Файл: Изучение и разработка технологии изготовления вертикального стального резервуара рвс400.docx
Добавлен: 04.12.2023
Просмотров: 115
Скачиваний: 4
ВНИМАНИЕ! Если данный файл нарушает Ваши авторские права, то обязательно сообщите нам.
крышей высотные отметки центрально щита, монтажной стойки должны определяться с учетом проектной высоты и строительного подъема, предусмотренных рабочей документацией.
Монтаж люков и патрубков резервуаров:
При разметке мест установки в стенки резервуара люков и патрубков должны выполняться требования по допускаемым расстояниям между сварными швами.
Расстояние от внешнего края усиливающих накладок до оси горизонтальных стыковых швов стенки должно быть не менее 100 мм, а до оси вертикальных стыковых швов стенки или между внешними краями двух рядом расположенных усиливающих накладок патрубков — не менее 250 мм.
Допускается перекрытие горизонтального шва стенки усиливающим листом приемо-раздаточного патрубка или люка-лаза Dу 800-900 мм на величину не менее 150 мм от контура накладки. Перекрываемый участок шва должен быть проконтролирован радиографическим методом.
Контроль качества сварной конструкции:
Контроль качества сварных соединений производят способами и в объёмах, предусмотренных ППР согласно требованиям ПБ 03-605-03 и СНиП 3.03.01-87.
Качество сварных соединений должно соответствовать требованиям ПБ 03-605-03, СНиП 3.03.01-87.
При сооружении резервуара необходимо выполнить следующие виды контроля качества сварных соединений:
- визуальный контроль всех сварных соединений;
- измерительный;
- контроль герметичности (непроницаемости) сварных швов;
- гидравлические прочностные испытания.
Визуальному контролю должны подвергаться 100% длины всех сварных соединений резервуара.
По внешнему виду сварные швы должны удовлетворять следующим требованиям:
- по форме и размерам швы должны соответствовать проекту;
- швы должны иметь гладкую или равномерно чешуйчатую поверхность (высота или глубина впадин не должна превышать 1 мм);
- металл шва должен иметь плавное сопряжение с основным металлом;
- швы не должны иметь недопустимых внешних дефектов: трещин любых видов и размеров, несплавлений, наплывов, грубой чешуйчатости, наружных пор и цепочек пор, прожогов и свищей.
При этом сварные соединения должны удовлетворять следующим требованиям:
- смещение кромоксварных соединений по внутренней поверхности резервуара не должно превышать 0,1t, где t - наименьшая толщина листов стыка;
- для стыковых соединений из деталей одной толщины смещение свариваемых кромок относительно друг друга - 1 мм;
- выпуклость швов вертикальных стыковых соединений стенки при толщине листов не должна быть более 1,5 мм, прочих соединений - 2,0 мм;
- подрезы основногометалла:
вертикальные поясные швы и соединениестенки с днищем - 5% толщины, но не более 0,5 мм; горизонтальные соединения стенки - 5% толщины, но не более 0,8 мм; прочих сварных соединений - 5% толщины, но не более 0,8 мм;
- выпуклость или вогнутость углового шва не должна превышать более чем на 20% величину катета шва;
- уменьшение катета углового шва допускается не более 1мм.
Увеличение катета углового шва допускаетсяне более следующих значений:
- для катетов до 5 мм -1 мм;
- для катетов свыше 5 мм - 2,0 мм;
- в местах пересечения сварных швов и в местах исправления дефектов необходимо обеспечивать минимальную концентрацию напряжений за счет обеспечения плавного сопряжения шва с основным металлом; угловатость вертикальных и горизонтальных сварных соединений допускается не более 3 мм на базе 200 мм.
Контролю на герметичность подлежат все сварныешвы, обеспечивающие герметичность резервуара.
Контроль герметичности сварных соединений стенки и днища производят вакуумно-пузырьковым методом с применением вакуумных камер по ГОСТ 3242-79. Величина разрежения не менее 2,5 кПа.
