Добавлен: 22.11.2023
Просмотров: 50
Скачиваний: 3
ВНИМАНИЕ! Если данный файл нарушает Ваши авторские права, то обязательно сообщите нам.
Закоксованный катализатор из отпарной зоны Р-1 по наклонному катализаторопроводу поступает в зону кипящего слоя регенератора Р-2, где осуществляется выжиг кокса в режиме полного окисления оксида углерода в диоксид. Регенерированный катализатор по нижнему наклонному катализаторопроводу далее поступает в узел смешения лифт-реактора. Воздух на регенерацию нагнетается воздуходувкой. При необходимости он может нагреваться в топке под давлением. Дымовые газы через внутренние двухступенчатые циклоны направляются на утилизацию теплоты (на электрофильтры и котел-утилизатор).
В К-1 для регулирования температурного режима предусмотрены верхнее острое и промежуточные циркуляционные орошения. Отбор легкого и тяжелого газойля осуществляется через отпарные колонны К-2 и К-3. Нижняя часть колонны является отстойником (скруббером) катализаторного шлама, который возвращается в отпарную зону Р-1. Часть тяжелого газойля подается в узел смешения лифт-реактора как рециркулят. С верха колонны выводится смесь паров бензина, воды и газов крекинга, которая после охлаждения и конденсации разделяется в газосепараторе С-1 на газ, нестабильный бензин, направляемые в блок газофракционирования и стабилизации бензина. Водный конденсат после очистки от сернистых соединений выводится с установки.
2 ТЕХНИЧЕСКАЯ ЧАСТЬ
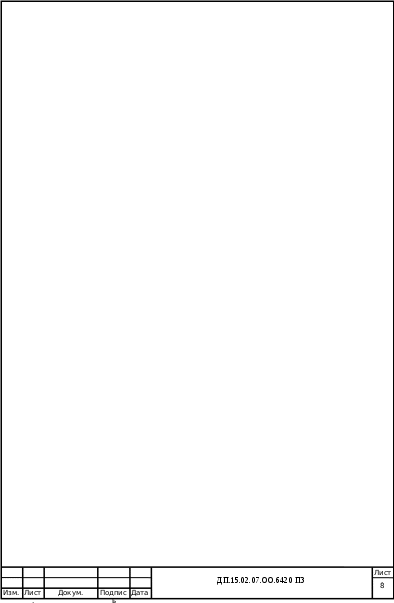
Был разработан чертеж технического проекта процесса каталитический крекинг c применением реакционных аппаратов

Рисунок 2 - Схема технологического процесса каталитического крекинга
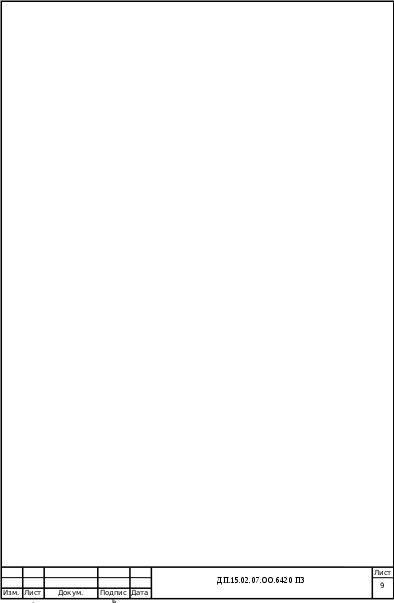
Предварительно подогретое гидроочищенное сырье в печах смешивается с рециркулятором и водяным паром и вводится в узел смешения реактора.Контактируя с регенерированным горячим катализатором с цеолитом, сырье испаряется, подвергается катализу в реакторе и далее поступает в зону кипящего слоя реактора. Продукты реакции отделяются от катализаторной пыли в двухступенчатых циклонах и поступают в нижнюю часть ректификационной колонны на разделение.
