Файл: Особенности технологии непрерывной разливки высокоуглеродистой стали.docx
ВУЗ: Не указан
Категория: Не указан
Дисциплина: Не указана
Добавлен: 22.11.2023
Просмотров: 484
Скачиваний: 9
ВНИМАНИЕ! Если данный файл нарушает Ваши авторские права, то обязательно сообщите нам.
СОДЕРЖАНИЕ
1 СОРТОВАЯ МНЛЗ ЭСПЦ ПАО «ММК»
2 ТЕХНОЛОГИЯ РАЗЛИВКИ СТАЛИ ЗАКРЫТОЙ СТРУЕЙ
3 РАСЧЕТ ОСНОВНЫХ ПАРАМЕТРОВ РАЗЛИВКИ СТАЛИ МАРКИ 80 НА СОРТОВОЙ МНЛЗ
3.2 Продолжительность затвердевания сортовой непрерывнолитой заготовки
3.3 Скорость разливки металла и диаметр каналов разливочных стаканов
3.4 Скорость вытягивания заготовки из кристаллизатора
3.5 Расход материалов для смазки в кристаллизаторе
3.6 Параметры кристаллизатора и направляющих элементов вторичного охлаждения
3.7 Режим первичного охлаждения заготовки
3.8 Режим вторичного охлаждения заготовки
4 АНАЛИЗ КАЧЕСТВА СОРТОВЫХ НЕПРЕРЫВНОЛИТЫХ ЗАГОТОВОК ИЗ СТАЛИ МАРКИ 80
мм;
– наличие гранул в смеси, а также отсутствие в ней нефелинового концентрата, оптимальная основность и низкое содержание оксидов алюминия способствуют улучшению смазывающей способности шлака, формирующегося при расплавлении смеси. В результате этого сила трения при вытягивании заготовки из кристаллизатора снижается примерно вдвое при применении гранулированной шлакообразующей смеси по сравнению с порошкообразной.
В качестве основного шлакообразующего компонента при изготовлении гранулированных смесей в ПАО «Магнитогорский металлургический комбинат» используется портландцемент. Другими компонентами являются аморфный графит, плавикошпатовые концентраты, силикатная глыба, датолитовый и кварцевый концентраты. Для снижения себестоимости шлакообразующей смеси кварцевый концентрат впоследствии был заменен формовочным песком. Гранулометрический состав смеси в основном (на 75…85 %) представлен фракцией 0,2…1,0 мм. Расход смеси составляет 0,8…1,0 кг на тонну разливаемой стали.
Шлакообразующая смесь имеет основность 0,8…1,1, влажность – не более 0,5 %,ее температура плавления не превышает 1150…1200 ºС. При разливке стали с разной температурой рекомендуется иметь следующие значения вязкости шлака:
Температура металла, °С 1500 1250…1300
Вязкость шлака, Па·с 0,04…0,10 0,3…1,0.
Поверхность смеси в кристаллизаторе должна быть темной. В случае уменьшения толщины слоя смеси, признаком которого является яркое ее свечение или появление поверхности жидкого металла, производится дополнительная присадка смеси в кристаллизатор. При комковании смеси осуществляется ее обновление.
Рабочий уровень жидкого металла в гильзовом кристаллизаторе сортовой МНЛЗ находится на расстоянии 100…150 мм от верхней кромки медной гильзы, имеющей высоту 900 мм. Шлакообразующая смесь вводится на поверхность жидкого металла сразу после наполнения кристаллизатора до рабочего уровня.
Прежде, чем жидкий металл достиг в кристаллизаторе рабочего уровня, производится включение привода вытягивания заготовки из кристаллизатора. На сортовой МНЛЗ это осуществляется при заполнении гильзового кристаллизатора металлом на 75 % его высоты. Одновременно с пуском машины включается механизм качания кристаллизатора. По громкой связи передается сообщение: «Машина пущена».
Вытягивание заготовки из кристаллизатора начинается с минимальной скоростью, чтобы исключить отрыв головки затравки от заготовки.
