ВУЗ: Не указан
Категория: Не указан
Дисциплина: Не указана
Добавлен: 05.12.2023
Просмотров: 76
Скачиваний: 1
ВНИМАНИЕ! Если данный файл нарушает Ваши авторские права, то обязательно сообщите нам.
СОДЕРЖАНИЕ
Смачиваемость пыли также важно учитывать при определении метода очистки (в данном варианте достаточно высоко значение смачиваемости пыли - 70 %): чем больше смачиваемость, тем частицы лучше улавливаются, что непосредственно оказывает влияние на эффективность пылеулавливания в мокрых аппаратах.
Абразивность пыли характеризует интенсивность износа металла при одинаковых скоростях газов и концентрациях пыли. Особенно это касается сухих инерционных аппаратов (в том числе циклонов), стенки которых подвержены интенсивному износу. Это свойство пыли учитывается при расчетах аппаратуры (выбор скорости газа, толщины стенок аппаратуры и облицовочных материалов)[3].
Глава 2. Анализ используемых методов и систем обеспечения техносферной Безопасности на выбранном объекте.
2.1 Анализ существующей системы защиты от ОВФ, возможных инженерно-конструкторских решений, обеспечивающих достижение поставленной в техническом задании задачи.
Для очистки выбросов от газообразных примесей (оксиды серы и азота, оксид углерода, сероводород, аммиак и др.) применяют методы абсорбции, хемосорбции, адсорбции, каталитического и термического дожигания.
Метод абсорбции основан на поглощении одного или нескольких вредных веществ жидким поглотителем, называемым абсорбентом. При выборе абсорбента учитывается растворимость извлекаемого компонента и её зависимость от температуры и давления. В качестве растворителя применяют воду, кислые, щелочные и другие растворы. Например, для удаления из технологических выбросов аммиака, хлористого или фтористого водорода целесообразно применять воду, так как растворимость этих газов в воде составляет сотни граммов на 1 кг. Для удаления ароматических углеводородов из коксового газа применяются вязкие масла.
По конструкции абсорбционные аппараты близки к мокрым пылеуловителям.
Эффективность абсорбционного (мокрого) метода очистки газов, например, от хлористого водорода, может достигать 85-92% при использовании в качестве абсорбента 2-3% раствора едкой щёлочи, и 75% - при использовании воды.
Метод хемосорбции основан на поглощении газов и паров твёрдыми или жидкими поглотителями с образованием малолетучих или малорастворимых химических соединений.
Метод адсорбции основан на селективном поглощении вредных газов и паров твёрдыми сорбентами, имеющими развитую микропористую структуру.
В качестве адсорбента чаще всего применяют активированный уголь с помощью которого очищают газы от органических паров, летучих растворителей, дурно пахнущих веществ. Кроме того, в качестве адсорбента применяют силикагель, активированный глинозём, оксид алюминия, цеолиты. Часто адсорбенты пропитываются соответствующими реагентами, повышающими эффективность адсорбции, в этом случае происходит и хемосорбция.
Каталитический метод основан на превращении вредных компонентов промышленных выбросов в вещества менее вредные или безвредные за счёт химических реакций взаимодействия удаляемых веществ с одним из компонентов, присутствующим в очищаемом газе, или со специально добавляемым в смесь веществом на твёрдых катализаторах. В качестве катализатора обычно используются платина и металлы платинового ряда, оксиды меди и марганца, марганцевая руда и другое, выполненные в виде шариков, гранул, колец или проволоки, свитой в – спираль. В последние годы методы каталитического дожигания нашли применение и в автомобилестроении.
Термический метод основан на высокотемпературном сжигании вредных примесей, содержащихся в технологических вентиляционных и других выбросах. Для осуществления дожигания необходимо поддержание высоких температур очищаемого газа и наличие достаточного количества кислорода. Система огневого обезвреживания обеспечивает эффективность очистки, например, от оксида углерода, на 90-99%, если время пребывания газовой смеси в высокотемпературной зоне не менее 0,5 сек. и температура обезвреживаемых газов 600-750 °С.
Выбор очистных устройств состоит в определении способа очистки загрязнённого воздуха, количества ступеней очистки и типа пылегазоулавливающих аппаратов. Принимать к установке следует только такие устройства, которые в конкретных условиях сочетали бы в себе требующуюся эффективность очистки, надёжность и экономичность, например, возможность возврата уловленной пыли (продукта) в производство [3].
Принято считать, что при запылённости 5000 мг/м3 нетоксичной пылью достаточно одной ступени очистки, а при большей – нужна двух-трёхступенчатая очистка. Чем крупнее частицы пыли (золы) и больше их плотность, чем ниже температура газа, тем эффективнее при прочих равных условиях газ будет очищаться от пыли в аппаратах любого типа.
Совершенствование технологических процессов, применение высокоэффективных систем газоочистки позволяют в значительной степени уменьшить размеры промышленных выбросов в атмосферу.
