Файл: Расчёт и проектирование схемы управления станции лазерной резки.docx
ВУЗ: Не указан
Категория: Не указан
Дисциплина: Не указана
Добавлен: 04.12.2023
Просмотров: 82
Скачиваний: 6
ВНИМАНИЕ! Если данный файл нарушает Ваши авторские права, то обязательно сообщите нам.
2) с манипулятором оптики: луч лазера перемещается по заданной траектории, а стол с листом неподвижен;
3) смешанного типа: луч лазера перемещается в поперечном направлении, а стол с листом – в продольном. Сложение обоих движений по определенной траектории обеспечивает получение заданного контура вырезаемой детали.
Машины первого и третьего классов применяются для резки листов небольших и средних размеров, второго – для резки средних и крупных листов.
Особый интерес представляют лазерные роботы с манипуляторами оптики со сложной траекторией. Они предназначены для обработки тел вращения. В этом случае необходимо обеспечить перемещение по пяти-шести координатам.
В настоящее время металлообрабатывающие отрасли уже не устраивают специализированные лазерные комплексы для выполнения отдельных технологических операций (резки, сварки, прошивки и т.д.). Рынок требует оборудования с высокой степенью интеграции технологических операций. К такому оборудованию относятся лазерные обрабатывающие центры (ЛОЦ), предназначенные для операций сварки, прошивки, резки, термоупрочнения и маркировки с программным управлением. Переналадка с одной операции на другую происходит автоматически.
Особенно перспективные разработки ЛТК для совместного использования воздействия лазерного излучения и других источников нагрева, например, плазмы, газового пламени. В этих комплексах удается повысить скорость обработки, в несколько раз увеличить глубину резки при сохранении всех преимуществ лазерного излучения. Кроме того, такие ЛТК универсальны
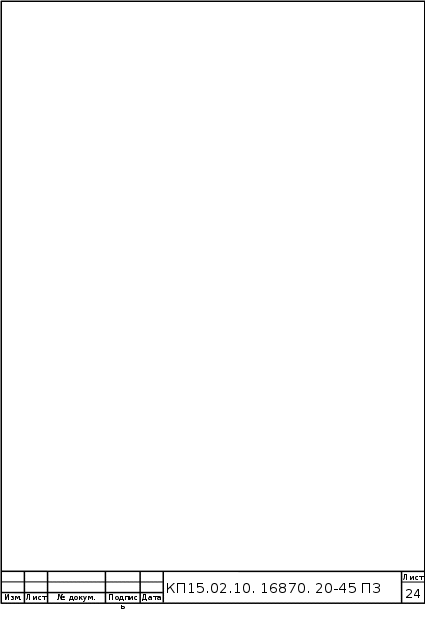
Большую перспективу имеют комбинированные системы, использующие лазер и оборудование для механической обработки материалов. Комбинации лазера и пресса для высечки, вырубки и штамповки реализованы в комплексах «лазер - пресс».
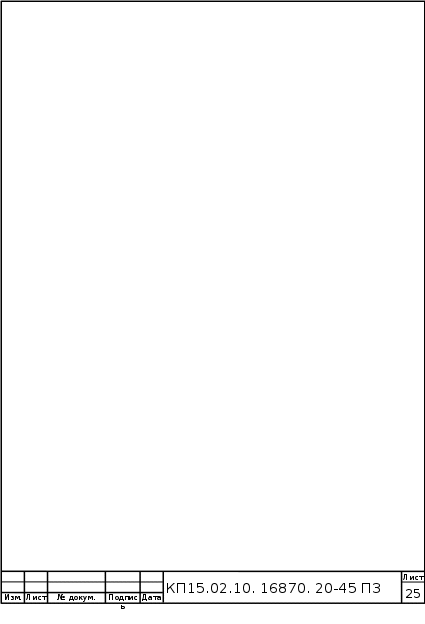
Плазменные стационарные и переносные машины и резательные комплекты сложны и дороги. В комплект оборудования для плазменно-дуговой резки входят режущий плазмотрон (резак), узел управления процессом, источники питания дуги электрическим током и плазмообразующей рабочей средой, механизм для перемещения плазмотрона вдоль линии реза, блок автономного охлаждения для плазмотронов с водяным охлаждением (при отсутствии системы водоснабжения). Источники тока для плазменной резки имеют крутопадающую внешнюю характеристику, повышенное напряжение холостого хода (более 100 В), естественное охлаждение, возможность ступенчатого или плавного регулирования тока.