За коксованный катализатор из отпорной зоны реактора поступает в зону кипящего слоя регенератора, где осуществляется выжиг кокса в режиме полного окисления оксида углерода в диоксид. Регенерированный катализатор далее поступает в узел смешения реактора. Воздух на регенерацию нагнетается воздуходувкой. Дымовые газы направляются на утилизацию теплоты.
Для регулирования температуры в ректификационной колонне К-1 предусмотрены верхнее острое и промежуточные циркуляционные орошения. Отбор легкого и тяжелого газойля осуществляется колоннами К-2 и К-3.Часть тяжелого газойля подается в узел смешения реактора как рециркулят. Сверха колонны выводится смесь паров бензина, воды и газов крекинга, которая после охлаждения и конденсации разделяется в газосепараторе на газ, нестабильный бензин, направляемый в блок газофракционирования и стабилизации бензина.Водный конденсат после очистки от сернистых соединений выводится с установки.

Был разработан чертеж функциональной схемы каталитического крекинга с применением реакционных аппаратов
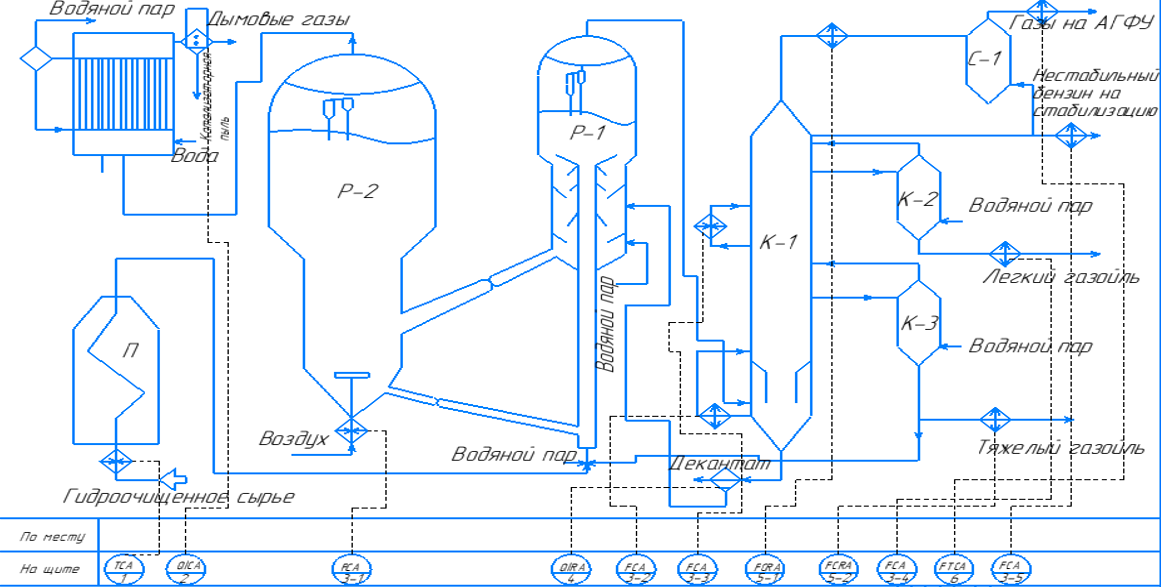
П- печь Р-2 – регенератор Р-1 – реактор К-1,2,3 – ректификационные колонны С-1 - газосепаратор
Рисунок 3 – Функциональная схема каталитического крекинга, с установленными датчиками на щите
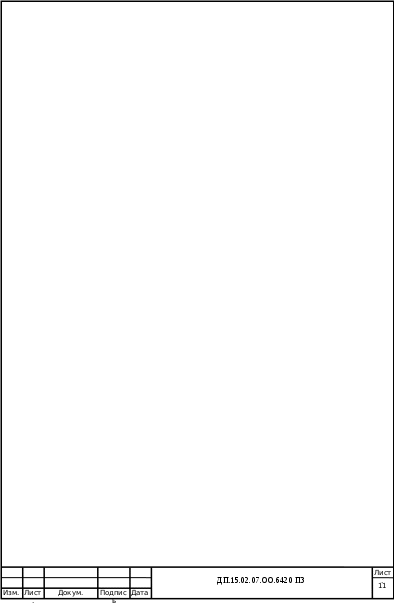
Для достижения цели управления нужно регулировать:
-
температуру; -
расход;
Контролю подлежат нерегулируемые режимные и входные параметры. Сигнализации подлежат все параметры, изменение которых может привести к аварийной ситуации или серьезному нарушению технологического режима и, в конечном счете, к изменению критерия управления. Параметрами автоматической защиты являются те параметры, при недопустимом отклонении которых должны срабатывать устройства автоматической защиты и не допустить перехода в аварийную ситуацию.
