ВУЗ: Не указан
Категория: Не указан
Дисциплина: Не указана
Добавлен: 10.01.2024
Просмотров: 62
Скачиваний: 1
ВНИМАНИЕ! Если данный файл нарушает Ваши авторские права, то обязательно сообщите нам.
Плавная регулировка сварочного тока Отказ от подвижных обмоток Принудительное охлаждение
Выбор рода тока и источника питания
Для сварки фермы рациональнее применить полуавтоматическую сварку в углекислом газе. Конструктивно сварочный полуавтомат состоит из источника тока (выпрямителя) и механизма подачи сварочной проволоки, выполненных в одном корпусе или раздельно и комплектуется сварочной горелкой (рис.3.1.). Основной принцип полуавтоматической сварки MIG/MAG заключается в том, что металлическая проволока во время сварки подается в зону сварки через сварочную горелку и плавится в электрической дуге. Сварочная проволока при этом методе играет двойную роль - она является токопроводящим электродом и служит присадочным материалом.
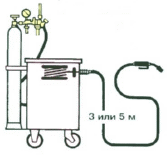
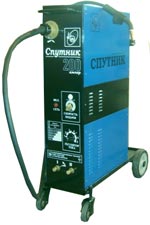
Рисунок 2- Основной механизм подачи проволоки толкающего типа с обычной горелкой
Исходя из конструктивных особенностей оборудования для полуавтоматической сварки в углекислом газе используют полуавтомат "Спутник". Силовой блок питания вырабатывает переменный сварочный ток, силовой выпрямитель преобразует переменный ток в постоянный, дроссель сглаживает пульсации тока после преобразования, блок управления включает и выключает силовой блок питания, пневмоклапан для подачи защитного газа в зону сварки и подающий механизм. Шлангом управления производится включение блока управления и производится сварка. На панели управления расположены все органы управления полуавтомата (кроме кнопки включения схемы, она на ручке шланга управления): регулировка подачи электродной проволоки, регулировка силы сварочного тока и напряжения, тумблер включения сети, сигнальная лампа (показывает наличие напряжения), универсальный разъем для подключения шланга управления, вывод для подключения кабеля обратного тока (массы).
Принцип работы полуавтомата основан на сварке металлов в среде защитного газа плавящимся электродом.
Посредством шланга управления в место сварки автоматически подается электрод и защитный газ, а перемещение сварочной горелки по шву производится вручную сварщиком.
Порядковый номер полуавтомата выбит на передней панели около подающего механизма и на табличке на задней панели. Пломбировка полуавтомата отсутствует.
Во время работы полуавтомата необходимо соблюдать время периода работы и паузы (ПВ), т.к. во время сварки происходит нагрев дросселя, силового выпрямителя и силового трансформатора, при нагреве они могут выйти из строя. Время сварки 3 минуты. Время паузы (перерыва) 2 минуты.
Во время паузы происходит охлаждение за счет естественной вентиляции силовых агрегатов полуавтомата через имеющиеся вентиляционные отверстия в корпусе.
Для сварки использовать сварочную проволоку, желательно омедненную, диаметром 0,6-1 мм (комплект поставки по диаметр 0,8 мм) нельзя использовать ржавую и гнутую сварочную проволоку.
Таблица 2 Технические характеристики полуавтомата "Спутник":
Технические характеристики | |
Напряжение питаниясети, В | 380 |
Максимальный сварочный ток полуавтомата, А | 175 |
Номинальное рабочее напряжение полуавтомата, В | 32 |
Максимальный режим работы ПВ, % | 60 |
Частота питающей сети, Гц | 50 |
Диаметр используемой проволоки, мм | 0,8-1,2 |
Скорость вылета электрода, м/мин | 0-11 |
Потребляемая мощность, кВт не более | 3,5 |
Масса полуавтомата, кг | 85 |
Размеры | 1000х815х355 |
Кроме сварочного полуавтомата сварка в углекислом газе предусматривает использование дополнительного оборудования - подогревателя и осушителя.
