Файл: Курсовой проект по дисциплине Технология бетона и железобетона Ташкент 2017 Оглавление.docx
ВУЗ: Не указан
Категория: Не указан
Дисциплина: Не указана
Добавлен: 29.11.2023
Просмотров: 66
Скачиваний: 3
ВНИМАНИЕ! Если данный файл нарушает Ваши авторские права, то обязательно сообщите нам.
-
Стендовый способ рекомендуется в тех случаях, когда габариты и масса конструкций превышают размеры и грузоподъемность виброплощадок и мостовых кранов. -
Армирование изделий не позволяет уплотнять изделия на виброплощадке и требует применения глубинных и навесных вибраторов.
На длинных стендах можно формовать длинномерные линейные конструкции с напряженным армированием, длина стенда достигает 75-222 м. Короткие стенды рассчитаны на одно изделие, а по ширине - на два и более.
Достоинства:
Возможность выпуска изделий широкой номенклатуры при относительно несложном переоборудовании.
Простота и универсальность оборудования.
Гибкость технологии на коротких стендах, преимущественно
в вибротермоформах, в 2-4 раза повышает оборачиваемость форм,
снижает трудоемкость формования.
Недостатки:
Стендовый способ производства требует больших производственных площадей, усложнения механизации и автоматизации, высоких трудозатрат.
1.3. Режим работы цеха
Для предприятий сборных железобетонных изделий следует принимать:
-количество расчетных рабочих суток за год-262;
-по выгрузке сырья и материалов с железнодорожного транспорта –365;
-количество рабочих смен в сутки (без тепловой обработки)-2;
-количество рабочих смен в сутки для тепловой обработки-3;
-количество рабочих смен в сутки по приему сырья и материалов и отгрузке готовой продукции:
а) железнодорожным транспортом –3;
б) автотранспортом -2 или 3, в зависимости от местных условий.
Количество рабочих суток в году (262) исходит из 5-дневной рабочей недели.
При 5-дневной рабочей неделе режим работы принимается:
а) при двух сменах: 8 час., всего 16 час. в сутки; кроме этого два перерыва на обед по 1 час;
б) при трех сменах: первая и вторая смены по 8 час (кроме этого по 0,5 час. перерыва); третья смена 7 час. без перерыва. Итого в сутки 23 рабочих часа.
Годовой фонд времени работы основного технологического оборудования принимается равным – 247 дням.
Годовой коэффициент использования основного технологического оборудования – 247: 262 = 0,943.
Таблица 1.2.
Режим работы предприятия
№ | Наименование цехов или отделений | К-во дней в году | К-во смен в сутки | Длительность рабочей смены, час | Годовой фонд рабочего времени, час | Коэф. использован. эксплуатац. времени | Годов. фонд эксплуа. времени, час |
1 | Формовочный цех | 262 | 2 | 8 | 4192 | 0,943 | 3953 |
2 | Тепловая обработка | 262 | 3 | 8 | 6288 | 0,943 | 5930 |
1.4. Расчет производительности цеха по видам изделий
Годовая программа цеха (предприятий) и номенклатура изделий задается в задание. Исходя из принятого режима работы цеха, производится расчет производственной программы изделий и полуфабрикатов с учетом возможного производственного брака и потерь на отдельных переделах.
Рекомендуются величины возможных производственных потерь и брак.
Для заводов железобетонных изделий:
-по бетонной смеси –до 0,5%;
-по изделиям -до 1,0%.
Расчет производительности для каждого технологического передела производится по формуле:
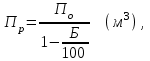
где, Пр – производительность рассчитываемого передела;
По – заданная производительность цеха (предприятия);
Б – производственные потери от брака – 1,5%.

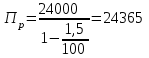
Производительность в штуках:
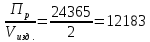
Таблица 1.3.