Информация от датчиков поступает в универсальные многофункциональные одноканальные индикаторы с функцией формирования сигнала тревоги при выходе за допустимые диапазоны.
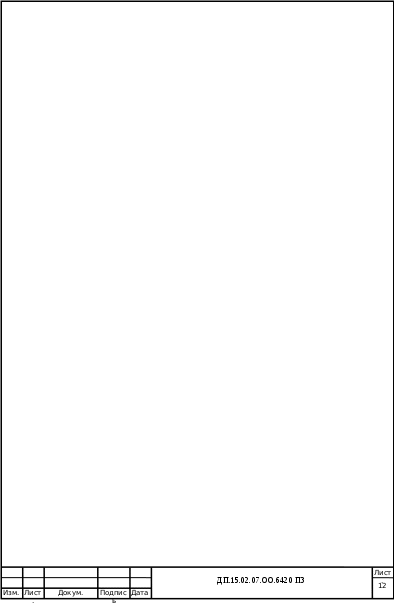
Был разработан чертеж автоматизации технологического процесса каталитического крекинга с применением реакционных аппаратов
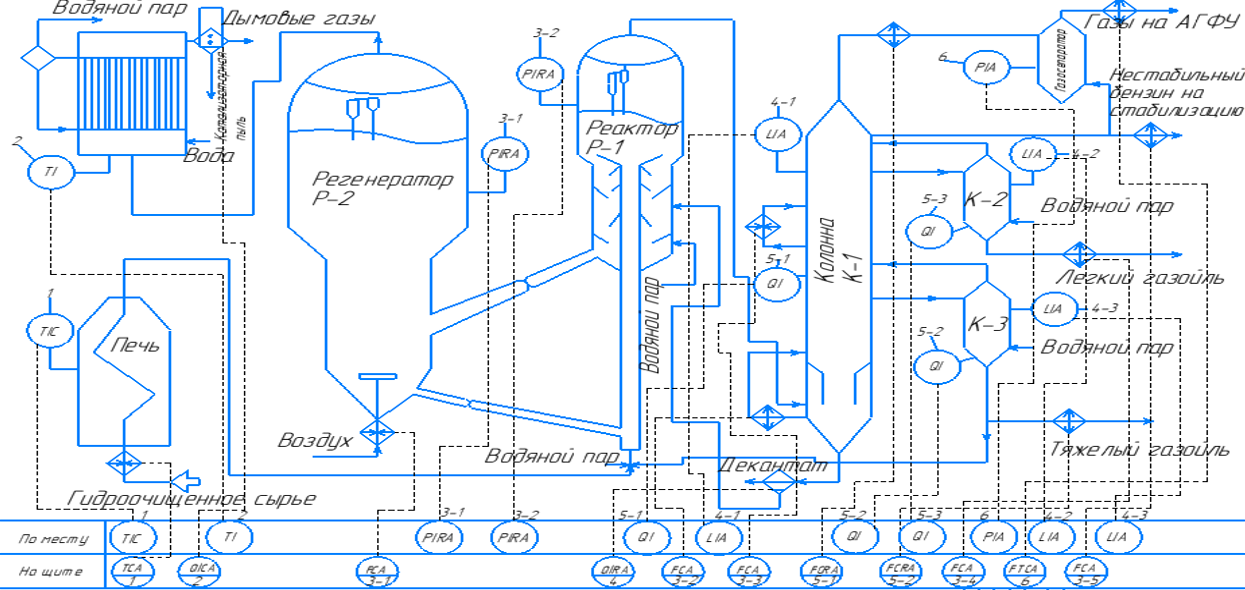
П- печь Р-2 – регенератор Р-1 – реактор К-1,2,3 – ректификационные колонны С-1 - газосепаратор
Рисунок 4 – Схема автоматизации каталитического крекингас применением реакционных аппаратов
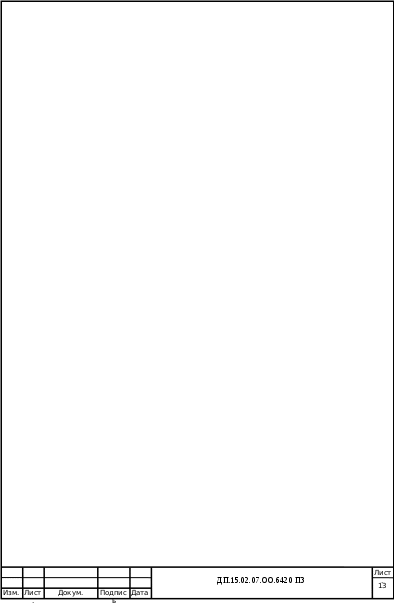
Датчик TIA(1) установленный на щите предназначен для измерения температуры и регулирования подачи гидроочищенного сырья; Датчик QICA(2) установленный на щите предназначен для измерения и регулирования концентрации дымовых газов на выходе; Датчик FCA(3-1) установленный на щите предназначен для регулирования расхода подачи воздуха на регенератор Р-2 и сигнализирования; Датчик QIRA(4) установленный на щите предназначен для показания концентрации и регистрирования полученных данных; Датчики FCA(3-2;3-3;3-4;3-5) установленные на щите предназначены для и регулирования расхода, подачи сырья, а также сигнализирования; Датчик установленный на щите FCRA(5-1) предназначен для измерения и регулирования расхода из колонны К-1 также регистрирования полученных данных; Датчик FСRA(5-2) установленный