Подогреватель используется только при сварке в углекислом газе. Испарение жидкого СО2 при большом его расходе приводит к резкому понижению температуры. Влага, содержащаяся в газе, замерзает в редукторе. Для безопасности подогреватель питается постоянным (20 В) или переменным током (36 В).
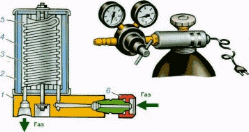
Рисунок 3 - Подогреватель: 1 - корпус, 2 - кожух, 3 - змеевик, 4 - теплоизоляция, 5 - нагревательный элемент, 6 - накидная гайка.
Осушитель поглощает влагу из углекислого газа. Выпускается двух модификаций: высокого и низкого давления. Осушитель высокого давления устанавливают перед регулятором (редуктором), а низкого - после него. Влагопоглощающим веществом служит силикагель или алюмогликоль. Путем прокаливания при t0 2500-300 0C эти вещества поддаются восстановлению.
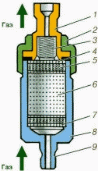
Рисунок 4 - Осушитель: 1 - втулка, 2 - накидная гайка, 3 - пружина, 4 - сетка, 5 - фильтр, 6 - осушающий материал, 7 - сетчатая шайба, 8 - корпус, 9 - штуцер.
5 Контроль качества сварного шва
Сварочные материалы перед использованием должны быть проконтролированы:
на наличие сертификата (на электроды, проволоку и флюс) с проверкой полноты приведенных в нем данных и их соответствия требованиям стандарта, технических условий или паспорта на конкретные сварочные материалы;
на наличие на каждом упаковочном месте (пачке, коробке, ящике, мотке, бухте и пр.) соответствующих этикеток (ярлыков) или бирок с проверкой указанных в них данных;
на отсутствие повреждений упаковок и самих материалов;
на наличие для баллонов с газом соответствующего документа, регламентированного стандартом.
Контроль качества сварных соединений стальных конструкций производится:
внешним осмотром с проверкой геометрических размеров и формы швов в объеме 100 %;
неразрушающими методами (радиографированием или ультразвуковой дефектоскопией) в объеме не менее 0,5 % длины швов. Увеличение объема контроля неразрушающими методами или контроль другими методами проводится в случае, если это предусмотрено чертежами КМ или НТД (ПТД).
Результаты контроля качества сварных соединений стальных конструкций должны отвечать требованиям СНиП 3.03.01-87 (пп.8.56-8.76), которые приведены в приложении 14.
Контроль размеров сварного шва и определение величины выявленных дефектов следует производить измерительным инструментом, имеющим точность измерения ±0,1 мм, или специальными шаблонами для проверки геометрических размеров швов. При внешнем осмотре рекомендуется применять лупу с 5-10-кратным увеличением.
Трещины всех видов и размеров в швах сварных соединений конструкций не допускаются и должны быть устранены с последующей заваркой и контролем.
Контроль швов сварных соединений конструкций неразрушающими методами следует проводить после исправления недопустимых дефектов, обнаруженных внешним осмотром.
Выборочному контролю швов сварных соединений, качество которых согласно проекту требуется проверять неразрушающими физическими методами, должны подлежать участки, где наружным осмотром выявлены дефекты, а также участки пересечения швов. Длина контролируемого участка не менее 100 мм.
В швах сварных соединений конструкций, возводимых или эксплуатируемых в районах с расчетной температурой ниже минус 40°С до минус 65°С включительно допускаются внутренние дефекты, эквивалентная площадь которых не превышает половины значений допустимой оценочной площади. При этом наименьшую поисковую площадь необходимо уменьшить в два раза. Расстояние между дефектами должно быть не менее удвоенной длины оценочного участка.
В соединениях, доступных сварке с двух сторон, а также в соединениях на подкладках суммарная площадь дефектов (наружных, внутренних или тех и других одновременно) на оценочном участке не должна превышать 5 % площади продольного сечения сварного шва на этом участке.
В соединениях без подкладок, доступных сварке только с одной стороны, суммарная площадь всех дефектов на оценочном участке не должна превышать 10 % площади продольного сечения сварного шва на этом участке. Сварные соединения, контролируемые при отрицательной температуре окружающего воздуха, следует просушить нагревом до полного удаления замерзшей воды.