Контролю давлением подлежат сварные швы приварки усиливающих листов люков и патрубков на стенке резервуара в соответствии с п. 7.4.5 ПБ 03-605-03.
Контроль герметичности сварных соединений крыши проводят в процессе гидравлических и пневматических испытаний за счёт создания избыточного давления воздуха внутри резервуара 1,5 - 2,0 кПа.
Испытание и приёмка резервуара.
Резервуардолжен быть подвергнут гидравлическому испытанию. Гидравлические испытания резервуара проводить в соответствии с рекомендациями ПБ 03-605-03.
Испытание резервуара проводят после окончания всех работ по монтажу и контролю, перед присоединением к резервуару трубопроводов (за исключением временных трубопроводов для подачи и слива воды для испытания) и после завершения работ по обвалованию.
До начала испытания должна быть представлена вся техническая документация по изготовлению, монтажу и контролю качества выполненных работ.
Испытания проводят в соответствии с технологическими картами испытаний проекта производства работ (ППР).
В течение всегопериода гидравлического испытания все люки и патрубки в стационарной крыше резервуара должны быть открыты.
По мере заполнения резервуара водой необходимо наблюдать за состоянием конструкций и сварных швов. При обнаружении течи из-под края днища или появления мокрых пятен на поверхности отмостки необходимо прекратить испытания, слить воду, установить и устранить причину течи.
Если в процессе испытания будут обнаружены свищи, течи или трещины в стенке резервуара (независимо от величины дефекта), испытания должно быть прекращено и вода слита до уровня в случаях:
- при обнаружениидефекта в 1-ом поясе - полностью;
- приобнаружениидефекта во 2-ом - 5-м поясах - на один пояс ниже расположения дефекта.
Резервуар,залитый водой до верхней проектной отметки, выдерживается под этой нагрузкой в течении не менее 24 часов.
Резервуар считается выдержившим гидравлические испытания, если в течение указанного времени на поверхности стенки или по краям днища не появляются течи и если уровень воды не снижается.
После окончания гидравлических испытаний, при залитой до проектной отметки водой резервуаре, производят замеры отклонений образующих от вертикали, замеры отклонений наружного контура днища для определения осадки основания (фундамента).
Предельные отклонения должны соответствовать требованиям таблицы 5.2 ПБ 03-605-03.
9.8 После завершения испытаний не допускается приварка к резервуару каких-либо деталей и конструкций. На резервуаре производят работы по антикоррозионной защите, установке оборудования с оформлением соответствующих документов.
Основные расчётные положения и показатели резервуара.
Список использованных ресурсов:
Овчинников В.В. «Расчет и проектирование сварных конструкций» Издательский центр «Академия» 2010 год.
Милютин В.С., Катаев Р.Ф «Источники питания и оборудования для электрической сварки плавлением» Издательский центр «Академия» 2010год.
Выборнов А.П. Маслов Б.Г «Производство сварных конструкций» Издательский центр «Академия» 2010год.
Полевой Г.В. «Газопламенная обработка металлов» Издательский центр «Академия» 2005год.
Чернышов Г.Г. Технология электрической сварки плавлением Издательский центр «Академия» 2010 год.
Овчинников В.В. «Оборудование, механизация и автоматизация сварочных процессов» Издательский центр «Академия» 2010год.
Боровков В.М., Калютик А.А « Изготовление и монтаж технологических трубопроводов» Издательский центр «Академия» 2007год.
Монтаж люков и патрубков резервуаров:
При разметке мест установки в стенки резервуара люков и патрубков должны выполняться требования по допускаемым расстояниям между сварными швами.
|
Расстояние от внешнего края усиливающих накладок до оси горизонтальных стыковых швов стенки должно быть не менее 100 мм, а до оси вертикальных стыковых швов стенки или между внешними краями двух рядом расположенных усиливающих накладок патрубков — не менее 250 мм.
