагрузок можно разделить на две группы: с преимущественно активным статическим моментом и преимущественно с реактивным статическим моментом.
К первой группе относятся электроприводы грузовых лебедок и стреловых лебедок с неуравновешенной стрелой, а ко второй группе – электроприводы механизмов горизонтального передвижения.
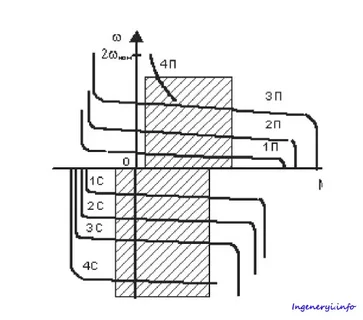
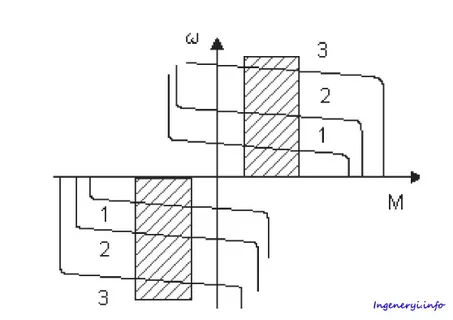
Рисунок 1. Желаемые механические характеристики электропривода механизмов подъема (а) и горизонтального передвижения (б)
Желаемые механические характеристики электроприводов механизмов подъема и горизонтального передвижения представлены на рис. 1.1. Электропривод должен обеспечивать жесткие механические характеристики во всем диапазоне нагрузок. Для выполнения операций по выбору слабины грузового каната необходимо иметь характеристику пониженной скорости 1П. Для точной установки груза необходима характеристика 1С. Характеристики, на которых осуществляется опускание груза, находятся как в четвертом (тормозной спуск), так и в третьем (силовой спуск) квадрантах.
Для кранов с большой высотой подъема для повышения производительности необходимо поднимать и опускать легкие грузы или пустой крюк со скоростью больше номинальной (характеристики 4). Поэтому электропривод должен обеспечивать двухзонное регулирование скорости.
Электропривод механизмов горизонтального передвижения имеет жесткие характеристики во всем диапазоне нагрузок. Для торможения с высших скоростей на низшие скорости электропривод должен обеспечивать автоматический переход из двигательного в тормозной режим с ограничением тормозного момента.
Основные типы кранов, их режимы работы и требования к электроприводу крановых механизмов
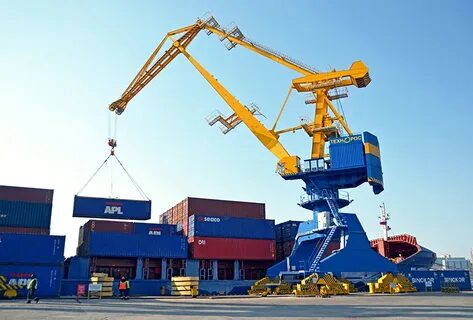
Рисунок 2. Портальный кран
Портальные краны
Портальные краны можно разделить на две группы:
-
Монтажные краны, применяющиеся в основном на судостроительных и судоремонтных заводах. Такие краны имеют умеренные номинальные скорости и повышенные требования к диапазону регулирования скорости и плавности переходных процессов. Режим работы, как правило, не превышает 5К.
-
Перегрузочные краны, работающие в морских и речных портах. Такие краны являются универсальными, т.е. могут работать как в крюковом режиме, так и в грейферном. Для работы с грейфером такие краны имеют две грузовые лебедки, которые управляются раздельно. При работе в крюковом режиме лебедки синхронизируются. Для обеспечения высокой производительности такие краны имеют высокие рабочие скорости. Режим работы может доходить до 8К. Диапазон регулирования скорости механизма подъема в крюковом режиме может доходить до 8:1.
Портальные краны имеют также механизмы поворота, изменения вылета стрелы и передвижения. У перегрузочных портальных кранов передвижение является установочным (т.е. редко используемым) движением.
