Файл: Особенности технологии непрерывной разливки высокоуглеродистой стали.docx
ВУЗ: Не указан
Категория: Не указан
Дисциплина: Не указана
Добавлен: 22.11.2023
Просмотров: 488
Скачиваний: 9
ВНИМАНИЕ! Если данный файл нарушает Ваши авторские права, то обязательно сообщите нам.
СОДЕРЖАНИЕ
1 СОРТОВАЯ МНЛЗ ЭСПЦ ПАО «ММК»
2 ТЕХНОЛОГИЯ РАЗЛИВКИ СТАЛИ ЗАКРЫТОЙ СТРУЕЙ
3 РАСЧЕТ ОСНОВНЫХ ПАРАМЕТРОВ РАЗЛИВКИ СТАЛИ МАРКИ 80 НА СОРТОВОЙ МНЛЗ
3.2 Продолжительность затвердевания сортовой непрерывнолитой заготовки
3.3 Скорость разливки металла и диаметр каналов разливочных стаканов
3.4 Скорость вытягивания заготовки из кристаллизатора
3.5 Расход материалов для смазки в кристаллизаторе
3.6 Параметры кристаллизатора и направляющих элементов вторичного охлаждения
3.7 Режим первичного охлаждения заготовки
3.8 Режим вторичного охлаждения заготовки
4 АНАЛИЗ КАЧЕСТВА СОРТОВЫХ НЕПРЕРЫВНОЛИТЫХ ЗАГОТОВОК ИЗ СТАЛИ МАРКИ 80
Машина оборудована двумя сталеразливочными стендами полупортального типа, каждый из которых имеет одно место для сталеразливочного ковша (рисунок 1.2). Наличие двух стендов позволяет осуществлять разливку стали методом «плавка на плавку». Номинальный уровень жидкого металла в промежуточном ковше равен 700 мм, максимальный – 800 мм. В ковше (рисунок 1.3) установлено пять разливочных стаканов. Регулирование подачи металла из ковша в кристаллизаторы зависит от способа разливки стали. При разливке открытой струей в качестве дозирующих элементов металлической проводки применяются постоянные верхние и сменные нижние циркониевые стаканы. Регулирование подачи жидкого металла осуществляется путем смены нижних стаканов, имеющих разный (15…19 мм) диаметр калиброванных отверстий. Смена этих стаканов осуществляется при помощи специальных механизмов быстрой замены.
В режиме разливки закрытой струей для регулирования подачи металла из промежуточного ковша в кристаллизаторы применяются стопора промежуточного ковша, представляющие собой корундографитовые моноблоки с нижней пробкой из периклазоуглеродистого материала. Жидкий металл поступает в кристаллизаторы под уровень через погружные стаканы с осевыми отверстиями.