Плазмотроны в зависимости от мощности имеют воздушное или водяное охлаждение, снабжены кабель-шлангом длиной до 6 м (иногда до 20 м). Ручной плазмотрон состоит из режущей головки и пластмассового корпуса с подходящими к нему воздухо-токоподводом и проводами. На его рукоятке размещена кнопка включения процесса. Плазмотроны для механизированной резки обычно имеют проточное водяное охлаждение
Плазмотрон имеет дуговую камеру, содержащую электродный элемент для формирования катодной области режущего разряда 1 и электрически изолированное от него сопловое устройство 3. Катод плазмотрона 4 изготавливают из тугоплавких материалов с высокими эмиссионными характеристиками. Для работы в нейтральных плазмообразующих средах используют вольфрам. В окислительных средах применяют катоды из циркония и гафния (пленочные катоды). В плазмотронах для машинной резки наиболее часто используют гильзовую конструкцию катодов. Катододержатель интенсивно охлаждают проточной водой. Рабочий торец пленочных катодов – плоский, вольфрамовые катоды имеют коническую заточку. Формирующее сопло обеспечивает ограничение диаметра столба
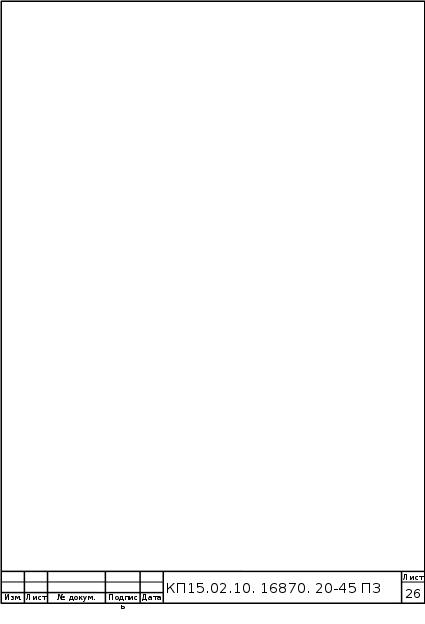
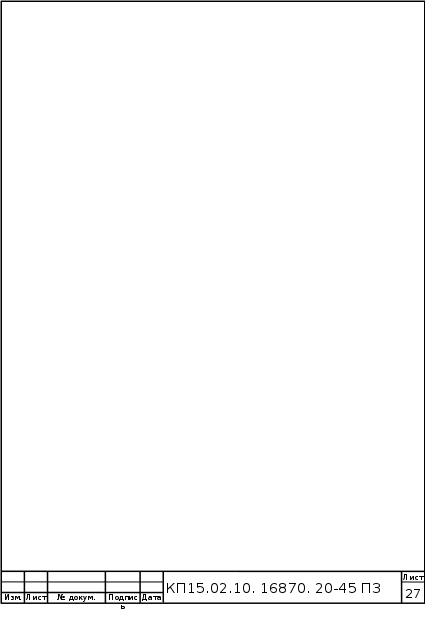
Механизированный плазмотрон может быть размещен на стационарных установках портального, портально-консольного, шарнирно-пантографического типов с использованием различных систем управления перемещением: с ЧПУ, фотоэлектронной, линейной с ручным регулированием скорости, с магнитным копированием.
