Добавлен: 22.11.2023
Просмотров: 52
Скачиваний: 3
ВНИМАНИЕ! Если данный файл нарушает Ваши авторские права, то обязательно сообщите нам.
Содержание
Введение
. Выбор литейного сплава
. Литниково-питающая система
.1 Выбор типа литниково-питающей системы
. Пресс-формы
. Изготовление моделей
.1 Классификация и свойства модельных составов
.2 Приготовление модельных составов
.3 Изготовление моделей
.4 Сборка моделей в блоки
. Литейные формы
. Плавка металла и заливка форм
. Выбивка, очистка и термообработка отливок
.1 Охлаждение залитых форм и выбивка отливок
.2 Предварительная очистка блоков отливок
.3 Отделение отливок от литниковой системы
.4 Удаление остатков литников
.5 Термообработка стальных отливок
. Контроль качества и исправление дефектов отливок
Список литературы
Введение
Метод литья по выплавляемым моделям, благодаря преимуществам по сравнению с другими способами изготовления отливок, получил значительное распространение в машиностроении и приборостроении.
Промышленное применение этого метода обеспечивает получение из любых литейных сплавов сложных по форме отливок массой от нескольких граммов до десятков килограммов со стенками, толщина которых в ряде случаев менее 1 мм, с шероховатостью от


Указанные возможности метода позволяют максимально приблизить отливки к готовой детали, а в ряде случаев получить литую деталь, дополнительная обработка которой перед сборкой не требуется. Вследствие этого резко снижаются трудоемкость и стоимость изготовления изделий, уменьшается расход металла и инструмента, экономятся энергетические ресурсы, сокращается потребность в рабочих высокой квалификации, в оборудовании, приспособлениях, производственных площадях. Применение литья по выплавляемым моделям открывает перед конструкторами возможности проектировать сложные тонкостенные конструкции, объединять различные детали в компактные цельнолитые узлы, уменьшая массу и габариты изделий, создавать детали (например, охлаждаемые лопатки со сложными лабиринтными полостями газового тракта), невыполнимые каким-либо другим методом обработки. Вследствие химической инертности и высокой огнеупорности оболочек форм, пригодных для нагрева до температур, превышающих температуру плавления заливаемого сплава, создается возможность эффективно использовать методы направленной кристаллизации, управлять процессом затвердевания для получения, например, герметичных прочных тонкостенных точных отливок, либо монокристаллических деталей с высокими эксплуатационными свойствами.
Прообразом современного процесса изготовления отливок по выплавляемым моделям является известный со времен глубокой древности метод восковой формовки. При изготовлении художественных отливок, ювелирных изделий, а также зубных протезов этот метод литья по выплавляемым моделям применяют и в настоящее время. Одним из образцов высокого мастерства литейщиков прошлого является отлитая по выплавляемым моделям конная статуя Петра I ("Медный всадник", Фальконе, 1782 г.).
Начало промышленного освоения метода относится к 1940-1942 гг. и связано в основном с необходимостью получения из труднообрабатываемых жаропрочных сплавов лопаток авиационных газотурбинных двигателей (ГТД). Первые промышленные партии отлитых по выплавляемым моделям лопаток из сплавов на кобальтовой и никелевой основе были получены в СССР в 1944 г. В конце 40-х годов было освоено получение по выплавляемым моделям разнообразных мелких, преимущественно стальных отливок, например, для мотоциклов, охотничьих ружей, швейных машин, а также бурового и металлорежущего инструмента.
По мере развития и совершенствования процесса усложнялась конструкция изготовляемых по выплавляемым моделям отливок. Так, в начале 60-х годов из жаропрочных сплавов на никелевой основе изготовлялись уже крупные цельнолитые роторы с бандажным кольцом. В 1951 г. в НИИТавтопроме были начаты работы по проектированию механизированных и автоматизированных линий массового производства мелких точных отливок. Первый механизированный цех литья по выплавляемым моделям был создан на Подольском механическом заводе им. М. И. Калинина для изготовления деталей швейных машин, а в 1964 г. на ГАЗе введена в строй типовая комплексно-автоматизированная линия для производства 2-2,5 тыс.т в год стальных автомобильных отливок массой от нескольких граммов до 1,5 кг.