Допускается перекрытие горизонтального шва стенки усиливающим листом приемо-раздаточного патрубка или люка-лаза Dу 800-900 мм на величину не менее 150 мм от контура накладки. Перекрываемый участок шва должен быть проконтролирован радиографическим методом.
Контроль качества сварной конструкции:
Контроль качества сварных соединений производят способами и в объёмах, предусмотренных ППР согласно требованиям ПБ 03-605-03 и СНиП 3.03.01-87.
Качество сварных соединений должно соответствовать требованиям ПБ 03-605-03, СНиП 3.03.01-87.
При сооружении резервуара необходимо выполнить следующие виды контроля качества сварных соединений:
- визуальный контроль всех сварных соединений;
- измерительный;
- контроль герметичности (непроницаемости) сварных швов;
- гидравлические прочностные испытания.
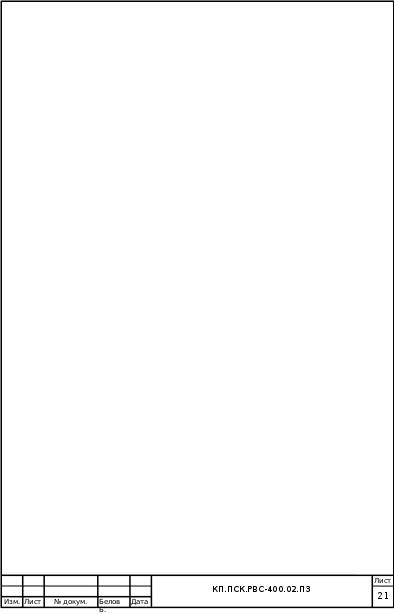
По внешнему виду сварные швы должны удовлетворять следующим требованиям:
- по форме и размерам швы должны соответствовать проекту;
- швы должны иметь гладкую или равномерно чешуйчатую поверхность (высота или глубина впадин не должна превышать 1 мм);
- металл шва должен иметь плавное сопряжение с основным металлом;
- швы не должны иметь недопустимых внешних дефектов: трещин любых видов и размеров, несплавлений, наплывов, грубой чешуйчатости, наружных пор и цепочек пор, прожогов и свищей.
При этом сварные соединения должны удовлетворять следующим требованиям:
- смещение кромоксварных соединений по внутренней поверхности резервуара не должно превышать 0,1t, где t - наименьшая толщина листов стыка;
- для стыковых соединений из деталей одной толщины смещение свариваемых кромок относительно друг друга - 1 мм;
- выпуклость швов вертикальных стыковых соединений стенки при толщине листов не должна быть более 1,5 мм, прочих соединений - 2,0 мм;
- подрезы основногометалла:
вертикальные поясные швы и соединениестенки с днищем - 5% толщины, но не более 0,5 мм; горизонтальные соединения стенки - 5% толщины, но не более 0,8 мм; прочих сварных соединений - 5% толщины, но не более 0,8 мм;
- выпуклость или вогнутость углового шва не должна превышать более чем на 20% величину катета шва;
- уменьшение катета углового шва допускается не более 1мм.
Увеличение катета углового шва допускаетсяне более следующих значений:
- для катетов до 5 мм -1 мм;
- для катетов свыше 5 мм - 2,0 мм;
- в местах пересечения сварных швов и в местах исправления дефектов необходимо обеспечивать минимальную концентрацию напряжений за счет обеспечения плавного сопряжения шва с основным металлом; угловатость вертикальных и горизонтальных сварных соединений допускается не более 3 мм на базе 200 мм.