6 Техника изготовления уменьшенной копии решетчатой сварной конструкции
Узлы фермы сваривают последовательно - от середины фермы к опорным узлам. Сначала выполняют стыковые, а затем угловые швы. Если швы разного сечения, то вначале накладывают швы с большим сечением, а затем с меньшим. Каждый элемент при сборке прихватывают швом длиной 30-40мм. Близко расположенные швы не выполняются сразу. Сначала дают остыть тому участку основного металла, где будет накладываться близко расположенный шов. Это снизит перегрев металла и пластические деформации. Концы (фланговых) продольных швов выводят на торец привариваемого элемента на длину 20 мм., что гарантирует прочность сварных соединений. (см.рис.2.4.1)
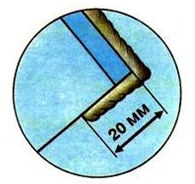
Рисунок 5 - Длина продольного шва.
При сварке деталей ферм используют следующие виды соединений:
нахлесточное соединение с обваркой контура уголка прочнее и жестче.
Целесообразно перекрещивать полки уголков, перпендикулярные к плоскости
соединения. Во избежание появления в стержнях лишних изгибающих и крутящих моментов целесообразно соединять элементы фермы так, чтобы линии центров изгиба сечений пересекались в одной точке.
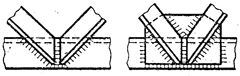
Рисунок 6
Соединение полками, обращенными в одну сторону компактнее.
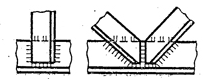
Рисунок 7
Узел фермы с косынкой - жесткость соединения усиливают косынками.
Соединение с накладными косынками значительно прочнее и жестче.
.
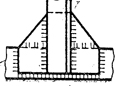
Рисунок 8 - Узел фермы с косынкой.
Узел фермы с накладкой: к горизонтальному стержню фермы, представляющему в сечениидвутавр, приваривается двумя угловыми швами 1 надставка.
При длине швов более 500 мм они накладываются обратноступенчатым способом.
Два стержня, каждый из которых состоит из двух уголков, устанавливаются на надставку и прихватываются к ней с таким расчетом, чтобы геометрические оси стержней и балки пересекались в одной точке. Сначала накладываются лобовые швы 2, затем фланговые 3 и 4, направление сварки которых должно быть от лобового шва к краям надставки. Во избежание коробления надставки швы 3 и 4 следует накладывать одновременно с обеих сторон надставки либо поочередно с одной и с другой стороны .
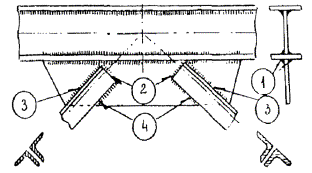
Рисунок 9 - Узел фермы с надставкой.
Конец продольного шва выводят на торец привариваемого элемента на длину узел фермы с прокладкой используют в случае, когда сечение всех стержней состоит из парных элементов - уголков или швеллеров. Парные элементы стержней соединяют между собой с зазором, в который вставляется прокладка. Сначала приваривается горизонтальный стержень к прокладке швами 1 и 2. Сварку рекомендуется вести одновременно с обеих сторон прокладки двумя сварщиками. Затем таким же образом приваривается вертикальная стойка, а потом две наклонные стойки.
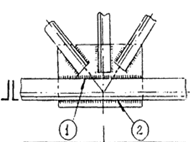
Рисунок 10 -Узел фермы с прокладкой.
Меры, применяемые по борьбе со сварочными напряжениями
Для борьбы с остаточными деформациями и напряжениями следует соблюдать следующие правила.
При сборке конструкций применять по возможности сборочные приспособления (стяжные планки, клинья и т.п.), обеспечивающие свободное перемещение свариваемых конструкций от усадки швов. Прихватки можно применять только для стыков деталей из тонкого металла (3-5 мм) и в нахлесточных соединениях. Следует строго соблюдать размеры притуплений, зазоров и соосность элементов.