Разгон машины до достижения регламентированного уровня скорости вытягивания заготовки из кристаллизатора производится в автоматическом режиме.
Промежуточный ковш наполняется до достижения рабочего уровня жидкого металла в нем.
При разливке высокоуглеродистой стали с содержанием углерода 0,65…0,90 % и низколегированной стали на одной из сортовых МНЛЗ используется устройство электромагнитного перемешивания, установленное в нижней части каждого кристаллизатора. Рациональный режим перемешивания с использованием пониженных значений частоты и силы тока: 3,0…3,5 Гц и 300…350 Aпозволяет повысить плотность осевой части отливаемой заготовки и улучшить качество горячекатаного проката.
Начальный период разливки металла завершается после отделения затравки от заготовки. После выхода головки затравки из тянуще-правильной клети сортовой машины происходит ее отделение. После отделения гибкая затравка поднимается вверх и устанавливается на выдвижные упоры. С выдвижных упоров затравка поднимается машиной для ввода затравки на разливочную площадку, где она находится до следующего цикла разливки. Жесткая затравка принимается манипулятором и перемещается им в положение затравки для ее подготовки к разливке. В случае невозможности отделения головки гибкой заготовки из-за приваривания к заготовке производится отделение только корпуса затравки. Это осуществляется при помощи механизма аварийного отделения затравки. Корпус затравки захватывается за хвостовую часть и лебедкой поднимает вверх на разливочную площадку.
Основной период разливки металла характеризуется стабильностью процесса вытягивания заготовки из кристаллизатора с постоянной рабочей скоростью.
После разливки 8…9 % массы металла в сталеразливочном ковше производится первое измерение температуры металла в промежуточном ковше. Второе измерение температуры металла производится после разливки половины металла и третье измерение – после разливки примерно 90 % массы металла, находившегося в сталеразливочном ковше.
В соответствии с первым результатом измерения температуры металла выбирается рабочая скорость вытягивания заготовки из кристаллизатора. На основании последующих замеров производится корректировка выбранной скорости.
Величина рабочей скорости вытягивания заготовки из кристаллизатора выбирается в зависимости от следующих параметров:
– группы марок стали;
– размеров поперечного сечения отливаемой заготовки;
– температуры металла в промежуточном ковше;
– содержания серы в разливаемом металле.
Каждая марка разливаемой стали относится к определенной группе.
С увеличением сложности марки разливаемой стали скорость вытягивания заготовки из кристаллизатора уменьшается при постоянстве значений других параметров. На рисунке 2.2 представлены данные о диапазоне изменения и средней величине скорости вытягивания сортовой непрерывнолитой заготовки с размерами поперечного сечения 150×150 мм из стали различных марок.
Из рисунка следует, что с наибольшей скоростью из кристаллизатора вытягивается заготовка из углеродистой стали обыкновенного качества марки Ст3сп. Наблюдается тенденция снижения скорости вытягивания заготовки при увеличении содержания в металле углерода и легирующего элемента.
Чем больше площадь поперечного сечения отливаемой заготовки, тем меньше скорость ее вытягивания из кристаллизатора при постоянстве других параметров.
С увеличением температуры металла в промежуточном ковше скорость вытягивания заготовки из кристаллизатора уменьшается.
– минимальное значение;
– среднее значение;
– максимальное значение
Рисунок 2.1 - Диапазон изменения и средняя величина скорости вытягивания из кристаллизатора сортовой заготовки сечением 150×150 мм из стали различных марок
При увеличении содержания серы в разливаемом металле возрастает опасность образования горячих трещин и аварийных прорывов жидкого металла под кристаллизатором. Поэтому с увеличением содержания серы в металле скорость вытягивания заготовки из кристаллизатора должна снижаться.
Рабочая скорость вытягивания заготовки из кристаллизатора выбирается с учетом информации о химическом составе металла после окончания ковшевой обработки, а также после получения результатов анализа первой пробы металла с разливки.
