Добавлен: 22.11.2023
Просмотров: 46
Скачиваний: 3
ВНИМАНИЕ! Если данный файл нарушает Ваши авторские права, то обязательно сообщите нам.
Министерство образования Красноярского края
Краевое государственное АВТОНОМНОЕ профессиональное образовательное учреждение
«Ачинский техникум нефти и газа ИМЕНИ Е.А.ДЕМЬЯНЕНКО»
Допуск к защите
Приказ от __________ № ___________
ВЫПУСКНАЯ КВАЛИФИКАЦИОННАЯ РАБОТА
Вид ВКР: дипломный проект
Эксплуатация систем автоматического управления с учетом специфики технологического процесса регулирования реакционных аппаратов
Специальность | 15.02.07 Автоматизация технологических | ||
| процессов и производств (по отраслям) | ||
Группа | АП-18 | ||
| | | |
| | | |
Разработал | | | Д.Е.Моргунов |
Руководитель дипломного проекта | | | Е.Н.Ступаков |
Консультант по экономической части | | | Е.А.Херувимова |
Нормоконтроль | | | Е.Н.Ступаков |
Председатель предметно-цикловой комиссии | | | С.В.Помелова |
Ачинск, 2022
Согласовано Филиал «Макрорегион Восточная Сибирь» ООО ИК «СИБИНТЕК» Ачинское РПУ Начальник участка цеха КИПиА № 5 _____________________ А.В.Масловский подпись «____»_________________ 2022 г. | Утверждаю зам. директора по УПР ___________ Н.А.Константинова подпись «____»_________________ 2022 г. |
ЗАДАНИЕ
НА ВЫПУСКНУЮ КВАЛИФИКАЦИОННУЮ РАБОТУ
обучающегося специальности 15.02.07 «Автоматизация технологических процессов и производств (по отраслям)»
Моргунова Дмитрия Евгеньевича
Тема ВКР: Эксплуатация систем автоматического управления с учетом специфики технологического процесса регулирования реакционных аппаратов
СОДЕРЖАНИЕ ПОЯСНИТЕЛЬНОЙ ЗАПИСКИ
ВВЕДЕНИЕ
1.ОБЩАЯ ЧАСТЬ
1.1 Описание технологического процесса
1.2 Описание работы схемы автоматизации
2 ТЕХНОЛОГИЧЕСКАЯ ЧАСТЬ |
2.1 Разработка технологического процесса 2.2 Построение функциональной схемы |
2.3 Конструирование схемы автоматизации технологического процесса |
3 СПЕЦИАЛЬНАЯ ЧАСТЬ 3.1 Устройство и работа новейшего прибора 3.2 Подготовка к работе прибора, Измерение параметров, регулирование и настройка прибора 3.3 Техническое обслуживание 3.4 Возможные неисправности и способы их устранения |
4. ЭКОНОМИЧЕСКАЯ ЧАСТЬ
4.1 Расчёт амортизационных отчислений
4.2 Расчёт капитальных затрат на процесс автоматизации
5. ОХРАНА ТРУДА И ПРОМЫШЛЕННАЯ БЕЗОПАСНОСТЬ
5.1 Общие требования безопасности
5.2 Пожаробезопасность
5.3 Электробезопасность