1.3 Область нагрузок и требования к механическим характеристикам крановых электроприводов
Выбор системы электропривода кранового механизма в значительной степени определяется требованиями к его механическим характеристикам, которые изменяются в зависимости от рода технологических операций, выполняемых краном. Например, высокая точность монтажных операций, выполняемых с помощью крана, требует от характеристик электроприводов большой жесткости при значительном диапазоне регулирования, в то время как для магнитных кранов, транспортирующих скрап, стружки и т.д., указанные требования не играют столь существенной роли.
В большинстве случаев для крановых механизмов подъема обобщенные характеристики электропривода можно привести к изображенным на рис. 3 и 4.
Каждая из них имеет определенное назначение:
Характеристики 1 и 2 служат для подъема и опускания грузов с высокой скоростью;
характеристика 3 и ей подобные необходимы для плавного пуска двигателя при реостатном регулировании, а иногда служат для получения промежуточных скоростей движения грузов;
жесткая характеристика 4 в некоторых случаях необходима для доводки грузов до определенного уровня при его подъеме;
характеристика 5 позволяет осуществить спуск легких и тяжелых грузов с малой скоростью в тормозном режиме (квадрант IV), а также спуск легких грузов и пустого крюка при необходимости использования силового режима работы (квадрант III);
характеристика 6 необходима для механизмов, работающих с возможной резкой перегрузкой, например для грейферов.
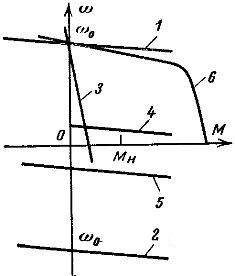
Рисунок 3. Механические характеристики электроприводов крановых механизмов.
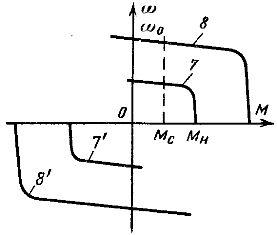
Рисунок 4. Механические характеристики электроприводов крановых механизмов с ограничением момента.
Следует обратить внимание на то, что в ряде случаев, особенно для механизмов передвижения, основным, требованием к механическим характеристикам электропривода является поддержание постоянства ускорения при пуске двигателя. Такой режим работы может быть получен, например, при наличии характеристик, приведенных на рис. 4. Малые скорости движения при моменте на валу, равном Мс, и малом ускорении обеспечиваются характеристиками 7 и 7', а повышенные скорости и ускорения — характеристиками 8 и 8'.
Приведенные графики (рис. 3) позволяют судить о том, какая система электропривода должна быть выбрана, если необходим определенный набор характеристик. Очевидным, например, является то, что характеристики 1, 2, 3 могут быть получены от обычного асинхронного двигателя с фазным ротором при реостатном регулировании в цепи ротора.
Более сложным будет электропривод, если необходимо иметь характеристики 1, 2, 3, 5. В этом случае можно использовать асинхронный двигатель с фазным ротором и дросселями, насыщения или тиристорным регулятором напряжения в цепи статора, асинхронный двигатель с фазным ротором и вихревым генератором на валу. Приведенные характеристики могут быть получены и от электроприводов с двигателями постоянного тока.
Выбор системы электропривода нельзя закончить, рассмотрев только возможность получения от нее определенных механических характеристик. Необходимо также оценить ее динамические качества, экономические показатели, надежность и простоту обслуживания.
Вместе с тем следует отметить, что общее изображение характеристик, необходимых для крановых механизмов (рис. 3), не дает полного представления о требованиях к электроприводу кранов. Для того, чтобы полностью представить, каковы требования к электроприводу при наличии характеристик 4 и 5, необходимо знать минимальную скорость при номинальной нагрузке и жесткость характеристик либо диапазон регулирования и необходимый перегрузочный момент при минимальной скорости движения.
При уточнении приведенных показателей следует вновь обратиться к технологическим требованиям. Рассматривая жесткость характеристик, необходимых, например, для механизмов монтажных кранов, в первую очередь следует исходить из точности остановки при выполнении операций спуска и подъема грузов.
Если эта точность составляет при операциях подъема несколько миллиметров, то минимальная скорость подъема груза составит 0,005—0,02 м/с при номинальной скорости около 0,1—0,5 м/с. Отметим, что по приведенным цифрам может быть непосредственно определен необходимый диапазон регулирования. Очень важно поэтому правильно установить требования в отношении точности остановки электропривода.
