Добавлен: 22.11.2023
Просмотров: 54
Скачиваний: 3
ВНИМАНИЕ! Если данный файл нарушает Ваши авторские права, то обязательно сообщите нам.
Тип IV. Вертикальный коллектор, заполняемый снизу. Обычно такой коллектор имеет вид обратного стояка круглого сечения. Применяют его при литье постоянных магнитов, в том числе в сборные формы и при литье под низким давлением.
Тип V. Боковая прибыль. Эта прибыль имеет вид вертикального тела, напоминающего стояк, но отличающегося от него существенно большим поперечным сечением; допускается применение коллекторов в виде местных утолщений. Боковую прибыль используют преимущественно при изготовлении крупных и протяженных отливок, при вертикальной ориентации которых обеспечивается спокойное заполнение формы снизу вверх и сосредоточение в верхней части отливки наиболее горячих порций расплава. На рис. 4 приведена характерная боковая прибыль, используемая при получении крупных и сложных тонкостенных отливок из сложнолегированных сталей.
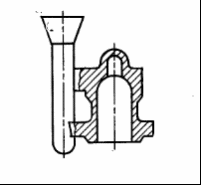
Рис.4. Литниково-питающая система типа V (боковая прибыль)
Тип VI. Верхняя прибыль. Эта прибыль представляет собой массивный резервуар металла над главным тепловым узлом отливки, получаемой в одноместной форме. При наличии в отливке вторичных узлов их питают от этой же прибыли через дополнительные отводы и шейки. Металл в прибыль заливают из ковша или непосредственно из тигля печи. Сосредоточение наиболее горячего расплава в верхней части прибыли приводит к созданию в форме наиболее благоприятного для питания отливки градиента температур. Отличаясь вследствие этого высокой питающей способностью, верхняя прибыль надежно обеспечивает получение плотного металла крупных высоконагруженных литых деталей. Примеры сложных отливок с верхней прибылью представлены на рис.5.
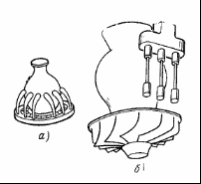
Рис.5. Литниково-питающая система типа VI (верхняя прибыль)
Примеры применения: а) ротор с бандажом; б) рабочее колесо газотурбинного наддува дизеля.
Тип VII. Местная прибыль и коллектор. От стояка с нижним горизонтальным коллектором осуществляется питание нижних узлов у вертикально ориентированных отливок и местных соединенных со стояком прибылей над верхним узлом каждой отливки (рис.6). Эта комбинированная ЛПС обладает следующими преимуществами: происходит спокойное заполнение формы снизу, что особенно важно при литье из пленообразующих сплавов, и обеспечивается подвод горячего расплава в прибыль к концу заливки. При центральном расположении стояка создаются условия для размещения в форме нескольких надежно питаемых отливок, в том числе массой более 1 кг каждая, и облегчается применение моделей с металлическим каркасом. В отдельных случаях хорошие результаты дает ЛПС типа VII в сочетании с подводом металла в тонкую кромку через вертикально-щелевой питатель. При таком подводе расплава по сравнению с заливкой сифоном и сверху был обеспечен наивысший уровень плотности, прочности и пластичности металла в лопатках из жаропрочного сплава. Необходимо, однако, иметь в виду, что в случае применения сравнительно широких вертикально-щелевых питателей, подводимых к протяженной стенке, возможно поражение отливки поверхностными раковинами.
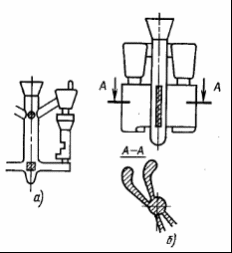
Рис.6. Литниково-питающая система типа VII (местная прибыль и коллектор):
а) четырехместная при центральном расположении стояка; б) заливка лопаток через вертикальный щелевой питатель
Тип VIII. Система местных прибылей. Каждая прибыль в ЛПС этого типа питает отдельный узел или участок протяженного узла сравнительно крупной отливки, преимущественно корпусного типа. Заливают ее обычно через стояк с литниковыми ходами. Система местных прибылей при развитой в пространстве отливке позволяет наиболее эффективно использовать ЛПС путем приближения прибылей непосредственно к питаемым ими участкам, а также достаточно полно учесть взаимное обогревающее влияние элементов отливки и ЛПС. Примеры представлены на рис.7.
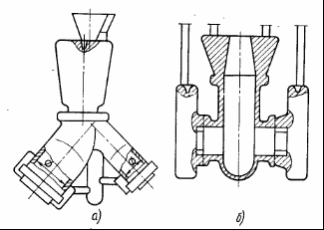
Рис.7. Литниково-питающая система типа VIII (система местных прибылей).