Однако полностью ловить пыле- и газообразные примеси в отходящих газах практически невозможно, часть вредных веществ всё равно выбрасывается в атмосферу. Для того, чтобы концентрации вредных веществ в приземном слое атмосферы не превышали ПДК, отходящие газы выбрасываются через высокие трубы с целью создания условий для эффективного рассеивания.
Чем выше труба, тем больше ее рассеивающий эффект и, к сожалению, большая вероятность выпадения кислотных осадков в отдаленных районах.
Рассеивание вредных веществ в атмосфере – это временное, вынужденное мероприятие, которое осуществляется вследствие того, что существующие очистные устройства не обеспечивают полной очистки выбросов от вредных веществ.
Важное место в системе мероприятий по охране атмосферного воздуха занимают планировочные мероприятия, позволяющие существенно снизить воздействие загрязнения ОС на человека. При проектировании и строительстве промышленных предприятий особое значение придаётся выбору площадки и взаимному расположению производственных и жилых массивов. Предприятие должно быть расположено на ровном возвышенном месте, хорошо продуваемом ветрами. Площадка жилой застройки не должна быть выше предприятия. Предприятия должно располагаться за чертой населённых пунктов и с подветренной стороны от жилых массивов по отношению к господствующим ветрам. Цехи, выделяющие наибольшее количество вредных веществ, следует располагать на краю производственной площадки со стороны, противоположной жилому массиву. Взаимное расположение цехов должно быть таким, чтобы при направлении ветров в сторону жилых кварталов их выбросы не объединялись.
Предприятия, являющие источниками выделения в ОС вредных веществ, согласно «Санитарным нормам проектирования промышленных предприятий», следует отделять от жилой застройки санитарно-защитными зонами. Размеры этих зон до границы жилой застройки устанавливаются в зависимости от мощности предприятия, характера технологического процесса, количества и вида выделяемых в ОС ЗВ. В соответствии с санитарной классификацией предприятий и производств, тепловых электрических станций, складских зданий и сооружений установлены следующие размеры санитарно-защитных зон: для предприятий 1 класса – 1000 м; 2 – 500 м; 3 – 300 м; 4 – 100 м; 5 класса – 50 м. Предприятия, не выделяющие в атмосферу вредных веществ, допускается размещать в пределах жилых районов [2].
Основные задачи любой системы очистки атмосферного воздуха на предприятии сводятся к:
Улавливанию частиц — остатков продуктов горения, пыли, аэрозольных частиц и т.д. для их последующей утилизации.
Отсеиванию посторонних примесей — пара, газов, радиоактивных компонентов.
Улавливанию ценных частиц — отсеивание от основной массы частиц, сохранение которых имеет экономическое обоснование, к примеру оксидов ценных металлов.
Виды очистки воздуха можно классифицировать как по способу работы:
Химические методы очистки загрязненного воздуха (каталитическиее и сорбционные методы очистки)
Механические методы очистки воздуха (центробежная очистка, очистка водой, мокрая очистка)
Физико-химические методы очистки воздуха (конденсация, фильтрование, осаждение)
Так и по тому типу загрязнения:
Аппараты для очистки воздуха от пылевогозагрязнения
Аппараты для очистки от газового загрязнения
Теперь рассмотрим сами методы.
Осаждение — посторонние частицы отсеиваются от основной массы газа за счет воздействия определенной силы:
Силы тяжести в пылеосадительных камерах.
Инерционных сил в аппаратах-циклонах, в инерционных пылеуловителях в механических сухих пылеуловителях.
Электростатические силы, которые используются в электрофильтрах (Рисунок 2).
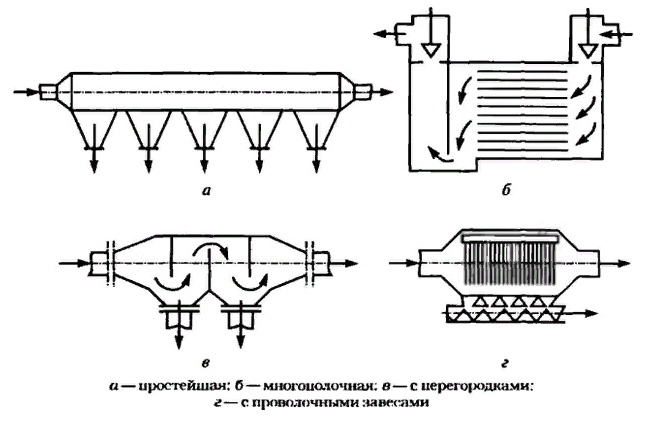
Рисунок 2 – виды электрофильтров.