В некоторых случаях получение механической характеристики определенного вида, по существу, диктует выбор системы электропривода. Так, характеристики 6, 7, 8 (рис. 3 и 4), необходимые для грейферов, могут быть обеспечены с наилучшими показателями системой управляемый преобразователь — двигатель постоянного тока. Такое решение связано еще и с тем, что для электроприводов грейферных механизмов требуются обычно еще две-три промежуточные пониженные скорости, а это определяет необходимость в дополнительных регулировочных характеристиках.
Существенное значение при создании системы электропривода крановых механизмов имеет возможность получения характеристик, близких по виду к характеристикам 3 и 7 (рис. 3 и 4), которые обеспечивают снижение ударных нагрузок на механизм при выборке слабины канатов и люфтов в передачах.
Для пояснения указанного положения следует заметить, что при работе электропривода подъемного кранового механизма часто возникает такой режим, когда двигатель начинает вращаться, а груз находится в состоянии покоя. После выборки слабины каната и люфтов груз трогается с места рывком, так как двигатель мог к этому времени достигнуть значительной скорости. В этом случае осуществляется так называемый режим подъема с подхватом.
Если при этом характеристика двигателя жесткая, то канат и механизм испытывают ударные нагрузки, которые приводят к их повышенному износу. Кроме того, повышается опасность возникновения раскачивания груза.
При мягких характеристиках по мере натяжения канатов и выборки люфтов момент, развиваемый двигателем, растет, а скорость его падает. Поэтому при начале движения груза удары на механическое оборудование значительно снижаются. В меньшей степени вследствие проявления только наличия люфтов снижение ударов при мягкой начальной характеристике наблюдается также и на механизмах передвижения.
1.4 Типовые узлы, устройства крановых электроприводов
В зависимости от назначения и типа крана, вида механизма и требований, предъявляемых к приводу, применяются различные системы крановых электроприводов.
Промышленностью выпускаются комплектные крановые электроприводы и панели управления электродвигателями. Ниже приведены основные из них.
Электроприводы постоянного тока:
а) с управлением магнитным контроллером МК-ДП (магнитным контроллером, называют устройство управления, состоящее из командоконтроллера и контакторных панелей);
б) по системе тиристорный преобразователь – двигатель ТП-Д;
в) по системе генератор- двигатель Г-Д.
Электроприводы переменного тока:
а) с односкоростным или двухскоростным асинхронным короткозамкнутым двигателем, управляемым магнитными пускателями, МП-АДК, МП-АДД;
б) с асинхронным двигателем с фазным ротором, управляемым магнитным контроллером с торможением противовключением, МКП-АДФ;
в) с асинхронным двигателем с фазным ротором, управляемым магнитным контроллером с динамическим торможением с самовозбуждением СМКД-АДФ;
г) по системе асинхронный двигатель с фазным ротором – управляемый тиристорный преобразователь напряжения ТПН-АДФ;
д) асинхронный двигатель с фазным ротором, управляемый магнитным контроллером с тиристорным импульсно-ключевым регулированием МКИ-АДФ;
е) по системе тиристорный преобразователь частоты с непосредственной связью – двухскоростной асинхронный короткозамкнутый двигатель (НПЧ-АДД).
Технические данные некоторых из указанных приводов приведены в таблице 5.
Таблица 5.