Примеры применения: а) тройники; б) корпус вентиля
3. Пресс-формы
Формы для изготовления выплавляемых моделей называют пресс-формами. К пресс-формам предъявляются следующие основные требования.
. Размеры и чистота поверхности полости пресс-формы должны обеспечивать получение отливок с заданной точностью и чистотой поверхности. При этом точность размеров и чистота поверхности рабочей полости пресс-формы должны быть на 1-2 класса выше требуемой точности и чистоты поверхности отливки.
. Пресс-формы должны иметь минимальное количество разъемов, причем должно быть обеспечено удобное, быстрое и надежное извлечение моделей. Извлечение модели из пресс-формы без повреждений и искажений достигается правильным выбором разъема, выполнением уклонов и применением выталкивающих устройств. Величину уклонов принимают не менее 0,5°. Выталкиватели делаются местными или сплошными. Местные выталкиватели могут оставлять следы на моделях, поэтому их надо ставить на обрабатываемых или на неответственных поверхностях, сплошные выталкиватели не оставляют следов на поверхности модели.
. Для удаления воздуха из полости пресс-формы при заполнении ее модельным составом на разъемах делают тонкие риски (0,1 мм), а в глухих углублениях, где образуются воздушные мешки, следует предусматривать тонкие вентиляционные отверстия.
. Размеры каналов для подвода модельного состава должны обеспечивать получение модели без пузырей, усадочных и других дефектов. Место подвода не должно портить поверхность модели и должно компенсировать объемную усадку. Если питатели отливки нельзя использовать как литники модели, следует подводить модельную массу в наиболее толстое сечение модели и к обрабатываемой поверхности данной отливки.
. Пресс-форма должна быть удобной в работе. Для удобства сборки и разборки на пресс-форме предусматриваются ручки, углубления для пальцев рук, а также зажимные приспособления для быстрого и надежного запирания пресс-формы.
. Детали и узлы пресс-формы должны быть прочными, жесткими и износоустойчивыми.
. Конструкция пресс-формы должна быть технологичной в изготовлении. Сложные детали пресс-формы, изготовляемые механической обработкой, целесообразно расчленять на более простые элементы.
Выбор типа пресс-формы обусловлен в основном характером производства (опытное, серийное, массовое), а также требованиями, предъявляемыми к отливкам по точности размеров и чистоте поверхности. При крупносерийном, а особенно при массовом производстве следует применять стальные пресс-формы, изготовленные механической обработкой.
Анализируя целесообразность изготовления сложной и дорогостоящей многогнездной пресс-формы, необходимо исходить из себестоимости отливок, которые можно получить за период нормальной эксплуатации пресс-форм. В массовом производстве высокая стоимость такой пресс-формы окупается быстрее, чем стоимость нескольких более дешевых одногнездных пресс-форм.
При серийном производстве отливок рекомендуется изготовлять пресс-формы по эталону, из металлических легкоплавких сплавов или пластмассы. В таких пресс-формах можно изготовить до нескольких тысяч моделей с удовлетворительной точностью.
При изготовлении очень сложных по конфигурации моделей используют эластичные пресс-формы, выполненные из формопласта, виксинта или резины.
4. Изготовление моделей
.1 Классификация и свойства модельных составов
Процесс изготовления моделей включает операции приготовления модельных составов, получения моделей отливок и ЛПС, отделки и контроля моделей, сборки их в блоки и контроля последних.
При выборе составов для изготовления моделей руководствуются следующими требованиями:
) состав должен точно воспроизводить конфигурацию рабочей полости пресс-формы, не прилипать к пресс-форме;
) после затвердевания в пресс-форме состав должен иметь твердость и прочность достаточные для того, чтобы модели не деформировались и не повреждались на всех технологических операциях;
) усадка состава при охлаждении и расширение при нагреве должны быть минимальными и стабильными;
) состав должен быть несложным в приготовлении, иметь минимальное число компонентов, желательно недорогих и недефицитных;
) температура плавления модельного состава должна быть в пределах 60-100°, а температура начала размягчения - выше температуры рабочего помещения;
) состав должен обладать хорошей жидкотекучестью в расплавленном состоянии для облегчения изготовления моделей и выплавления их из форм;
) продолжительность затвердевания модельного состава в пресс-форме должна быть минимальной;
) плотность состава должна быть невысокой (желательно менее 1000 кг/м3);
) химическое взаимодействие состава с материалом пресс-форм недопустимо;
) желательно хорошее спаивание модельного состава, т.к. это облегчает сборку блоков;
) структура состава должна быть механически однородной;
) модельный состав в любом состоянии должен быть безвредным для здоровья работающих.
