Добавлен: 03.12.2023
Просмотров: 53
Скачиваний: 2
ВНИМАНИЕ! Если данный файл нарушает Ваши авторские права, то обязательно сообщите нам.
1.5Принятый маршрутный и операционный техпроцесс
В принятом технологическом процессе на всех операциях, требующих большой точности изготовления, базовыми поверхностями являются центровые отверстия. При этом технологические и конструкторские базы совпадают.
Таблица 4 – Технологический процесс изготовления детали втулка глухая
Наименование операции, содержание переходов | Оборудование, приспособление | Инструмент | |
Режущий | Средства измерения | ||
005 Токарно–револьверная 1. Подрезать торец Ø 124, выдержав 102 2.Точить с Ø 124 до Ø 120, выдержав 20 3.Точить фаску 3×45. | Токарно– револьверный станок 1П365 Трех-кулачковый патрон ГОСТ 2675-80 | Резец проходной 2102–0005 Т15К6 ГОСТ18877–73 | Штангенциркуль ШЦ-1-250-0,1 ГОСТ 166-89 |
010 Токарно–револьверная 1. Подрезать торец Ø 84, выдержав размер 100 2. Точить наружную поверхность Ø 80, выдержав 80 3. Точить фаску 2×45 на Ø 80 4. Расточить отверстие Ø 50 глубиной 90, выдержав 10 5. Расточить выточку Ø 60 шириной 5, выдержав 40 6. Точить фаску 2×45 в отверстии Ø 50 | Токарно-револьверный станок мод. 1П365 Трех-кулачковый патрон ГОСТ 2675-80 | Резец подрезной Т15К6 ГОСТ 18880-73 Резец проходной Т15К6 ГОСТ 18879-73 Резец расточной Т15К6 ГОСТ 18882-73 | Штангенциркуль ШЦ-1-150-0,1 ГОСТ 166-89 |
Продолжение таблицы 4 | |||
015 Сверлильная 1. Сверлить 3 отверстия Ø 6 под углом 120 поочередно 2. Сверлить 3 отверстия Ø 12 под углом 120 поочередно. | Радиально-сверлильный станок мод. 2Е52 Кондуктор. | Сверло спиральное 6 ГОСТ 4010-77 Сверло спиральное 12 ГОСТ 4010-77. | Калибр-пробка 6 ГОСТ 14811-69 Калибр-пробка 12 ГОСТ 14811-69. |
020 Сверлильная Сверлить отверстие Ø 12 под резьбу | Вертикально-сверлильный станок мод. 2Н118. Приспособление для зажима детали | Сверло спиральное 12 ГОСТ 4010-77 Метчик М12 ГОСТ3266-81 | Штангенциркуль ШЦЦ-1-125-0,01 ГОСТ 166-89 |
025 Резьбонарезная Нарезать резьбу М12-6Н | Вертикально-сверлильный станок мод. 2Н118 Приспособление для зажима детали | Сверло спиральное 12 ГОСТ 4010-77 Метчик М12 ГОСТ3266-81 | Штангенциркуль ШЦЦ-1-125-0,01 ГОСТ 166-89 |
030 Фрезерная 1. Фрезеровать лыску, выдержав размер 110 и угол 30 2. Фрезеровать вторую лыску, выдержав размер 110 и угол 30 | Вертикально-фрезерный станок мод. 6М13П Делительное приспособление для фрезерования | Фреза концевая Р6М5 ГОСТ 9304-69 | Штангенциркуль ШЦЦ-1-125-0,01 ГОСТ 166-89 |
035 Токарная Точить шпоночный паз шириной 14, выдержав 40 и 53,8 | Токарный станок мод. 16А20ФЗ с ЧПУ Трех-кулачковый патрон ГОСТ 2675-80 | Резец долбежный специальный | Штангенциркуль ШЦЦ-1-125-0,01 ГОСТ 166-89 |
040Термическая Закалка HRC45…50. | Печь | | |
045 Моечная | | | |
050Контрольная | | | |
2Расчетный раздел
2.1Расчет припусков на обработку и исходных размеров заготовки
Величина припуска зависит от количества операций, квалитета точности и типа оборудования. Завышенный припуск влияет на себестоимость продукции, т к увеличивается время на обработку , расход энергии, материала. Заниженный припуск также влияет на себестоимость (она увеличивается). При заниженном припуске невозможно получить заданную точность и размеры. Происходит перерасход материала, деталь уходит в неисправимый брак. Затраты на электроэнергию и заработанную плату увеличивают себестоимость. Припуски принимаются аналитическим путём (по справочнику) или рассчитываются по формулам:
Так как деталь является телом вращения , то формула для расчёта имеет вид:
2 Zmin= 2[????????+????+√????2+????2],
где Zmin– величина припуска;
Rz– высота микронеровностей (шероховатостей) профиля, полученная на предшествующем переходе обработки данной поверхности.;
T– высота дефектного слоя с предыдущей операции.;
ρ – суммарное значение пространственных отклонений ( увод инструмента и смещение отверстия, непаралельность осей, кривизна поверхности;
???? – погрешности установки заготовки в приспособлении.
Для приведения всех показателей в соответствие, табличные данные в мкм переводим в мм, разделив их на 1000.
Принимаем за основу деталь втулка глухая. Выбираем для обработки наружную поверхность Ø 80, длина мм.
В данном случае суммарное значение пространственных отклонений определяется по формуле:
ρ =????кор· Δк ,
где ????кор – погрешность коробления; мкм.
Δк – удельная кривизна обрабатываемой поверхности, мкм/мм.
Принимаем Δк=0,25мкм/мм
????кор = 0,25 · 80 =20мкм.
Погрешность установки для однопозиционной обработки определяется по формуле
εу=√???????? + ????З ,
где εδ – погрешность базирования, мкм;
εЗ – погрешность закрепления, мкм.
При обработке на токарно-револьверных патронных станках погрешность закрепления мала , и ею можно пренебречь, т е. εз=0 мкм.
Так как обработка происходит без снятия детали за один установ, то погрешность базирования εδ = 0 мкм.
Тогда, при точении εу= 0 мкм.
Определяем величину межоперационного припуска по каждому переходу:
Значения для токарной операции: Rz=40 мкм; Т=20 мкм.
Значение для заготовки Rz=160 мкм; Т=200 мкм.
Тогда припуск для чистовой токарной:
2 Zmin ток = 2 ·[50+60+√202+02] = 260мкм;=0,26мм
Для заготовки:
2 Zmin п = 2 ·[160+200+√202+02] = 760мкм;=0,76мм.
Определяем диаметр заготовки для токарной операции:
Диаметр минимальный рассчитывается по формуле :
Dmin ток = Dn+????,
где Dmin ток – диаметр минимальный;
Dn- диаметр номинальный 80 мм;
????- величина допуска (для данного чертежа допуск равен 0).
Dmin ток=80+0= 80мм.
Диаметр максимальный рассчитывается по формуле :
Dmах ток= Dmin ток+ Zmin ток ,
где Dmах ток – диаметр максимальный;
Dmin ток – диаметр минимальный 80 мм;
Zmin ток – величина припуска 0,17 мм.
Dmах ток= 80 +0,26 = 80,26мм;
Определяем диаметр заготовки(поковки):
Dmin п = Dn+????,
???? = 0 мм;
Dn – номинальным диаметром для поковки является максимальный диаметр с предыдущей операции, т.е.80,17.
Dmin п= 80,26+ 0 =80,26мм.
Dmах п = Dmin п + Zmin п
Dmах п= 80,26+ 0,76 = 81,02мм;
Таблица 2 – Расчет межоперационных припусков
Наименование операции | Rz,мкм | T,мкм | ρ ,мкм | ![]() | Dmin ,мм | Dmax,мм |
Заготовка | 160 | 200 | 20 | 0 | 80,26 | 81,02 |
Чистовая токарная | 50 | 60 | 20 | 0 | 80 | 80,26 |
Исходя из размеров поковки по ГОСТ 1050–2013 принимаем размер заготовки диаметром 84мм.
2.2Расчет веса заготовки и детали
Для определения веса заготовки и детали втулка глухая разобьем конструкцию детали на геометрические фигуры – цилиндры. Вес детали определяется по формуле:
Gдет = Vобщ · g ,
где Gдет – вес детали, кг;
Vобщ – объем детали, см3;
g – плотность материала Стали 45Х –7,82 кг/см3.
Рассчитываем вес заготовки. Для этого разбиваем заготовку на отдельные объемы.
Vобщ = V1+V2 –V3,
где V1 – объем цилиндра 1, см3;
V2 – объем цилиндра 2, см3;
V3 – объем цилиндра 3 (отверстия), см3.
Проводим расчеты, используя формулу вычисления объема цилиндра:

где d- диаметр цилиндра, см;
h - длина цилиндра, см;
V1=

V2=

V3=

Vобщ.заг= 289,7 + 443,11–132,8 = 600,01см3,
Gзаг= 600,01 · 7,82 =4,692 кг.
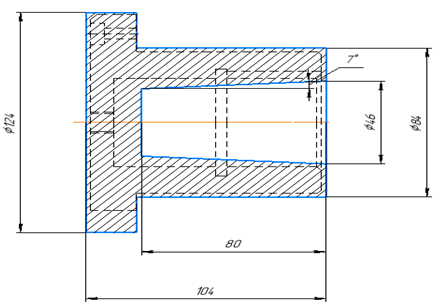
Рисунок 1 – заготовка
Рассчитываем вес детали, также разбивая ее на отдельные объемы.
V1=

V2=

V3=

V4=

V5= 0,4·1,4·5,38 = 3,01см3,
V6=

V7=

V8=πhR – объем лысок,
V8= 3,14·0,7·1,4=4,3·2=0,54см3,
Vобщ.дет=241,4+401,9–254,3–78,5–3,01–4,5–1,1=301,8см3,
Gдет = 301,8 · 7,82 =2,356 кг
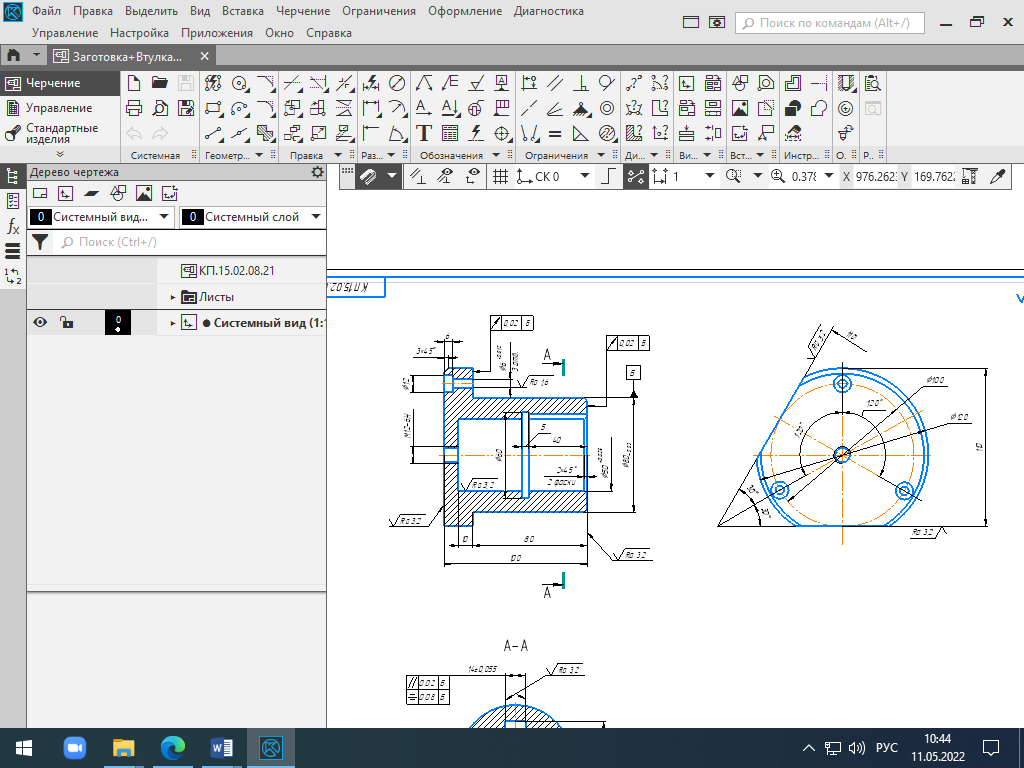
Рисунок 2 – деталь гайка глухая
2.3 Расчет КИМ(коэффициента использования материала)
КИМ =

где G