Современный процесс изготовления отливок по выплавляемым моделям состоит в следующем. В пресс-формах изготовляют модели деталей и литниковой системы, для чего обычно используют легкоплавкие воскообразные материалы, составы на основе смол и пластмасс, сплавы солей. Модели соединяют в блок, после чего на них слоями наносят суспензию из связующего раствора и пылевидного огнеупорного материала. Слои суспензия для их упрочнения и лучшей взаимной связи обсыпают песком, а затем сушат. Из полученной многослойной неразъемной оболочковой формы удаляют выплавлением, растворением или выжиганием модельный состав либо сначала заформовывают блок моделей с образованной на его поверхности огнеупорной оболочкой в отверждаемый формовочный состав, а после этого удаляют модели. Освобожденные от модельного состава оболочки отдельно (без опок) или в заформованном виде прокаливают и заливают металлом.
В начальной стадии промышленного освоения метода литья по выплавляемым моделям использовали весьма сложный и трудоемкий процесс, основанный на применении дорогих исходных материалов - натуральных восков, жидких формовочных наполнителей с гидролизованными растворами этилсиликата в качестве связующего. Ввиду длительности процесса (до 5-6 суток) и высокой стоимости получаемых отливок метод имел ограниченное применение.
Проведенные работы по совершенствованию технологического процесса, изысканию новых модельных и формовочных материалов, созданию высокопроизводительного оборудования, интенсификации основных и вспомогательных производственных операций позволили значительно расширить возможности метода литья по выплавляемым моделям, сделать высокоэффективным его применение в условиях массового, серийного и опытного производства.
1. Выбор литейного сплава
Отливки по выплавляемым моделям изготавливают практически из всех литейных сплавов: углеродистых и легированных сталей, коррозионно-стойких, жаростойких и жаропрочных сталей и сплавов, чугуна, цветных сплавов, например алюминиевых, медных, титановых и др.
При проектировании литых деталей учитывают условия их работы, в связи с чем некоторые свойства металла отливок приобретают первостепенное значение. Показатели их регламентируют, в то время как другие свойства считают менее важными. Например, литой корпус тормозного цилиндра должен быть герметичным, поэтому необходимо выбрать для него сталь, не склонную к образованию рассредоточенных усадочных рыхлот и пористости. Рабочие литые лопатки газотурбинных двигателей в первую очередь должны обладать высокой жаропрочностью, удовлетворительной окалино-стойкостью при рабочих температурах и напряжениях, иметь возможно меньший коэффициент линейного расширения.
При выборе литейного сплава необходимо четко сформулировать требования к материалу отливок, сгруппировать эти требования с учетом назначения и условий службы деталей. Далее уточняют марку сплава, свойства которого наиболее близки к требуемым, причем учитывают технологичность этого сплава в специфических условиях изготовления отливок по выплавляемым моделям.
2. Литниково-питающая система
Литниково-питающая система (ЛПС) служит для обеспечения заполнения литейной формы металлом с оптимальной скоростью, исключающей образование в отливке недоливов и неметаллических включений, и компенсации объемной усадки в период затвердевания отливки с получением в ней металла заданной плотности. ЛПС должна также удовлетворять требованиям технологичности при изготовлении моделей, форм и отливок. При этом необходимо стремиться к созданию по возможности компактных ЛПС.
Конкретная литая деталь представляет собой оригинальную конструкцию, что приводит к необходимости создания самостоятельной ЛПС для каждой отливки. Вместе с тем литые детали имеют много общего в размерах стенок, узлов, их сочленений, благодаря чему открываются возможности для типизации конструкций ЛПС и выработки общих методов их расчета.
2.1 Выбор типа литниково-питающей системы
модельный заливка форма отливка
При выборе конструкции ЛПС необходимо стремиться к соблюдению следующих принципиальных положений, направленных на получение годных отливок и на экономичность их производства:
) наиболее протяженные стенки и тонкие кромки ориентировать в форме вертикально, т.е. наиболее благоприятно для их спокойного и надежного заполнения;
) обеспечивать принцип направленного затвердевания, т.е. последовательного затвердевания от наиболее тонких частей отливки через ее массивные узлы к прибыли, которая должна затвердевать последней;
) создавать условия для экономичного и механизированного производства отливок, в том числе: унификацию типоразмеров ЛПС и их элементов с учетом эффективного использования оснастки, имеющегося технологического оборудования, печей; удобство выполнения и минимальный объем механической обработки при отрезке отливок и последующем изготовлении из них деталей.