Для определения химического анализа в процессе разливки отбираются четыре пробы металла.
Первая проба отбирается через 10…12 мин после начала разливки металла, две маркировочные пробы – в середине разливки и последняя – за 5…10 мин до конца разливки. Информация о результатах анализа металла первой
разливочной пробы должны быть известна не позднее, чем через 35 мин после начала разливки для своевременного уточнения задания по выбору длины мерных частей заготовки.
Рабочая скорость вытягивания заготовки из кристаллизатора в основной период разливки должна быть неизменной. Подача жидкого металла в кристаллизатор из промежуточного ковша синхронизируется со скоростью вытягивания заготовки таким образом, чтобы уровень металла в кристаллизаторе был постоянен.
Частота качания кристаллизатора увеличивается с возрастанием скорости вытягивания заготовки.
Выбранному уровню рабочей скорости вытягивания заготовки из кристаллизатора соответствует регламентированный расход воды на первичное охлаждение заготовки в кристаллизаторе. Например, сборный кристаллизатор двухручьевой слябовой МНЛЗ при отливке заготовок с размерами поперечного сечения 250×(1250…1550) мм с рабочей скоростью вытягивания охлаждается водой в количестве не менее 350 м3/ч.
В соответствии с рабочей скоростью вытягивания заготовки из кристаллизатора автоматически или в ручном режиме устанавливается расход охладителей в зоне вторичного охлаждения (ЗВО) МНЛЗ. Расход охладителя также зависит и от группы марок разливаемой стали, типа и размеров отливаемой заготовки, конструктивных особенностей МНЛЗ.
У сортовой заготовки в зоне вторичного охлаждения машины охлаждаются все четыре грани заготовки.
Разделение отлитой заготовки на мерные части производится путем осуществления поперечной порезки заготовок, как правило, на машине газовой резки. Мерные части заготовки маркируются с указанием номера плавки, номера ручья МНЛЗ и порядкового номера отрезанной мерной части заготовки.
Головная часть сортовой заготовки с вмороженными холодильниками отрезается. Величина технологической обрези регламентируется в зависимости от назначения металла.
Отрезанные заготовки мерной длины отправляются по транспортно-отделочной линии в транспортно-отделочное отделение. В случае остановки линии заготовки складируются в копильниках.
Перед окончанием разливки защитная труба между сталеразливочным и промежуточным ковшами убирается. При появлении шлака в струе жидкого металла закрывается шиберный затвор сталеразливочного ковша. Опорожненный сталеразливочный ковш при помощи стенда перемещается из позиции разливки в позицию подготовки. При помощи крана с ковша снимается крышка, убирается гидроцилиндр шиберного затвора. После этого сталеразливочный ковш краном снимается со стенда.
При уменьшении уровня жидкого металла в промежуточном ковше до отметки около 250 мм прекращается подача металла в кристаллизаторы из-за опасности образования воронок и затягивания в них шлака. В начале рекомендуется закрывать стопора крайних ручьев, а затем – средних. Это связано с меньшей температурой металла в промежуточном ковше над дальними от «бойного» места ручьями.
Промежуточный ковш на тележке поднимается в верхнюю позицию и перемещается из рабочего положения в резервное, производится отсоединение погружных стаканов.
В хвостовой части заготовки образуется усадочная раковина. Эта часть заготовки с раковиной должна удаляться в технологическую обрезь. На величину этой обрези решающее влияние оказывает не объём, а форма образующейся раковины. Желательно иметь концентрированную усадочную раковину открытого типа с полусферическим дном. Такая раковина имеет относительно небольшую глубину. Для получения желаемой формы усадочной раковины существуют специальные технологические приёмы. Эти приемы различаются при отливке слябовой и сортовой заготовок. Данное различие объясняется неодинаковыми возможностями утяжки металла хвостовой части заготовки разного типа для сокращения наружных размеров стенок усадочной раковины.