5.4 Безопасность труда на рабочем месте
ЗАКЛЮЧЕНИЕ
СПИСОК ИСПОЛЬЗУЕМЫХ ИСТОЧНИКОВ
ПЕРЕЧЕНЬ ГРАФИЧЕСКОГО МАТЕРИАЛА
1.Общая схема технологического процесса
2. Схема автоматизации процесса
3. Прибор (общий вид прибора, схема составных частей, или схема подключения)
Задание принял к исполнению __________ __________
подпись инициалы, фамилия
Руководитель дипломного проекта __________ __________
подпись инициалы, фамилия
Председатель ПЦК __________ __________
подпись инициалы, фамилия
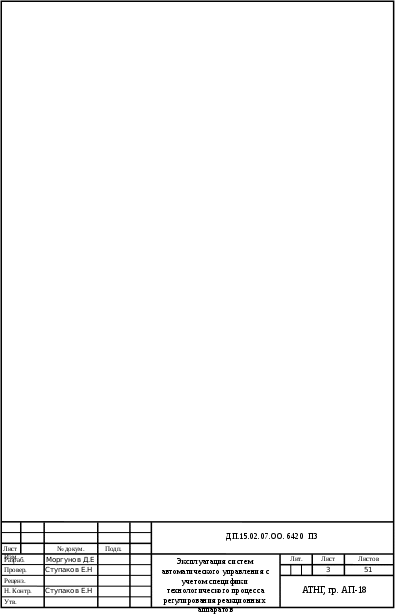

Константинова
СОДЕРЖАНИЕ
| ВВЕДЕНИЕ | 4 |
1 | ОБЩАЯ ЧАСТЬ | 5 |
1.1 | Описание технологического процесса | 5 |
1.2 | Описание работы схемы автоматизации с применением экстрактивной ректификации | 6 |
2.1 | Разработка технологического процесса каталитического крекинга c применением реакционных аппаратов | 8 |
2.2 | Построение функциональной схемы процесса каталитический крекинг с применением реакционных аппаратов | 8 |
2.3 | Конструирование схемы автоматизации технологического процесса каталитический крекинг с применением реакционных аппаратов | 10 |
2.1 | Разработка технологического процесса каталитического крекинга c применением реакционных аппаратов | 12 |
3 | СПЕЦИАЛЬНАЯ ЧАСТЬ | 14 |
3.1 | Устройство и работа прибора Метран – 150 | 14 |
3.2 | Подготовка к работе прибора, Измерение параметров, регулирование и настройка прибор | 15 |
3.3 | Техническое обслуживание | 17 |
3.4 | Возможные неисправности и способы их устранения | 19 |
4 | ЭКОНОМИЧЕСКАЯ ЧАСТЬ | 20 |
4.1 | Расчет амортизационных отчислений | 20 |
4.2 | Расчет капитальных затрат на процесса каталитического крекинга с применением реакционных аппаратов | 25 |
5 | ОХРАНА ТРУДА И ПРОМЫШЛЕННАЯ БЕЗОПАСНОСТЬ | 28 |
5.1 | Общие требования безопасности | 28 |
5.2 | Пожаробезопасность | 32 |
5.3 | Электробезопасность | 38 |
5.4 | Безопасность труда на рабочем месте | 42 |
| ЗАКЛЮЧЕНИЕ | 44 |
| СПИСОК ИСПОЛЬЗУЕМЫХ ИСТОЧНИКОВ | 45 |
| ПЕРЕЧЕНЬ ГРАФИЧЕСКОГО МАТЕРИАЛА 1. Общая схема технологического процесса 2. Схема автоматизации процесса 3. Прибор (общий вид прибора, схема составных частей, или схема подключения) | |
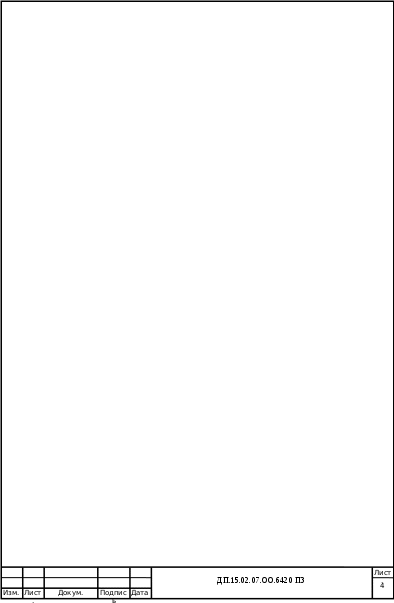
Автоматизация производственных процессов – основное направление, по которому в настоящее время продвигается производство во всем мире. Автоматизация ведет к повышению качества процесса и производительности труда.