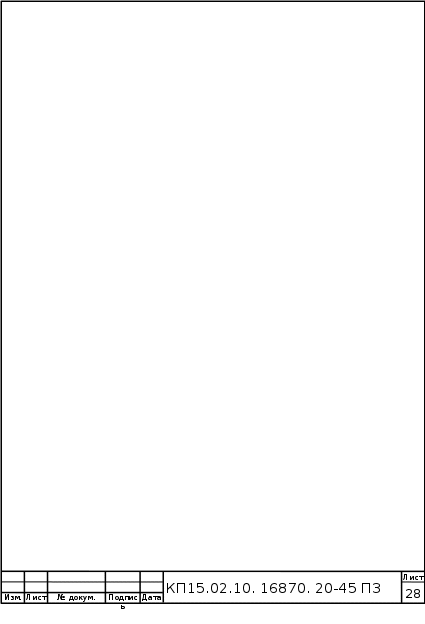
Оборудование для гидроабразивной резки. Учитывая специфику ГАР, выпускаются только стационарные установки для резки. В комплект оборудования для ГАР обычно входят следующие функционально объединенные узлы:
– насос высокого давления – предназначен для сжатия рабочей жидкости (воды) до требуемого давления и передачи ее в режущую головку;
– блок режущей головки – служит для преобразования статического давления рабочей жидкости в кинетическую энергию струи, выполнения собственно процесса резки, а также для хранения и выдачи абразива в смесительную камеру;
– станция очистки воды – предназначена для забора рабочей жидкости из водопроводной сети, очистки и подачи её в насос высокого давления;
– стол технологический с водосборником и устройством позиционирования – предназначен для размещения заготовок, приема рабочей жидкости и отходов резания, перемещения режущей головки по заданной траектории.
– блок подачи абразива – предназначен для хранения, дозирования и подачи в режущую головку абразива;
– система управления – предназначена для программирования и управления гидроабразивным комплексом. Для удобства оператора в непосредственной близости к зоне резки установлен пульт оператора с расположенными на нем органами управления комплексом;
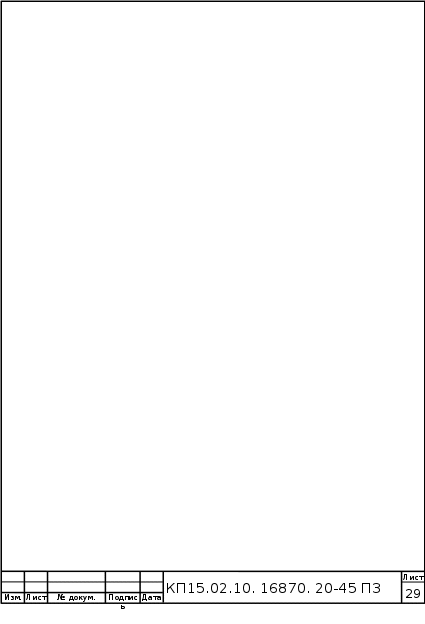
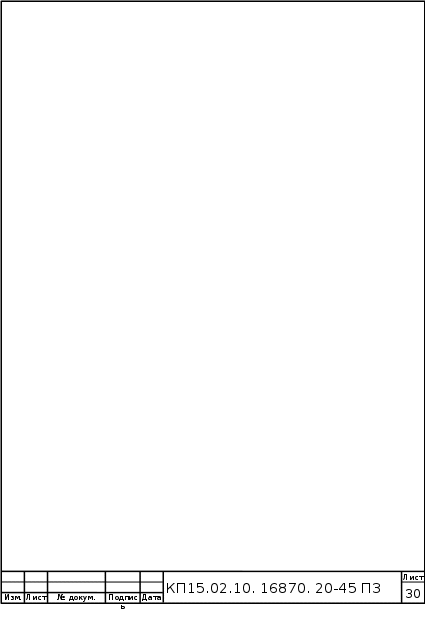
Разработанное программное обеспечение UniCut имеет простое, ориентированное на пользователя управление. В ПО UniCut реализованы функции, существенно упрощающие и оптимизирующие процесс резки. Это такие функции как: пауза, обратный ход по контуру, быстрый переход к любой врезке, быстрое изменение точки врезки, начало резки с любого места контура и т.д. Управление с одного рабочего места и из одной программы. Для безусловного комфорта работы с установкой интерфейсы управления всеми узлами станка интегрированы в одну программную оболочку. Дополнительным удобством для оператора является контроль над всеми модулями раскройного комплекса с одного рабочего места.