Наибольшими возможностями для этого обладает слябовая заготовка при условии, что усадочная раковина не является закрытой сверху мостом затвердевшего металла, который жестко стягивает широкие стенки раковины.
При отливке сортовой заготовки ее затвердевший каркас обладает значительно большей жесткостью по сравнению со слябовой заготовкой. Этот каркас не позволяет получить заметную утяжку стенок усадочной раковины в хвостовой части заготовки для уменьшения их высоты. На снижение глубины усадочной раковины благоприятно влияет утепление зеркала металла в кристаллизаторе шлакообразующей смесью. Поэтому удаление смеси из кристаллизатора сортовой МНЛЗ в конце разливки не производится.
5>
– наличие гранул в смеси, а также отсутствие в ней нефелинового концентрата, оптимальная основность и низкое содержание оксидов алюминия способствуют улучшению смазывающей способности шлака, формирующегося при расплавлении смеси. В результате этого сила трения при вытягивании заготовки из кристаллизатора снижается примерно вдвое при применении гранулированной шлакообразующей смеси по сравнению с порошкообразной.
В качестве основного шлакообразующего компонента при изготовлении гранулированных смесей в ПАО «Магнитогорский металлургический комбинат» используется портландцемент. Другими компонентами являются аморфный графит, плавикошпатовые концентраты, силикатная глыба, датолитовый и кварцевый концентраты. Для снижения себестоимости шлакообразующей смеси кварцевый концентрат впоследствии был заменен формовочным песком. Гранулометрический состав смеси в основном (на 75…85 %) представлен фракцией 0,2…1,0 мм. Расход смеси составляет 0,8…1,0 кг на тонну разливаемой стали.
Шлакообразующая смесь имеет основность 0,8…1,1, влажность – не более 0,5 %,ее температура плавления не превышает 1150…1200 ºС. При разливке стали с разной температурой рекомендуется иметь следующие значения вязкости шлака:
Температура металла, °С 1500 1250…1300
Вязкость шлака, Па·с 0,04…0,10 0,3…1,0.
Поверхность смеси в кристаллизаторе должна быть темной. В случае уменьшения толщины слоя смеси, признаком которого является яркое ее свечение или появление поверхности жидкого металла, производится дополнительная присадка смеси в кристаллизатор. При комковании смеси осуществляется ее обновление.
Рабочий уровень жидкого металла в гильзовом кристаллизаторе сортовой МНЛЗ находится на расстоянии 100…150 мм от верхней кромки медной гильзы, имеющей высоту 900 мм. Шлакообразующая смесь вводится на поверхность жидкого металла сразу после наполнения кристаллизатора до рабочего уровня.
Прежде, чем жидкий металл достиг в кристаллизаторе рабочего уровня, производится включение привода вытягивания заготовки из кристаллизатора. На сортовой МНЛЗ это осуществляется при заполнении гильзового кристаллизатора металлом на 75 % его высоты. Одновременно с пуском машины включается механизм качания кристаллизатора. По громкой связи передается сообщение: «Машина пущена».
Вытягивание заготовки из кристаллизатора начинается с минимальной скоростью, чтобы исключить отрыв головки затравки от заготовки.
Разгон машины до достижения регламентированного уровня скорости вытягивания заготовки из кристаллизатора производится в автоматическом режиме.
Промежуточный ковш наполняется до достижения рабочего уровня жидкого металла в нем.
При разливке высокоуглеродистой стали с содержанием углерода 0,65…0,90 % и низколегированной стали на одной из сортовых МНЛЗ используется устройство электромагнитного перемешивания, установленное в нижней части каждого кристаллизатора. Рациональный режим перемешивания с использованием пониженных значений частоты и силы тока: 3,0…3,5 Гц и 300…350 Aпозволяет повысить плотность осевой части отливаемой заготовки и улучшить качество горячекатаного проката.