Цель курсового проекта: разработка не сложных систем регулирования реакционных аппаратов.
Задачи:
-
Разработать автоматизированную систему управления регулирования реакционных аппаратов; -
Разработать требования к техническим средствам и безопасности -
Построить функциональную схему и схему автоматизации -
Как происходит процесс регулирования в реакционных аппаратах
Автоматизация производственных процессов – основное направление, по которому в настоящее время продвигается производство во всем мире. Автоматизация ведет к повышению качества процесса и производительности труда.
Реакционные аппараты. Это устройства с перемешивающим механизмом, используемые для проведения процессов суспендированы и диспергирования
Процесс каталитического крекинга является одним из наиболее распространенных крупнотоннажных процессов углубленной переработки нефти. На сегодняшний день процесс каталитического крекинга является самым массовым процессом получения высокооктанового бензина, компонента дизельного топлива и сырья для получения технического углерода.
Актуальность темы заключается в том, что современные нефтеперерабатывающие заводы не могут обходиться без реакционных аппаратов.
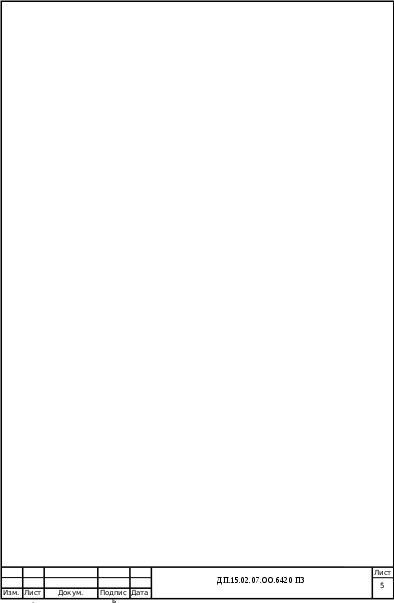
-
Описание технологического процесса