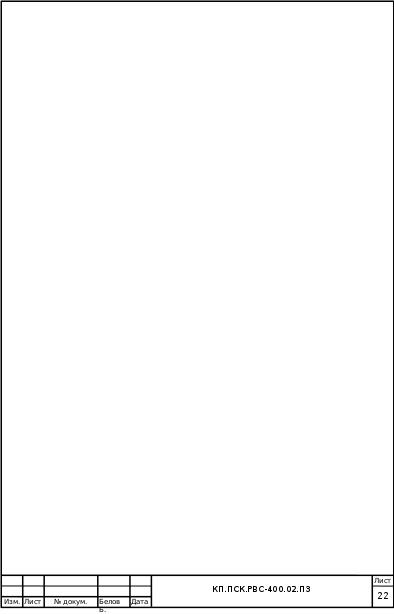
Контроль герметичности сварных соединений стенки и днища производят вакуумно-пузырьковым методом с применением вакуумных камер по ГОСТ 3242-79. Величина разрежения не менее 2,5 кПа.
Контролю давлением подлежат сварные швы приварки усиливающих листов люков и патрубков на стенке резервуара в соответствии с п. 7.4.5 ПБ 03-605-03.
Контроль герметичности сварных соединений крыши проводят в процессе гидравлических и пневматических испытаний за счёт создания избыточного давления воздуха внутри резервуара 1,5 - 2,0 кПа.
Испытание и приёмка резервуара.
Резервуардолжен быть подвергнут гидравлическому испытанию. Гидравлические испытания резервуара проводить в соответствии с рекомендациями ПБ 03-605-03.
Испытание резервуара проводят после окончания всех работ по монтажу и контролю, перед присоединением к резервуару трубопроводов (за исключением временных трубопроводов для подачи и слива воды для испытания) и после завершения работ по обвалованию.
До начала испытания должна быть представлена вся техническая документация по изготовлению, монтажу и контролю качества выполненных работ.
Испытания проводят в соответствии с технологическими картами испытаний проекта производства работ (ППР).
В течение всегопериода гидравлического испытания все люки и патрубки в стационарной крыше резервуара должны быть открыты.
По мере заполнения резервуара водой необходимо наблюдать за состоянием конструкций и сварных швов. При обнаружении течи из-под края днища или появления мокрых пятен на поверхности отмостки необходимо прекратить испытания, слить воду, установить и устранить причину течи.
Если в процессе испытания будут обнаружены свищи, течи или трещины в стенке резервуара (независимо от величины дефекта), испытания должно быть прекращено и вода слита до уровня в случаях:
- при обнаружениидефекта в 1-ом поясе - полностью;
- приобнаружениидефекта во 2-ом - 5-м поясах - на один пояс ниже расположения дефекта.
Резервуар,залитый водой до верхней проектной отметки, выдерживается под этой нагрузкой в течении не менее 24 часов.
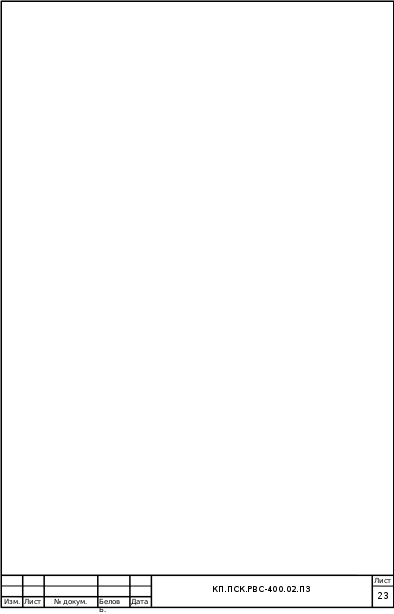
После окончания гидравлических испытаний, при залитой до проектной отметки водой резервуаре, производят замеры отклонений образующих от вертикали, замеры отклонений наружного контура днища для определения осадки основания (фундамента).
Предельные отклонения должны соответствовать требованиям таблицы 5.2 ПБ 03-605-03.
9.8 После завершения испытаний не допускается приварка к резервуару каких-либо деталей и конструкций. На резервуаре производят работы по антикоррозионной защите, установке оборудования с оформлением соответствующих документов.
