Файл: Назначение и общая характеристика электрооборудования радиальносверлильного станка стр.doc
Добавлен: 30.11.2023
Просмотров: 87
Скачиваний: 3
ВНИМАНИЕ! Если данный файл нарушает Ваши авторские права, то обязательно сообщите нам.
Смазка всех механизмов коробки скоростей, подач и включения подач осуществляется от специального насоса, расположенного на крышке сверлильной головки.
Включение и выключение вращения шпинделя осуществляется командоаппаратом, расположенным слева, внизу сверлильной головки.
Полная остановка вращения шпинделя осуществляется тормозом под действием пружины.
Механизм включения подачи.
Механизм состоит из полого вала 4, на котором на подшипниках сидит ступица 2, несущая червячное колесо I, входящее в зацепление с червяком последнего вала коробки подач.
На валу на шлицах сидит обойма 19, в которой перемещаются две собачки 17, отжимающиеся от зубчатого венца ступицы 2 пружинами. При движении рукояток II «от себя» толкатель 16 через ролики 18 прижимает собачки к зубчатому венцу ступицы 2.
Благодаря этому от червячного колеса начинает вращаться полый вал 4, шестерня которого сообщает гильзе шпинделя подачу. Движением рукояток II «на себя» механическая подача отключается, и вращением этих рукояток можно производить вручную быстрое перемещение шпинделя. Механизм подачи снабжен устройством для автоматического выключения механической подачи на заданной глубине. Устройство состоит из лимба 6 с фланцем 5, несущим упор 14. Фланец фиксируется прихватом 15.
При наезде упора 13, расположенного на рукоятке II, на упор 14 на лимбе происходит выключение механической подачи.
Механизм подачи снабжен устройством, позволяющим работать по жесткому упору. Для этой цели в ступице 7 рукояток II имеется выдвижной упор 9, а на фланце 5 постоянный упор 10. При включении выдвижного упора, наезде его на фиксированный лимб происходит останов шпинделя на заданной глубине.
Механизм подачи снабжен блокирующим устройством. Во избежание включения (при нарезании резьбы) механической подачи шпинделя, последняя блокируется фиксацией толкателя 16 упором 12 с рукояткой 8.
В механизме подачи помещается пружина 3, уравновешивающая вес гильзы и шпинделя.
Механизм перемещения и зажима сверлильной головки.
Сверлильная головка расположена на направляющих рукава и перемещается на подшипниках 3 и 9. Оси подшипников 4 и 10 выполнены эксцентричными, что позволяет регулировать величину зазора в направляющих сверлильной головки.
Перемещение сверлильной головки осуществляется маховиком 8, расположенным с правой стороны головки, через пару конических шестерен 6, 7 и реечную шестерню 5.
Зажим сверлильной головки осуществляется рукояткой II, расположенной на передней стороне головки. Усилие через эксцентриковый вал I передается упору 2, который прижимает сверлильную головку к ласточкину хвосту и фиксирует ее на рукаве.
Поворотный стол.
Поворотный стол представляет собой жесткую чугунную отливку.
Стол монтируется на бочке и имеет три Т-образных паза на горизонтальной плоскости и один в вертикальной, что позволяет базировать и закреплять детали и приспособления. Сектор червячного колеса I позволяет осуществлять поворот стола вокруг горизонтальной оси на +90 и -80° вручную. Для ограничения поворота стола предусмотрен ограничительный палец.
На фланце стола нанесены деления в градусах, позволяющие вести отсчет угла поворота.
В горизонтальном положении стол фиксируется коническим штифтом 2. Подставка 3 с резиновой подушкой служит для расположения измерительных инструментов.
Система охлаждения.
В фундаментной плите расположен резервуар для охлаждающей жидкости, которую заливают через отверстия, закрытые крышками.
Жидкость подается к сверлильной головке электронасосом 3 через ниппель 5 по шлангу 4, через поворотное соединение 6, кран 7 и трубку 8.
Положение трубки по высоте можно регулировать, перемещая штангу 2, закрепляемую в нужном положении винтом I.
Охлаждающая жидкость возвращается в резервуар по каналам плиты через отверстия, защищенные сетками.
Командоаппарат.