Применяемые модельные составы могут быть классифицированы: а) в зависимости от основных компонентов и их соотношения; б) в зависимости от температур плавления и размягчения, прочности и т д.; в) по состоянию при введении в пресс-форму (жидкие составы, пастообразные, подогретые до размягчения); г) по способу удаления из литейных форм (выплавлением, растворением, выжиганием).
В машиностроении наибольшее распространение получили модельные составы четырех групп.
К первой группе относятся модельные составы, представляющие собой сплав высокоподобных материалов, содержащий в ряде случаев улучшающие добавки. Основными компонентами составов этой группы являются парафин, стеарин, церезин, буроугольный и торфяной воск, сложные эфиры высших кислот. В качестве добавок, повышающих пластичность, прочность, теплостойкость, используют этилцеллюлозу, кубовый остаток крекинга парафина, полиэтилен и др.
В маркировке модельных составов буквы обозначают наименования компонентов: П - парафин; С - стеарин; Ц - церезин; Б - буроугольный воск; Ко - кубовый остаток крекинга; Т - торфяной воск; Тр - триэтаноламин; Пс - полистирол; Пэв - полиэтиленовый воск; Кб - карбамид; Бк - борная кислота; Нк - нитрат калия; К - канифоль; Св - сибирский воск. Цифры в маркировке указывают массовую долю (%) компонентов в составе.
Во вторую группу входят модельные составы на основе натуральных и синтетических смол, термопластов (например, полиэтилена, полистирола) с добавками воскообразных материалов (церезина, парафина и др.) От составов первой группы они отличаются более высокой прочностью и теплоустойчивостью. Однако высокая температура плавления ограничивает выбор технологического оборудования.
Третья группа включает водорастворимые модельные составы на основе карбамида, азотных и азотокислотных солей щелочных металлов, поливинилового спирта и других материалов, плавящихся при температуре не выше 350°C. Эти составы обладают малой усадкой (около 0,20%), высокой прочностью, хорошо растворяются в воде. Их недостаток - хрупкость. Наиболее распространены составы КБ 98-2 и КН 90-10.
К четвертой группе относятся выжигаемые модельные составы. Наибольшее распространение получил вспенивающийся полистирол ПСВ - ЛД. Плотность изготовленных из него моделей составляет 0,24-0,30 г/см3, прочность при изгибе - 10-14 МПа, усадка - 0,2-0,3%.
4.2 Приготовление модельных составов
Предварительное приготовление большинства модельных составов состоит в поочередном или одновременном расплавлении составляющих, фильтровании расплавов и разливке в формы.
Легкоплавкие модельные составы (парафин, стеарин, церезин и др.) приготовляют в водяных, глицериновых или масляных банях с электрическим или газовым подогревом. Применяют также бани-термостаты.
Пастообразные модельные составы при малом масштабе производства приготовляют вручную, при более крупном - на специальных установках. Эти установки могут быть с лопастными, поршневыми и шестеренными смесителями.
Модельные составы с высокой температурой плавления (канифоль, полистирол и др.) изготовляют в специальных поворотных электропечах, оснащенных терморегуляторами.
4.3 Изготовление моделей
Процесс изготовления моделей в пресс-формах включает подготовку пресс-формы, введение в ее полость модельного состава, выдержку модели до затвердевания, разборку пресс-формы и извлечение моделей, а также охлаждение моделей до температуры производственного помещения.
Модельный состав вводят в полость пресс-формы следующими способами: свободной заливкой расплава; запрессовкой в пастообразном состоянии; заливкой под давлением расплава; запрессовкой под высоким давлением подогретых до состояния размягчения порошка или крупки модельных составов типа пластмасс.
4.4 Сборка моделей в блоки
Сборка готовых моделей в блоки осуществляется различными способами:
а) модели деталей припаиваются к модели литниковой системы с помощью подогретого ножа, электропаяльником или расплавленным модельным составом;
б) модели соединяются в кондукторе с элементами литниковой системы механически или склеиванием (позволяет устранить припаивание вручную, обеспечить прочное соединение, точно выдержать заданное положение моделей на литниковой системе);
в) механическое соединение моделей деталей и литниковой системы применяется в тех случаях, когда модели делаются из материала, не поддающегося спаиванию (например, полистирол).