Технические данные типовых электроприводов кранов
Тип электропривода | Механизм | Диапазон регул. Скорости | Тип магнит. Контроллера и преобразователя | Наибольшая расчетная мощность электродвигателя, кВт при Uном=380В | Тип кранов | ||||
1М-3М | 4М | 5М | 6М | ||||||
МК-АДД | Подъем, пере-движение | 6:1 3:1 | Б5701 Б5701 | 22 22 | 18,5 18,5 | - - | - - | Облегченные | |
МКД-АДФ | Подъем, крюковой, грейферный | 8:1 при спуске | ТСД60, ТСД160, ТСД250, ТСД400, ТСДГ160 | 37, 85, 140, 250, 85 | 30, 70, 110, 200, 70 | 25, 58 90, 160 58 | - | Краны мостовые козловые, башенные, где требуется диапазон регулирования 8:1 | |
| | | | | | | | | |
Продолжение таблицы 26.4 | |||||||||
МКИ-АДФ | Передвижение | 10:1 | БОК6511, БОК6502 | 37 2х18,5 | 30 2х15 | 22 2х11 | - | Все типы кранов, где требуются жесткие характеристики | |
ТПН-АДФ | Подъем, пере-движение | 4:1 Подъем 8:1 Спуск 8:1 Передвижение | П6512...ПУ ПС512...КУ | | До 80 | | | Контейнерные краны с двухдвигательными и кратным двум двигателями приводами | |
НПЧ-АДД | Поворот, пере-движение | (10...20):1 | ТТС40, ТТС100 Б004 | | | 24 60 | | Башенные краны | |
МК-ДП | Подъем, передвижение | 6...1 | ПСО160...ПС630 ПСО...П630 или (ДП) двухдвигательный | 38, 150 | 30...125 | 25...100 | 16...80 | Мостовые металлургические краны | |
ТП-Д | Подъем, поворот | 40:1 | ТПЕ, панель управления П9203 | | 240 | | | Башенные краны | |
| Поворот, пере-движение | 100:1 | Комплексный привод ЭТУ 360 | | 20 | | | Краны штабелеры |
Типовые электроприводы крановых механизмов
Крановые электроприводы по способу управления подразделяются на две большие группы:
- с управлением от силовых контроллеров (при мощности двигателей до 30 кВт)
- с управлением от сложных комплектных устройств, содержащих магнитные контроллеры с преобразователем энергии или без него.
При этом используются следующие системы электропривода.
В случае применения асинхронных двигателей:
1. электроприводы с регулированием сопротивления в цепи ротора асинхронного двигателя и торможением в режиме противовключения (магнитные контроллеры типа ТСА, ТСАЗ, КС, ДКС для механизмов подъема, силовые контроллеры типов ККТ61А, ККТ62А и ТА, ДТА, К, ДК – для механизмов передвижения).
2. электроприводы механизмов подъема с реостатным регулированием и динамическим торможением с самовозбуждением (магнитные контроллеры типов ТДС и КСДБ).
3. электроприводы с тиристорными регуляторами напряжения в цепи статора и дополнительными резисторами в цепи ротора двигателей (типа РСТ)
4. электроприводы с частотным регулированием асинхронных короткозамкнутых двигателей.
В случае применения двигателей постоянного тока:
1. С реостатным регулированием и потенциометрическим включением двигателя (силовые контроллеры типа КВ1О1 для механизмов передвижения моста и типа КВ102 – для механизмов передвижения тележки и ПС, ДПС – для механизмов подъема).
2. С тиристорными преобразователями типов АТК и АТРК.
В крановых электропривода наибольшее распространения получили асинхронные электродвигатели (свыше 90%).
Электроприводы с магнитными контроллерами охватывают диапазон номинальных мощностей двигателей от 11 до 180 кВт для механизмов подъема и от 3,5 до 100 кВт для механизмов передвижения.
Электроприводы механизмов передвижения с магнитными контроллерами выполняются по тому же принципу, что и электроприводы механизмов подъема. Основными отличиями схемы являются реализации симметричных механических характеристик для обоих направлений вращения двигателя и отсутствие характеристик, которые необходимы лишь для спуска грузов.
1.5 Общая характеристика судовых грузовых кранов
Судовые краны позволяют значительно увеличить производительность погрузочно-разгрузочных работ за счет уменьшения времени, затрачиваемого на эти операции. Судовой кран может одновременно осуществлять поворот, наклон, подъем и опускание груза. Краны обладают большей подвижностью, чем стрелы. Все механизмы крана смонтированы на поворотной платформе рядом с постом управления, который размещен в специальной кабине.
В судовом кране грузовая лебедка и грузовая стрела объединены в одну установку большей производительности, которая заменяет от двух до трех лебедок.
Судовые краны обычно выполняют с шарнирной укосиной и переменным вылетом. Грузовой гак крана перемещается почти горизонтально, его можно точно установить в любой точке, причем, в отличие от стрел, кран может вращаться по всей окружности на 360º.