В конкретном производстве конструкцию ЛПС необходимо выбирать на возможно более ранней стадии разработки технологии, лучше всего - при эскизном и рабочем проектировании изделия, когда требования к надежной работе ЛПС могут быть учтены в чертеже детали наиболее полно.
ЛПС при литье по выплавляемым моделям строят из известных традиционных элементов: литниковых воронок, стояков, зумпфов и литниковых ходов, прибылей и коллекторов. Благодаря характерной для литья по выплавляемым моделям неразъемной форме указанные конструктивные элементы удается расположить наиболее эффективно, максимально используя объем формы. ЛПС, применяемые в современном производстве отливок литьем по выплавляемым моделям, целесообразно разделить на восемь типов (табл.1).
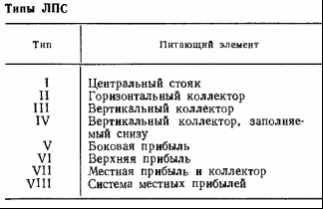
таблица 1
Тип I. Центральный стояк. ЛПС этого типа представляет собой стояк компактного сечения, непосредственно к которому с разных сторон присоединяются небольшие отливки с одним-двумя индивидуальными питателями (рис.1).
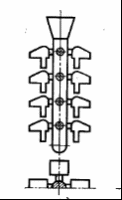
Рис.1. Литниково-питающая система типа I (центральный стояк)
Центральный стояк является одновременно и литниковым ходом, и коллективной прибылью, а питатели соответственно выполняют и роль шеек прибылей. Центральное расположение стояка обусловливает естественное замедление его охлаждения и способствует направленному затвердеванию периферийно расположенных отливок. Зумпф в нижней части стояка смягчает отрицательное действие механического и теплового ударов, имеющих место в начальный момент заливки. ЛПС типа I находят широкое применение в производстве отливок массой до 1 кг.
Тип II. Горизонтальный коллектор. ЛПС этого типа представляет собой центральный стояк, на котором в один-два яруса и более расположены горизонтальные коллекторы, обычно в виде радиальных лучей, дисков и колец (рис.2).
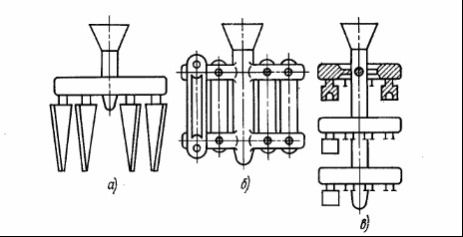
Рис.2. Литниково-питающая система типа II (горизонтальный коллектор):
а) лучевой одноярусный; б) лучевой двухъярусный; в) кольцевой трехъярусный
Существуют ЛПС типа II с горизонтальными коллекторами нескольких разновидностей: дисковыми, кольцевыми, радиальными прямоугольного сечения из двух, трех, четырех и пяти лучей, в виде двух параллельных брусьев прямоугольного сечения.
Тип III. Вертикальный коллектор. Обычно этот коллектор имеет вид системы заливаемых сверху параллельных стояков, единого вертикально-замкнутого коллектора или полого стояка (рис.3). Параллельные стояки применяют при литье деталей типа плиты или коробки, отличающихся распределенными в плоскости узлами. Вертикально-замкнутый коллектор позволяет эффективно питать отливку типа кольца.
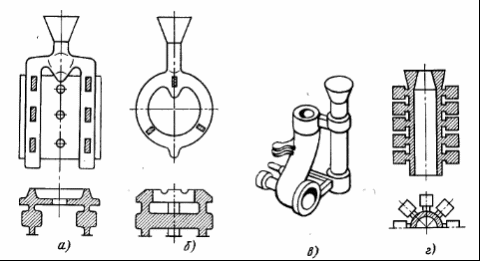
Рис.3. Литниково-питающая система типа III (вертикальный коллектор): а) параллельные стояки; б) вертикально-замкнутый кольцевой коллектор; в) стояк с цилиндрическим коллектором для сложного патрубка; г) полый стояк.
Представляет интерес вертикальный коллектор типа полого стояка. Полый стояк, имея развитую поверхность, позволяет разместить в форме в 2-4 раза больше небольших отливок, чем сплошной. Благодаря ограниченному теплоотводу в сторону полости формы, он отличается высокой питающей способностью в период затвердевания отливок.