Добавлен: 07.11.2023
Просмотров: 99
Скачиваний: 3
ВНИМАНИЕ! Если данный файл нарушает Ваши авторские права, то обязательно сообщите нам.
СОДЕРЖАНИЕ
Расчет электрических нагревателей
Разработка электрической принципиальной схемы печи для сушки электродвигателей
Выбор элементов силовой цепи и цепи управления для двигателя вентилятора
Выбор элементов силовой цепи и цепи управления для двигателя перемещения тележки
Выбор элементов силовой цепи и цепи управления для схемы калорифера
Выбор ограничивающих резисторов и ламп цепи сигнализации

Таким образом, фонд работы оборудования составляет 1980 агрегато-ч/год.
3.3 Выбор формы организации производства
Форма организации производства – это порядок перемещения предметов труда в производственном процессе по рабочим местам (позициям). Каждая форма организации соответствует определенному типу производства.
В нашем случае целесообразным является применение прямоточной формы организации производства. Прямоточная форма характеризуется расположением рабочих мест в порядке закрепленных за ними технологических операций. Ремонтируемые единицы передаются поштучно, но время выполнения отдельных операций не всегда одинаково, то есть синхронизация времени операций имеет место не на всех участках линии. Поэтому около рабочих мест, на которых время выполнения операций больше такта, создаются заделы деталей.
3.4 Разработка графика процесса ремонта основной продукции и графика загрузки рабочих
Организация процесса ремонта сложных сборочных единиц осуществляется на основе технологического графика, выполняемого по линейному или сетевому принципу.
При разработке технологических графиков используют технически обоснованные нормы времени, действующие карты технологического процесса.
В данном дипломном проекте, основываясь на таблицу 3.1, представлен линейный график работы электромашинного отделения по циклу ТР-3 и график загрузки рабочих, представляющий собой эпюру потребности трудовых ресурсов (лист 3 графической части).
3.5 Определение оборотного задела сборочных единиц электромашинного отделения
Норма простоя локомотива на ТР - 3составляет 7 суток [1]. Для соблюдения необходимых норм простоя локомотива при проведении ремонтных работ в объеме ТР-3 необходимо создание оборотного задела тяговых электродвигателей.
1 2 3 4 5 6 7 8 9 10
Оборотный фонд запасных деталей и узлов
,
где


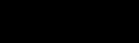
где


p - число тяговых электродвигателей на секции.
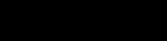
Тогда страховой запас запасных деталей и узлов
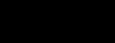
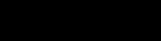
Таким образом, оборотный фонд запасных деталей и узлов

Следовательно, оборотный фонд составляет 2,16 тяговых электродвигателей.
3.6 Расчет трудоемкости производственной программы
Трудоемкость годовой программы ремонта секций электровоза

где qi – трудоемкость ремонта i-го изделия цикла ТР-3, чел.ч/секция, взята по опыту депо Барановичи и представляем в таблице 3.1.
Таблица3.1 – Трудоемкость текущего ремонта ТР-3 секции электровоза ВЛ-80с по электромашинному отделению
Наименование работ выполняемых в объеме ТР-3 | Разряд | Условияработы | Трудоёмкость,чел.ч/секцию | |||||||||||
Расщепитель фаз НБ 455А снять и поставить | 4 | 2 | 2,07 | |||||||||||
Расщепитель фаз разобрать, восстановить, собрать | 5 | 3 | 3,27 | |||||||||||
Тяговый электродвигатель разобрать, восстановить,собрать | 5 | 3 | 111,00 | |||||||||||
Тяговый электродвигатель – палец кронштейнащеткодержателя отремонтировать | 4 | 3 | 5,28 | |||||||||||
Тяговый электродвигатель – щеткодержательразобрать, восстановить, собрать | 4 | 2 | 12,72 | |||||||||||
Электродвигатель вентилятора АЭ-92-4 разобрать,восстановить, собрать | 5 | 3 | 14,70 | |||||||||||
Электродвигатель вентилятора АЭ-92-4 с двумя центробежными вентиляторами снять и поставить | 4 | 2 | 3,06 | |||||||||||
Электронасос ЭЦТ-63/10 снять и поставить | 4 | 2 | 0,57 | |||||||||||
Вентилятор разобрать, собрать, зазоры отрегулировать | 5 | 2 | 2,00 | | ||||||||||
Шунт индуктивный ИШ-84 или ИШ-95 снять ипоставить | 4 | 3 | 2,68 | | ||||||||||
Шунт индуктивный ИШ-84 или ИШ-95 разобрать, восстановить, собрать | 4 | 3 | 5,92 | | ||||||||||
Тяговый электродвигатель – якорь динамическиотбалансировать | 8 | 2 | 9,52 | | ||||||||||
Крыльчатку мотора вентилятора отбалансировать | 8 | 2 | 3,20 | | ||||||||||
Электродвигатель компрессора отремонтировать | 7 | 2 | 0,57 | | ||||||||||
Электронасос ЭЦТ-63/10 разобрать, восстановить,собрать | 5 | 3 | 1,92 | | ||||||||||
Реактор переходной ПРА-3А разобрать, восстановить, собрать | 4 | 3 | 3,66 | | ||||||||||
Реактор сглаживающий РС-32 снять и поставить | 4 | 2 | 1,60 | | ||||||||||
Реактор сглаживающий РС-32 отремонтировать | 4 | 3 | 2,94 | | ||||||||||
Электродвигатель вентилятора АЭ-92-4 с двумя вентиляторами разобрать, восстановить, собрать | 5 | 3 | 11,46 | | ||||||||||
Электродвигатель вентилятора АЭ-92-4 – ротор динамически отбалансировать | 8 | 2 | 1,80 | |||||||||||
Электродвигатель вентилятора АЭ-92-4 снять и поставить | 4 | 2 | 3,57 | |||||||||||
Итого: | 203,61 | |
1 2 3 4 5 6 7 8 9 10
Таким образом, трудоемкость годовой программы ремонта цикла ТР-3 по электромашинному отделению составляет