Командоаппарат расположен в нижней левой части сверлильной головки.
Он предназначен для включения и реверсирования вращения шпинделя. Командоаппарат состоит из корпуса, трех микропереключателей и рукоятки.
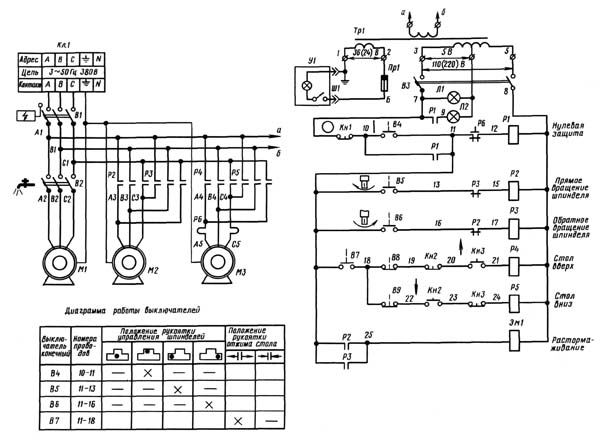
Рисунок 4. Электрическая схема радиально-сверлильного станка 2Л53У до модернизации
2. РАСЧЕТАЯ ЧАСТЬ
Металлообрабатывающие станки по количеству типов и потребляемой ими энергии занимают одно из основных мест среди электрифицированных машин и агрегатов. Электрооборудование и автоматика станков оснащаются современными типами электроприводов и средствами автоматического управления, что обеспечивает высокую производительность и точность обработки, безопасность и удобство управления и их обслуживания.
2.1. Расчет мощности электродвигателей станка и их выбор
Мощность, необходимая для работы станка, определяется режимом работы станка с учетом обеспечения его высокой производительности экономичности и безопасности обслуживания. Как известно, режим резания и другие режимы обработки деталей на станках характеризуются определенными расчетными параметрами, к которым относят: глубину резания (t), подачу или перемещение сверла на один оборот шпинделя (S), скорость резания или скорость перемещения стружки относительно сверла (V).
По указанным параметрам, а также по коэффициентам, характеризующий обрабатываемый материал и материал сверла, можно найти усилие резания или усилие другой обработки, а по ней и скорость сверления определить необходимую мощность станка. Эта мощность определяется самым тяжелым режимом обработки, задаваемым технологической картой станка или картами технологических нормативов станка.
2.1.1. Расчет и выбор электродвигателя шпинделя
Скорость резания при сверлении VZС (м/мин), рассчитывается по формуле:
VZС = (CV • dCZv)/ (TMv • SYv), (2.1)
где S – подача инструмента, мм/об, (ПРИЛОЖЕНИЕ 1, Таблица 1);
dC– диаметр рабочего инструмента (сверла), мм, (из задания);
CV- cкоростной коэффициент обработки материала, (ПРИЛОЖЕНИЕ 1,
Таблица 2);
Zv, Mv, Yv - показатели степени, (ПРИЛОЖЕНИЕ 1, Таблица 2);
T - стойкость инструмента, мин,( ПРИЛОЖЕНИЕ 1, Таблица 3).
VZС = (9,8 • 30 0,4)/(50 0,2 • 0,5 0,5) = 24,58 м/мин.
Частота вращения шпинделя NШП(об/мин), определяется по формуле:
NШП= (VZС • 1000) /( π • dC), (2.2)
dC – диаметр рабочего инструмента (сверла), мм, (из задания).
NШП = (24,58 • 1000) / (3,14 • 30) = 260,93 об/мин.
Мощность резания при сверлении PZС (кВт), рассчитывается по формуле:
PZС = MC • NШП / 9550, (2.3)
где MC -вращающий момент на шпинделе при сверлении, Н∙м;
MC = 9,81• CM • SYm • dсZm, (2.4)
где CM, Ym, Zm– моментные коэффициенты и показатели степени, отн. ед. для сверления принимаются по (ПРИЛОЖЕНИЕ 1, Таблица 4).
MC = 9,81 • 0,0345 • 0,5 0,8 • 30 2=174,84 Н∙м;
PZС= 174,84 • 260,93 / 9550 = 4,78 кВт.