Производственная программа цеха (предприятия)
№ | Наименование изделий | Ед. изм. | Цифровая формула для годовой производ. | Производительность | |||
в год | в сутки | в смену | в час | ||||
1 | Двухскатная балка | м3 | ![]() | 5,8 | 46 | 93 | 24365 |
шт. | Пр /Vизд | 3 | 23,2 | 46,4 | 12183 |
1.5. Определение потребности цеха (предприятия) в сырье и полуфабрикатах
Качество бетона в большей степени зависит от используемых материалов. Правильный выбор материалов для бетона, учитывающий как требования к бетону, так и свойство самих материалов, имеет важное значение по технологии бетона. При этом должно достигаться максимальная экономия цемента и трудовых затрат на производство бетона. Для изготовления фундаментных блоков используют следующие сырье и полуфабрикаты.
Для железобетонных изделий заводского изготовления принимают следующие вяжущие вещества.
Портландцемент и их разновидности соответствующие ГОСТ 10178-76.
В зависимости от минералогического состава цемента различают по характеру твердения как при нормальных условиях, так и при тепловлажностной обработке.
В результате их можно разделить на несколько видов. Для приготовления бетона строительных конструкций наиболее широко используют минеральные вяжущие вещества. Эти вещества при смешивании с водой под влиянием внутренних физико – химических процессов способны схватываться и твердеть.
Портландцемент
Портландцементы содержанием до 5 % C3А. В начальный период твердения прочность бетона на этих цементах нарастает медленно как при тепловлажностной обработки. При удлинение режимов тепловлажностной обработке (более 12-13 часов) и при последующем твердением рост прочности бетона достаточно интенсивно. Прочность бетона на этом цементе через 28 суток, после тепловлажностной обработке несколько (на 10-15 %) больше прочности бетона нормального твердения. Для фундаментных блоков принимают марку цемента М300. Прочность цемента составляет при сжатии 30-60 МПа.
При проектирование состава бетона лучше использовать активность бетона, так как это обеспечивает более точные результаты и экономии цемента.
В среднем в зависимости от состава бетона уменьшение нормальной густоты цемента на 1 % понижает водопотребность бетонной смеси на 2-5 л/м3 причем большое снижение водопотребности наблюдается у высокопрочных бетонов. В действительности начало схватывание цемента наступает через 1-2 часа, а конец через 5-8 часов. Эти сроки обеспечивают производство бетонных работ.
Плотность портландцемента при расчете состава бетона условно принимают в уплотненном состоянии – 1,3 кг/м3.
Щебень
Щебень из горных пород - неорганический зернистый сыпучий материал с зернами крупностью св. 5 мм, получаемый дроблением горных пород, гравия и валунов, попутно добываемых вскрышных и вмещающих пород или некондиционных отходов горных предприятий по переработке руд (черных, цветных и редких металлов металлургической промышленности) и неметаллических ископаемых других отраслей промышленности и последующим рассевом продуктов дробления.
Щебень должен удовлетворять всем требованиям указанных в ГОСТ 8267-95. Щебень и гравий должны изготовляться в соответствии с требованиями настоящего стандарта по технологической документации, утвержденной предприятием-изготовителем.
Щебень и гравий выпускают в виде следующих основных фракций: от 5 (3) до 10 мм; св. 10 до 15 мм; св. 10 до 20 мм; св. 15 до 20 мм; св. 20 до 40 мм; св. 40 до 80 (70) мм и смеси фракций от 5 (3) до 20 мм.
Прочность щебня и гравия характеризуют маркой, определяемой по дробимости щебня (гравия) при сжатии (раздавливании) в цилиндре.
Морозостойкость щебня и гравия характеризуют числом циклов замораживания и оттаивания, при котором потери в процентах по массе щебня и гравия не превышают установленных значений. Допускается оценивать морозостойкость щебня и гравия по числу циклов насыщения в растворе сернокислого натрия и высушивания. При несовпадении марок морозостойкость оценивают по результатам испытания замораживанием и оттаиванием. Щебень и гравий по морозостойкости подразделяют на следующие марки: F15; F25; F50; F100; F150; F200; F300; F400.