Начальный период разливки металла завершается после отделения затравки от заготовки. После выхода головки затравки из тянуще-правильной клети сортовой машины происходит ее отделение. После отделения гибкая затравка поднимается вверх и устанавливается на выдвижные упоры. С выдвижных упоров затравка поднимается машиной для ввода затравки на разливочную площадку, где она находится до следующего цикла разливки. Жесткая затравка принимается манипулятором и перемещается им в положение затравки для ее подготовки к разливке. В случае невозможности отделения головки гибкой заготовки из-за приваривания к заготовке производится отделение только корпуса затравки. Это осуществляется при помощи механизма аварийного отделения затравки. Корпус затравки захватывается за хвостовую часть и лебедкой поднимает вверх на разливочную площадку.
Основной период разливки металла характеризуется стабильностью процесса вытягивания заготовки из кристаллизатора с постоянной рабочей скоростью.
После разливки 8…9 % массы металла в сталеразливочном ковше производится первое измерение температуры металла в промежуточном ковше. Второе измерение температуры металла производится после разливки половины металла и третье измерение – после разливки примерно 90 % массы металла, находившегося в сталеразливочном ковше.
В соответствии с первым результатом измерения температуры металла выбирается рабочая скорость вытягивания заготовки из кристаллизатора. На основании последующих замеров производится корректировка выбранной скорости.
Величина рабочей скорости вытягивания заготовки из кристаллизатора выбирается в зависимости от следующих параметров:
– группы марок стали;
– размеров поперечного сечения отливаемой заготовки;
– температуры металла в промежуточном ковше;
– содержания серы в разливаемом металле.
Каждая марка разливаемой стали относится к определенной группе.
С увеличением сложности марки разливаемой стали скорость вытягивания заготовки из кристаллизатора уменьшается при постоянстве значений других параметров. На рисунке 2.2 представлены данные о диапазоне изменения и средней величине скорости вытягивания сортовой непрерывнолитой заготовки с размерами поперечного сечения 150×150 мм из стали различных марок.
Из рисунка следует, что с наибольшей скоростью из кристаллизатора вытягивается заготовка из углеродистой стали обыкновенного качества марки Ст3сп. Наблюдается тенденция снижения скорости вытягивания заготовки при увеличении содержания в металле углерода и легирующего элемента.
Чем больше площадь поперечного сечения отливаемой заготовки, тем меньше скорость ее вытягивания из кристаллизатора при постоянстве других параметров.
С увеличением температуры металла в промежуточном ковше скорость вытягивания заготовки из кристаллизатора уменьшается.
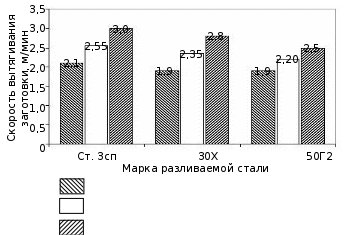
– минимальное значение;
– среднее значение;
– максимальное значение
Рисунок 2.1 - Диапазон изменения и средняя величина скорости вытягивания из кристаллизатора сортовой заготовки сечением 150×150 мм из стали различных марок
При увеличении содержания серы в разливаемом металле возрастает опасность образования горячих трещин и аварийных прорывов жидкого металла под кристаллизатором. Поэтому с увеличением содержания серы в металле скорость вытягивания заготовки из кристаллизатора должна снижаться.
Рабочая скорость вытягивания заготовки из кристаллизатора выбирается с учетом информации о химическом составе металла после окончания ковшевой обработки, а также после получения результатов анализа первой пробы металла с разливки.
Для определения химического анализа в процессе разливки отбираются четыре пробы металла.
Первая проба отбирается через 10…12 мин после начала разливки металла, две маркировочные пробы – в середине разливки и последняя – за 5…10 мин до конца разливки. Информация о результатах анализа металла первой
разливочной пробы должны быть известна не позднее, чем через 35 мин после начала разливки для своевременного уточнения задания по выбору длины мерных частей заготовки.
Рабочая скорость вытягивания заготовки из кристаллизатора в основной период разливки должна быть неизменной. Подача жидкого металла в кристаллизатор из промежуточного ковша синхронизируется со скоростью вытягивания заготовки таким образом, чтобы уровень металла в кристаллизаторе был постоянен.
