Файл: 1 Начало промышленного производства ряда полимеров и пластмасс.docx
ВУЗ: Не указан
Категория: Не указан
Дисциплина: Не указана
Добавлен: 10.01.2024
Просмотров: 342
Скачиваний: 1
ВНИМАНИЕ! Если данный файл нарушает Ваши авторские права, то обязательно сообщите нам.
Литьевые машины, приспособленные для интрузии, оснащены подпрессовочным устройством для компенсации значительного уменьшения объема материала при его охлаждении. Его можно отрегулировать с высокой точностью для компенсации объемной усадки и придания материалу оптимальной структуры.
Особенность подобного метода – объем отливки может быть увеличен в 2÷3 раза по сравнению с номинальным объемом впрыска для машин данного типа размера. Но развиваемое в литьевой форме давление невелико, вследствие чего геометрия изделия не должна быть сложной, гнездность формы ограничена, получение тонкостенных изделий затруднено, необходимо учитывать термостабильность полимера.
Инжекционно-газовое литье (ИГЛ) относится к новым методам переработки термопластов с помощью литьевых машин.
Расплав полимера инжектируется в форму, заполняя ее на 70÷95% . Затем в форму через ниппель в форме или специальное сопло подается под давлением газовая смесь (физический газообразователь - ФГО), которая раздувает расплав, увеличивая тем самым толщину слоя полимера, образовавшегося при его соприкосновении с холодной стенкой формы, и способствуя заполнению конструктивных углублений. После образования изделия газовая смесь удаляется в приемник 4, при осевом перемещении червяка впрыскивается остаток расплава, “запечатывающий” форму. Технология ИГЛ позволяет экономить до 40 % дорогостоящего полимерного материала за счет уменьшения толщины стенки изделия, сократить цикл изготовления на 35 %, уменьшить вероятность брака за счет исключения таких видов брака, как утяжины, коробления, развитый облой. Кроме того, ИГЛ-технология позволяет упросить конструкцию и понизить стоимость формующей оснастки. Существенная трудность ИГЛ-технологии это необходимость высокоточного управления ЛМ, усложняется конструкция сопла, повышаются требования к расчету и качеству изготовления литниковой системы и сопряжений литьевых форм.
Сэндвич-литье заключается в попеременной подаче в литьевую форму полимерных расплавов из двух инжекционных узлов, т.е. в межслойное пространство внешней оболочки (первый полимер) происходит впрыск другого компонента (второй полимер), играющего роль внутреннего заполнителя. Для литья применяется специальное сопло, состоящего из двух камер, и в конструкции которого предусмотрено переключающее устройство. Как правило, это управляемый игольчатый клапан (ИК). Клапан попеременно или одновременно соединяет с литьевой системой формы инжекционные узлы ЛМ. Конструктивно сэндвич-литье может осуществляться по двум схемам.
-
Входной контроль исходного сырья
4.6.3 Входной контроль
Сырье, поступающее на предприятие в любой упаковке, сопровождается соответствующим документом (паспортом), в котором указываются его основные характеристики на соответствие требованиям ГОСТ или ТУ.
Для определения параметров перерабатываемости сырья, а также соответствия характеристик значениям, указанным в сопроводительном документе, проводится входной контроль. При этом определяется однородность материала по гранулометрическому составу и количество посторонних включений, влажность и показатель текучести расплава (ПТР), определяемый на приборе ИИРТ-М2, по необходимости и другие технологические и физико-механические показатели качества сырья. Входной контроль проводится в лабораториях ОТК, имеющих отделения технологических, физико-механических и химико-аналитических испытаний.
По результатам входного контроля определяется необходимость в дальнейшей подготовке сырья и корректировке режимов переработки.
-
Формование литьевых изделий
4.6.5 Формование литьевых изделий
Правильно выбранный и хорошо отработанный технологический режим, применение прогрессивного оборудования – основные условия получения качественных изделий и достижения высокой производительности труда.
Процесс литья под давлением с использованием червячной пластикации (инжекционное литье) заключается в следующем (рис. 4.27). До начала впрыска литьевая форма закрыта (а)и доза расплава накоплена перед червяком в передней части инжекционного цилиндра. Инжекционный цилиндр подводится к форме. В момент впрыска червяк перемещается только поступательно под давлением усилия гидроцилиндра инжекционного узла (б). После заполнения формы наступает выдержка под давлением (в). Она продолжается до начала охлаждения материала до температуры стеклования (кристаллизации) в литниковых каналах и выдержки без давления. Происходит понижение давление на материал по сравнению с давлением впрыска. Далее одновременно происходит охлаждение материала в форме и пластикация дозы материала в инжекционном цилиндре для следующего цикла литья. При пластикации червяк, вращаясь от привода, отходит назад под давлением материала (г). При пластикации сохраняется некоторое давление в гидроцилиндре (противодавление, давление подпора). Противодавление обеспечивает стабильность пластикации материала от цикла к циклу, равномерность набора дозы, однородность температуры и плотности материала, точность порции материала по массе. При этом инжекционный цилиндр отводится от формы. После набора дозы движение червяка (вращение и осевое перемещение вправо) прекращается. По окончании охлаждения термопласта форма открывается и готовое изделие выталкивается