на щите предназначен для измерения и регулирования подачи расхода тяжелого газойля и регистрирования полученных данных; Датчик FTCA установленный на щите предназначен для измерения и регулирования расхода и температуры Газов на АГФУ а также сигнализирования.
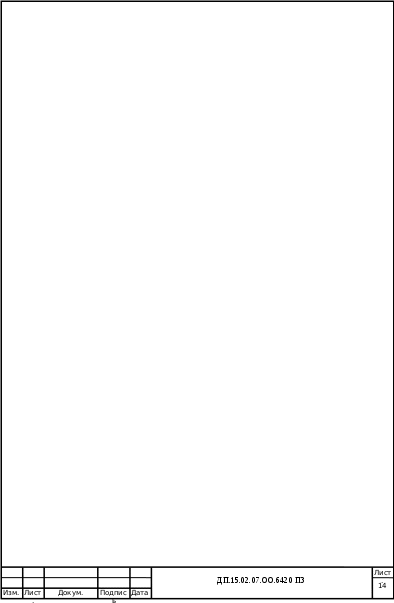
3.1 Устройство и работа прибора Метран – 150
Главным параметром при процессе каталитического крекинга с применением реакционных аппаратов является давление. Для измерения этого параметра я выбрал прибор метран-150. Метран 150 (Рисунок 5) - многопредельный микропроцессорный датчик давления. Метран-150 — умный, современный датчик избыточного, абсолютного, дифференциального (разности), гидростатического давлений, а также давления-разрежения. Цифровой датчик предназначен для постоянного измерения избыточного, вакуумметрического и абсолютного давлений, а также перепада давлений с мгновенным преобразованием полученного значения в унифицированный аналоговый токовый выходной сигнал. Технические характеристики М 150 варьируются в зависимости от особенностей исполнения модели. Датчик может измерять давление тех сред, которые не вызывают коррозионные изменения материалов, с ними контактирующих.
Принцип действия: заключается в том, что при подаче давления в камеры измерительного блока; оно способствует деформации чувствительного элемента и изменяет электрический сигнал.