Частота качания кристаллизатора увеличивается с возрастанием скорости вытягивания заготовки.
Выбранному уровню рабочей скорости вытягивания заготовки из кристаллизатора соответствует регламентированный расход воды на первичное охлаждение заготовки в кристаллизаторе. Например, сборный кристаллизатор двухручьевой слябовой МНЛЗ при отливке заготовок с размерами поперечного сечения 250×(1250…1550) мм с рабочей скоростью вытягивания охлаждается водой в количестве не менее 350 м3/ч.
В соответствии с рабочей скоростью вытягивания заготовки из кристаллизатора автоматически или в ручном режиме устанавливается расход охладителей в зоне вторичного охлаждения (ЗВО) МНЛЗ. Расход охладителя также зависит и от группы марок разливаемой стали, типа и размеров отливаемой заготовки, конструктивных особенностей МНЛЗ.
У сортовой заготовки в зоне вторичного охлаждения машины охлаждаются все четыре грани заготовки.
Разделение отлитой заготовки на мерные части производится путем осуществления поперечной порезки заготовок, как правило, на машине газовой резки. Мерные части заготовки маркируются с указанием номера плавки, номера ручья МНЛЗ и порядкового номера отрезанной мерной части заготовки.
Головная часть сортовой заготовки с вмороженными холодильниками отрезается. Величина технологической обрези регламентируется в зависимости от назначения металла.
Отрезанные заготовки мерной длины отправляются по транспортно-отделочной линии в транспортно-отделочное отделение. В случае остановки линии заготовки складируются в копильниках.
Перед окончанием разливки защитная труба между сталеразливочным и промежуточным ковшами убирается. При появлении шлака в струе жидкого металла закрывается шиберный затвор сталеразливочного ковша. Опорожненный сталеразливочный ковш при помощи стенда перемещается из позиции разливки в позицию подготовки. При помощи крана с ковша снимается крышка, убирается гидроцилиндр шиберного затвора. После этого сталеразливочный ковш краном снимается со стенда.
При уменьшении уровня жидкого металла в промежуточном ковше до отметки около 250 мм прекращается подача металла в кристаллизаторы из-за опасности образования воронок и затягивания в них шлака. В начале рекомендуется закрывать стопора крайних ручьев, а затем – средних. Это связано с меньшей температурой металла в промежуточном ковше над дальними от «бойного» места ручьями.
Промежуточный ковш на тележке поднимается в верхнюю позицию и перемещается из рабочего положения в резервное, производится отсоединение погружных стаканов.
В хвостовой части заготовки образуется усадочная раковина. Эта часть заготовки с раковиной должна удаляться в технологическую обрезь. На величину этой обрези решающее влияние оказывает не объём, а форма образующейся раковины. Желательно иметь концентрированную усадочную раковину открытого типа с полусферическим дном. Такая раковина имеет относительно небольшую глубину. Для получения желаемой формы усадочной раковины существуют специальные технологические приёмы. Эти приемы различаются при отливке слябовой и сортовой заготовок. Данное различие объясняется неодинаковыми возможностями утяжки металла хвостовой части заготовки разного типа для сокращения наружных размеров стенок усадочной раковины.
Наибольшими возможностями для этого обладает слябовая заготовка при условии, что усадочная раковина не является закрытой сверху мостом затвердевшего металла, который жестко стягивает широкие стенки раковины.
При отливке сортовой заготовки ее затвердевший каркас обладает значительно большей жесткостью по сравнению со слябовой заготовкой. Этот каркас не позволяет получить заметную утяжку стенок усадочной раковины в хвостовой части заготовки для уменьшения их высоты. На снижение глубины усадочной раковины благоприятно влияет утепление зеркала металла в кристаллизаторе шлакообразующей смесью. Поэтому удаление смеси из кристаллизатора сортовой МНЛЗ в конце разливки не производится.
5>