Трудоемкость ремонта тяговых электродвигателей цикла ТР-3

3.7 Определение потребного оборудования. Составление ведомости оборудования
При организации ремонтного производства в современных депо предусматривается узкая специализация рабочих мест, оснащенных механизмами, инструментами и приспособлениями, позволяющими снизить трудоемкость ремонта. Определение номенклатуры и количества специализированного и специального технологического оборудования электромашинного отделения производится с учетом технологического процесса ремонта электрических машин.
Количество необходимого оборудования определяется формулой
,
Тогда количество бандажировочных станков по формуле (3.8) будет равно
ед.
Принимаем один бандажировочный станок.
Аналогично рассчитывается количество остального технологического оборудования. В таблице 3.2 представлено оборудование проектируемого электромашинного отделения, его количество, габаритные размеры, потребляемая мощность, а также позиция на плане отделения, изображенного на листе 4 графической части дипломного проекта.
3.8 Расчет работников отделения
Явочный контингент работников, работающих в электромашинном отделении (ТР-3)
Ая


Подставляя численные значения, получаем для всего отделения
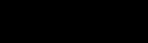
Принимаем АЯ = 7 человек.
Списочный контингент работников в электромашинном отделении (ТР-3)

Подставляя численные значения, получаем
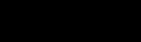
Принимаем списочное количество работников (ТР-3) Асп = 8 человек.
3.9 Определение площади и размеров отделения
Размеры электромашинного отделения определяем, исходя из стандартных размеров участков и условия размещения в них ремонтируемых сборочных единиц и ремонтного оборудования с учетом проходов, расстояний от оборудования до стен, проездов, установок передаточных тележек и грузоподъемных кранов.
Ширину отделения принимаем b = 12 м, длину a, кратную расстоянию между опорными колонами, определяем после расстановки оборудования. В соответствии с планом отделения, представленном на листе 4 графической части дипломного проекта, а = 54 м.
Площадь отделения, м2
S = ab,
S = 54·12= 648м2.
Полученное значение площади отделения используется в дальнейшем для определения энергетических затрат на освещение.
3.10 Расчет расхода энергетических ресурсов
Расход электроэнергии на работу технологического оборудования
Pоб = ΣPустФiηзηод ,
где | ΣPуст | – | суммарная мощность оборудования отделения, кВт; по таблице 3.2 ΣPуст = 545,6 кВт; |
| ηз | – | коэффициент загрузки оборудования; принимаем ηз = 0,75; |
| ηод | – | коэффициент одновременной работы оборудования; принимаем ηод = 0,27. |
| | | |
Pоб = 545,6·1980·0,75·0,27 = 218758,3 кВт·ч.
Расход электроэнергии на освещение электромашинного отделения
Pос = TосWS,
Pос = 3200·0,018·648 = 37324,8 кВт·ч.
Расчет расхода других энергоресурсов сводим в таблицу 3.3.
Годовой расход используемых энергоресурсов
Pгi = piПТЗ-3,
Таблица 3.3 – Расход используемых энергоресурсов
Вид энергоресурса | Расход i-го вида энергоресурса на секцию, ед. / секцию | Программа ремонта, секций | Общий расход i-го вида энергоресурса на всю программу ремонта |
Кислород, м3 | 2,2 | 70 | 154 |
Ацетилен, м3 | 2 | 140 | |
Вода техническая, м3 | 82 | 5740 | |
Пар, м3 | 21,7 | 1519 | |
Воздух сжатый, м3 | 896,13 | 62729,1 |
1 2 3 4 5 6 7 8 9 10
Полученные данные в дальнейшем используем для расчёта себестоимости ремонта.
3.11 Выбор подъемно-транспортного оборудования
Определение количества подъемно-транспортного оборудования электроаппаратного отделения производим с учетом обеспечения:
1 Полной механизации всех подъемных, транспортных и складских работ.
2 Обслуживания отдельных рабочих мест индивидуальными подъемными устройствами.
3 Создания удобной транспортной связи между отделениями, позициям и рабочими местам.
Грузоподъемность подъемно-транспортного оборудования определяется максимальной массой транспортируемой сборочной единицы электровоза. В электромашинном отделении таким узлом является тяговый двигатель, масса которого для электровоза ВЛ-80с не превышает шести тонн. Для пропиточно-сушильного отделения максимальную массу имеет остов тягового двигателя в сборе. Она равна 2350 кг.
Характеристики и количество выбранных подъемно-транспортных средств сводим в таблицу 3.4.
Таблица 3.4 – Подъемно-транспортные средства электромашинного отделения
Наименование подъемно-транспортного оборудования | Количество | Характеристика |
Кран мостовой однобалочный с электрической талью | 1 | Q= 10 т; L= 10,5 м |
Кран мостовой однобалочный с электрической талью | 1 | Q= 3 т; L= 10,5 м |
Тележка передаточная | 3 | Колея – 1000 мм Q= 6 т |
3.12 Разработка плана и поперечного разреза электромашинного отделения
План электромашинного отделения представлен на листе 4 графической части проекта. На территории отделения находится сушильно-пропиточный участок, отгороженный от основного помещения капитальными стенами вследствие вредности выделяемых паров при проведении пропитки, сушки и окраске электрических машин. Также на плане отображается потребное подъёмно-транспортное специализированное и специальное технологическое оборудование. Отделение оснащено станцией испытания тяговых двигателей методом взаимной нагрузки.