Песок
Песок – это механическая, осадочная горная порода, с размерами частиц от 0,14 до 0,5 мм (ГОСТ 8736 – 93).
Песок должен быть изготовлен в соответствии с требованиями настоящего стандарта по технологической документации, утвержденной предприятием-изготовителем.
Частный остаток – это остаток на данном сите, а полный остаток – это остаток на данном сите и всех выше лежащих сит.
Вода
Для приготовления бетонной смеси используют водопроводную питьевую, а также любую воду, имеющую водородный показатель рН не менее 4, то есть некислую, не окрашиваемую лакмусовую бумагу в красный цвет. Вода не должна содержать сульфатов более 2700 мг/л. В сомнительных случаях пригодность воды для приготовления бетонной смеси необходимо проверять путем сравнительных испытаний образцов, изготовленных на данной воде и на обычной водопроводной. Для приготовления бетонной смеси можно применят морскую и другие соленые воды, удовлетворяющие приведенным выше условиям. Исключением являются бетонирование внутренних конструкций жилых и общественных зданий и надводных железобетонных сооружений в жарком и сухом климате, так как морские соли могут выступить на поверхность бетона, а также вызвать коррозию стальной арматуры. Содержание растворимых солей допускается в воде для изготовление железобетона с ненапрягаемой арматурой не более 5000 мг/л, в том числе сульфатов не более 2700 мг/л, для бетона преднапрягаемых конструкций – соответствует не более 2000 и 600 мг/л.
Расчет состава бетона
Расчет состава бетона производится для каждого изделия отдельно.
Расчет состава тяжелого бетона можно произвести по методическому указанию для выполнения лабораторных работ по курсу «Технология бетонных и железобетонных изделий».
Полученные результаты служат исходными данными для определения потребности в сырье и полуфабрикатах проектируемого цеха, исходя из заданной программы, т.е. Пр.
Расчет ведется на 1 м3 бетона.
Проектное задание: двухскатная балка
Марка бетона – Rб = 400
Назначение бетона – для формовки
Подвижность бетонной смеси, осадка стандартного конуса ОК – 1-5 см
Исходные материалы:
-
Вяжущие материалы – цемент – Портландцемент
Активность цемента – Rц = 500 МПа
Истинная плотность – ρц = 3,1 г/см3
Насыпная плотность цемента – ρн.ц = 1,3 г/см3
-
Мелкий заполнитель – песок – Речной Чирчикский
Истинная плотность песка – ρп = 2,6 г/см3
Насыпная плотность песка – ρн.п. = 1,4 г/м3
Модуль крупности – Мкр =2
-
Крупный заполнитель – щебень
Истинная плотность щебня – ρк = 2,6 г/см3
Насыпная плотность щебня – ρн.к. = 1,4 г/см3
Пустотность щебня – Vк = 0,5
Методика расчета
1. Водоцементное отношение (В/Ц) определяют из условия получения бетона необходимой прочности при данной активности (марке) цемента

Определяем водоцементное отношение по формуле:

Коэффициент А зависящие от качества заполнителей, соответственно имеет следующие значение: для высококачественных заполнителей (мытые и фракционированные щебень и песок) – 0,65.
2. Определяем ориентировочный расход воды (кг) для приготовления 1 м3 бетонной смеси, по таблице 1.4: В=190 л/м3.
3. Расход цемента (кг) для приготовления бетонной смеси вычисляют, по уже известному водоцементному отношению и определенной водопотребности
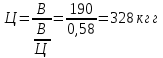
4. Расход крупного заполнителя (кг) для приготовления 1 м3 бетонной смеси определяется по формуле:
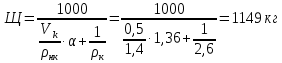
Таблица 1.4.
Водопотребность бетонной семеси