После сборки моделей методом спаивания, особенно при одновременной отливке элементов литниковой системы, необходима выдержка для полного охлаждения всех частей модельного блока до температуры производственного помещения.
. Литейные формы
Литейная форма - инструмент для обработки расплава металла в целях получения отливок с заданными размерами, шероховатостью поверхности, структурой и свойствами. Основа способа литья по выплавляемым моделям - оболочка. Известны два типа оболочек в зависимости от способа их изготовления: многослойные, получаемые нанесением суспензии с последующей обсыпкой и сушкой, и двухслойные, получаемые электрофоретическим способом.
Процесс изготовления литейной формы состоит в подготовке материалов, формирования оболочки на поверхности модели, удаления модели из оболочки, заформовывания оболочки в наполнитель и прокаливания формы.
Для образования литейной формы употребляются:
) связующие материалы - этилсиликат, жидкое стекло, глиноземистый цемент;
) материалы основы - пылевидный кварц, кварцевый песок, плавленый кварц, молотый шамот, пылевидный тальк, магнезит, циркон;
) растворители и прочие материалы-этиловый спирт, ацетон, эфир-альдегидная фракция, гидрозит, соляная кислота, дистиллированная вода.
Приготовление суспензии состоит в перемешивании связующего раствора с пылевидным материалом (предварительно промытым, просушенным, прокаленным и просеянным) до получения однородной массы.
Формирование оболочек на поверхностях моделей состоит в нанесении суспензии, обсыпке сухим песком и твердении слоя оболочки. Нанесение суспензии на поверхности моделей осуществляется методом погружения модели в суспензию. Другие методы нанесения (напылением, обливанием) не получили распространения.
Обсыпка песком в начале делалась вручную в непрерывно падающем потоке песка. В настоящее время она повсемесно механизирована. Способ удаления модельного материала зависит от его свойств и от того удаляется ли он непосредственно из оболочки, до формовки или после формовки.
Выплавление модельного материала может быть осуществлено в шкафах горячим воздухом, перегретым водяным паром; в ваннах горячей водой, инфракрасными лучами; токами высокой частоты. Наибольшее распространение получили способы выплавления моделей в жидкой и газообразной среде. Выжигание и растворение моделей широкого распространения не получили.
Формовка при литье по выплавляемым моделям - это упаковка оболочек в опорный наполнитель до прокаливания их или перед заливкой. Формовка оболочек производится в опоках с дном для сухих наполнителей или без дна для влажных наполнителей. Опоки обычно делают сварными из листового материала толщиной 4-5 мм, преимущественно цилиндрической формы, а также литьем в землю. В качестве наполнителей применяют формовочный песок.
По окончании формовки и удаления модели формы подвергают прокаливанию, благодаря чему достигается удаление из оболочки газотворных составляющих, а также лучшее заполнение нагретой формы жидким металлом. Прокаливание производится при температуре 850-900° в печах разных конструкций (электрических, газовых и др.).
6. Плавка металла и заливка форм
Плавка металла и заливка форм является важнейшей частью технологического процесса производства отливок, определяющей конечное качество литых деталей.
Для плавки металла могут быть использованы любые плавильные печи, которые обеспечивают требуемое качество сплава. При литье стали и чугуна по выплавляемым моделям широко применяют индукционные тигельные печи, позволяющие в широком диапазоне регулировать температуру заливаемого металла. Для плавки алюминиевых сплавов чаще всего используют тигельные печи, печи сопротивления и индукционные печи промышленной частоты. Стальные и чугунные отливки, как правило, изготавливают в формах, нагретых до 600°С. Температура форм для алюминиевого литья составляет 200-300°С.
Собранную и скрепленную форму подают на заливку. Для заливки форм используют ковши различных конструкций. Чайниковые, носковые и барабанные ковши применяют для заливки чугуна и цветных сплавов, стопорные - для заливки стали. Кожух ковша делается из листовой стали и футеруется изнутри огнеупорным материалом или обмазывается глиной (мелкие ковши). Перед заливкой ковши сушат и нагревают, чтобы уменьшить потери тепла металла.
В цехах с периодическим режимом работы формы заливают на специальной заливочной площадке. Жидкий металл из печи заливают в ковш, при помощи мостового крана (или тельфера) транспортируют к заливочной площадке и разливают по формам. После охлаждения формы мостовым краном подаются на выбивку, а пустые опоки - к месту формовки.
Заливка жидкого металла в формы имеет свои особенности. Заливка осуществляется одним из следующих способов:
свободная заливка;
вакуумная заливка;
центробежная заливка;
комбинированная центробежно-вакуумная заливка.