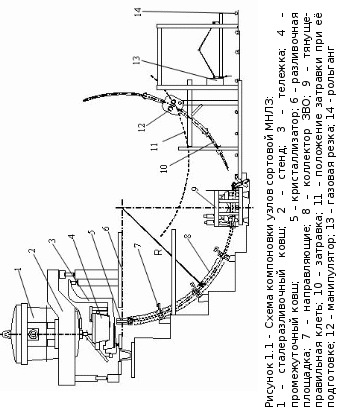
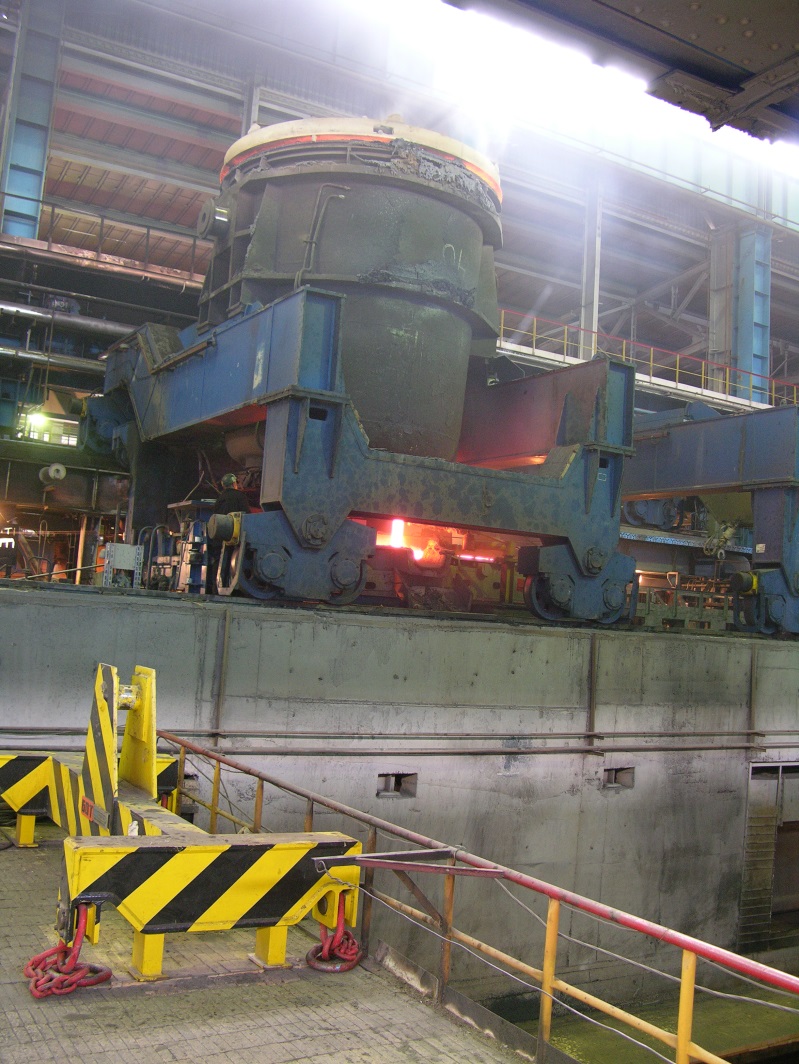
Рисунок 1.2 - Откатной сталеразливочный стенд сортовой МНЛЗ
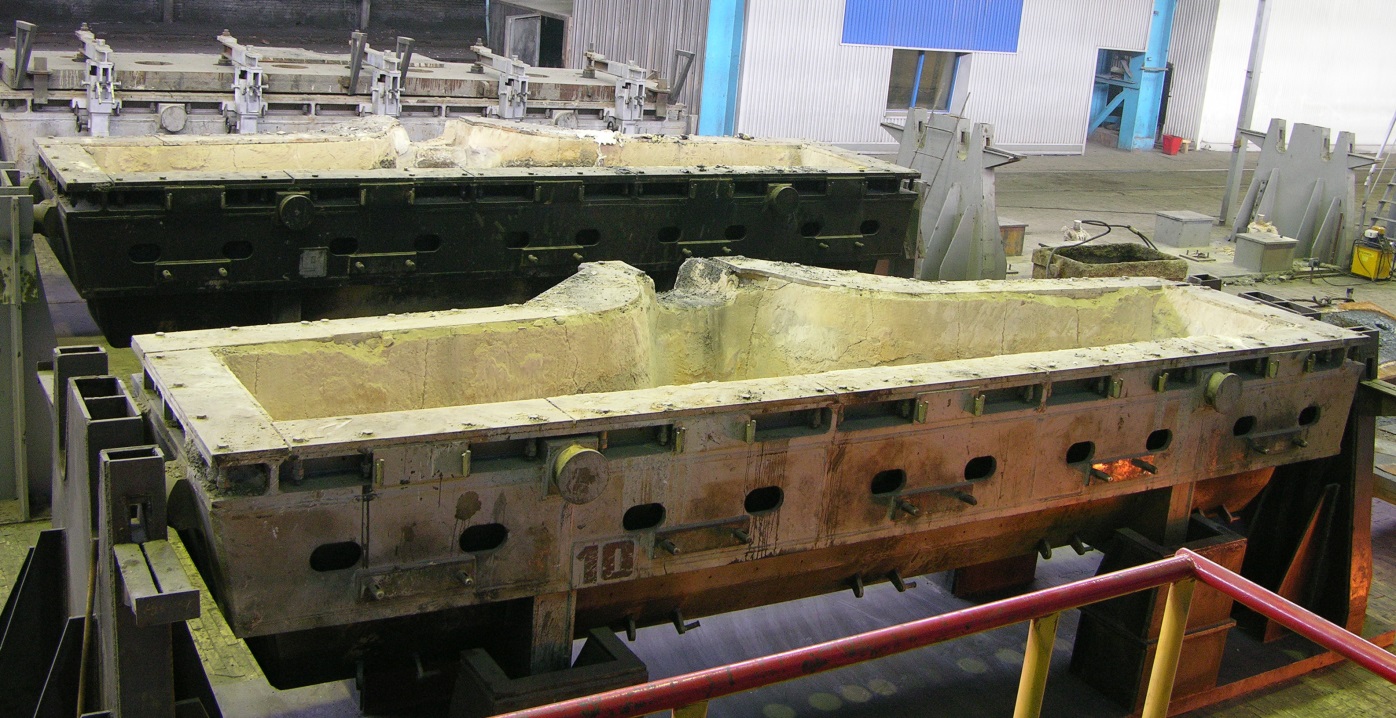
Рисунок 1.3 – Промежуточный ковш сортовой МНЛЗ
Радиальный кристаллизатор представляет собой гильзу с внутренней поверхностью параболического профиля. На одной раме с кристаллизатором сразу под ним крепятся ролики диаметром 100 мм, поддерживающие заготовку со всех четырех сторон (рисунок 1.4).
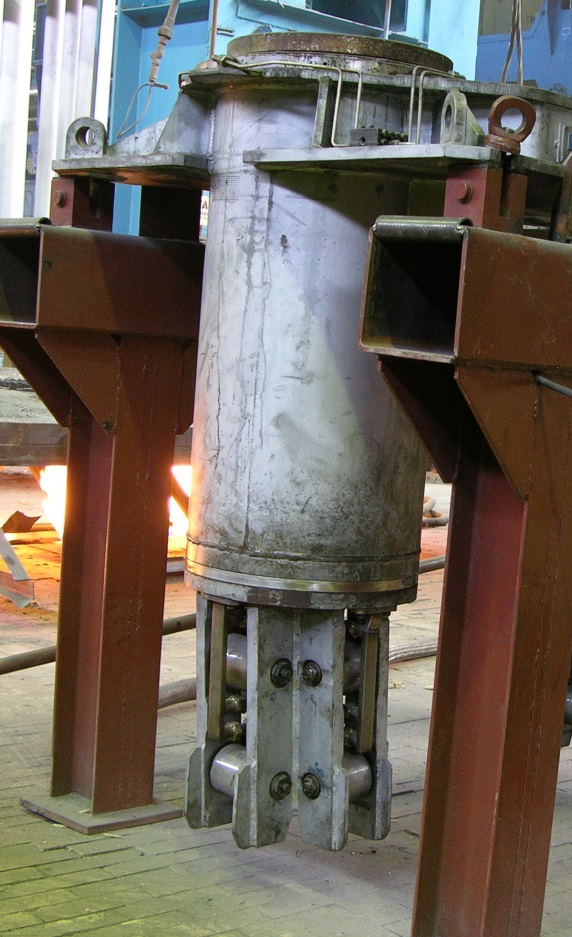
Рисунок 1. 4 - Гильзовый кристаллизатор с двумя рядами
поддерживающих роликов
При отливке заготовок сечением 124×124 мм ставится один ряд опорных роликов, а при отливке заготовок других сечений – два ряда роликов. Кристаллизатор оснащен радиометрической системой контроля уровня жидкого металла. В нее входят проволочный датчик
Co60 со стороны малого радиуса и счётчик вспышек со стороны большого радиуса. Высота измеряемого участка составляет до 210 мм в зависимости от толщины отливаемой заготовки. Информация об изменении уровня металла используется для соответствующего изменения скорости вытягивания заготовки из кристаллизатора путем автоматизированного управления приводом тянуще-правильной клети машины.