Судовой кран требует меньшего количества обслуживающего персонала и занимает меньше места на палубе. К тому же судовой кран может быть оборудован грейфером, что позволит разгружать и загружать сыпучий груз собственными корабельными средствами. Опыт показывает, что производительность грузового крана в среднем на 20% превышает производительность грузовых стрел
Кран состоит из колонны со стрелой, поворотной платформы, механизмов управления, тросов и баллера, который является основой крана. Баллер иногда проходит через верхнюю палубу до нижней палубы.
При всех своих видимых достоинствах краны имеют ограниченную грузоподъемность. Если грузоподъемность стрел ограничивается остойчивостью судна (фактически – углом заливания), так как работа стрел значительное ухудшает остойчивость любого судна, то кран не может работать при углах крена, больше 5º, так как его поворотный механизм не в состоянии работать в наклонном по отношению к вертикали положении. Грузоподъемность судовых кранов обычно бывает в пределах 1 – 10 тонн. Поэтому для погрузки тяжеловесных грузов можно использовать только стрелы.
Вторым существенным недостатком крана является его громоздкость, а, следова-тельно, большой вес и большая стоимость. Эти обстоятельства делают невыгодной установку такого устройства на относительно небольших судах.
Для увеличения грузоподъемности применяют сдвоенные грузовые краны.
1.6 Модернизация крановых электроприводов с использованием силовой полупроводниковой техники
Процесс обновления системы привода крана, включающий в себя замену традиционных электромеханических компонентов на силовые полупроводники, такие как инверторы частоты и силовые модули. Это позволяет улучшить энергоэффективность, контроль и надежность работы крановых систем. Вот некоторые ключевые аспекты модернизации крановых электроприводов с использованием силовой полупроводниковой техники:
-
Инверторы частоты: Основным компонентом модернизации являются инверторы частоты, которые заменяют традиционные методы управления скоростью электродвигателей. Инверторы частоты используются для регулирования частоты и напряжения подачи питания в электродвигатель, что позволяет контролировать его скорость и крутящий момент. Силовые полупроводники, такие как IGBT (интерполированный биполярный транзистор с изолированным затвором), используются в инверторах частоты для обеспечения высокой эффективности и точного управления. -
Энергоэффективность: Замена традиционных методов управления на инверторы частоты позволяет значительно улучшить энергоэффективность крановых систем. Силовые полупроводники обеспечивают более эффективное использование электроэнергии и регулируют скорость движения крана в зависимости от нагрузки, что позволяет снизить энергопотребление и эксплуатационные расходы. -
Улучшенный контроль: Использование силовой полупроводниковой техники в крановых электроприводах обеспечивает более точный и гибкий контроль над движением крана. Инверторы частоты позволяют регулировать скорость и крутящий момент электродвигателя с высокой точностью и быстродействием. Это особенно важно при выполнении точных позиционирований и манипуляций грузами. -
Улучшенная надежность и долговечность: Силовые полупроводники обладают высокой надежностью и долговечностью в сравнении с традиционными электромеханическими компонентами. Их использование позволяет снизить вероятность отказов и повреждений, что ведет к более надежной работе крановых систем и снижению времени простоя. -
Дополнительные возможности: Модернизация крановых электроприводов с использованием силовой полупроводниковой техники также открывает дополнительные возможности в области автоматизации и мониторинга. Современные системы управления и мониторинга позволяют осуществлять дистанционное управление, сбор и анализ данных о работе крана, предупреждать о возможных неисправностях и обеспечивать более высокий уровень безопасности.
Важно отметить, что модернизация крановых электроприводов с использованием силовой полупроводниковой техники требует профессионального подхода и экспертизы в области электротехники и автоматизации. Рекомендуется обратиться к специалистам или производителям оборудования для подробной консультации и разработки оптимального решения модернизации, учитывающего особенности конкретного крана и требования его работы.
1.7 Уровни модернизации
Модернизация крановых электроприводов может быть выполнена на разных уровнях, в зависимости от целей и требований. Вот некоторые уровни модернизации крановых электроприводов:
Уровень 1: Замена компонентов. На этом уровне модернизации производится замена отдельных компонентов электропривода, таких как электродвигатель, преобразователь частоты, контроллеры и реле. Замена компонентов может быть необходима в случае выхода из строя или устаревания существующего оборудования. Это позволяет повысить надежность и эффективность работы крана.