7. Выбивка, очистка и термообработка отливок
.1 Охлаждение залитых форм и выбивка отливок
После заливки формы охлаждают естественным путем - на воздухе - или принудительно - обдувкой холодным воздухом, душированием водой. Естественное охлаждение происходит весьма медленно. Например, средняя скорость охлаждения стальных отливок, залитых в форму с опорным наполнителем при 900 °С, составляет
6 °С/мин. Та же форма, но без наполнителя, охлаждается со скоростью 30 °С/мин.
В механизированных цехах формы с наполнителем охлаждают на конвейере, имеющем кожух с отсасывающей вентиляцией (скорость охлаждения до 12 °С/мин). Практика работы цехов литья по выплавляемым моделям и исследования показывают, что при медленном охлаждении металла (например, при заливке в формы, нагретые до 900 °С) качество металла выше, чем при заливке в подстуженные или холодные формы.
Выбивка является трудоемкой и тяжелой операцией при производстве отливок, так как в процессе выбивки выделяется большое количество теплоты, пыли, газов. Поэтому участки выбивки должны иметь хорошую вытяжную вентиляцию и местные бортовые отсосы запыленного воздуха. Для выбивки чаще всего используют выбивные решетки: механические (эксцентриковые и инерционные), пневматические и др.
Стержни из мелких отливок удаляют пневматическими зубилами, из сложных отливок среднего развеса - на пневматических вибрационных установках. Отливка зажимается в приспособлении между пружинным упором и бойком вибратора, который перемещается по направляющим при помощи пневматического толкателя. Стержень разрушается при вибрации отливки и высыпается из нее.
Выбивку стержней из крупных отливок осуществляют в гидравлических камерах. Отливку устанавливают в камере на поворотный стол и направляют на нее струю воды под большим напором. При этом одновременно с удалением стержня происходит очистка поверхности отливок.
.2 Предварительная очистка блоков отливок
На блоках отливок после выбивки имеются остатки оболочки и наполнителя. Чем выше температура выбитых блоков, тем больше и плотнее слой наполнителя. После охлаждения наполнитель осыпается, блоки проходят предварительную очистку и далее поступают на операцию отделения от ЛПС и окончательную очистку. Блоки предварительно очищают ударами по литниковой воронке. В механизированном производстве для этого применяют специальные вибрационные установки.
При изготовлении мелких отливок, часто применяют вибрационные установки, выполняющие две операции - предварительную очистку и отделение отливок. Предварительной очисткой оболочку удаляют только с наружных частей отливок, но она остается в отверстиях и поднутрениях.
.3 Отделение отливок от литниковой системы
Для отделения отливок от литниковой системы применяют следующие способы: отбивку на вибрационных установках, отрезку на металлорежущих станках, отделение на прессах, газопламенную и анодно-механическую резку.
Отбивка на вибрационных установках заключается в том, что при ударной вибрации блока отливка приобретает колебательное движение, вследствие чего разрушается металл питателя и отливка отваливается от стояка. Для этого в определенном месте на питателе выполняют пережим, являющийся концентратором напряжений.
Производительность вибрационных установок, в основном зависит от трех факторов: от способа закрепления обрабатываемого блока, от материала, из которого изготовлены отливки, и от мощности установленного вибратора. Отливки отделяются за 3-7 мин. Вибрационный способ позволяет отделять отливки, соединенные со стояком как одним, так и несколькими питателями, расположенными в любой плоскости.
При сложной конфигурации отливок с выступающими частями возможно появление микронадрывов и трещин, а иногда происходит и разрушение отливки. Поэтому рассмотренный способ можно применять для отбивки оболочки вибрацией до 30 с и его нельзя рекомендовать для отделения от стояка отливок любой конфигурации.
В некоторых случаях, например когда ЛПС кроме стояка и коллекторов имеет также прибыли, последние и отливки отрезают механическими ножовками, дисковыми пилами или на токарных фрезерных, шлифовальных станках. Токарный станок с узким отрезным резцом или фрезерный станок с дисковой фрезой удобнее всего использовать для отрезки отливок, изготовленных с дисковой или коллекторной литниковой системой. Отрезка отливок на металлорежущих станках может быть оправдана только в том случае, если другие способы отделения невозможны или в случае применения разнообразных литниковых систем, требующих универсального оборудования. Низкая стойкость режущего инструмента при отрезке отливок объясняется тяжелыми условиями его работы (на удар), а иногда и тем, что в местах реза имеются остатки оболочки. При использовании абразивных кругов на операции отрезки отливок производительность значительно увеличивается и не зависит от твердости литейного сплава.