Файл: 1. Описание технологического процесса 1 Конструктивное описание оборудования.docx
Добавлен: 06.12.2023
Просмотров: 97
Скачиваний: 3
ВНИМАНИЕ! Если данный файл нарушает Ваши авторские права, то обязательно сообщите нам.
2.7.4 Конструктивные размеры шестерни и колеса
Шестерню выполняют за одно целое с валом, ее размеры определены выше: d1 =43,922 мм; dа1 =49,922 мм; b1 = 69 мм.
Колесо кованое: d2 = 276,078 мм; dа2 = 282,078 мм; b2 = 64 мм.
Диаметр ступицы dст = 1,6 · dк2 = 1,6 · 75 = 120 мм;
Длина ступицы lст = (1,5 ÷ 1,6) · dк2 = 112,5 ÷ 120 мм, принимаем lст = 115 мм.
Толщина обода δ0 = (2,5 ÷ 4) · mn = 7,5 ÷ 12 мм, принимаем δ0 = 8 мм.
Толщина диска С = 0,3 · b2 = 19,2 мм, принимаем С = 20 мм.
2.8 Проверочный расчет
2.8.1 Проверка долговечности подшипника ведущего вала
Из предварительных расчетов имеем:
Ft = 9108 Н; Fr = 3095 Н; Fа = 2786 Н; l1 = 76,5 мм; d1 = 43,922 мм.
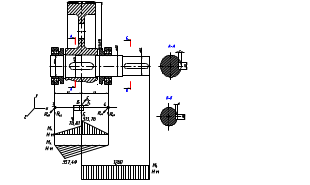
Рисунок 7 – Расчетная схема ведущего вала.
Реакции опор:
в плоскости xz



в плоскости yz
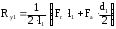

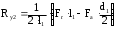

Проверка:
Ry1 + Ry2 – Fr = 1947 + 1148 – 3095 = 0.
Суммарные реакции:



Построение эпюр моментов в плоскости 0x:
Mx1 = 0,
Mx Ал = - Ry1 · l1 = - 1947 · 76,5 = - 148,95 Н·м,
Mx Ап = - Ry2 · l1 = -1148 · 76,5 = - 87,82 Н·м,
Mx2 = 0;
в плоскости 0y:Мy1 = 0,
Мy А = Rx1 · l1 = 4554 · 76,5 = 348,38 Н·м,
Мy 2 = 0;
в плоскости 0z:
Мz = M1 = 200 Н·м.
Подбираем подшипники по более нагруженной опоре 1. Намечаем радиальные шариковые подшипники 207 [3, с.335]: d = 35 мм; D = 72 мм; В = 17 мм; С = 25,5 кН; С0 = 13,7 кН.
Эквивалентная нагрузка определяется по формуле [3, с.117]:
Рэ = (X · V · PP1 + Y · Fa) · Kδ · KT,(73)
где PP1
– суммарная реакция, PP1 = 4953 Н;
Fa – осевая сила, Fa = 9108 Н;
V – коэффициент, зависящий от вращения подшипника; т.к. вращается внутреннее кольцо подшипника, то V = 1;
Kδ – коэффициент безопасности для приводов ленточных конвейеров, он равен Kδ = 1;
KT – температурный коэффициент, KT = 1 [3, с.117].
Отношение


Отношение

Рэ = (0,56 · 1 · 4953 + 1,86 · 3095) · 1 · 1 = 8530 Н.
Расчетная долговечность в млн.об.:


Расчетная долговечность, ч:

где n – частота вращения двигателя, n = 731,25 об/мин;

что больше установленных ГОСТ 16162 – 85.
2.8.2 Проверка долговечности подшипника ведомого вала
Ведомый вал несет такие же нагрузки, как и ведущий:
Ft = 9108 Н; Fr = 3095 Н; Fa = 2786 Н; l2 = 78,5 мм; d2 = 276,078 мм.

Рисунок 8 – Расчетная схема ведомого вала.
Реакции опор:
в плоскости xz


в плоскости yz
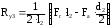

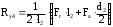

Проверка:
Ry4 – Ry3 – Fr = 3997 – 902 – 3095 = 0.
Суммарные реакции:




Построение эпюр моментов:
в плоскости 0x
Mx3 = 0,
Mx Бл = Ry3 · l2 = 902 · 78,5 = 70,81 Н·м,
Mx Бп = Ry4 · l2
= 3997 · 78,5 = 313,76 Н·м.
Mx4 = 0;
в плоскости 0y:
My3 = 0,
My Б = -Ry4 · l2 = -4554 · 78,5 = -357,49 Н·м,
My4 = 0;
в плоскости 0z
Mz = M2 = 1260 Н·м.
Выбираем подшипник по более нагруженной опоре 4 – шариковый однорядный подшипник 214 [3, с.335]:
d = 70 мм; D = 125 мм; В = 24 мм; С = 61,8 кН; С0 = 37,5 кН.
Отношение

Отношение

Эквивалентная нагрузка по формуле (74):
Рэ = (0,56 · 1 · 6059 + 2,10 · 2786) · 1 · 1 = 9244 Н.
Расчетная долговечность в млн.об. (75):

Расчетная долговечность в часах (76):
L =

что больше установленных ГОСТ 16162 – 85.
2.8.3 Проверка прочности шпоночных соединений
Шпонки призматические со скругленными торцами. Размеры сечений шпонок и пазов и длины шпонок – по ГОСТ 23360 – 78 [3, с.103]. Материал шпонок – сталь 45 нормализованная. Напряжения смятия и условия прочности по формуле [3, с.106]:

где М – вращающий момент, Н;
d – диаметр вала, мм;
b – ширина шпонки, мм;
h – высота шпонки, мм;
t1 – глубина паза шпоночной канавки, мм;
l – длина шпонки, мм;
Допускаемые напряжения смятия при стальной ступице [σсм] = 100 ÷ 120 МПа, при чугунной ступице [σсм] = 50 ÷ 70 МПа.
Ведущий вал:
d = 30 мм; b= 8 мм; h = 7 мм; t1 = 4 мм; l = 60 мм; М1 = 73 · 103 Н·мм.
[σсм] =

материал полумуфт МУВП – чугун СЧ20.
Ведомый вал:
d = 65 мм; b= 20 мм; h = 12 мм; t1 = 7,5 мм; l = 100 мм; М2 = 1260 · 103 Н·мм.
[σсм] =

материал полумуфт МУВП – чугун СЧ20.
2.9 Уточненный расчет ведомого вала
Материал вала – сталь 45 нормализованная, σв = 570 МПа. Предел выносливости при симметричном цикле изгиба:
σ-1 ≈ 0,43 · σв,(77)
σ-1 = 0,43 · 570 = 246 МПа.
Предел выносливости при симметричном цикле касательных напряжений:
τ-1 ≈ 0,58 · σ-1,(78)
τ-1 = 0,58 · 246 = 143 МПа.
Сечение А – А.
Коэффициент запаса прочности по формуле [3, с.100]:

где амплитуда и среднее значение отнулевого цикла:

Диаметр вала в этом сечении 75 мм. Концентрация напряжений обусловлена наличием шпоночной канавки. kσ=1,59 и kτ = 1,49 [3, с.98]; масштабные факторы εσ = 0,775 и ετ = 0,67; коэффициенты ψσ = 0,15 и ψτ = 0,1; М2 = 1260 · 103 Н·м.
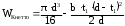
При d = 75 мм; b = 20 мм; t1 = 7,5 мм


s = sτ =

Изгибающий момент в горизонтальной плоскости:
М' = Rx3 · l2 = 4554 · 78,5 = 357,49 · 103 Н·м.
Изгибающий момент в вертикальной плоскости:
M" = Ry3 · l2 + Fa ·

Суммарный изгибающий момент в сечении А – А:
МА–А =

Момент сопротивления изгибу [3, с.100]:
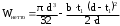

Амплитуда нормальных напряжений изгиба:


среднее напряжение σm = 0.
Коэффициент запаса прочности по нормальным напряжениям:


Результирующий коэффициент запаса прочности для сечения А – А


получился близким к коэффициенту запаса sτ = 7,8. Это незначительное расхождение свидетельствует о том, что консольные участки валов, рассчитанные по крутящему моменту и согласованные с расточками стандартных полумуфт, оказываются прочными, и что учет консольной нагрузки не вносит существенных изменений. Надо сказать и о том, что фактическое расхождение будет еще меньше, так как посадочная часть вала обычно бывает короче, чем длина полумуфты, что уменьшает значение изгибающего момента и нормальных напряжений.
Такой большой коэффициент запаса прочности (12,1 или 8,9) объясняется тем, что диаметр вала был увеличен при конструировании.
3.ЭКСПЛУАТАЦИЯ И РЕМОНТ ОБОРУДОВАНИЯ ЦЕПНОГО КОНВЕЙЕРА
В целях поддержания ленточного конвейера пригодном для эксплуатации состоянии и предупреждения преждевременного износа и поломок необходимо осуществлять качественное обслуживания, уход и своевременный ремонт оборудования.
Контроль за соблюдением правил обслуживания, и проведение ремонта возложены на ремонтные службы завода. Обеспечение правильной эксплуатации оборудования является также важнейшей обязанностью всего цехового персонала и в первую очередь производственных мастеров.
Эффективное использование оборудования возможно лишь при правильном его эксплуатации и бережном отношении к нему со стороны обслуживающего персонала.
Обслуживающий персонал обязан знать и строго соблюдать правила технической эксплуатации (ПТЭ) и инструкции по техническому обслуживанию, уходу за оборудованием. Знания соблюдение указанных правил и инструкции должны систематически проверяться.
Техническое обслуживание включает в себя:
- ежесменное техническое обслуживание
- ежесуточная проверка правильной эксплуатации и технического состояния.
- периодические технические осмотры, выполняемые после отработки оборудования определенного числа часов.[8]
3.1 Структура ремонтно-механической службы цеха
Цеховые ремонтные службы входят в состав производственных цехов и предназначаются для ремонтных операций по всем видам оборудования, установленного в цехе.[9]
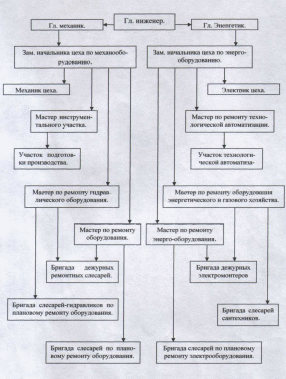
Рисунок 12 – Схема организационной структуры ремонтной службы цеха.
3.2 Годовой график планово-предупредительных ремонтов
Таблица 3 – Виды ремонтов.
Краткая техническая характеристика | Масса в тоннах | Вид ремонтов | Периодичность между ремонтами отработанных оборудованием часов | Периодичность ремонтов в часах | Число ремонтов в цикле |
Ленточный конвейер Ширина 1300мм. Длина 30000мм | 5,300 | ТО Т К | 730 4380 26280 | 8 36 144 | 30 5 1 |