При разливке открытой струей для смазки в кристаллизатор через кольцевой зазор подается растительное (рафинированное рапсовое) или синтетическое масло фирм «Mobil» или «Shell». В режиме разливки закрытой струей роль смазки в кристаллизаторе выполняет шлакообразующая смесь.
Кристаллизатор одной из МНЛЗ имеет устройство электромагнитного перемешивания стали фирмы «ABB Automation Systems». Это устройство представляет собой укороченную катушку, расположенную с внешней стороны нижней части кристаллизатора (рисунок 1.5).
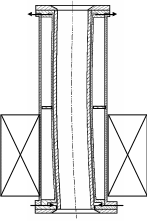
Рисунок 1.5 - Схема расположения устройства электромагнитного перемешивания металла в кристаллизаторе
Частота питающего тока равна 3…5,5 Гц. Напряжение составляет 500 В, а сила тока – 300…500 А. Устройство обладает кажущейся мощностью 433 кВ·А.
Механизм качания кристаллизатора имеет гидравлический привод. Параметры качания кристаллизатора могут регулироваться автоматически в процессе разливки в зависимости от скорости вытягивания заготовки: частота качания – в интервале от 30 до 300 кач./мин, амплитуда перемещения – от 0 до 9 мм.
Жесткая недеформируемая затравка состоит из скреплённых болтами сегментов и съемной головки. Она имеет радиус кривизны, соответствующий базовому радиусу МНЛЗ. Длина затравки составляет около 14,1 м. На головку затравки крепится расходуемый холодильник.
Ниже кристаллизатора для направления и поддерживания заготовки располагается направляющее устройство. Оно состоит из трех отдельных роликовых блоков. В каждый блок входят два ролика диаметром 160 мм. Ролик внешней дуги закреплен стационарно. Он подключен к системе централизованной смазки и имеет внутреннее водяное охлаждение. Ролик внутренней дуги прижимается к заготовке с помощью противовеса и не смазывается. Охлаждение ролика производится системой вторичного охлаждения заготовки. Зона вторичного охлаждения заготовки имеет общую протяженность 9,8 м. Она включает в себя четыре зоны со следующей характеристикой:
Зона I II III IV
Длина, м 0,34 2,36 3,46 3,61
Количество форсунок, шт. 12 24 20 20.
В первой зоне – от низа кристаллизатора до последнего ряда поддерживающих роликов, применяется водяное охлаждение, а во всех остальных – водовоздушное охлаждение. Коллекторы системы вторичного охлаждения крепятся на роликовых блоках. Для охлаждения поверхности заготовки используется система оросительного охлаждения. При помощи замкнутой системы охлаждаются направляющие ролики внешней дуги, ролики тянуще-правильной клети, ролики рольганга и машины газовой резки.
Тянуще-правильная клеть (рисунок 1.6) имеет три нижних стационарно установленных ролика и два верхних прижимных ролика диаметром 350 мм.