Отдельная настройка режимов прожига, гравировки и резки Режимы прожига, гравировки и резки настраиваются оператором по отдельности до начала резки. Оператору не придется останавливать процесс обработки материала, чтобы перенастроить станок и ввести новые уставки, т.к. переключение между режимами происходит автоматически, что увеличивает производительность раскройного комплекса.
Для получения качественных острых и прямых углов мощность лазерного излучения автоматически регулируется в зависимости от скорости передвижения оптической головки. При нулевой скорости движения оптической головки (в момент остановки на углу) выходная мощность излучения равняется минимальной мощности, заданной в настройках, что предотвращает выгорание углов.
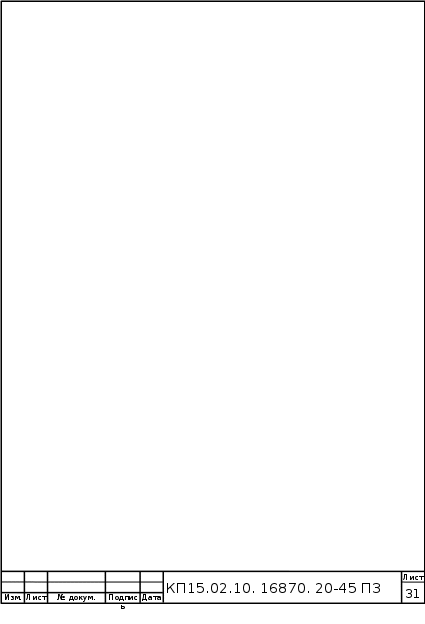
Лазерная резка металла признана одной из самых перспективных технологий раскроя листовых материалов, разрезания корпусных заготовок. Преимущества бесконтактного метода в высокой скорости, исключительной точности и образцовом качестве получаемого реза. По окончании кроя детали, полученные из заготовок, не требуют дальнейшей доработки, готовы для последующих операций. Гибкость настроек лазерной резки обуславливает возможность изготовления деталей сложной формы.
В результате проделанной работы был у нас проект, где был произведен расчёт и спроектирован……, минимум проанализирован….!описан принцип работы лазера, виды лазеров для резки металла, в результате исследований была создана структурная схема лазерного технологического комплекса, а также произведён анализ и расчёт системы ЧПУ.
Таким образом, задание на курсовой проект выполнено.
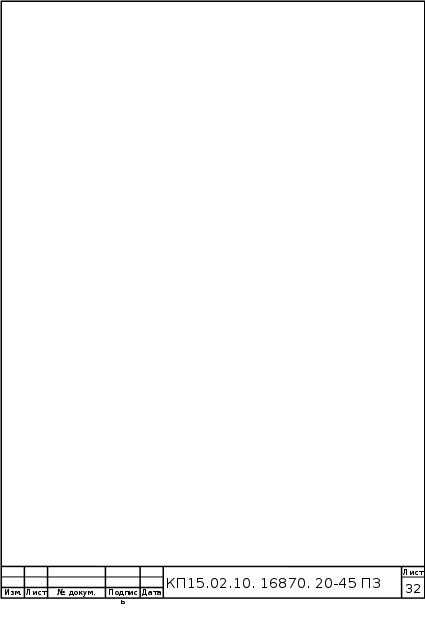
-
Нормативно техническая документация , технологический процесс. -
Лазерная и электронно-лучевая обработка материалов: Справочник /Н.Н. Рыкалин, А.А. Углов, И.В. Зуев, А.Н. Кокора. - М.: -
Машиностроение, 2009 - 496 с. 21.Лазерная техника и технология. В 7 кн. Кн. 4. Лазерная обработка неметаллических материалов. А.Г. Григорьянц, А.А. Соколов. - М.: Высш. шк, 2011 - 192 с. -
Лазерная техника и технология. В 7 кн. Кн. 7. Лазерная резка металлов. А.Г. Григорьянц, А.А. Соколов - М.: Высш. шк, 2011. - 128 с.