Фильтрование — посторонние частицы отсеиваются при помощи специальных фильтров, которые пропускают основную массу воздуха, но задерживают взвешенные частицы. Основные типы фильтров:
Рукавные фильтры — в корпусе таких фильтров расположены рукава из ткани (чаще всего используется орлон, байка или стекловолоконная ткань), через которые проходит поток загрязненного воздуха из нижнего патрубка. Грязь оседает на ткани, а чистый воздух выходит из патрубка в верхней части фильтра. В
качестве профилактики, рукава периодически встряхиваются, грязь с рукавов падает в специальный отстойник.
Керамические фильтры — в таких устройствах используют фильтрующие элементы из пористой керамики.
Масляные фильтры — такие фильтры представляют собой набор отдельных ячеек-кассет. Внутри каждой ячейки располагаются насадки, которые смазываются специальной смазкой с высокой вязкостью. Проходя через такой фильтр, частицы грязи прилипают к насадкам (Рисунок 3).
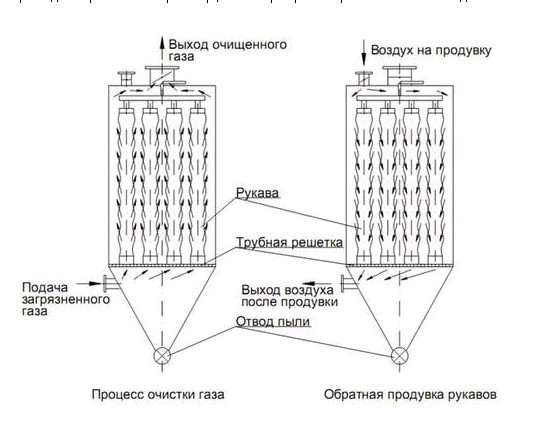
Рисунок 3 - Рукавный фильтр.
Электрические фильтры — в таких устройствах газовый поток проходит через электрическое поле, мелкодисперсные частицы получают электрический заряд, после чего оседают на заземленных осадительных электродах (Рисунок 4).
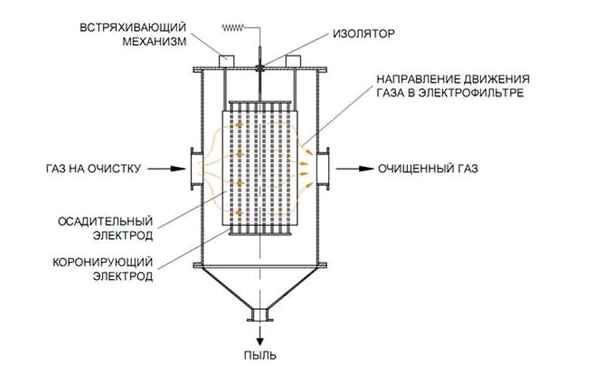
Рисунок 4 – Электрический фильтр.
Мокрая очистка — посторонние частицы в газовом потоке осаждаются при помощи водяной пыли или пены — вода обволакивает пыльи с помощью силы тяжести стекает в отстойник.
Чаще всего для мокрой очистки газа используются скрубберы — в этих устройствах поток загрязненного газа проходит через поток мелкодисперсных капель воды, они обволакивают пыльи под действием силы тяжести оседают и стекают в специальный отстойник в виде шлама.
Существует около десяти типов скрубберов, различающихся по конструкции и принципу работы, отдельно стоит выделить:
Скрубберы Вентури — имеют характерную форму в виде песочных часов. В основе работы таких скрубберов — уравнение Бернулли — увеличение скорости и турбулентности газа вследствие уменьшение площади потока. В точке максимальной скорости, в центральной части скруббера, газовый поток смешивается с водой ( Рисунок 5).
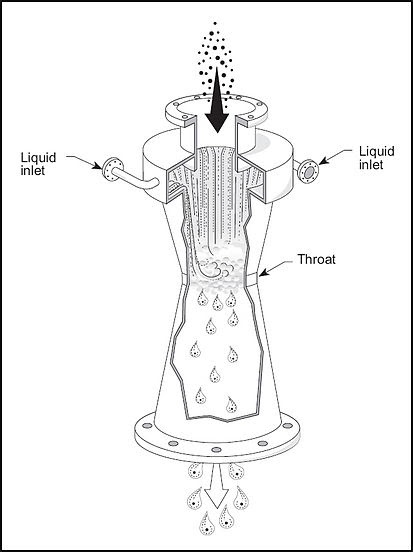
Рисунок 5 – Скруббер Вентури.
Форсуночные полые скрубберы — конструкция такого скруббера представляет полую цилиндрическую емкость, внутри которой расположены форсунки для распыления воды. Капли воды захватывают частицы пыли и под действием силы тяжести стекают в отстойник (Рисунок 6).
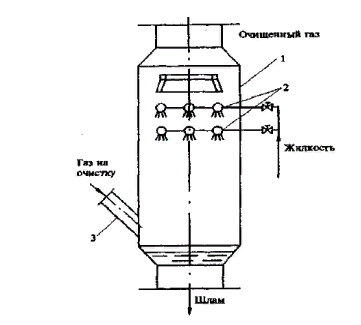