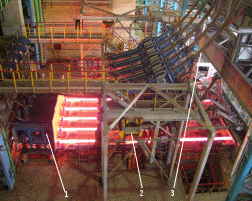
Рисунок 1.6 - Горизонтальная часть сортовой МНЛЗ:
1 – тянуще-правильные клети; 2 – участок резки; 3 – жесткие затравки
Прижим роликов осуществляется с помощью гидроцилиндров. Передние верхний и нижний ролики являются приводными. Охлаждение роликов производится через внутренние каналы. Для охлаждения клети предназначен водоохлаждаемый тоннель. Задний верхний ролик может опускаться для отделения затравки от заготовки.
После тянуще-правильной клети выпрямленная заготовка поступает на рольганг из пяти роликов диаметром 270 мм. Над пятым роликом расположен верхний приводной ролик, который может перемещаться вверх-вниз, для вытягивания заготовки из тянуще-правильной клети и транспортировки на отводящий рольганг.
На каждом ручье МНЛЗ для разделения заготовки на мерные части имеется машина газовой резки. Она состоит из одной навесной горелки с электромеханическим приводом маятникового типа, пневматического зажимного устройства, ролика для измерения длины, грануляционного оборудования и оборудования для охлаждения. Максимальная длина перемещения горелки составляет 3 м. Сбор и удаление шлама, окалины и обрези производится в желоба из нержавеющей стали и сварные бадьи.
Разрезанные заготовки последовательно поступают на отводящий рольганг и поперечный передаточный рольганг (рисунок 1.7).
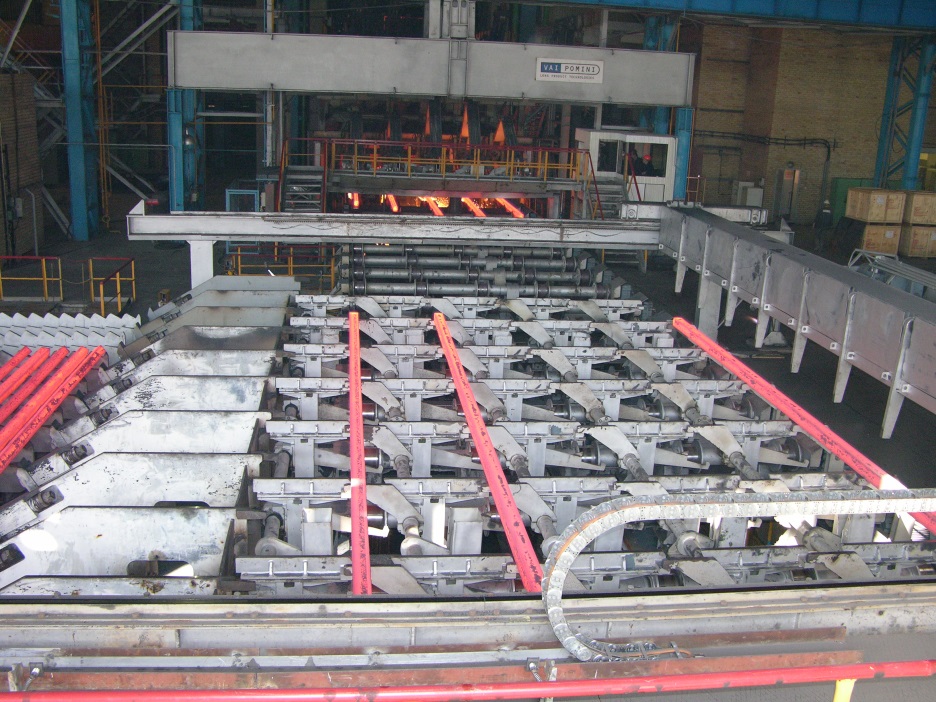

Рисунок 1.7 - Вид поперечного передаточного рольганга
С поперечного передаточного рольганга заготовки поднимаются при помощи рычагов с гидравлическим приводом на поперечное передаточное устройство. Далее заготовки перемещаются перпендикулярно направлению их вытягивания на наклонный отрезок перед холодильником. Кантующий холодильник (рисунок 1.8) служит для последующей транспортировки заготовок.