Основные расчётные положения и показатели резервуара.
2.1 | Наименование продукта | мазут |
2.2 | Плотность продукта | 0,99 т/м3 |
2.3 | Плотность при гидроиспытаниях | 1,0 т/м3 |
2.4 | Температура наиболее холодных суток (с обеспеченностью 0,98 по СНиП 23-01-99) | минус 31°С |
2.5 | Расчётная температура металла | минус 26°С |
2.6 | Внутренне избыточное давление в газовом пространстве аварийное | 2,0 кПа 2,3 кПа |
2.7 | Относительный вакуум в газовом пространстве аварийный | 0,2 кПа 0,40 кПа |
2.8 | Расчётный вес снегового покрова | 1,2 кПа |
2.9 | Нормативный скоростной напор ветра | 0,45 кПа |
2.10 | Расчётная сейсмичность | до 6 баллов |
2.11 | Теплоизоляция: стенки крыши | 80 мм 80 мм |
2.12 | Диаметр резервуара | 8,44 м |
2.13 | Высота стенки резервуара | 7,5 м |
2.14 | Площадь зеркала продукта | 57,2 м2; |
2.15 | Рабочая высота налива продукта | 6,75 м |
2.16 | Расчётная высота налива воды при гидроиспытаниях | 7,4 м |
2.17 | Номинальный объём резервуара | 426,1 м3; |
2.18 | Полезный объём резервуара | 386,1 м3; |
2.19 | Конструкции днища | полистовой сборки |
2.20 | Конструкция стенки | полистовой сборки |
2.21 | Конструкция крыши | щитовая коническая |
2.22 | Лестница для подъёма на резервуар | многомаршевая кольцевая |
2.23 | Припуски на коррозию: стенки днища крыши | + 1 мм + 2 мм + 1 мм |
2.24 | Нормативный срок эксплуатации резервуара | 30 лет |
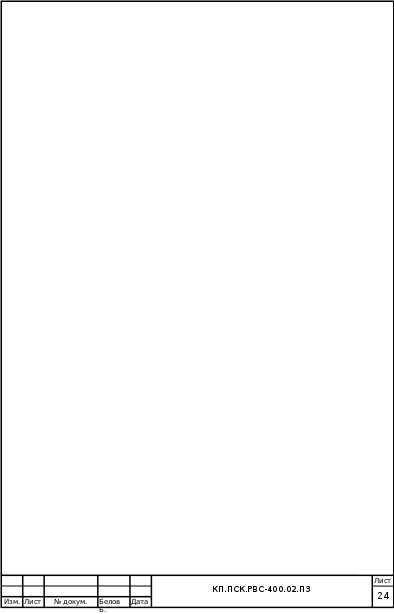
Овчинников В.В. «Расчет и проектирование сварных конструкций» Издательский центр «Академия» 2010 год.
Милютин В.С., Катаев Р.Ф «Источники питания и оборудования для электрической сварки плавлением» Издательский центр «Академия» 2010год.
Выборнов А.П. Маслов Б.Г «Производство сварных конструкций» Издательский центр «Академия» 2010год.
Полевой Г.В. «Газопламенная обработка металлов» Издательский центр «Академия» 2005год.
Чернышов Г.Г. Технология электрической сварки плавлением Издательский центр «Академия» 2010 год.
Овчинников В.В. «Оборудование, механизация и автоматизация сварочных процессов» Издательский центр «Академия» 2010год.
Боровков В.М., Калютик А.А « Изготовление и монтаж технологических трубопроводов» Издательский центр «Академия» 2007год.
-
http://gazovik-pgo.ru -
http://www.metalbak.ru -
http://www.energypoint.ru -
http://ru.wikipedia.org -
http://www.neft-rus.ru -
http://www.himstalcon.ru -
http://www.r-stroitel.ru -
http://www.drevniymir.ru -
http://metallicheckiy-portal.ru