Уровень 2: Улучшение системы управления. На этом уровне модернизации сосредоточиваются на обновлении системы управления крановым электроприводом. Это включает в себя замену старых реле и контроллеров на современные панели оператора или программные контроллеры. Обновленная система управления может предоставить более точное и гибкое управление краном, а также дополнительные функции, такие как автоматическое позиционирование и мониторинг состояния.
Уровень 3: Внедрение системы автоматизации. На этом уровне модернизации крановых электроприводов осуществляется внедрение системы автоматизации. Это включает в себя установку датчиков, системы видеонаблюдения, системы предотвращения столкновений и других систем, позволяющих автоматически контролировать и управлять работой крана. Система автоматизации может значительно повысить безопасность и эффективность работы крана.
Уровень 4: Улучшение энергоэффективности. На этом уровне модернизации крановых электроприводов акцент делается на улучшении энергоэффективности системы. Это может включать замену электродвигателя на более энергоэффективный вариант, установку преобразователей частоты с высоким КПД и функцией регулирования момента, а также оптимизацию процессов работы крана для снижения энергопотребления.
Уровень 5: Полная реконструкция. На этом уровне модернизации производится полная реконструкция кранового электропривода, включая замену всех компонентов системы, улучшение структуры и конструкции крана. Полная реконструкция может быть необходима в случае устаревания или повреждения кранового оборудования. Это позволяет полностью обновить и современизировать крановую систему, обеспечивая максимальную эффективность и надежность.
Каждый уровень модернизации имеет свои преимущества и рекомендуется в зависимости от конкретных потребностей и бюджета. При выборе уровня модернизации рекомендуется консультироваться с профессионалами и специалистами в области крановых систем для определения наиболее подходящего варианта и разработки индивидуального плана модернизации.
1.8 Предлагаемые варианты точек управления
При выборе точек управления судового крана необходимо учитывать ряд факторов, связанных с безопасностью, эффективностью и удобством оператора. Вот несколько рекомендаций по выбору точек управления судового крана:
Обзорность: Точки управления должны обеспечивать хорошую обзорность для оператора. Это позволяет ему наблюдать за рабочей зоной крана, окружающей средой и обеспечивает безопасную работу. Разместите точки управления таким образом, чтобы оператор имел хороший обзор на все рабочие места и окружающую территорию.
Удобство и доступность: Точки управления должны быть удобными для оператора и легко доступными. Разместите их так, чтобы оператор мог легко достигнуть их, иметь комфортное положение и свободу движений. Размещение точек управления рядом с рабочим местом оператора или на высоте, откуда легко видны рабочие места, может быть предпочтительным.
Безопасность: важно учитывать безопасность при выборе точек управления. Разместите их на безопасном расстоянии от опасных зон или мест работы крана, чтобы предотвратить риски для оператора и окружающих. Также обеспечьте надежное ограждение и защиту точек управления от нежелательного доступа.
Функциональность: Точки управления должны обеспечивать полный контроль над работой крана и его функциями. Убедитесь, что оператор имеет доступ к необходимым кнопкам, рычагам и панелям управления для управления движением, подъемом, поворотом и другими функциями крана. Возможно, потребуется использование дополнительных точек управления для различных задач и мест работы.
Эргономика: обратите внимание на эргономику точек управления. Они должны быть спроектированы таким образом, чтобы минимизировать усталость и напряжение оператора во время работы. Учитывайте удобство рычагов, кнопок и панелей управления, а также возможность регулировки высоты и положения точек управления для соответствия индивидуальным потребностям оператора.
При выборе точек управления судового крана рекомендуется также учитывать местные нормативные требования, стандарты безопасности и рекомендации производителя кранового оборудования. Консультация с профессионалами и специалистами в области крановых систем может помочь в определении наиболее подходящего варианта для конкретных условий и требований.
Разновидности точек управления краном:
Пульт управления на кабеле: это ручной пульт управления, подключенный к крану с помощью кабеля. Оператор может управлять краном, находясь на земле рядом с краном или в другом безопасном месте.
Пульт управления на проводах: это похожий на пульт управления на кабеле, но с проводами, обеспечивающими подачу электроэнергии на пульт. Такой пульт управления может быть использован, когда требуется более длинное расстояние между оператором и краном.