(д). Далее форма замыкается и начинается следующий цикл литья.
Технологические параметры литья.
Основными технологическими параметрами литья под давлением является:
♦ температура литья (Тл, оС) – это температура, с которой материал поступает из инжекционного цилиндра в форму;
♦ температура формы (Тф, оС);
♦ давление литья (Рл,, МПа) устанавливают в гидроцилиндре литьевой машины;
♦ объемная скорость впрыска (Q, см3/с) или параметр обратно пропорциональный ей – время заполнения формы (τз , с);
♦ время выдержки под давлением (τвпд , с);
♦ давление формования (в форме) или давление подпитки (Рф,МПа)
♦ объем впрыска (V, см3);
♦ общая продолжительность цикла (τц , с).
Технологические параметры литья под давлением зависит от размеров и конфигурации изделий. В этой связи изделия классифицируют по зависимости объема отливки от толщины V=f(h). В зависимости от толщины h литьевые изделия условно разделяют на три группы.
Первая группа – изделия тонкостенные сложной формы (h=0,5÷2,25 мм). Изделий этой группы имеют повышенное гидравлическое сопротивление заполнению формы. При их литье применяют верхние значения рабочего диапазона технологических параметров и низковязкие марки термопластов, которые обладают хорошей формуемостью и легко заполняют формы сложной формы. Вторая группа – изделия общего назначения средних размеров (h=1,0÷4,5 мм). Третья группа – изделия толстостенные простой конфигурации (h=1,9÷6,0 мм). Изделия данной группы имеют пониженное гидравлическое сопротивление заполнению формы и применяют нижние значения рабочего диапазона технологических параметров литья. Для литья толстостенных изделий можно применять высоковязкие марки полимеров, которые имеют повышенные молекулярную массу и ударную вязкость.
-
Диаграмма формования литьевых изделий (Диаграмма изменения давления Pи температуры Tв литьевой форме)
Периоды формования
Процесс формования состоит из трех периодов (рис. 4.29):
–
![]() | Рис. 4.29. Диаграмма изменения давления Pи температуры Tв литьевой форме: τз – период заполнения формы, τн– период нарастания давления, τсп – период спада давления, τвпд – время выдержки под давлением, τвбд – время выдержки без давления; т. А – заполнения форы, т. С – гидроудара, т. D – максимального давления, т. Е – окончание выдержки под давлением. |
-
периода впрыска расплава и заполнение оформляющей полости литьевой формы (τз) –точка А; -
периода нарастания давления (τн) и уплотнения материала за счет втекания новых порций расплава под давлением. Точка D – точка максимального давления. В данный момент за счет термической усадки при охлаждении давление уравновешивается притоком новых порций материала. -
периода спада давления (τсп) – это период интенсивного охлаждения и усадки материала. Характеризуется уменьшением давления в форме и увеличением перепада давления по ее длине. В этот период входит и время выдержки без давления (τвбд).
Время выдержки под давлением (τвпд); состоит из периода нарастания давления и части периода спада давления. В точке Е литник “перемерзает” (стеклование материала в литниковом канале) и приток новых порций материала прекращается. Давление литья отключается и давление в детали резко падает. В точке К форма раскрывается, происходит съем изделия из формы.
Технологические параметры впрыска:
-
температура расплава на входе в форму; -
скорость заполнения и время полного заполнения формы.
Эти параметры сильно зависят от конфигурации, размеров и формы литникового канала. Изменение параметров впрыска возможно путем регулирования температуры формы, давления в гидроцилиндре впрыска и скорости осевого перемещения шнека (времени впрыска).
-
Технологические расчеты при литье под давлением
4.6.6.10 Технологические расчеты при литье под давлением
1. Расчетный объем впрыска вычисляют по формуле:
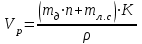
где Vр – расчетный объем впрыска, см3; mд – масса отливаемой детали, г; mл.с. – масса литниковой системы, г; n – число гнезд формы; К – коэффициент, учитывающий сжатие расплава полимера и его утечки при впрыске в форму, К =1,21,3; ρ – плотность перерабатываемого полимера, г/см3.
2. Производительность литьевой машины рассчитывают по формуле:

где m – масса изделия (детали), г; n – число гнезд формы; ц - продолжительность цикла литья изделия, с.
3. Продолжительность цикла литья под давлением определяют следующим образом:

где см,,р,впр – время смыкания и размыкания формы, время впрыска (заполнения формы), с; их сумма называется машинным временем м:

Время смыкания и размыкания формы берут из технической характеристики машины.
Время впрыска рассчитывают по формуле:

где Q– объемная скорость впрыска, см3/с (из технической характеристики).
Продолжительность паузы между циклами п=23 с.
Сумма продолжительности выдержки материала в форме под давлением выд и продолжительность охлаждения изделия в форме без давления охл.б/д называется технологическим временем т, с:

Технологическое время показывает продолжительность охлаждения до заданной температуры в центре изделия Ти, при которой возможно извлечение без деформации готового изделия.
Технологическое время рассчитывается на основе закона контактной теплопередачи:
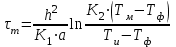
где h – толщина стенки изделия, м; a – коэффициент температуропроводности, м2/с; Tм – температура расплава полимера, впрыскиваемого в формующую полость литьевой формы – температура литья,