Основным элементом технологических схем нефтехимических производств является реакционный аппарат (реактор), от работы которого в большой степени зависит качество выпускаемой продукции. Реакторы различают по типу действия, по тепловому режиму, по организации процесса перемешивания, по числу фаз, участвующих в реакции, по конструктивным особенностям, по способу размещения катализатора в рабочем объеме.
Выбор типа реактора для осуществления данного химического процесса зависит от многих факторов, из которых важнейшими являются: необходимость использования катализатора, его свойства и расход; термодинамические особенности процесса — адиабатические, изотермические или политропические условия проведения химической реакции;
методы теплообмена, используемые для обеспечения заданного температурного режима в зоне реакции; свойства используемых теплоагентов; периодическое или непрерывное осуществление процесса.
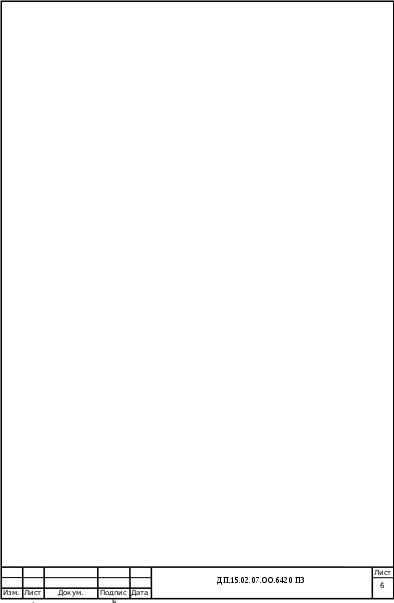
В некоторых случаях небольшое изменение температуры в адиабатическом реакторе достигается подачей вместе с сырьем инертного (не участвующего в реакции) вещества (теплоагента), которое поглощает (при экзотермической реакции) или компенсирует (при эндотермической реакции) часть теплового эффекта реакции. Примером адиабатического реактора
1.2 Описание работы схемы автоматизации
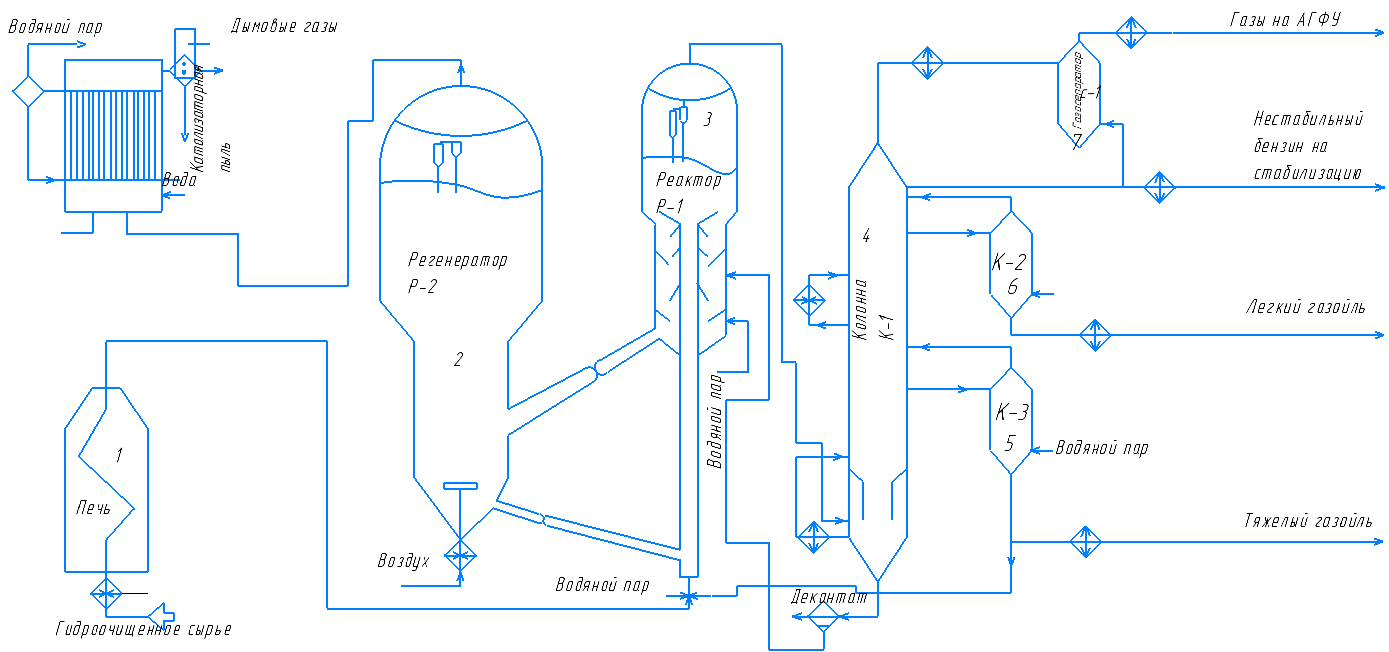
Оборудование: П – печь; Р-1 – лифт-реактор; Р-2 – регенератор; К-1 – ректификационная колонна; К-2 и К-3 – отпарные колонны; С-1 – газосепаратор;
Рисунок 1- Схема процесса каталитический крекинг
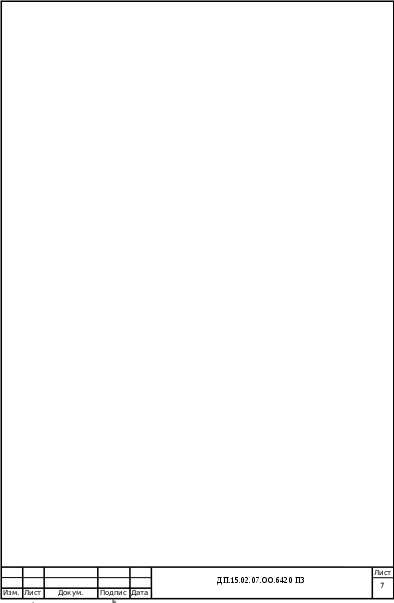