Кабина оператора: Некоторые краны оснащены кабиной оператора, которая располагается непосредственно на кране. Оператор управляет краном из кабины, имея отличный обзор на рабочую зону и окружающую территорию.
Пульт управления на радио: это беспроводной пульт управления, который позволяет оператору управлять краном с расстояния. Оператор может находиться в безопасном месте и иметь свободу перемещения вокруг крана при управлении им.
Автоматическая система управления: Некоторые краны могут быть оборудованы автоматическими системами управления, которые могут выполнять предварительно заданные операции и последовательности действий без участия оператора. Это может включать автоматическое позиционирование, автоматическую навигацию или использование датчиков для контроля и управления краном.
Конкретный выбор точки управления зависит от требований к работе крана, условий безопасности, видимости и комфорта оператора. Важно выбрать точку управления, которая обеспечивает эффективное управление краном и минимизирует риски для оператора и окружающих.
Глава 2 Расчетная часть системы электропривода механизма подъёма КПП.
2.1 Технологическое описание работы механизма подъёма КПП.
Портальный кран — это полноповоротный стреловой кран, поворотная часть которого установлена на портале, передвигающемся по рельсам, проложенным на земле или эстакаде.
Механизм подъема крана портального перегрузочного обеспечивает вертикальное перемещение грузовых грузоподъемных приспособлений (таких как крюки, захваты или специальные контейнеры) вдоль вертикальных опорных стоек. Он состоит из нескольких основных компонентов:
-
Лебедка: Лебедка является главным приводным элементом механизма подъема и обеспечивает движение грузовых грузоподъемных приспособлений вверх и вниз. Она обычно устанавливается на верхней части опорных стоек и оснащена электрическим или гидравлическим приводом. Лебедка имеет канат или цепь, которые подключены к грузовому приспособлению для подъема и опускания груза. -
Вертикальные опорные стойки: Опорные стойки являются вертикальными конструктивными элементами крана и служат для поддержки и направления движения грузовых приспособлений вдоль вертикальной оси. Они часто изготавливаются из прочных стальных профилей, способных выдерживать значительные нагрузки. Опорные стойки монтируются на фундаменте или к другим конструкциям, обеспечивающим их надежную фиксацию. -
Механизм перемещения по опорным стойкам: Этот механизм позволяет подъемному механизму перемещаться вдоль опорных стоек, обеспечивая равномерное и стабильное вертикальное движение. Он может включать в себя систему направляющих роликов или путей, которые помогают лебедке двигаться по вертикальным опорным стойкам с минимальным сопротивлением. -
Приводная система: Приводная система механизма подъема обеспечивает передачу энергии от источника питания (электрического или гидравлического) к лебедке. Она включает в себя электродвигатели, гидронасосы, передачи и другие компоненты, которые обеспечивают движение и управление подъемным механизмом. -
Управление: Механизм подъема обычно имеет систему управления, которая позволяет оператору контролировать подъем, опускание и остановку грузовых приспособлений. Управление может быть ручным, при помощи кнопок или рычагов, или автоматическим, при помощи программного обеспечения и датчиков.
2.2 Последовательность расчета механизма подъёма КПП.
Расчёт механизма подъёма крана портального перегрузочного включает в себя несколько основных шагов. Вот полная последовательность расчёта:
-
Определение рабочей нагрузки: сначала необходимо определить максимальную рабочую нагрузку, которую механизм подъёма должен поддерживать. Это может быть вес груза, который кран должен поднимать, или сумма весов нескольких грузовых приспособлений, которые будут использоваться. -
Расчёт грузоподъёмности: на основе рабочей нагрузки необходимо определить грузоподъёмность механизма подъёма. Грузоподъёмность обычно указывается производителем крана и зависит от различных факторов, таких как конструкция лебедки, опорных стоек и привода. -
Расчёт суммарного веса грузоподъёмных приспособлений: если вам необходимо поднимать несколько грузовых приспособлений одновременно, необходимо определить суммарный вес этих приспособлений. Это поможет определить требуемую грузоподъёмность лебедки и прочность опорных стоек. -
Расчёт момента подъёма: Момент подъёма является силой, необходимой для подъёма груза. Он может быть рассчитан, учитывая вес груза и расстояние от центра тяжести груза до оси вращения лебедки. -
Выбор соответствующих компонентов: на основе расчётов выбираются соответствующие компоненты, такие как лебедка, опорные стойки, механизмы перемещения и приводная система. Компоненты должны иметь достаточную грузоподъёмность и прочность для обеспечения безопасной работы крана. -
Учёт стандартов и нормативов: при расчёте механизма подъёма необходимо учитывать применимые стандарты и нормативы безопасности, такие как местные строительные коды или индустриальные стандарты. Это включает требования к нагрузке, прочности, электробезопасности и другим аспектам работы крана.