При этом заготовки квадратного сечения дополнительно поворачиваются вокруг своей продольной оси в процессе передвижения с целью обеспечения равномерного охлаждения. Заготовки из флокено- и трещиночувствительного металла должны сниматься с участка перед кантующим холодильником и помещаться в специальные теплоизолирующие термосы при помощи крана.
Сортовая МНЛЗ оснащена современной автоматизированной системой управления технологическим процессом разливки стали. Эта система позволяет осуществлять разливку в автоматизированном режиме с предоставлением полной информации в удобном интерфейсе и выдачей предупреждающих сигналов в случае возникновения аварийных ситуаций.
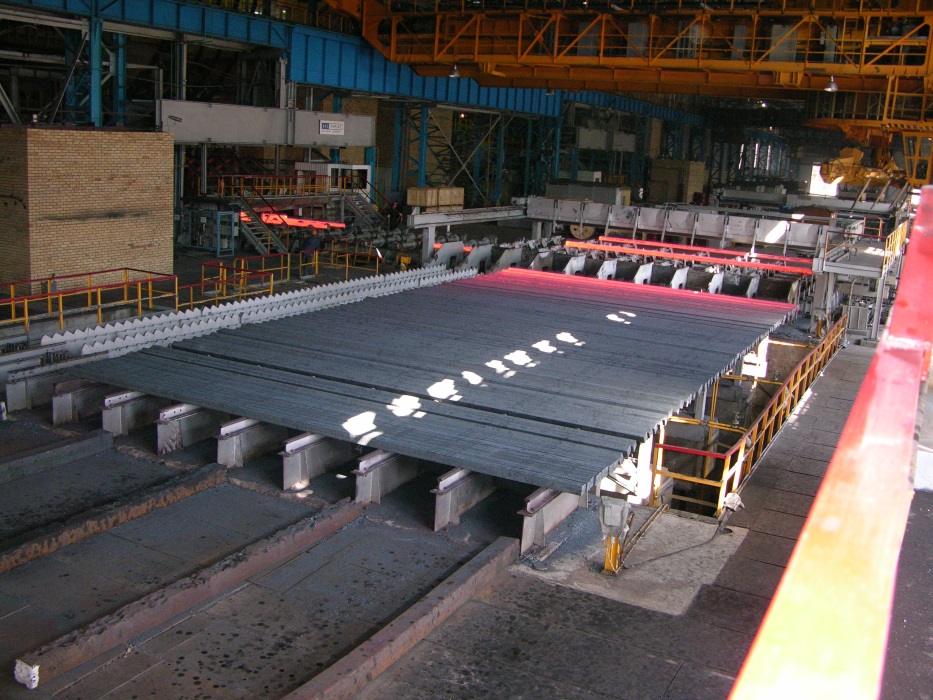
Рисунок 1.8 -. Кантующий холодильник сортовой машины
2 ТЕХНОЛОГИЯ РАЗЛИВКИ СТАЛИ ЗАКРЫТОЙ СТРУЕЙ
Подача жидкого металла из промежуточного ковша в кристаллизаторы под уровень с использованием удлиненных погружных стаканов, показанная на рисунке 2.1, является основным способом непрерывной разливки стали различного сортамента на заготовки всех типов. При использовании этого способа струя жидкого металла на участке промежуточный ковш – кристаллизатор, а также зеркало металла в кристаллизаторе защищены от вторичного окисления кислородом атмосферного воздуха. Это позволяет избежать снижения содержания растворённых в металле химических элементов, обладающих высоким сродством к кислороду (алюминия, кальция, титана и др.), увеличения содержания оксидных неметаллических включений в разлитом металле и снижения качества отлитой заготовки. Такой способ обладает более широкими возможностями для поддержания стабильного уровня жидкого металла в кристаллизаторе, гарантирующего отсутствие аварийных прорывов металла под кристаллизатором и высокое качество отливаемой заготовки.