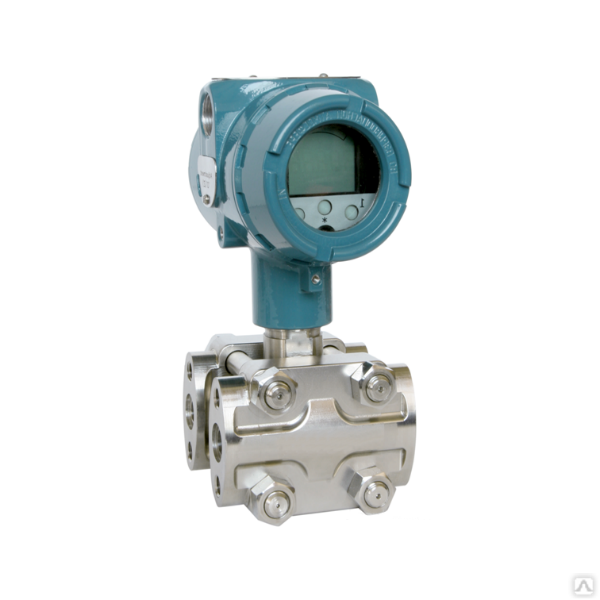
Рисунок 5 – Расходомер Метран – 150
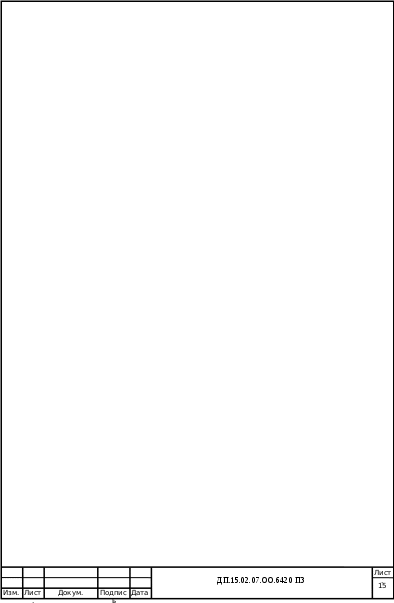
Перед включением датчиков убедитесь в соответствии их установки и монтажа указаниям. Подключите питание к датчику. Через 0,5 мин после включения электрического питания проверьте и, при необходимости, проведите корректировку значение выходного сигнала, соответствующее нижнему пределу измерений. Эта корректировка должна производиться после подачи и сброса измеряемого параметра, составляющего 80-100% верхнего предела измерений.
При заполнении измерительных камер датчика разности давлений необходимо следить за тем, чтобы в камерах датчика не осталось пробок газа (при измерении разности давлений жидких сред) или жидкости (при измерении разности давлений газа). Заполнение камер датчика жидкостью осуществляется после установки его в рабочее положение. Подача жидкости производится под небольшим давлением (желательно самотеком) одновременно в обе камеры при открытых дренажных клапанах. После того, как жидкость начинает вытекать через дренажные клапаны, их следует закрыть. Для продувки камер датчика и слива конденсата во фланцах сенсора имеются дренажные клапаны, ввернутые в пробки.
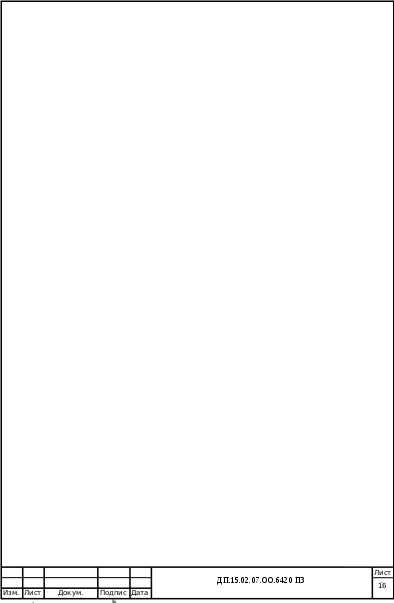