2.3. Определение нагрузки на барабан.
Выбор каната, блока, барабана.
Для выбора барабана требуется определить параметры каната и блока
1)Определение параметров каната:
![]() Где: Smax - максимальное рабочее натяжение каната; Gгр - вес груза; Gпод - вес грузового органа; iпол - кратность полиспаста; ![]() | 2.1 |
a– число ветвей каната (таблица)
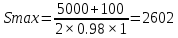
КПД полиспаста определяется по формуле:
![]() | 2.2 |
где:

iпол - кратность полиспаста; (таблица)
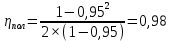
Разрывное усилие каната определяется п формуле:
![]() Где: | 2.3 |
Sр - расчётное разрывное усилие каната
К – наименьший коэффициент запаса прочности

2)Определение параметров блока:
Определение параметров блока производится при диаметре каната = 19.5мм.
![]() | 2.4 |
где:
Dбл – диаметр блока;
dк – диаметр каната;
l – коэффициент, зависящий от выбора диаметра блока(таблица)

С полученными ранее дынными мы можем произвести выбор барабана:
![]() | 2.5 |
где
Dбар – минимальной диаметр барабана;
Dбл – диаметр блока;

Полученное значение Dбар следует округлить в большую сторону до стандартного значения из нормального ряда диаметров: 160, 200, 250,
Исходя из этого полученное значение 214,2мм округляем до 250 мм
2.4. Выбор приводного электродвигателя
Исходя из проведенных расчетов выбрал ЭД типа 4A250 мощностью 45кВт. Характеристики данного двигателя приведены в таблице 6.
Таблица 6.
Тип двигателя | n1 об/мин | Pн кВт | КПД, % | Cos φ | Sн, % | ![]() | ![]() | ![]() | ![]() | Момент инерции Кг*м2 | Масса, кг |
АИР200S2 | 3000 | 45 | 92 | 0,88 | 2 | 1,8 | 2,8 | 1,5 | 7,5 | 0,14 | 240 |
Методика расчета:
![]() | 2.6 |
![]() | |
Где:
Ррд — расчетная мощность ЭД механизма подъема мостового крана, кВт;
Кз — коэффициент запаса, отн.ед.;
Учитывает дополнительную нагрузку при пуске и торможении. Рекомендуется принимать Кз = ... 1,2.
Рсэ — статическая эквивалентная мощность на валу ЭД за рабочий цикл, кВт;
Для механизма подъема рабочий цикл состоит из 4 рабочих операций: подъема и опускания груза, подъема и опускания грузозахватывающего устройства.
ПВр — продолжительность включения расчетная, отн. ед.;
ПВк — продолжительность включения каталожная, отн. ед.
![]()
| 2.7 |
Где:
Рспг — статическая мощность на валу ЭД при подъеме груза, кВт;
Рспо — статическая мощность на валу ЭД при подъеме без груза, кВт;
Рсог — статическая мощность на валу ЭД при опускании груза, кВт;
Рсоо — статическая мощность на валу ЭД при опускании без груза, кВт.
![]()
| 2.8 |
Где:
Gном — грузоподъемность номинальная, кг;
Go — масса грузозахватывающего устройства, кг;
v — скорость подъема (опускания) груза (грузозахватывающего устройства), м/с;
Принято, что скорости при подъеме (опускании) груза или пустого грузозахватывающего устройства равны. Для механизма подъема рекомендуется принимать v = 0,15...0,20 м/с.
q — ускорение силы тяжести, м/с 2.
Для перевода массы в силу кг = 9,81 Н (Ньютон).