Разливка стали начинается после открытия шиберного затвора сталеразливочного ковша. В случае отсутствия жидкого металла ковш поднимается на стенде в верхнее положение и отверстие сталеразливочного стакана прожигается кислородом, подаваемым через кислородную трубку. При непоступлении металла или плохой организации струи разливка осуществляется через второй – резервный шиберный затвор.
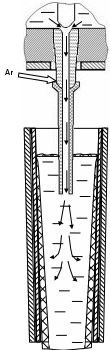
Рисунок 2.1 - Схема разливки стали на сортовой МНЛЗ закрытой струей через погружной стакан с осевым отверстием
После появления жидкого металла по громкой связи передается сообщение: «Металл в промежуточном ковше».
Ковш на стенде опускается в рабочее положение. Через короткий промежуток времени шиберный затвор закрывается и при помощи манипулятора к стакану-коллектору снизу с использованием изолирующей прокладки прижимается огнеупорная труба, предохраняющая жидкий металл от вторичного окисления атмосферным воздухом на участке сталеразливочный ковш – промежуточный ковш. В верхнюю часть полости трубы подается аргон с целью исключения эжектирования воздуха. Для этого применяется тонкая трубка с надетым шлангом, вставляемая в специальное отверстие огнеупорной трубы. После этого шиберный затвор сталеразливочного ковша открывается и разливка металла возобновляется.
Расход аргона выбирается таким, чтобы отсутствовало сильное искрение из стыка стакана-коллектора и защитной трубы.
После поднятия уровня жидкого металла в промежуточном ковше на высоту 300…400 мм от его «бойной» части, гарантирующую невозможность затягивания шлака с поверхности металла в результате образования воронок, приподнимаются стопора и начинается наполнение металлом кристаллизаторов. В случае разливки металла в три и более ручьев сначала открываются крайние стопора, а затем средние. При этом по громкой связи передается сообщение: «Металл в кристаллизаторе».
На поверхность поднимающегося в промежуточном ковше жидкого металла вводится шлакообразующая смесь. После ее расплавления должен образоваться покровной шлак определенной толщины. Шлак в промежуточном ковше выполняет следующие функции:
– препятствует вторичному окислению жидкого металла;
– снижает тепловые потери металла;
– ассимилирует (поглощает) всплывающие из металла неметаллические включения.
Расход шлакообразующей смеси в промежуточный ковш составляет около 0,3…0,5 кг на тонну металла, находящегося в ковше.
После расплавления смеси в кристаллизаторе образуется жидкоподвижный шлак, который в дополнение к трем вышеназванным функциям шлака в промежуточном ковше имеет очень важную дополнительную функцию – играет роль смазки между рабочей поверхностью кристаллизатора и затвердевшей коркой заготовки.
Состав смеси зависит от марки разливаемой стали. В качестве примера можно привести следующий состав смеси, используемой для разливки большинства низкоуглеродистых марок стали, % (по массе):
Компонент C CaO SiO2 Al2O3 Na2O+K2O F
Содержание 6…10 30…36 30…36 <5 3…6 6…9
Шлакообразующая смесь может быть как в порошкообразном виде, так и в виде гранул. Гранулированные смеси обладают рядом преимуществ перед порошкообразными смесями:
– шлакообразующие смеси в виде гранул имеют гарантированно постоянный и равномерный состав, так как не подвержены расслоению по ингредиентам при хранении и транспортировке;
– при использовании гранулированных смесей существенно улучшается экологическая обстановка на рабочих местах разливщиков вследствие меньшего пылевыделения;
– такие смеси характеризуются лучшей «растекаемостью» по зеркалу жидкого металла в кристаллизаторе, образуя равномерный слой покрытия необходимой толщины. Это способствует созданию одинаковых условий для процесса шлакообразования в любой точке зеркала и получению слоя жидкого шлака толщиной не менее 7…8