Расчетная мощность двигателя РДР (кВт), определяется по формуле:
РДР1= PZС / ηСТ, (2.5)
где ηСТ – КПД главного привода при полной нагрузке, отн.ед.,
ηСТ = 0,75.
РДР1= 4,78 / 0,75 = 6,4 кВт.
Согласно условия Р1 ≥ РДР1 выбирается асинхронный двигатель.
Параметры двигателя M1: по справочнику выбираю трехфазный двигатель типа АИР 132 S4, мощность Р1 = 7,5 кВт; номинальный ток
I1=15,6 А; напряжение питающей сети 380 В; частота f=50 Гц; частота вращения n=1455об/мин; =87,5%; соs=0,83; коэффициент пуска
Кпуск. = 7, (ПРИЛОЖЕНИЕ 2).
2.1.2. Расчет и выбор двигателя подачи суппорта
Мощность, расходуемая исполнительным органом станка на осуществление подачи суппорта, осуществляется двигателем М2 и может быть определена по мощности электродвигателя шпинделя М1.
PП = (0,001…0,01) • PZС, (2.6)
где PП– мощность подачи суппорта, кВт.
PП = (0,001…0,01) • 4,78 = 4,78 • 10-3... 4,78 • 10-2 кВт.
Принимаем PП = (4,78 • 10-3 + 4,78 • 10-2) : 2 = 2,64 • 10-2 кВт, что является средним арифметическим значением диапазона 4,78 • 10-3...4,78 • 10-2.
Расчетная мощность двигателя РДР2(кВт), определяется по формуле:
РДР2= PП / ηСТ2, (2.7)
где ηСТ2 – КПД привода подачи супорта, отн.ед.,
ηСТ2 = 0,15.
РДР2 = 0,0264 / 0,15 = 0,176 кВт.
Согласно условия Р2 ≥ РДР2 выбирается асинхронный двигатель.
Параметры двигателя M2: по справочнику выбираю трехфазный двигатель типа АИР 56 А2 мощностью Р2 = 0,18 кВт; номинальный ток I2 = 0,52 А; напряжение питающей сети 380 В; частотой f=50 Гц; частотой вращения n = 2700 об/мин; = 68%; соs = 0,78; коэффициент пуска Кпуск. = 5 [2](ПРИЛОЖЕНИЕ 3).
2.1.3. Расчет и выбор двигателя насоса подачи охлаждающей жидкости
Мощность двигателя М3 (кВт) определяется по формуле [2]:
РДР3 = (Кзап• U3 • Q3 • H3)/ (1000 • н3 • п3) , (2.8)
где Кзап= 1,5 – коэффициент запаса;
U3= 9810 н/м3 – плотность перекачиваемой жидкости;
Q3= 28•10-5 м3/с – производительность насоса;
Н3= 12 м – напор насоса;
н3= 0,5– КПД насоса охлаждения;
п3= 0,98 – КПД передачи.
РДР3 = (1,5 • 9810 • 0,00028 • 12 )/ (1000 • 0,5 • 0,98) = 0,1 кВт.
Согласно условия Р3 ≥ РДР3 выбирается асинхронный двигатель.
Параметры двигателя M3: по справочнику выбираю трехфазный электрический двигатель для насоса охлаждения типа АИР 50 В2 мощностью Р3= 0,12 кВт; номинальным током I3 = 0,39А; напряжение питающей сети 380 В; частотой f=50 Гц; частотой вращения n = 1325 об/мин; = 63%;
соs = 0,75; коэффициент пуска Кпуск.=5 (ПРИЛОЖЕНИЕ 2).
Основные параметры выбранных двигателей сведены в табл. 2.1.
Таблица 2.1
Технические данные электродвигателей станка
Обозначение на схеме | Марка двигателя | Р, кВт | Iном, А | КПД , % | cos | К пуск | n , об/мин |
М1 | АИР 132 S4 | 7,5 | 15,6 | 87,5 | 0,83 | 7 | 1455 |
М2 | АИР 56 A2 | 0,18 | 0,52 | 68 | 0,78 | 5 | 2700 |
М3 | АИР 50 В2 | 0,12 | 0,39 | 63 | 0.75 | 5 | 1325 |